Howie Markson is the Director of Research for Digital Innovation at Tech-Clarity, where he covers digital innovation across product design, simulation, PLM, PDM, SLM, IoT, AI, and other product development solutions for manufacturing and industrial companies. Howie has over 25 years’ experience as an engineer, software product manager, and technology marketing professional. He brings a…
- The impact of high expectations and high unpredictability on businesses.
- How companies are coping with labor shortages, and the role culture and continuous improvement can play.
- What technology underpinnings or architecture WMS needs to not only accommodate, but foster constant improvement and beneficial change.
- The role of automation in today’s warehouses and how it integrates to the WMS, including ASRS, conveyors, AIVs, and AMRs.
- What a partnership between a company and its software provider can and should be to sustain and deepen value over time.
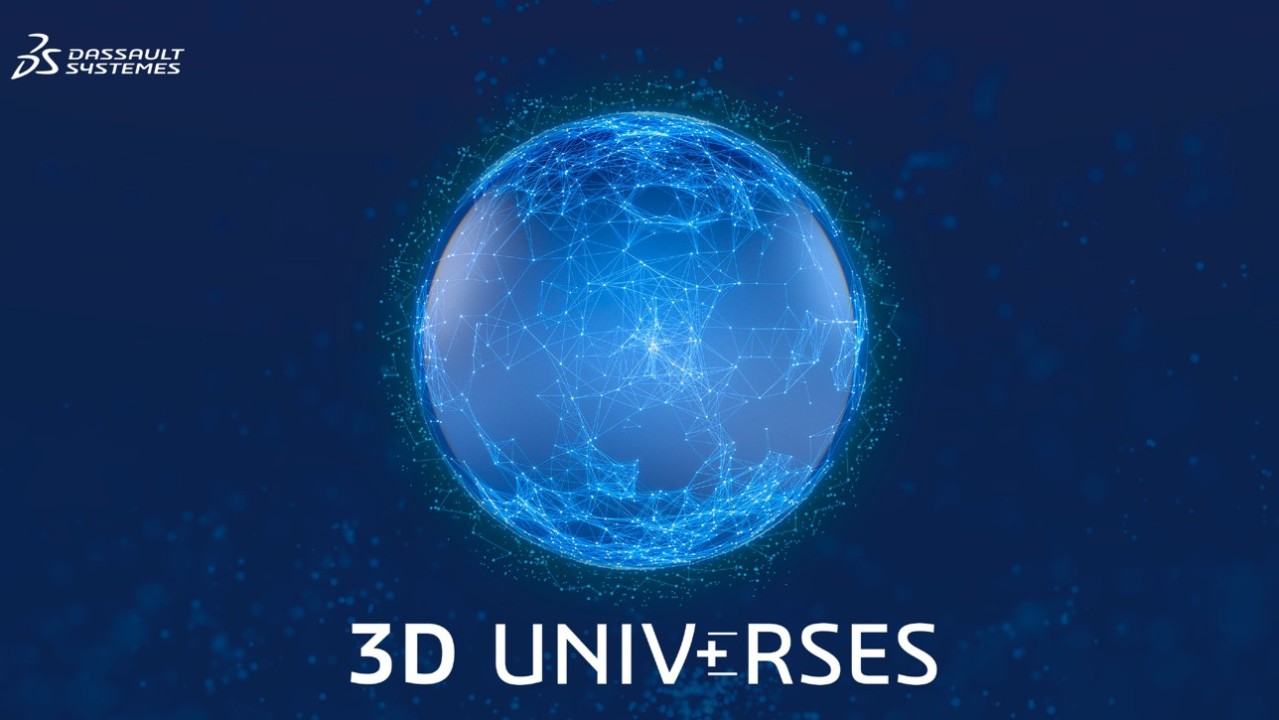
Dassault Systèmes’ Strategic Evolution
We recently had the opportunity to attend an invitation-only analyst event in Paris. The event offered general updates on the Dassault Systèmes business, brand news, and industry experiences. Some of the most important discussions, however, revolved around their new business strategy. Although the strategy was announced earlier this year, this was our first chance to hear about it in more detail from Dassault Systèmes leadership, including CEO Pascal Daloz.
This is not the first time we’ve been introduced to one of their visionary shifts. Dassault Systèmes intentionally reinvents themselves about every seven years. The path has taken them from their 3D modeling roots to their current, much broader role in the industry. Today, that includes much more than mechanical design, encompassing “product, nature, and life,” including significant focus on life sciences. The company takes this process seriously, following a forward-looking, structured process to go beyond what their customers are asking for today and setting their sights on what they believe their customers will need in the future. The graphic below highlights the transitions along their 40+ year journey.
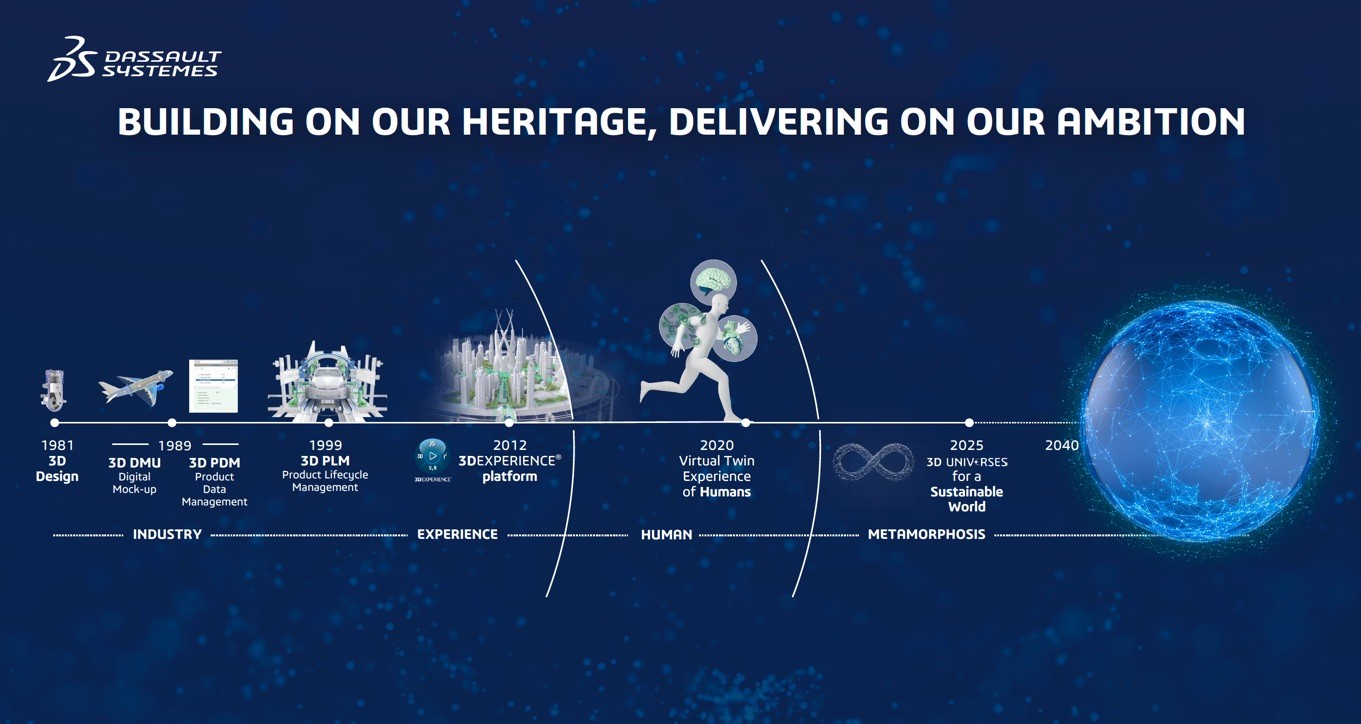
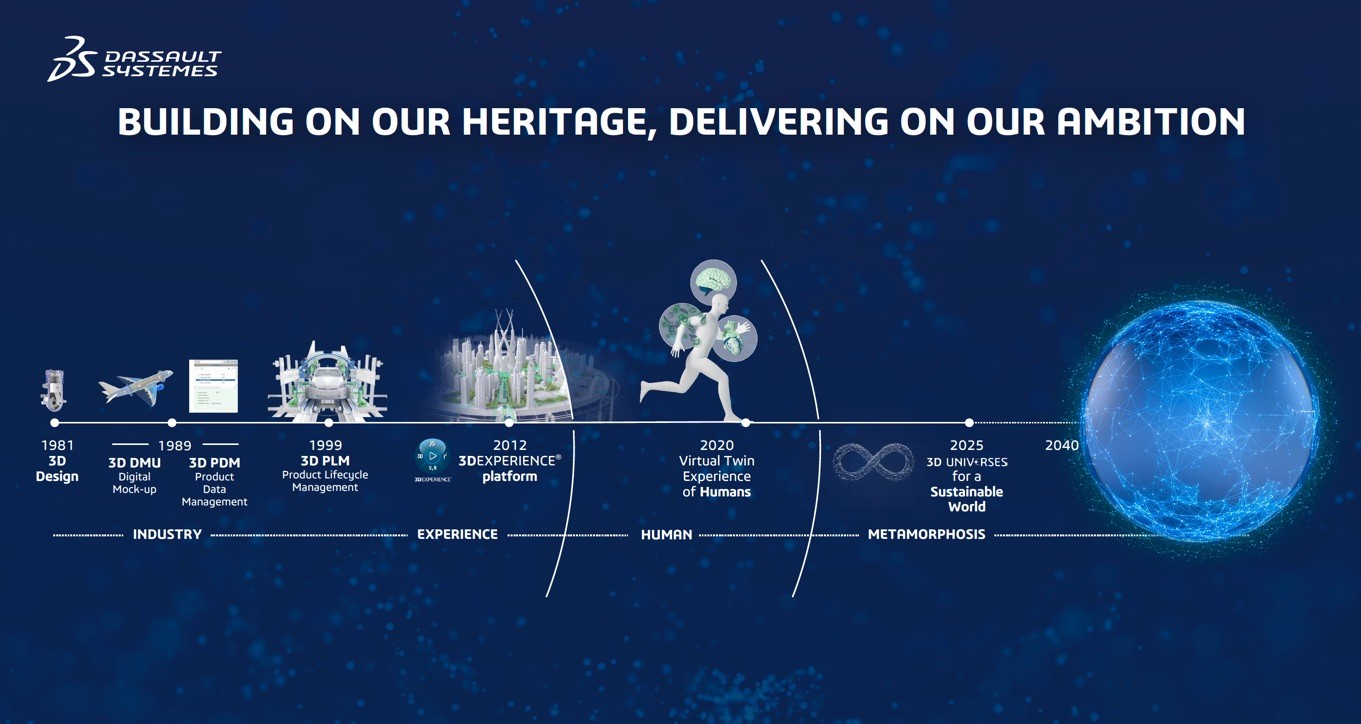
We expect this announcement to receive a mixed reception from customers. Dassault Systèmes is not afraid to be a little ahead of their customers. We distinctly remember the unveiling of the 3D Experience vision. The strategy was met with a combination of reactions, with many customers more focused on what they need from their products today. But Dassault Systèmes’ view of “V+R” combining virtual and reality was prescient and led them down the path to a robust collection of digital twins, what they call “virtual twins,” which connect the virtual, model-based reality with the physical reality. At the same time, they have transitioned from an engineering software company to a “scientific company.” This furthers their ability to add value in traditional industries but also frees them to continue to grow in other realms including life sciences.
3D UNIV+RSES
The new strategy, 3D UNIV+RSES, builds on Dassault Systèmes’ strengths. They see the strategy, which is pronounced as “3D Universes,” as recreating themselves for what they see as the “generative economy,” where “IP is the new currency.” The goal is no longer to stop at representing the real world virtually, but begin to generate it. This requires a strong combination of modeling, simulation, and AI.
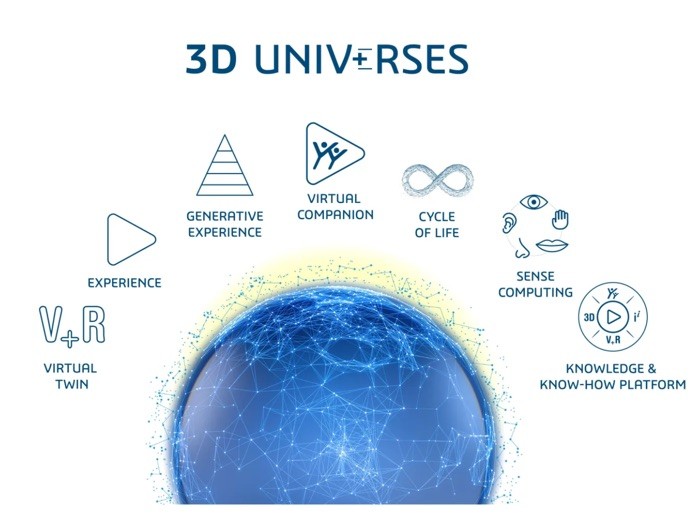
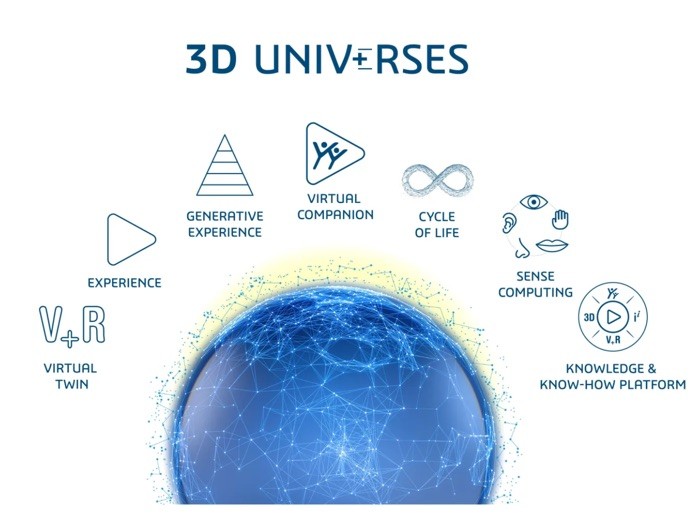
EVP Industry, Marketing & Sustainability, Corporate Strategy & Platform Transformation Elisa Prisner-Levyne shared details of the strategy. She explained that representative modeling will give way to living virtual models that learn and evolve over time. This continued connection between the virtual and real leverages their position as a scientific company and their industrial knowledge and knowhow. The goal is to create a feedback loop so that each experience generates new knowledge.
