Jim Brown presents on this webinar about “Building the PLM Foundation with PDM” sponsored by Siemens PLM. Jim’s presentation highlights the importance of PDM basics – control, access, and sharing product data- to successful product development. View a Replay of the Webcast
- Executive Overview
- Raising the Bar on Product Development Performance
- Boosting Team Performance and Collaboration
- Capturing Product Knowledge from “Social” Interactions
- Discovering Knowledge from Product Networks
- Developing New Product IP from Communities
- Going Social with Product Development
- Conclusion
- Recommendations
- About the Author
- Today’s product development environment has become much more complex, making the development of profitable products more difficult.
- Competitive adoption of engineering and product development software has increased performance and raised the standards for product development.
- Enhance product development team execution and collaboration
- More naturally capture and share product knowledge and expertise
- Enable the discovery of new IP and product value


- Executive Overview
- Defining the Roles of ERP and PLM
- Where does PLM Stop, and ERP Begin?
- Roles: The Technical Perspective
- Integrating Innovation to Execution
- Evolution: Bi-Directional Integration
- Further Evolution: Advanced Integration
- Integration: The Technical Perspective
- Conclusion
- Recommendations
- About the Author


- Preface
- About the Author
- Executive Overview
- Lifecycle Service for Medical Equipment
- Servicing the Top Line
- Bottom Line Results
- Managing Medical Equipment Complexity
- Establishing Operational Control and Equipment Intelligence
- Summary
- Recommendations


- Introducing the Issue
- Mining the Value from PLM Data
- Sources of Value from BI in PLM
- Special Considerations for BI in PLM
- Conclusion
- Recommendations
- About the Author
- Manufacturers have moved forward along the maturity curve with their PLM implementations.
- PLM has evolved and expanded to incorporate more valuable, business-focused data in addition to technical information


- Introducing the Issue
- Calculating the Benefits of Product Portfolio Management
- Growing the Top Line
- Calculating Cost Savings
- Incorporating the “Soft” Benefits
- Example
- Recommendations
- About the Author
- Footnotes
- Selecting higher value products
- Making better – and more timely – decisions to correct or cancel product development projects with limited return
- Improving time to market
- Improving product development efficiency
- Aligning their product portfolio with company strategy
- Balancing product development work with available resources
- Balancing the risk in their product portfolio




- Mechanical Complexity
- Mechatronics
- Global Markets
- Global Design and Manufacturing
- Lifecycle Profitability