To deliver this solution, they no longer see themselves as just a software company. Instead, they are now positioning themselves as “The Industry Trusted IP Generation & Management Company.” This is intentional to recognize the growing value of intellectual property, including both physical and digital knowledge. This focus on IP brings significant focus on cybersecurity and sovereignty, key factors to support corporate knowledge and knowhow which are high business priorities according to our research on long-term business success. Further, they are moving beyond the term Product Lifecycle Management (PLM) to IP Lifecycle Management (IPLM), reflecting their vision to protect and master IP on their platform.
They have unveiled their vision for 3D UNIV+RSES, comprised of seven pillars supported by the 3DEXPERIENCE Platform:
- Virtual twin
- EXPERIENCE
- Generative Experience
- Virtual Companion
- Cycle of life
- Sense computing
- Knowledge and Know-how Platform
These pillars are designed to help Dassault Systèmes’ clients create “Generative V+R Experiences” by leveraging AI built for Industries. This strategy relies heavily on the transition of computing to incorporate more artificial intelligence, and Dassault Systèmes is making significant investments in that direction.
Dassault Systèmes is Investing in Industry-Savvy AI
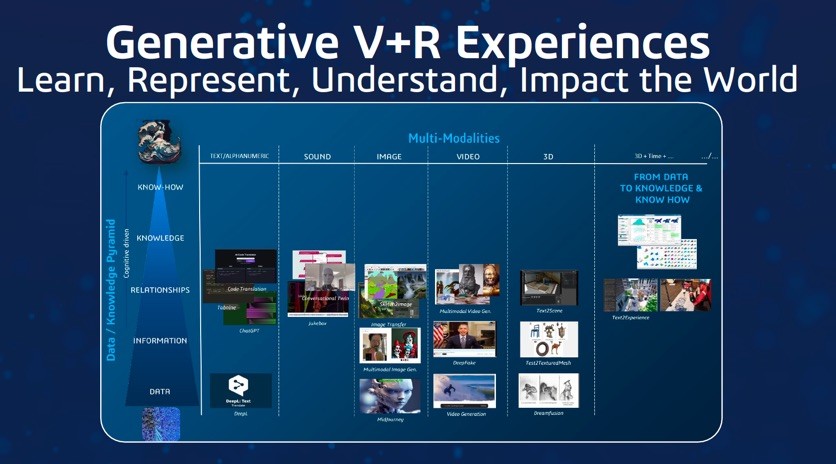
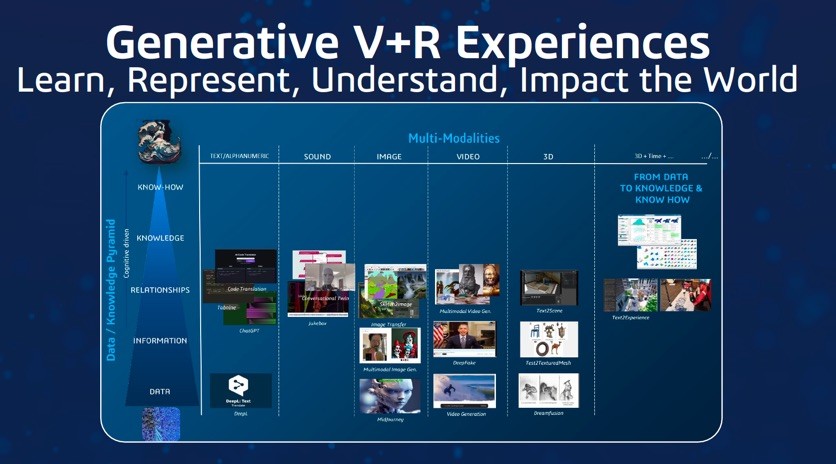
A key enabler for 3D UNIV+RSES is AI. EVP Research & Development Florence Hu shared more details on Dassault Systèmes’ plans in this area. She explained that the AI they deliver will include:
- Trustable Generativity
- Science-based Technologies
- Industry AI-Operations
They also plan for their approach, “AI for Industries,” to be trustable, secure, and sovereign. This is essential in today’s current environment. They will do this by hosting AI on their own sovereign cloud.
Dassault Systèmes plans to roll out AI to complement humans, not substitute for them, with virtual companions. Florence provided several examples of “Industry Companions,” including a regulatory companion that can generatively compile data from documents, powered by AI. She explained that companions will be heavily specialized on tasks and rolled out in waves across all brands. The companion introduction will start with companions that assist and teach, will then expand to those that work with company employees, and expand to agents that actively orchestrate and organize information and processes. In other words, “Help me, teach me, do it for me.”
EVP Corporate Research and Sciences Patrick Jonhson furthered the discussion by discussing how they plan to elevate generative AI to generate industrial grade knowledge and knowhow by creating generative V+R Experiences. Not only will Dassault Systèmes use leading commercially available models, they will also create their own industrial models based on 3DS ontologies built from over 30 years of industrial experience across industries. To do this, they plan to leverage the customer industrial corpus (data). They explained that customers own their data, which will be protected, while Dassault Systèmes will leverage the ontology, for example data packaged in roles, available as metadata separate from customer data. They will maintain a lineage graph on any process, such as a learning or combining processes, to trace the information AI is leveraging
When we asked how much of the AI progress we’ve seen demonstrated is available and adopted, they said that it has “already started in 2025.”
More Than We Can Share
Although the event is only two days, there is always much more presented than we have time to share. Dassault Systèmes brought together leaders from across their brands and industries to share great customer stories, including traditional manufacturing customers like Volkswagen Group, Renault Group, and Airbus. They also highlighted Enterprise, Architecture, and Construction (EAC) customers EDF Hinkley Point C, a nuclear facility, and MINERVE for train stations. AEC is a targeted growth area for Dassault Systèmes with significant room for expansion. They also shared stories from Life Sciences companies, including Precision Therapies and Sanofi, showcasing the success of their acquisitions that furthered prior strategies beyond manufacturing to product, nature, and life, where they now have a leadership position.
Dassault Systèmes also announced that they are moving beyond software delivery to work directly with companies. They are delivering what they call “V+R Consulting,” a consulting practice toward generative. Beyond generative work, we also heard examples of scientific work done collaboratively between Dassault Systèmes and customers, showing their willingness to engage to further knowledge and knowhow.
We should also mention that Group CFO Dr. Rouven B. shared impressive financial updates, showing continued growth in subscription, cloud adoption, and 3DEXPERIENCE revenue. One of the most surprising statements he made is that he sees an incremental revenue opportunity of 1 billion euros over the next five years as AI brings “pull through” for 3DEXPERIENCE and the cloud.
Our Take
We realize that these visions are sometimes hard to digest and will require time for customers to understand how it will impact the products and services they rely on Dassault Systèmes for. But the direction is compelling, and we’re excited about what they are doing next. We look forward to seeing them continue to exploit a broader view than their peers in the industry, serving three distinct sectors; Manufacturing, Life Sciences & Healthcare, and Infrastructure & Cities.
We look forward to IP Lifecycle management supporting knowledge and knowhow in addition to products and services with robust cybersecurity and sovereignty, generative experiences supporting the industrial metaverse, and their major investments in AI intended to deliver a trusted environment for industrial AI through the combination of 3DEXPERIENCE and 3D UNIV+RSES. We look forward to following their progress.
Thank You
Dassault Systèmes invests a lot of effort and their executives’ time to make sure analysts understand their strategy. Always a pleasure to reconnect with Pascal Daloz and his team, and it was a nice surprise to enjoy a special appearance by former CEO and current Executive Chairman Bernard Charles.Thank you Joe Horine, Kurt Chen, and the rest of the analyst and events team for the invitation and for putting on an excellent event.
[post_title] => Dassault Systèmes Shares Updated Strategy: 3D UNIV+RSES [post_excerpt] => [post_status] => publish [comment_status] => open [ping_status] => open [post_password] => [post_name] => 3d-univrses [to_ping] => [pinged] => [post_modified] => 2025-08-08 16:47:25 [post_modified_gmt] => 2025-08-08 20:47:25 [post_content_filtered] => [post_parent] => 0 [guid] => https://tech-clarity.com/?p=22438 [menu_order] => 0 [post_type] => post [post_mime_type] => [comment_count] => 0 [filter] => raw ) [3] => WP_Post Object ( [ID] => 22349 [post_author] => 2574 [post_date] => 2025-07-24 13:26:10 [post_date_gmt] => 2025-07-24 17:26:10 [post_content] =>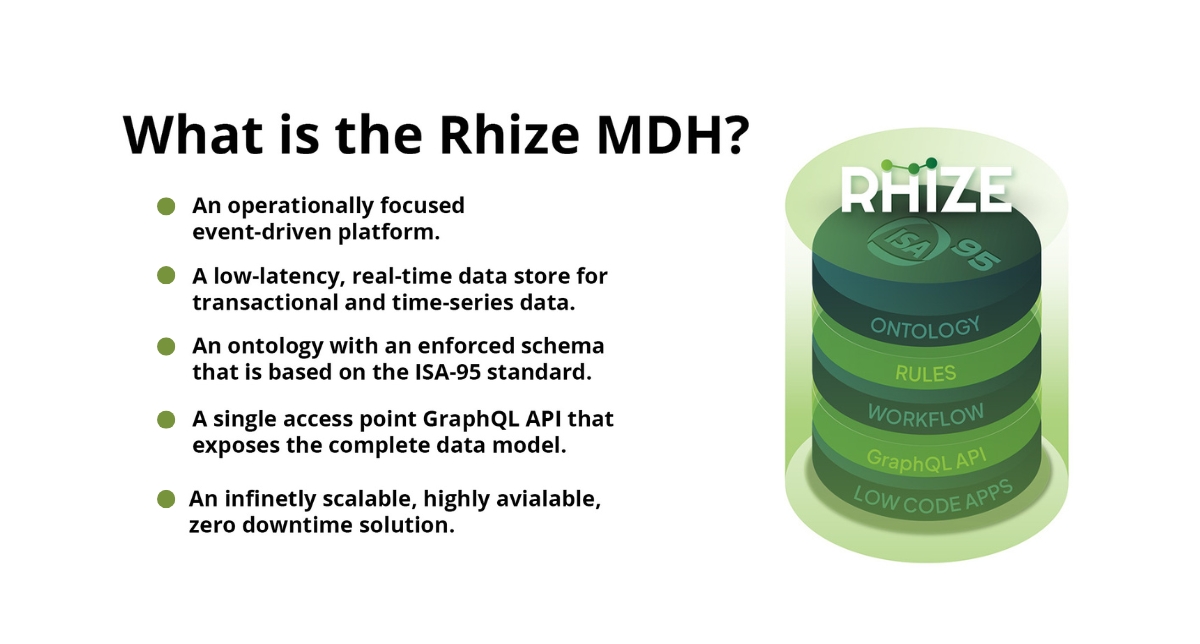
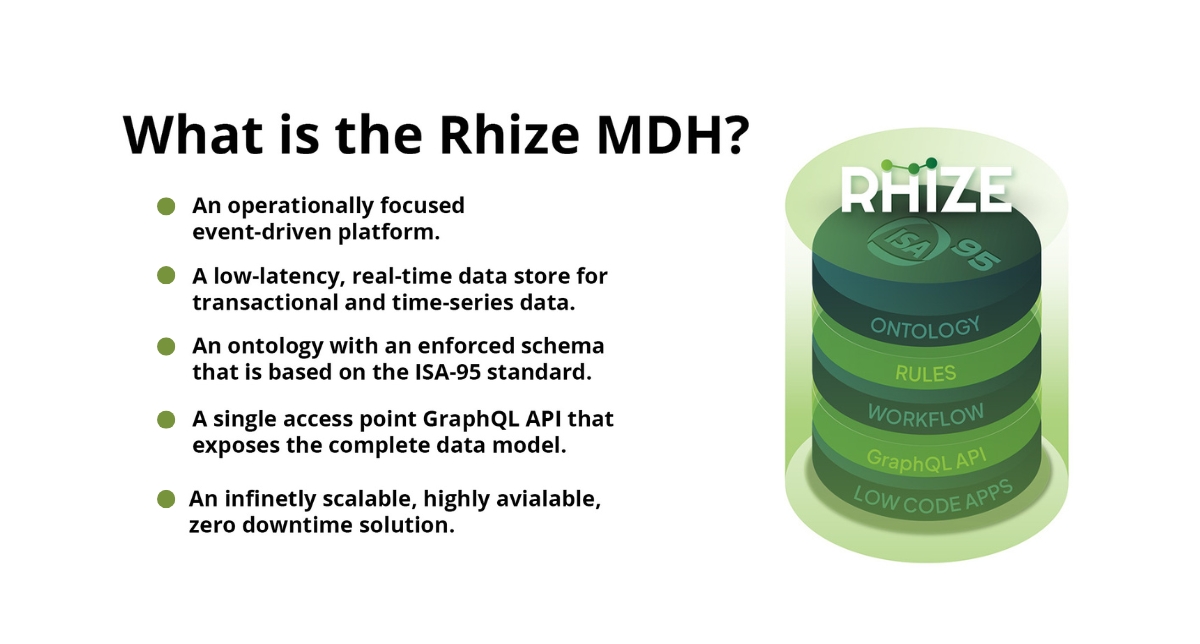
Manufacturing Data Hub
So, what is this Rhize Manufacturing Data Hub (MDH)? The MDH includes the ISA-95-based ontology, model and transactional storage (graph) and time-series storage, complex rules processing, a workflow engine for modeling, and a single access point GraphQL API.
It is a headless manufacturing system, meaning that applications are built via access to the GraphQL API and Workflow Engine. By converting all incoming operational data to comply with the ISA-95 schema, the platform acts as a Rosetta Stone for the existing disparate data models. ISA95 defines how to model and structure entities and the relationships between them for optimal interoperability.
Every system (MES, ERP, CMMS, DCS, Historian, etc.) can connect to this hub. The hub will convert that data into the MDH standard and insert it into the knowledge graph with its properties and myriad relationships.
The goal is to avoid the common problem of managing manufacturing data and processes across disparate systems with their own databases and structures. An ontology is a complete description of a domain that shows the properties and relationships between every piece of data. With the diversity and interconnectedness of equipment, personnel, and material data, this is no mean feat in manufacturing.
These are often not just parent-child or simple relationships, and the MDH ontology can represent them accurately using the ISA95 elements. Each entity exists only once in the MDH, making it truly a “single source of truth.”
The Foundational Digital Transformation Challenge
Our research shows that Rhize’s declaration that “data modeling and governance are the root of every problem for digital transformation” is correct for the technology. (We feel it ignores some crucial people and process issues.) To overcome this, Rhize has created a standard data model with an API to ingest and convert data from any source into a comprehensive ontology. With this structured approach stored and exposed as a knowledge graph, Rhize aims to make data mismatches, IT/OT disconnects, and dirty data issues problems of the past for its customers.
This also addresses a challenge companies face with AI: getting high-quality in-context data for data scientists. The number one challenge companies face is their data for AI and analytics projects, so this is excellent news for continuing rapid adoption and benefits from AI for large manufacturers.
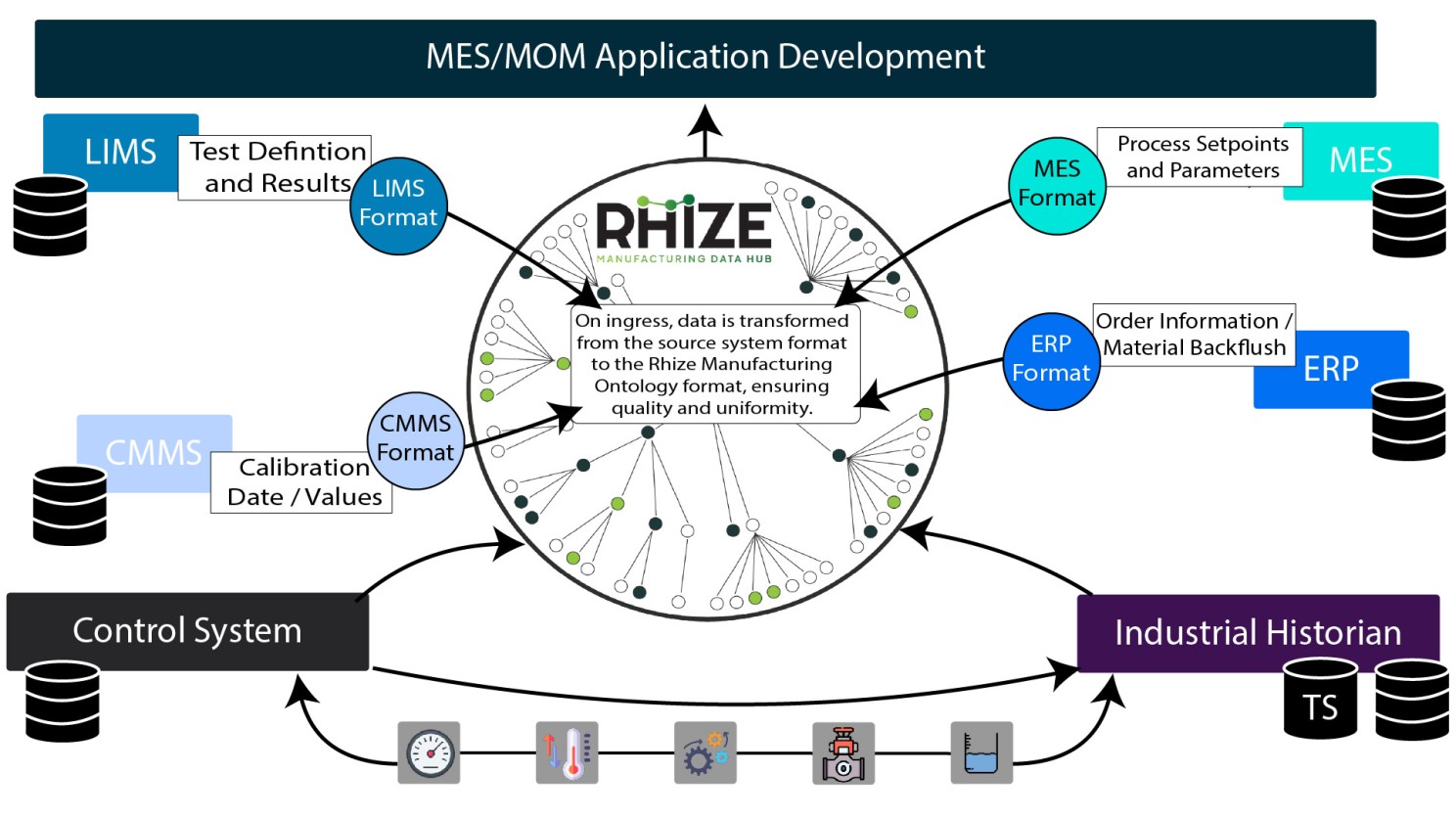
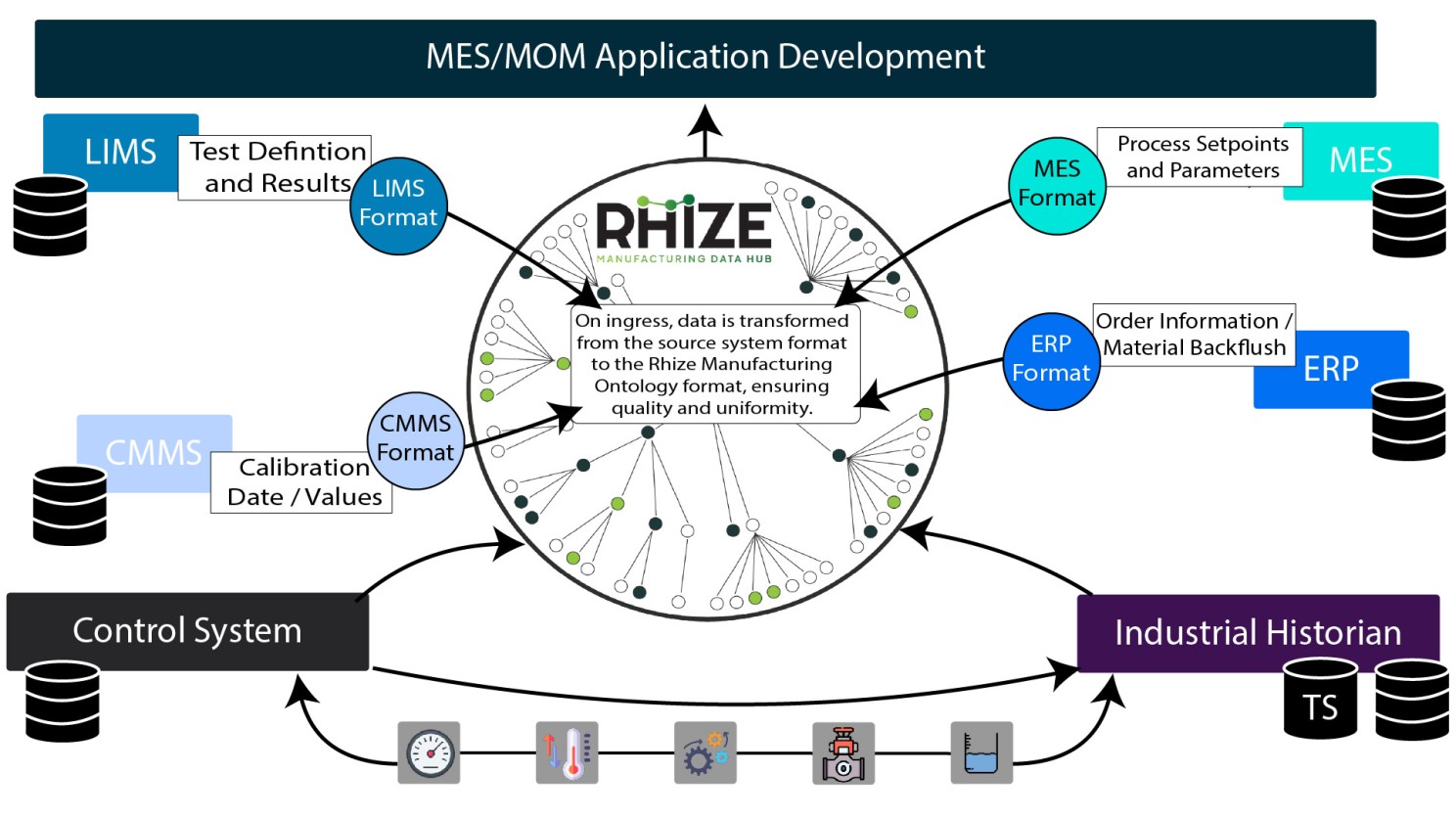
Addressing Other Challenges
In addition to that foundational issue, the MDH can do more.
- Replace MES/MOM when it becomes outdated or unsupported. Rhize MDH enables companies to replace MES and MOM applications incrementally using an approach called the Strangler-Fig method. No rip and replace of systems is required.
- Overcome data and discipline siloes for better and easier data context. With this Rosetta Stone, each discipline can keep its systems and still agree on a single source of truth.
- Solve specific intractable problems. Rhize customers have tackled initial use cases that have been nagging issues that previous approaches could not solve.
- Expanding use cases rapidly across a large enterprise with multiple sites. MDH customers are deploying multiple functional capabilities simultaneously across one site and multiple sites, using an iterative process call “use case stacking.”
- Leveraging existing data relationships for new applications. The central ontology means that each new application can build on the previously defined data and relationships.
Leveraging Standards
Rhize has developed its MDH with standards at the core, including not only ISA95 but also BPMN for business process model notation, GraphQL API for exposing the knowledge graph in a natively introspective way, and MQTT and OPC UA for OT input.
At the heart of the Rhize manufacturing data hub is the ISA95 model. The dozens of manufacturing experts who created the ISA95 standard crafted a model that recognizes and enables a plant or company to model the environment precisely. People are arguing that it’s obsolete, but that may be because it is often shown layered on the Purdue 5-layer model, which is not an inherent part of the standard. Rhize has not yet encountered a use case that the ISA95 ontology could not accurately model.
Technology Basis
Other industries, like banking, have used headless data backends to drive digital transformation, separating applications and interfaces from data structures. MDH does that. Uniquely crucial for manufacturing, it handles both event-driven and time-series data.
All of this is stored in a knowledge graph. This ensures semantics, context, and data integration with many bi-directional relationships (known as edges in a knowledge graph). Whether IT or OT data, MDH is intended to be the translator or Rosetta Stone.
A drag-and-drop workflow engine sits on top of the graph but inside the MDH. Composable process modeling using the BPMN standard is crucial to the capabilities. MDH also uses a low-code approach to workflow and business process modeling.