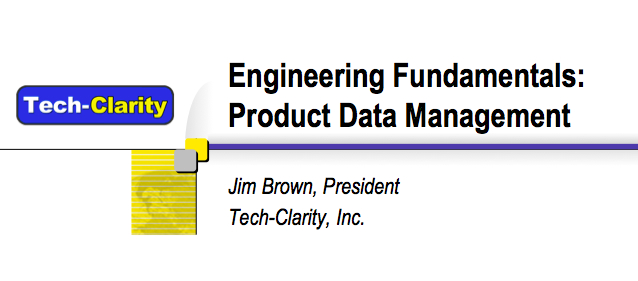
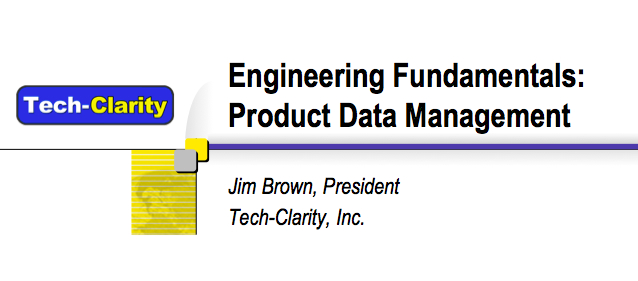
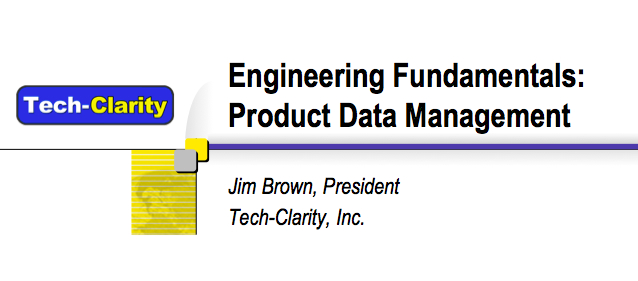
All Results for "All"
Taking PPM to the Next Level
Jim Brown presents his views on Advanced PPM on this joint SAP / SmartOrg webinar. He will share his views from his report on improving product development decision making. View a Replay of the Webcast Note: The sign-in screen is very sparse, don’t be alarmed.
System-Driven Product Development
Jim Brown continues this webcast series by presenting the challenges companies face developing mechatronic products. Jim joins Siemens PLM to discuss the importance of smarter products and how companies can manage the complexity associated with developing them. Watch the Webcast Replay
Securing Market Access for Medical Devices
Jim Brown will join Supply & Demand Chain Executive and IHS to help healthcare companies understand how the market for their products can be put at risk by regulations and supply chain issues such as counterfeit components and shortages. View a Replay of the Webcast
Developing Sustainable Products
Jim Brown presents on how companies can design more sustainable products. Jim joins Siemens on another of their webcast series on product complexity to address environmental compliance and sustainability. Register for the Webinar
How to Drive More Product Innovation with Embedded Software
Jim Brown shares his recent research on innovating with embedded software in mechatronic products on this EETimes webinar. Jim joins PTC to discuss the challenges and benefits of developing software-intensive products. View the Event Replay
Jump-start your Product Pipeline Process to Drive Innovation
Jim Brown presents about implementing best practice processes and tools for Product Portfolio Management (PPM). Jim joins Planview and Kalypso on this webcast describing how companies can put in place an integrated innovation process without reinventing the wheel. Watch the Recorded Webinar
Mobile PLM for Improved Profitability
Jim Brown joins Siemens PLM on this webcast on the value that PLM plays in a mobile setting. His presentation discusses the use of mobile Product Lifecycle Management Solutions and how they can help Engineering and Product or Program managers improve business performance. Register for the Webinar View Related Webinar on IT Considerations
IT Considerations for Leveraging Mobility to Extend PLM Value
Jim Brown speaks on this Siemens PLM webcast on what the CIO’s team needs to know to support a mobile PLM strategy. Includes an overview of six practical considerations IT must consider for mobile applications for PLM. View a Replay of the Webcast
Navigating Today’s Global Regulatory Environment
Jim Brown will speak on this Environmental Leader webcast sponsored by IHS to share his research and perspective on the challenges of addressing environmental regulatory compliance and sustainability in product development and the product lifecycle. View a Replay of the Event
Going Social with Product Development
Going Social with Product Development: Improving Product Development Performance with Social Computing explores how manufacturers are taking advantage of social computing and “Web 2.0” technologies to raise the bar on product development performance. Provides examples of how the concepts behind social networking are being applied in to help new product development (NPD) teams boost performance…
Nuage Social Business Collaboration Launch
The Nuage Social Business Collaboration Launch was the official launch of a new company focused providing social computing capabilities to business. Jim Brown presented his views from his recent report on social business collaboration and the product lifecycle as a guest host of the launch of software company Nuage Corporation. View a Replay of the…
Evolving Roles of ERP and PLM
The Evolving Roles of ERP and PLM: Integrating the Roles of Execution and Innovation extends past research on the roles of ERP and PLM, describes the evolution of ERP-PLM integration beyond the basics to a more mature, bi-directional interaction. Reviews how companies can close the loop between product innovation and managing the business of manufacturing….
Servicing Medical Equipment
Servicing Medical Equipment: World Class Service Management for Medical Equipment extends prior research on world class service management to the medical device industry. The research suggests that there are two fundamentals that service organizations must master to rise above the competition – operational control of service operations and equipment intelligence. The paper discusses how medical device…
Business Intelligence Extending PLM Value
Business Intelligence Extending PLM Value: PLM Maturity Enables New Value from Analytics points out the significant value that has accumulated in PLM systems as implementations and usage have matured, and how manufacturers can tap into that value with business intelligence (BI) solutions. Please enjoy the free Introduction below, or click the report title above to…
The ROI of Product Portfolio Management
Issue in Focus: The ROI of Product Portfolio Management: The “How to Guide” for Predicting Return on Investment for PPM explains that companies are frequently challenged when they are required to develop a credible, supportable financial model to determine the benefits of PPM initiatives. This “Issue in Focus” is intended to help guide companies in developing…
The Business Value of Innovation in Manufacturing
Jim Brown joined McGladrey to share his thoughts on the business value of innovation, the complexity of global manufacturing, and how ERP and PLM solutions can help. View the webinar replay.
The Five Degrees of Product Complexity
Jim Brown presents on this webcast sponsored by Siemens PLM. The presentation examines how manufacturers address the five critical dimensions of product complexity to achieve maximum profitability, and how Product Lifecycle Management (PLM) solutions help manage these five dimensions of product complexity on an enterprise scale, resulting in greater efficiency and better products. Complexities addressed…
Innovating in Consumer Goods without Buckling under Compliance Pressures
Tech-Clarity, Inc. President Jim Brown, joins a Consumer Goods Technology webcast and Dr. John Sottery of Dassault Systemes on this web presentation, Increase the Velocity of Value Creation in Your Organization. Jim will share his perspective on how companies can develop highly innovative products in shorter time through the use of best practices and PLM…
Streamlining Product Documentation and Raising the Bar with 3D Communication
Jim Brown presented with Garth Coleman of Dassault Systemes on a IndustryWeek webinar, Streamlining Product Documentation and Raising the Bar with 3D Communication. The webinar shared Tech-Clarity research on how to use 3D product communications to improve efficiency, time to market, quality, cost, and customer experience. Click the title to see the recorded webcast. Registration…