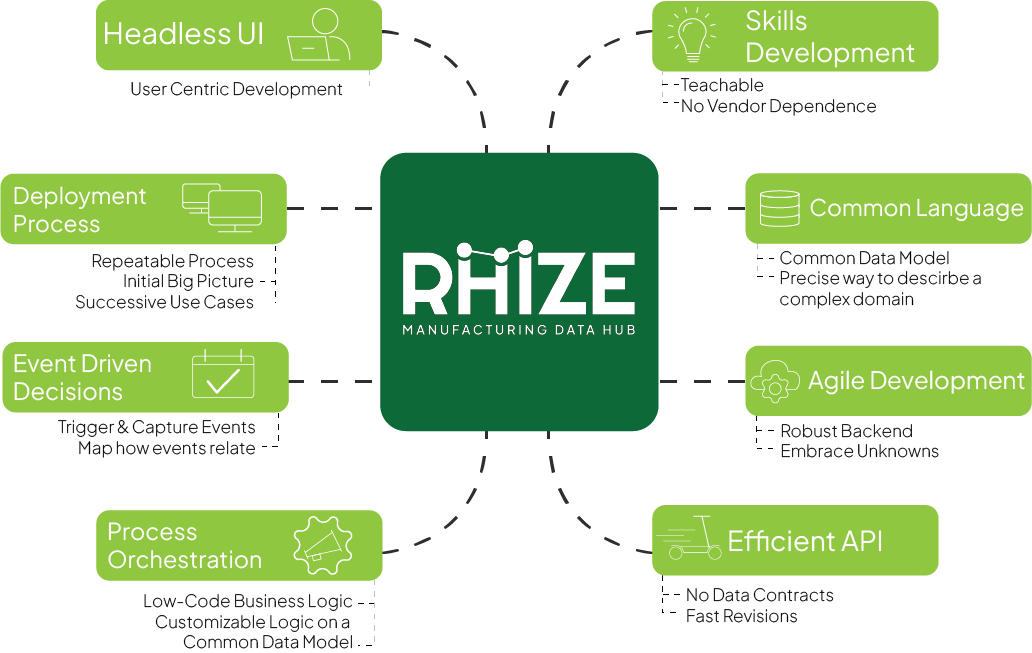
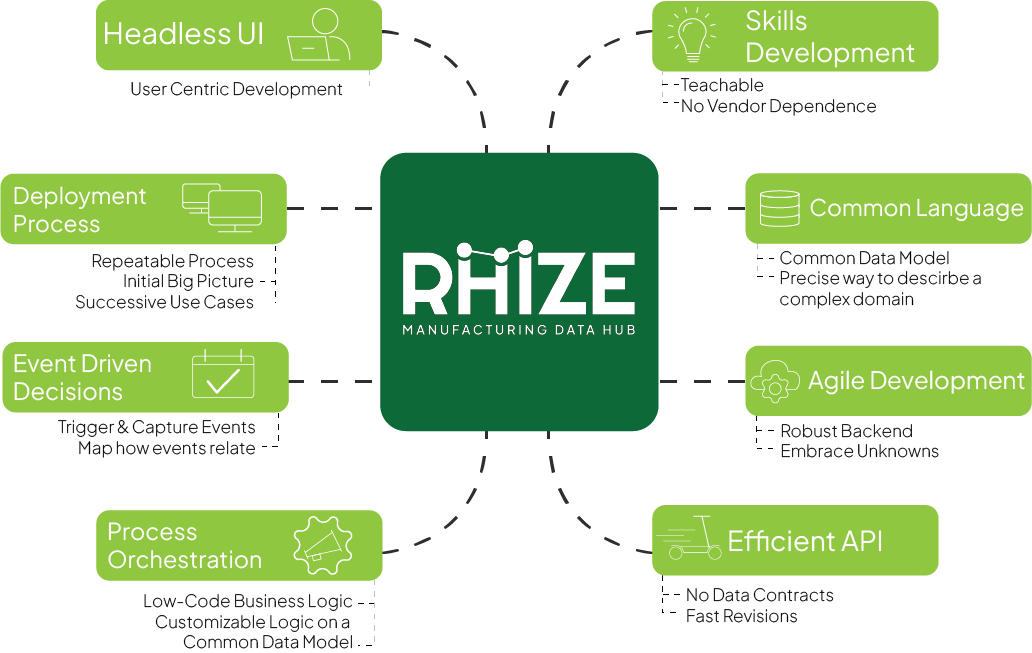
Target Market
Rhize MDH will be most useful in the hands of large, enterprise-scale manufacturers. The criteria for their target customers include having:
- Multi-site (10+ is ideal)
- Multiple failed MES/MOM implementations
- Highly technically skilled and curious personnel
- Executive backing for a long-term program (often 3-5 years)
- An understanding and commitment to an ontological approach
Watching for Breakthroughs
Rhize says, “To be successful in an enterprise digital transformation and to enable innovation at scale, you must be able to iterate." We agree. The MDH combination of graph backend, enforced ISA95 schema, ability to develop apps accessing the data via APIs, and composable workflow could do just that. We believe it could facilitate new levels of digitalization and MES longevity in many manufacturing environments.
Thank you, Kirt Anderson, for explaining the Rhize Manufacturing Data Hub offering. We look forward to following your progress in the market.
[post_title] => Rhize Enables Enterprise Digital Transformation with Ontology-Based Data Hub [post_excerpt] => [post_status] => publish [comment_status] => open [ping_status] => open [post_password] => [post_name] => manufacturing-data-hub [to_ping] => [pinged] => [post_modified] => 2025-07-24 13:27:10 [post_modified_gmt] => 2025-07-24 17:27:10 [post_content_filtered] => [post_parent] => 0 [guid] => https://tech-clarity.com/?p=22349 [menu_order] => 0 [post_type] => post [post_mime_type] => [comment_count] => 0 [filter] => raw ) [4] => WP_Post Object ( [ID] => 22217 [post_author] => 2574 [post_date] => 2025-07-23 21:13:26 [post_date_gmt] => 2025-07-24 01:13:26 [post_content] =>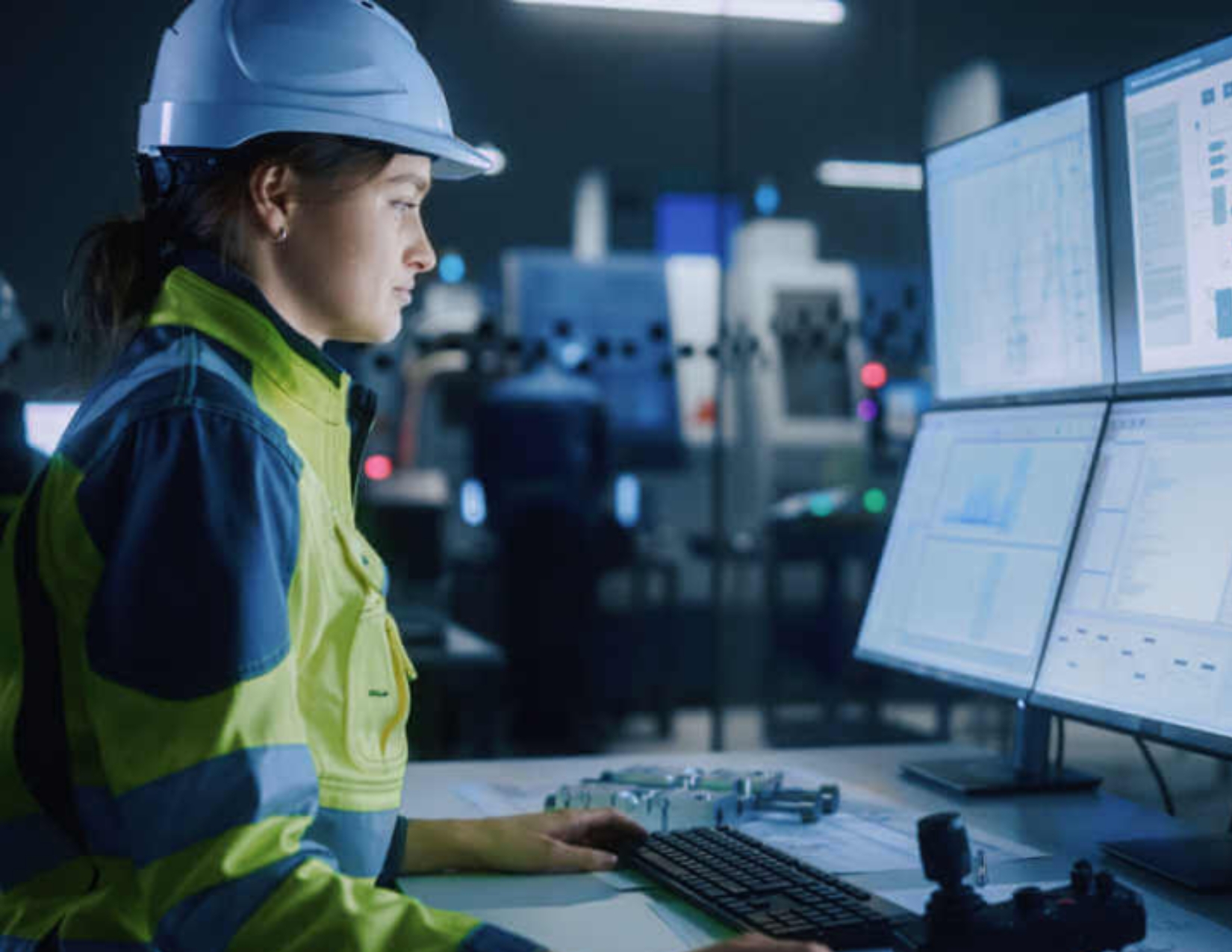
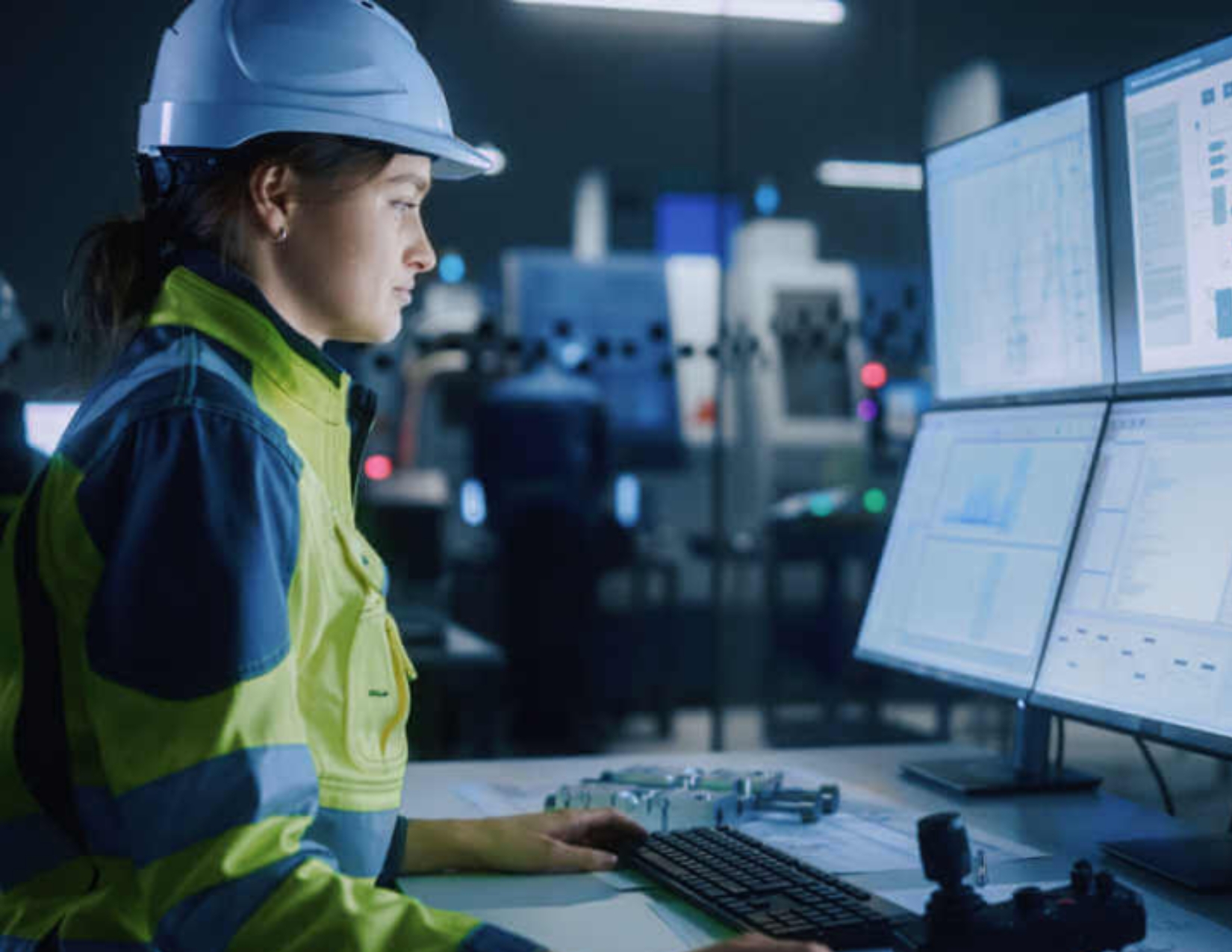
Brain of MES Summary
Manufacturers must separate GenAI’s promise from reality, confront cultural resistance, and stay focused on collective intelligence if they want their MES strategy to succeed in the AI era, according to Rick Franzosa. For him, the GenAI conversation is moving dangerously fast, and large sections of the manufacturing world are simply not ready.GenAI Works, People Are Not Ready
The overall message Rick delivered is that there is a gap between expectations and reality for GenAI. It is coming, but right now manufacturers don’t have the foundational capabilities in place. The order must be people first, then, process, data, and technology. Cognitive entrenchment, an unconscious belief that the current way of doing things is the only sensible one, stands in the way. The cure is collective intelligence and collaborative decision-making across disciplines.Data, Agents, and More
Data is a crucial part of the infrastructure for successful AI and MES also. “MES does not fail because the software does not work,” Franzosa explains. “It fails because the data is inconsistent, irrelevant, or siloed. That is not a technology problem. It is a leadership problem.” Agentic AI is already proving useful, but Franzosa also warned that human-in-the-loop will be important for some time. He does not believe agentic AI will replace MES, but rather that they will evolve together. Above all, he also believes that human intelligence, creative, imaginative, and interpretative, will remain the brain of MES. Leaders have an opportunity to make better decisions, leveraging their data, AI, MES and people.Thank You
Mark picked up much of the content and thrust of the original presentation in this 1500-word article, so those of us who were unable to attend can get the benefit of Rick’s well-researched view of where AI and MES intersect and how AI might be part of the evolution of MES. Thank you to Critical Manufacturing for hosting this event, and Mark Venables of Connected Technology Solutions for the article on the presentation. This is a summary of the CTS article. For the full content, go to the publication’s website. [post_title] => CTS Article on Rick Franzosa’s MES Industry 4.0 Summit Presentation [post_excerpt] => [post_status] => publish [comment_status] => open [ping_status] => open [post_password] => [post_name] => brain-of-mes [to_ping] => [pinged] => [post_modified] => 2025-07-24 08:30:34 [post_modified_gmt] => 2025-07-24 12:30:34 [post_content_filtered] => [post_parent] => 0 [guid] => https://tech-clarity.com/?p=22217 [menu_order] => 0 [post_type] => post [post_mime_type] => [comment_count] => 0 [filter] => raw ) [5] => WP_Post Object ( [ID] => 22286 [post_author] => 2 [post_date] => 2025-07-23 10:00:56 [post_date_gmt] => 2025-07-23 14:00:56 [post_content] =>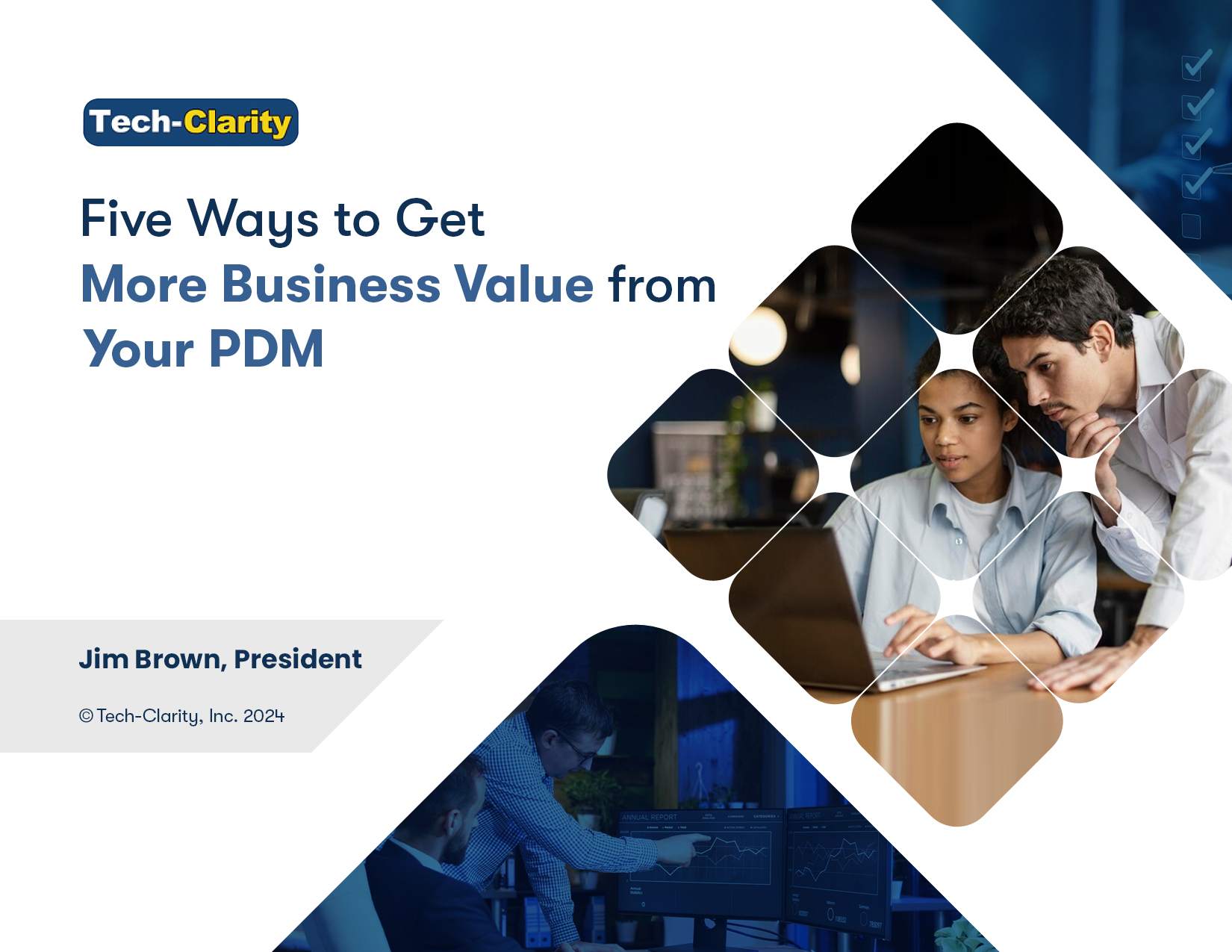
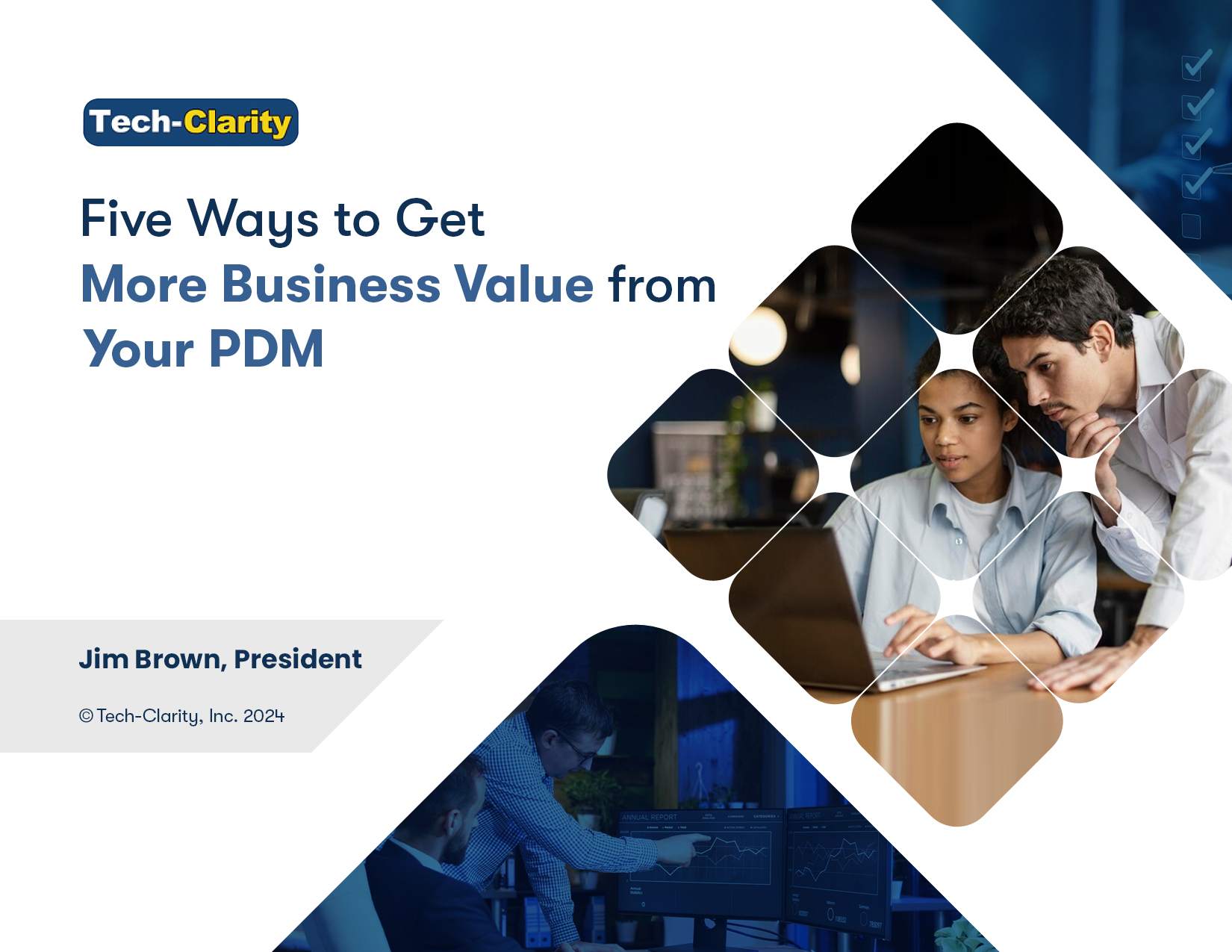
Table of Contents
- Leverage PDM as the Foundation for Greater Value
- Chart a Course to Extend PDM Value with PLM
- Take Advantage of the Basics
- Go Beyond the Basics
- Communicate and Collaborate
- Enrich and Extend
- Review and Release
- Projects and Processes
- Adopt Cloud PLM
- Conclusion / Call to Action
- Acknowledgments
Chart a Course to Extend PDM Value with PLM
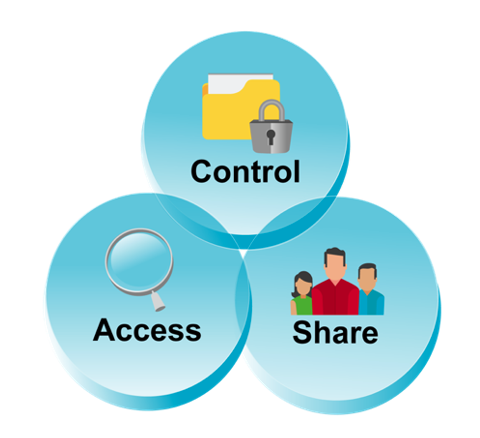
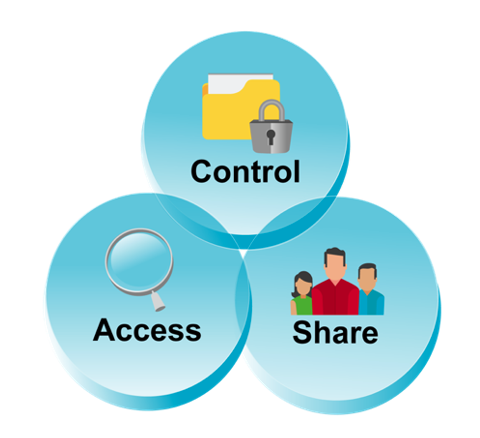
Take Advantage of the Basics
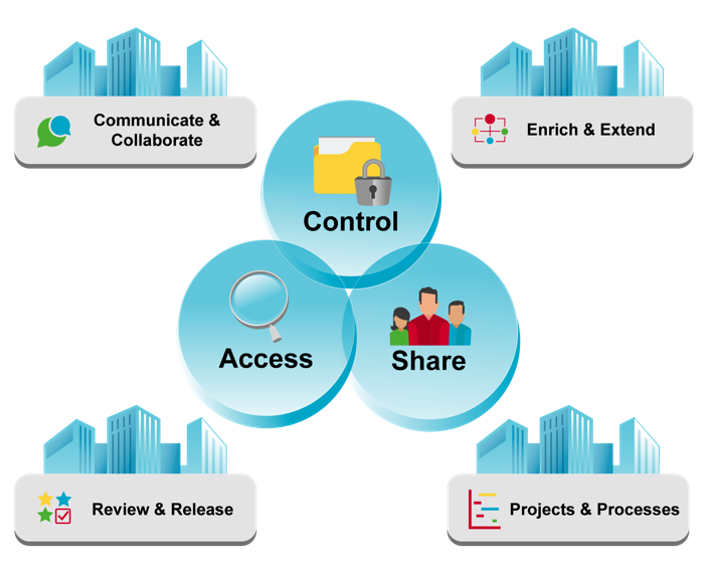
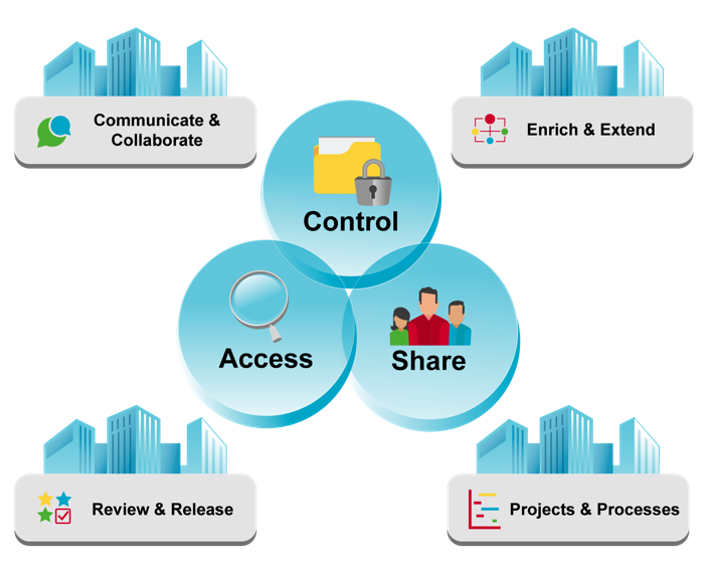
- Controlling CAD files and data to make sure that data is not lost, overwritten, or corrupted
- Providing efficient access to information, allowing engineers to quickly find design files so they can update or reuse them
- Sharing designs with others, typically within Engineering at this stage, so people can work together on different aspects of a product
Go Beyond the Basics
Recognize the Potential Beyond the Basics These core PDM capabilities provide the data backbone for significant improvements. Our research finds four primary ways that manufacturers can extend the value they get from PDM data:- Communicate and collaborate around product data, moving beyond designers to others in the organization and into the supply chain
- Enrich and extend product data to capture a broader view of the product beyond CAD and technical specifications
- Manage processes to review and release design data, including revisions and change management if they aren’t already in place
- Expand scope to include processes and projects to coordinate design and product development efforts in a broader context
Communicate and Collaborate
Improve and Extend Collaboration Many companies start their PDM journey because they need to control data. They face overwritten files or revision control problems that result in lost work or version conflicts. However, the data in PDM is the heart of the design and product development process and is far more valuable as it is shared. Companies typically start by collaborating inside the Engineering department. This helps multiple designers coordinate their work, for example on a multi-part assembly. They may also extend collaboration by connecting engineering organizations across design disciplines, locations, or product lines. Companies get more value as they share PDM data beyond Engineering further into the enterprise to those who need product information to do their jobs. Sharing data from PDM ensures everyone is working on the most recent information and nobody is waiting for someone to gather and send them the data they need. It also prevents people from interrupting engineers whenever they’re looking for a product image or a design specification. Further, setting this data up for self-service allows engineers to focus on engineering instead of spending non-value-added time preparing data for others. Potential Focus Areas Where should companies start getting more collaboration value with PLM? One approach is sharing designs with Manufacturing and Sourcing so they can get a jump start on manufacturing and vendor selection. They can start by automating the creation of neutral 3D formats on check-in and make them available to others downstream so they can view them without the need for a CAD tool. They can also extend this collaboration to design partners or suppliers that need selective access to product information. In some industries, companies may also choose to share data with regulators for audits or submissions.Enrich and Extend
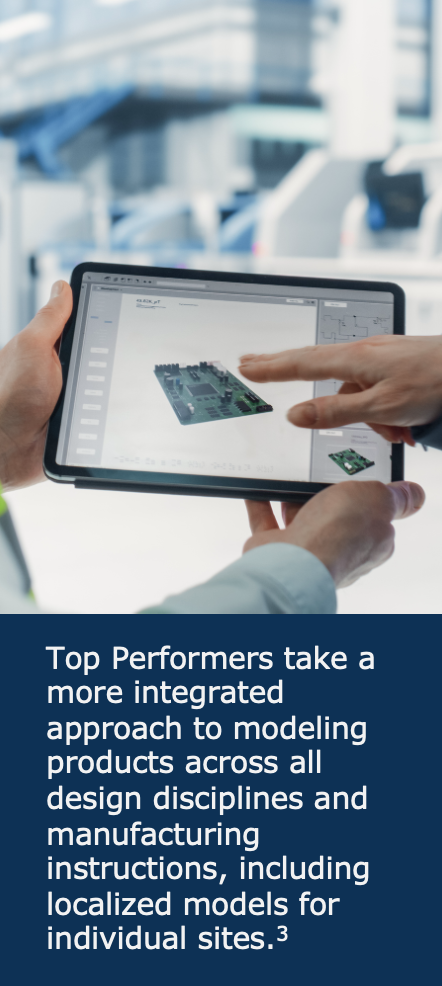
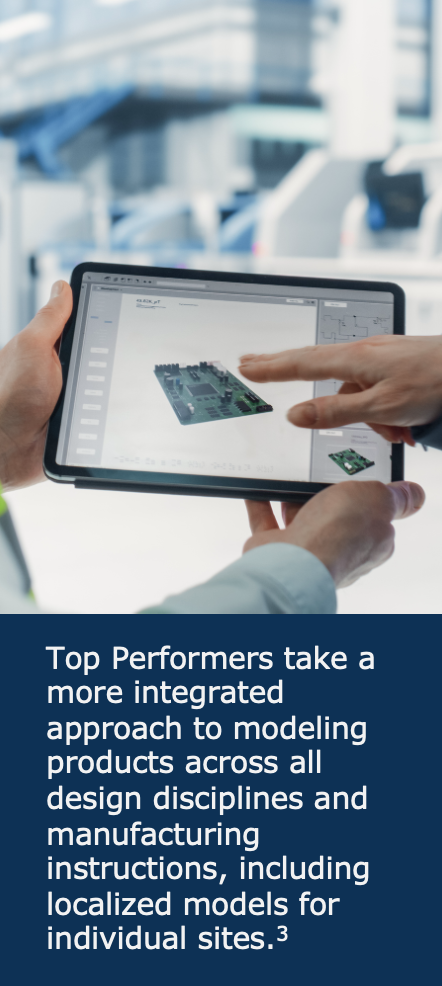
Review and Release
Implement Review and Release Processes in PLM Many companies start by sharing released product data in PDM with a simple, state-based representation of its product lifecycle status. Having a common view of the release state is valuable, but PLM can do more by managing review and release processes themselves.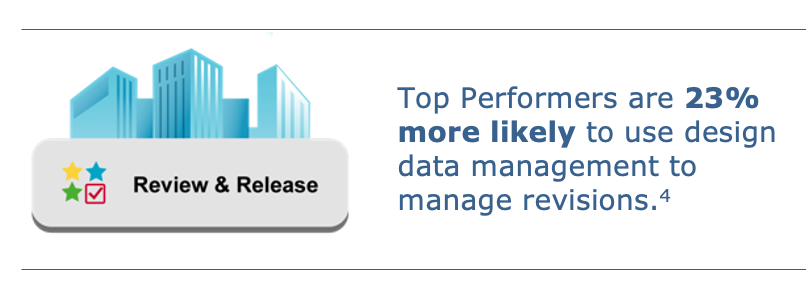
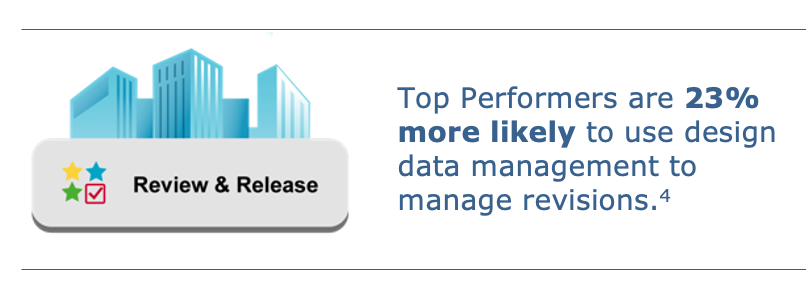
Projects and Processes
Expand the Value of Data with Tasks and Workflows PDM typically starts with data management. As companies expand, they may add some ad-hoc collaboration. The transition from PDM to PLM, however, involves expanding from a data-centric view to one focused on the intersection of data and processes. PLM is designed to help companies implement and execute repeatable, automated digital tasks and workflows. Digital processes can be managed, standardized, enforced, and continuously improved to drive quality and continuous improvement through automation and repeatability. PLM-driven processes can also improve efficiency because digital processes can be contextualized with links to the right PDM data so designers or downstream parties, organization-wide, can immediately take action on them. Managed processes also set the stage to provide visibility and transparent reporting to executives. Workflows can be further enhanced to manage projects and monitor product development processes, projects, and programs. A comprehensive PLM system allows companies to define dependencies and manage activities by role, making sure all activities are sequenced and have resources assigned. It can also provide better coordination across teams, departments, and the supply chain to further improve efficiency and time to market in new product development, or it can be used for other projects like LEAN or continuous improvement efforts. Potential Focus Areas Where should companies start getting more value from PDM by managing processes and projects with PLM? One possibility combines some of the other improvements mentioned above into a more efficient workflow. For example, PLM could automatically route a designer’s changes downstream for review. The PLM system could send the changes to another engineer for a standards review, to Environmental, Health, and Safety (EHS) for compliance and sustainability feedback, to Manufacturing to ensure it can be produced on existing equipment, and to others. Managing tasks with PLM is not only more efficient but the process can be monitored for delays so they can be expedited, for example, if someone is on vacation.Adopt Cloud PLM
Take Advantage of the Cloud Keen observers probably noticed that we only introduced four of the five ways to enhance PDM value with PLM. The fifth is to take advantage of the cloud. Managing product data and processes in the cloud extends the value of PLM to more people across the business and into the supply chain, allowing companies to instantly share the right data, with the right people, in the right context. That’s important because our research shows that 40% of companies waste valuable time because they use outdated or wrong data. Cloud PLM enhances PDM because it allows suppliers, customers, design partners, and others to access the latest information without downloading new applications. Providing cloud data access also enhances security because designs are kept in a secure location instead of being shared through uncontrolled methods like email, and provides a clear audit trail of who accesses which designs and when.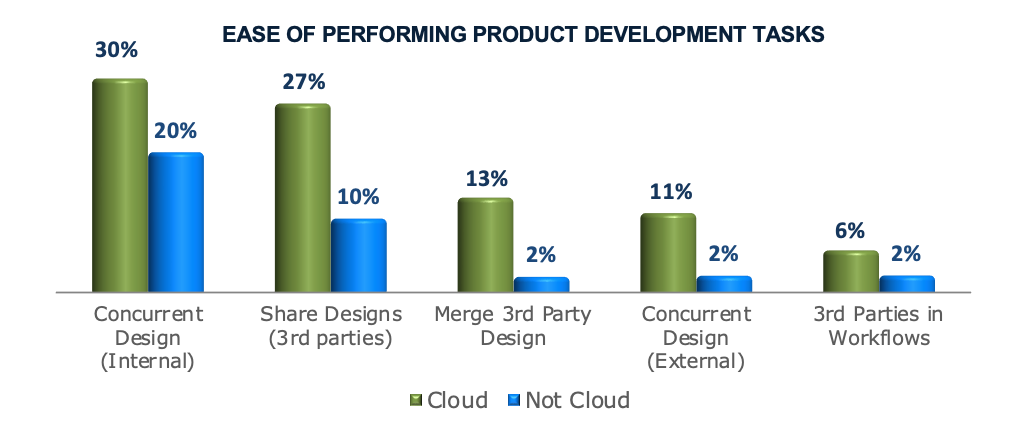
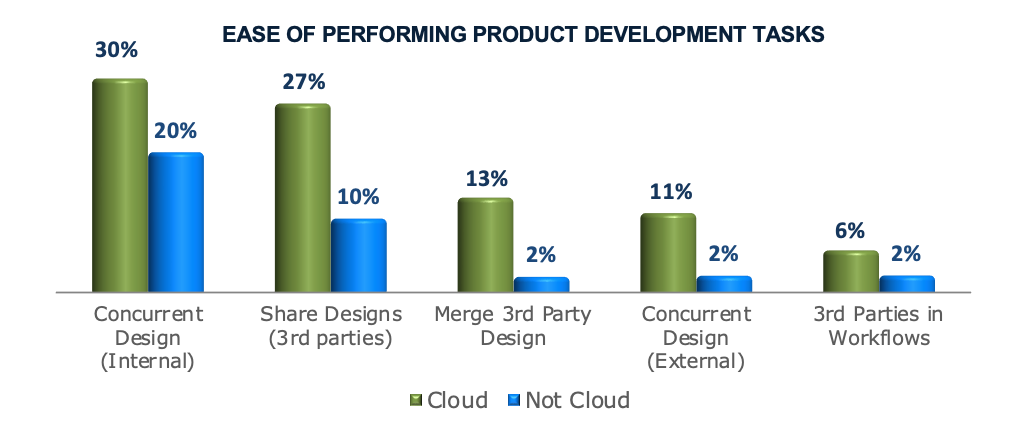
- Implementation benefits like reduced cost and lower barriers to entry
- Operational benefits like improved security and scalability
- Business benefits like supporting digital transformation
Conclusion / Call to Action
Add Strategic Value to PDM PDM provides significant operational value to engineers and their teams. It helps them control, access, and share product information in a trusted, secure way. An effective PDM implementation helps improve engineering and design efficiency, quality, and speed. In addition to PDM, PLM offers the ability to expand value to a broader context including product innovation and new product development. PLM expands PDM value in four functional areas, including:- Extending communication and collaboration
- Enriching product data
- Reviewing and releasing designs
- Managing processes and projects
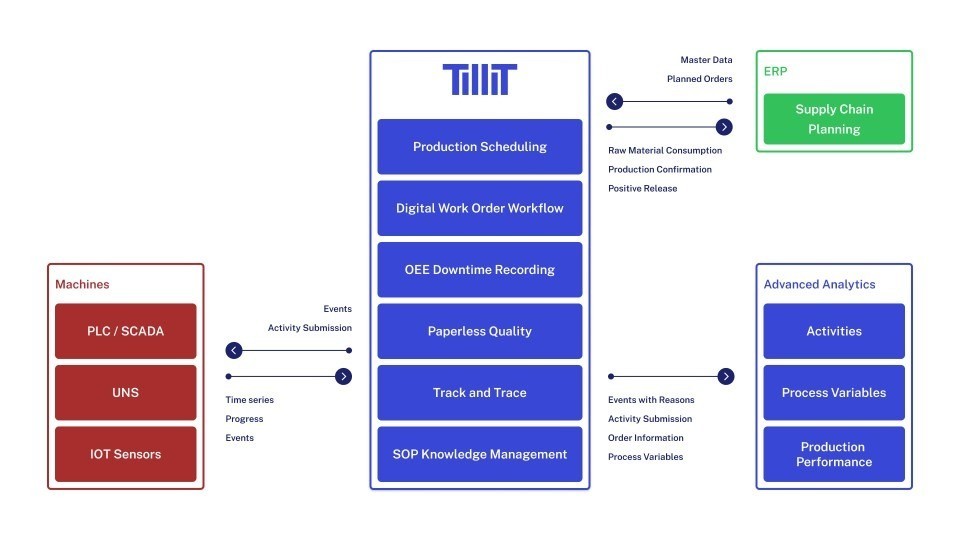
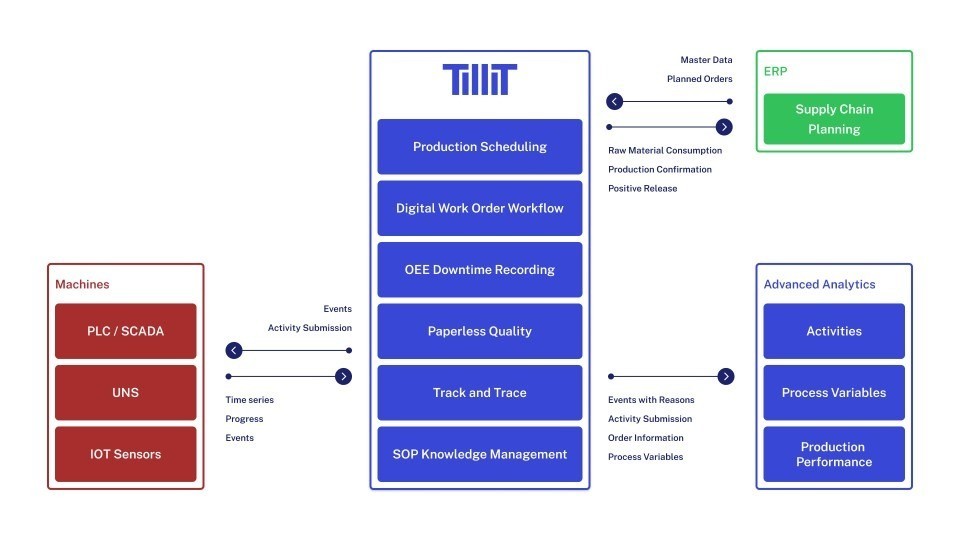
With the June announcement of Australia-based TilliT being acquired by Nordics-based Roima Intelligence, we expect more manufacturers will start to consider this system. Roima has a broad global presence and is growing rapidly, raising its profile for both software and services. TilliT adds digital execution and production scheduling that can deliver value quickly.
MES, Quality, APS, CWP, Analytics
TilliT’s functions include production scheduling, workflow for digital work orders, OEE and downtime recording, paperless quality, track and trace, a mini data historian, and knowledge management, including SOPs. In addition to these capabilities, it includes analytics for activities, process variables, and production performance.
- Quality or auditing is a common entry point into TilliT, leveraging its workflow capabilities.
- Scheduling is designed for multi-step batch or discrete manufacturing operations, but not complex assembly.
- Operators use an action panel that lists tasks and instructions for performing them. The panel can also open forms to ensure process adherence. If something goes wrong, the system can order a root cause analysis.
- Supervisors approve activity as needed.
- A mini data historian is also built-in to show analog trended historized data from sensors and equipment.
The system is designed to orchestrate machines, people, processes, and materials, flowing seamlessly among the functions an operator, engineer, or supervisor needs to perform. While we list functional areas, they do not appear separate to the user.
TilliT was already a merger of two companies, one with MES or digital execution modules and another with AI-based production scheduling. Each of these is still available independently, but is integrated natively. Naturally, the systems also have integration with automation and equipment as well as ERP and SCP.
Event-Driven, Cloud-Based, Low-Code
TilliT is event-driven and based on the concepts of assets, orders, and activities, which the system models and manages in workflows. In these workflows, the project team can work bottom-up to specify automated sets of activities and triggers where and when human interactions are needed. They can also specify expiration times for activities and escalation methods. Using events, triggers, and rules is typically an easy way to record tribal knowledge and create an accurate model of production.
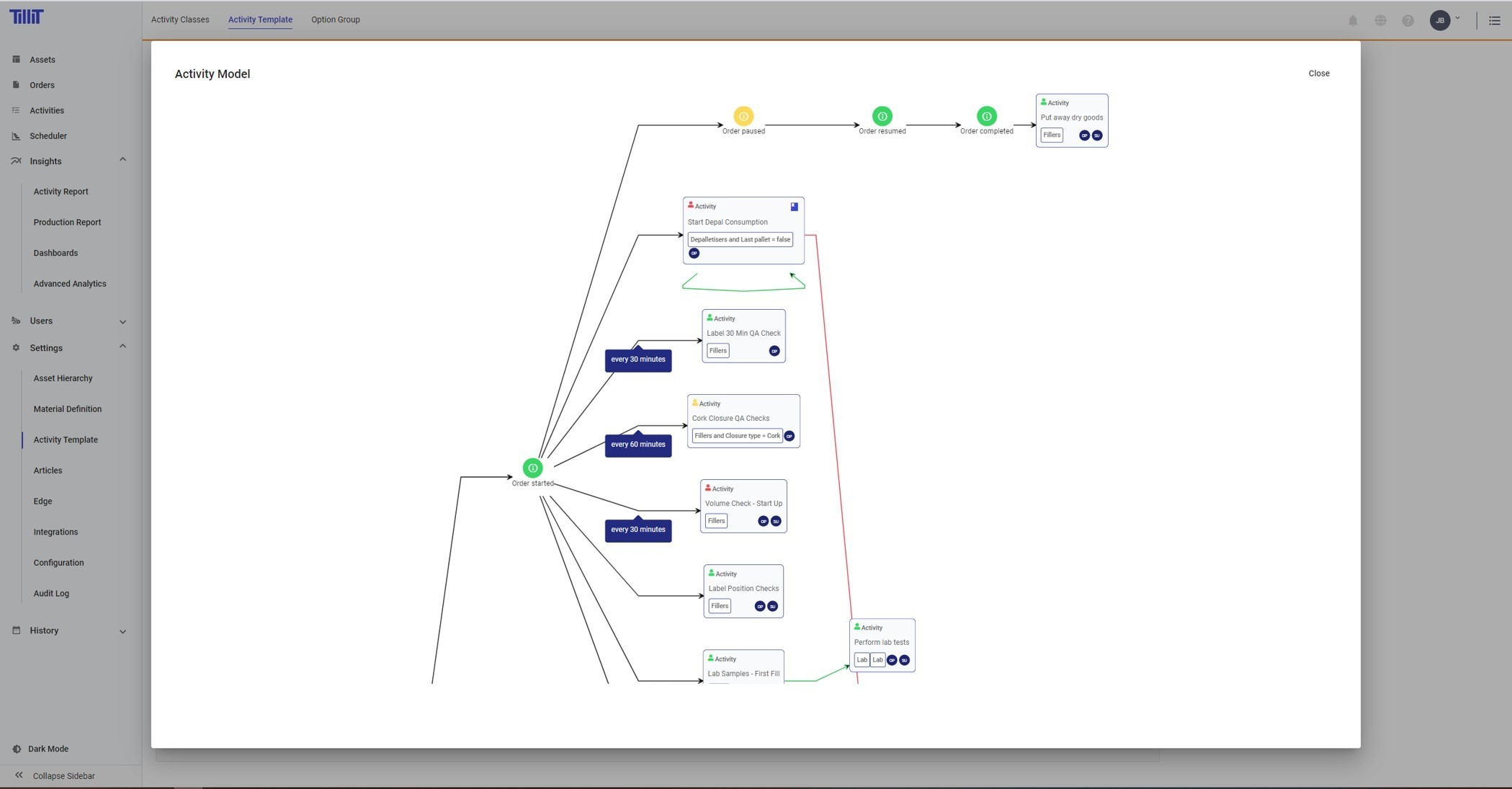
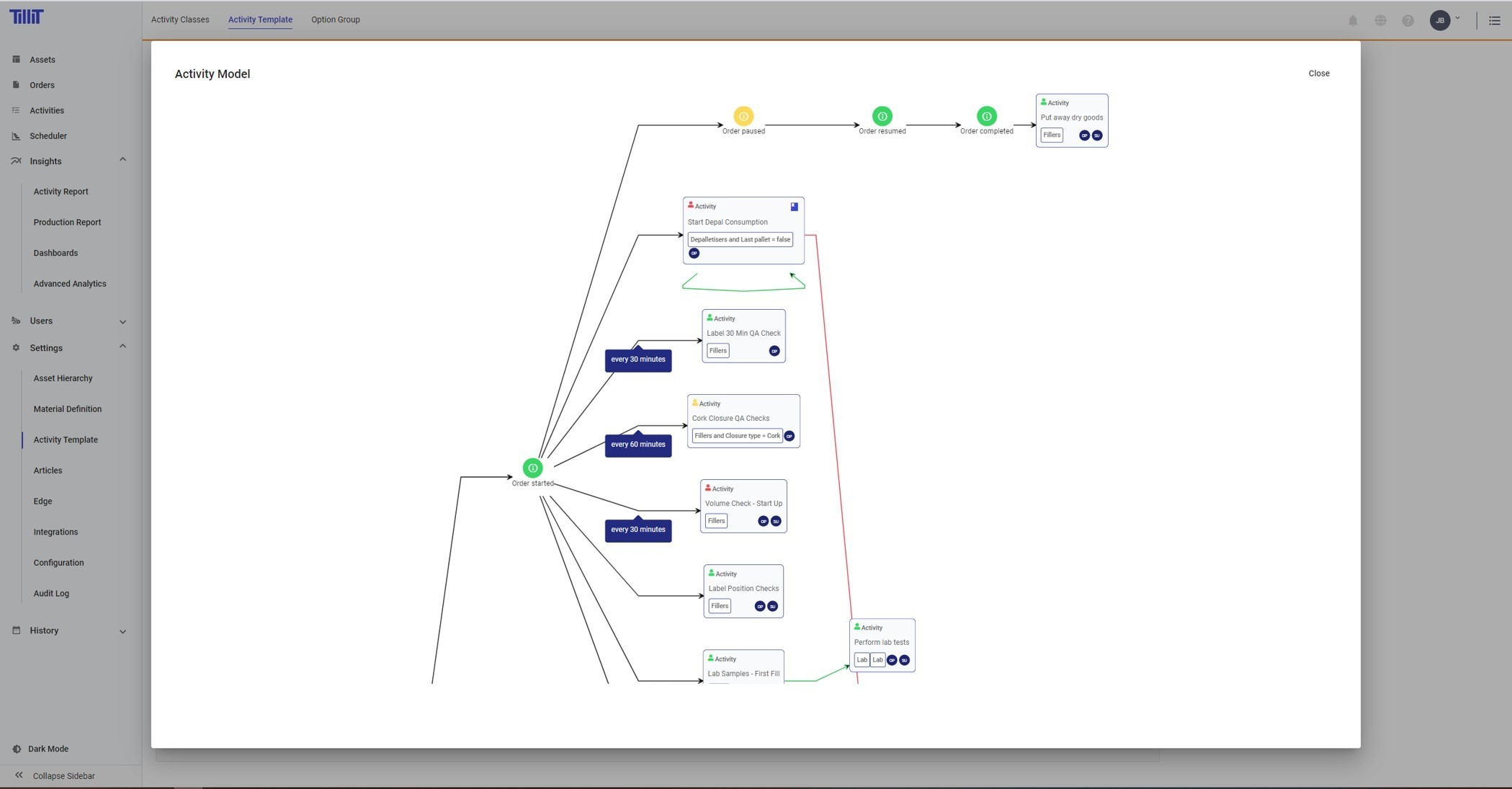
Part of the magic of TilliT is that it is no- / low-code. It needs no customization. Low-code configuration of assets, materials, and attributes is with a proprietary manufacturing-specific form builder. TilliT uses drag-and-drop, not coding, to create forms and workflows.
TilliT is hosted on AWS, which has the inherent benefits of the cloud. These include speed to deploy and change, seamless upgrades, and professional-grade cybersecurity. The system connects to a virtual or physical low-code edge device to connect to automation or equipment. All of this fosters a fast time to benefit.
Analytics
TilliT includes several types of standard reports: activity, production, dashboards, advanced analytics, and more. Reporting and visualization can serve operators and supervisors, plant managers, and others who need an overview of performance. Customers build dashboards with pre-built cubes. In addition to their own dashboarding, they also OEM AWS’ QuickSight BI tools.
TilliT can use an LLM to build forms and SOPs automatically. These are excellent uses of LLMs’ strength in processing language-based information.
Two new features of note also leverage AI.
- Heads-up notes for the operator are based on AWS Bedrock, which pulls from recent examples and trends about what might go wrong.
- Shift handover summary of what the previous shift did with any issues, plus what the coming shift is due to make.
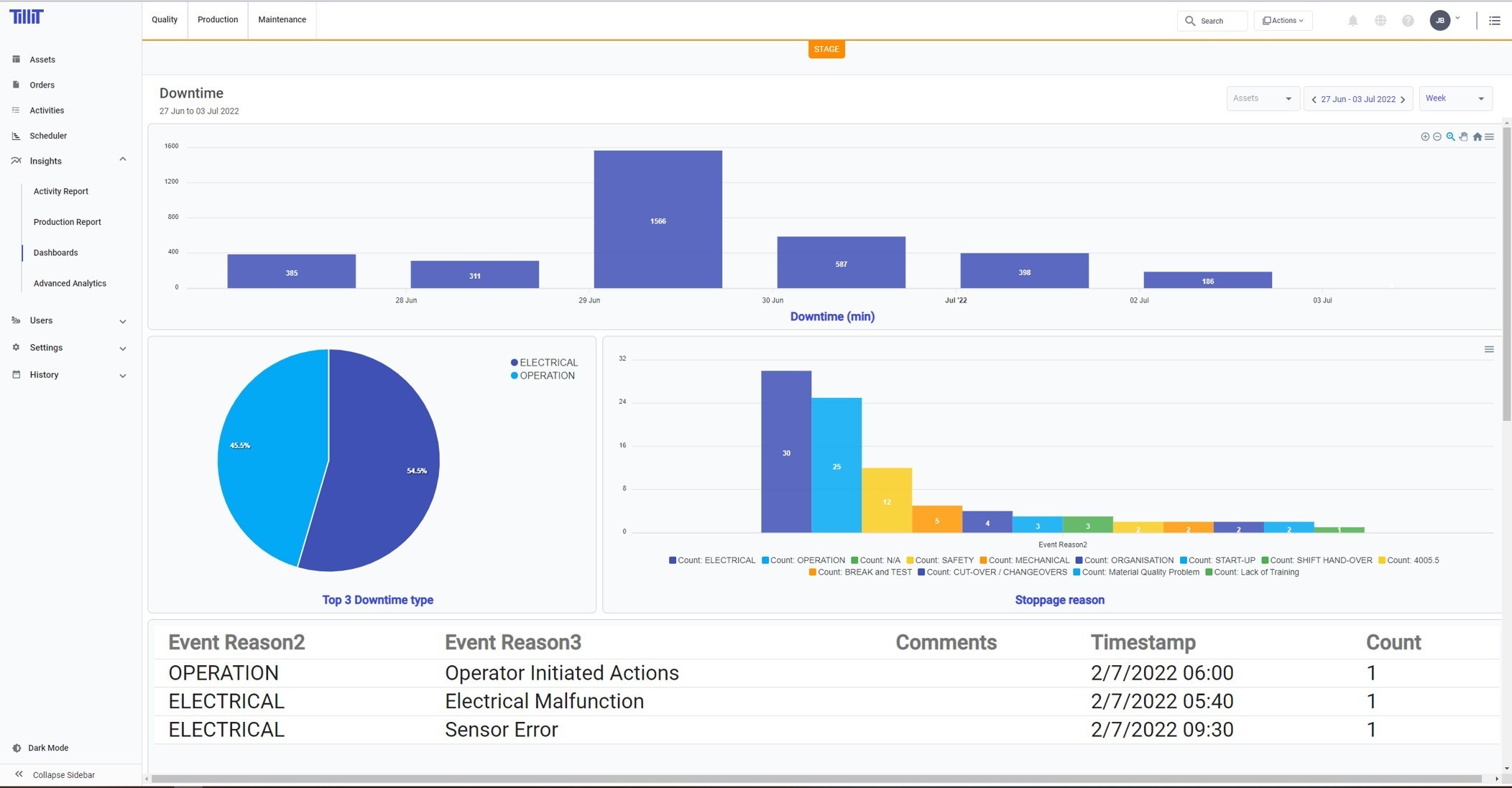
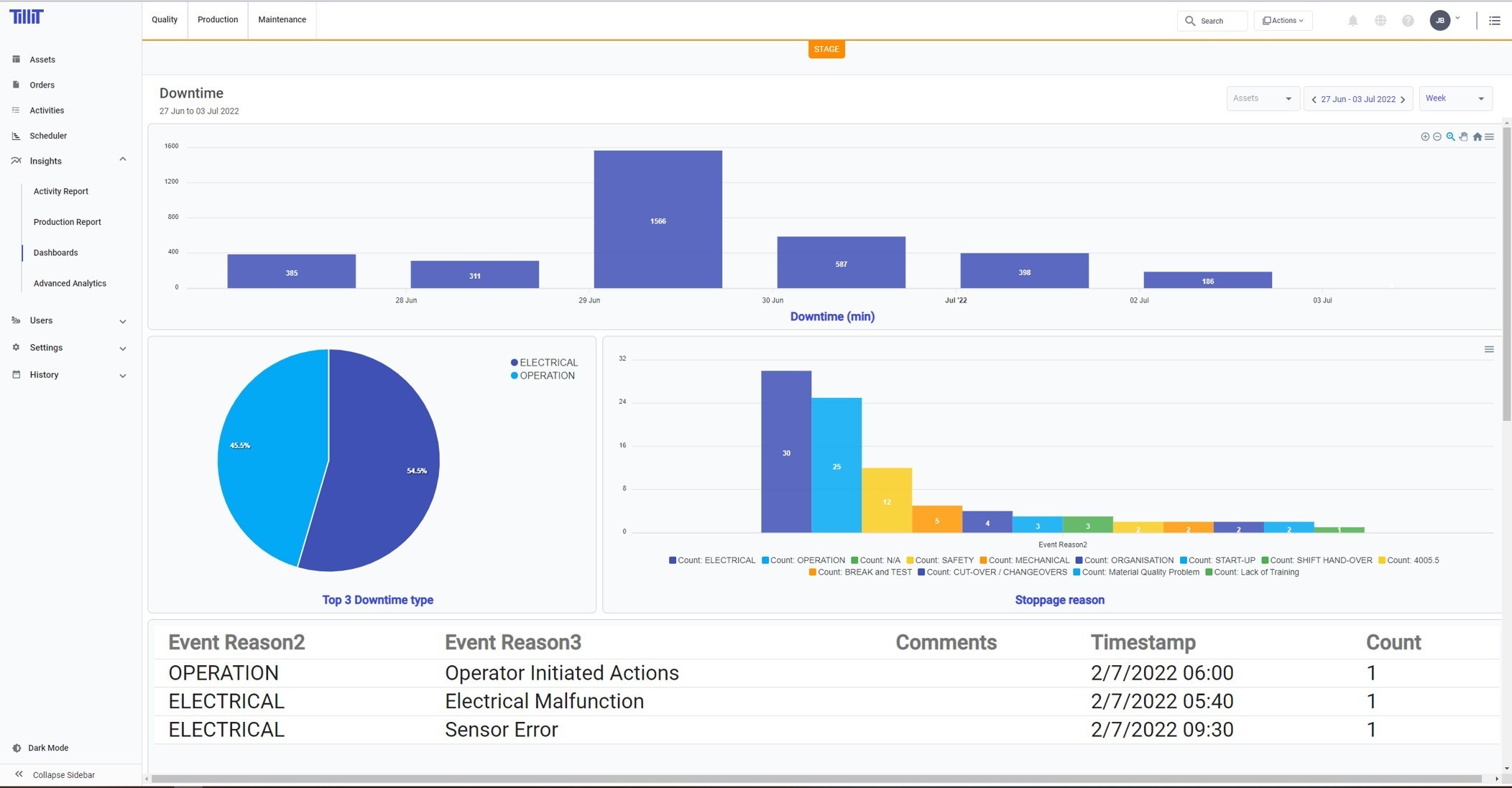
Customer Successes
Many Australian winemakers already use TilliT. Other Customers in beverages, food CPG, consumer durables, and industrial equipment are also using it successfully. Some large companies are also customers: Schneider Electric is using it to optimize injection molding operations, and Carlsberg is replacing a more traditional MES and IIoT platform with TilliT across its 80+ site global brewing footprint.
- A vegetable processor uses an activity report to quickly get an overview of their high-volume operation’s passes, fails, expires, and skips.
- One customer who took over a year to deploy a traditional MES did it in five months with TilliT.
- A manufacturer of kitchen sinks applied scheduling, execution, quality, safety, and SOPs with wireless IIoT devices and saw a 25% reduction in raw materials and a 10% reduction in finished goods while increasing production by over 4%. They saved a planning resource and reduced changeover time by 15%.
Roima Digital Thread
The acquisition of TilliT is part of a roll-up play for mature manufacturing solution provider Roima. A long-time implementation partner to AVEVA and others, Roima has been increasing their focus towards delivering their own software technologies to the global manufacturing industry after several acquisitions since 2016. The vision is to create a digital thread for visibility and control from product innovation (PLM) to integrated business planning (IBP) to customer management (CRM/CPQ) to digital commerce and product twin, to WMS and MES.
This is an ambitious vision, and achieving it will depend on how well Roima manages the many acquisitions and the increased focus on a unified multi-tenant platform for the industry. Another key factor will be how well its WIRE integration middleware can overcome gaps and create the data and information flows to connect this thread. Yet another open question is whether the private equity backers will have the patience to support everything needed to be profitable in the comparatively conservative and slower-moving manufacturing markets.
Looking Forward
We appreciate the lightweight low-code approach, particularly for the consumer goods segments TilliT has traditionally served. We also like the bottom-up approach to pulling tribal knowledge to build the value map. TilliT has plans to expand AI across its functions.
We look forward to following the progress of TilliT and Roima’s software suite. Thank you, James Balzary, for introducing us to your modern approach to operations software.
[post_title] => TilliT Low-Code MES and APS Soon to Weave into Roima [post_excerpt] => [post_status] => publish [comment_status] => open [ping_status] => open [post_password] => [post_name] => low-code-mes-and-aps [to_ping] => [pinged] => [post_modified] => 2025-07-24 14:12:26 [post_modified_gmt] => 2025-07-24 18:12:26 [post_content_filtered] => [post_parent] => 0 [guid] => https://tech-clarity.com/?p=22386 [menu_order] => 0 [post_type] => post [post_mime_type] => [comment_count] => 0 [filter] => raw ) [7] => WP_Post Object ( [ID] => 22272 [post_author] => 2580 [post_date] => 2025-07-22 09:00:05 [post_date_gmt] => 2025-07-22 13:00:05 [post_content] => How can manufacturers digitally transform their factory lifecycle to get the most out of their plant investments? As highlighted in Tech-Clarity's eBook "Digitally Transforming the Factory Lifecycle," top manufacturers have adopted more digital tools and taken a collaborative, integrated approach across the factory lifecycle. This infographic explains how companies can digitally transform factory designs and manufacturing planning to plan, design, build, and operate their factories. When done effectively, manufacturers can increase design efficiency, reduce time to full production, improve quality, increase throughput, and accelerate innovation. Click here to view or download the full infographic. For more information about digital factory, please visit our sponsor, Autodesk.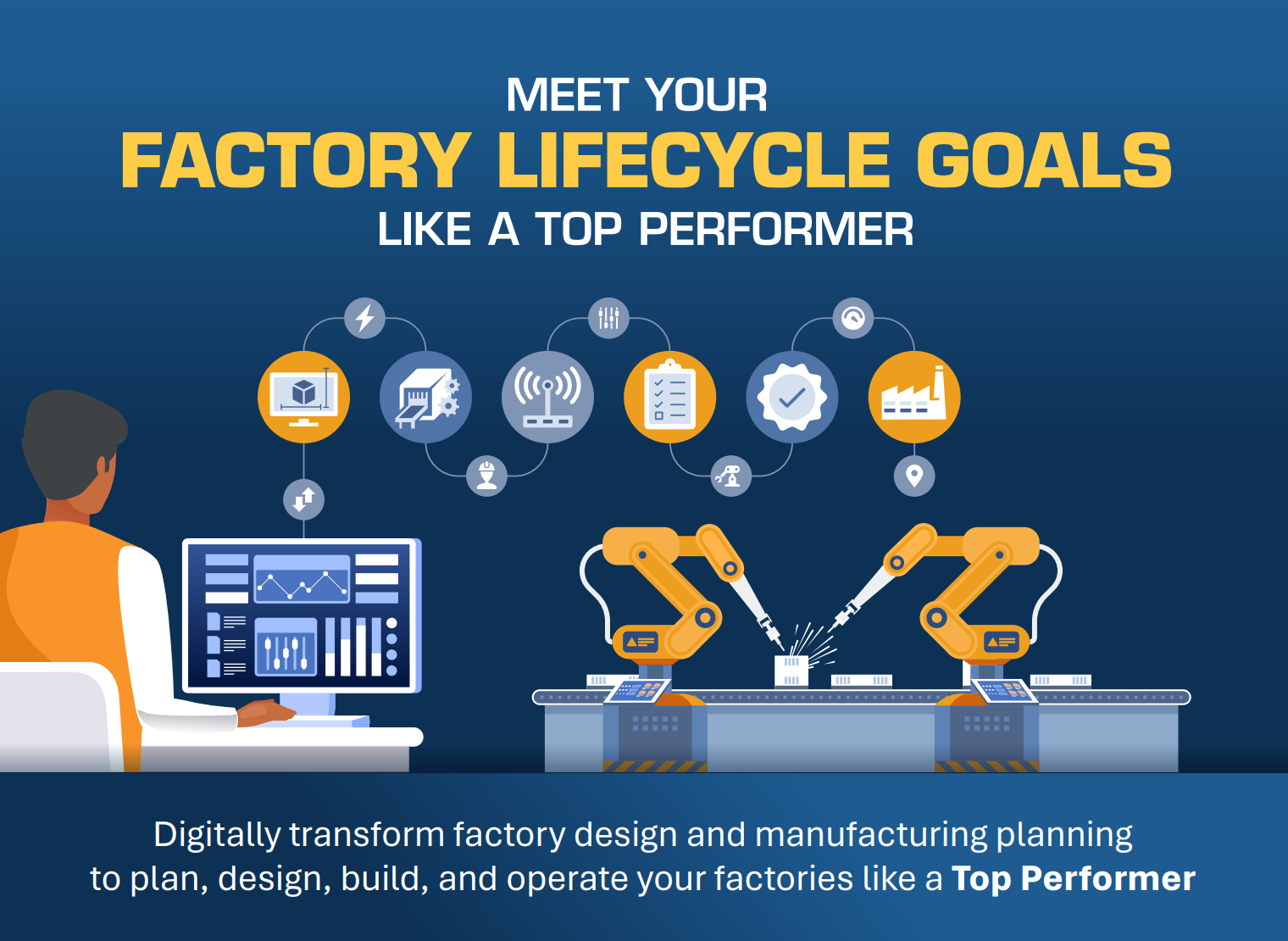
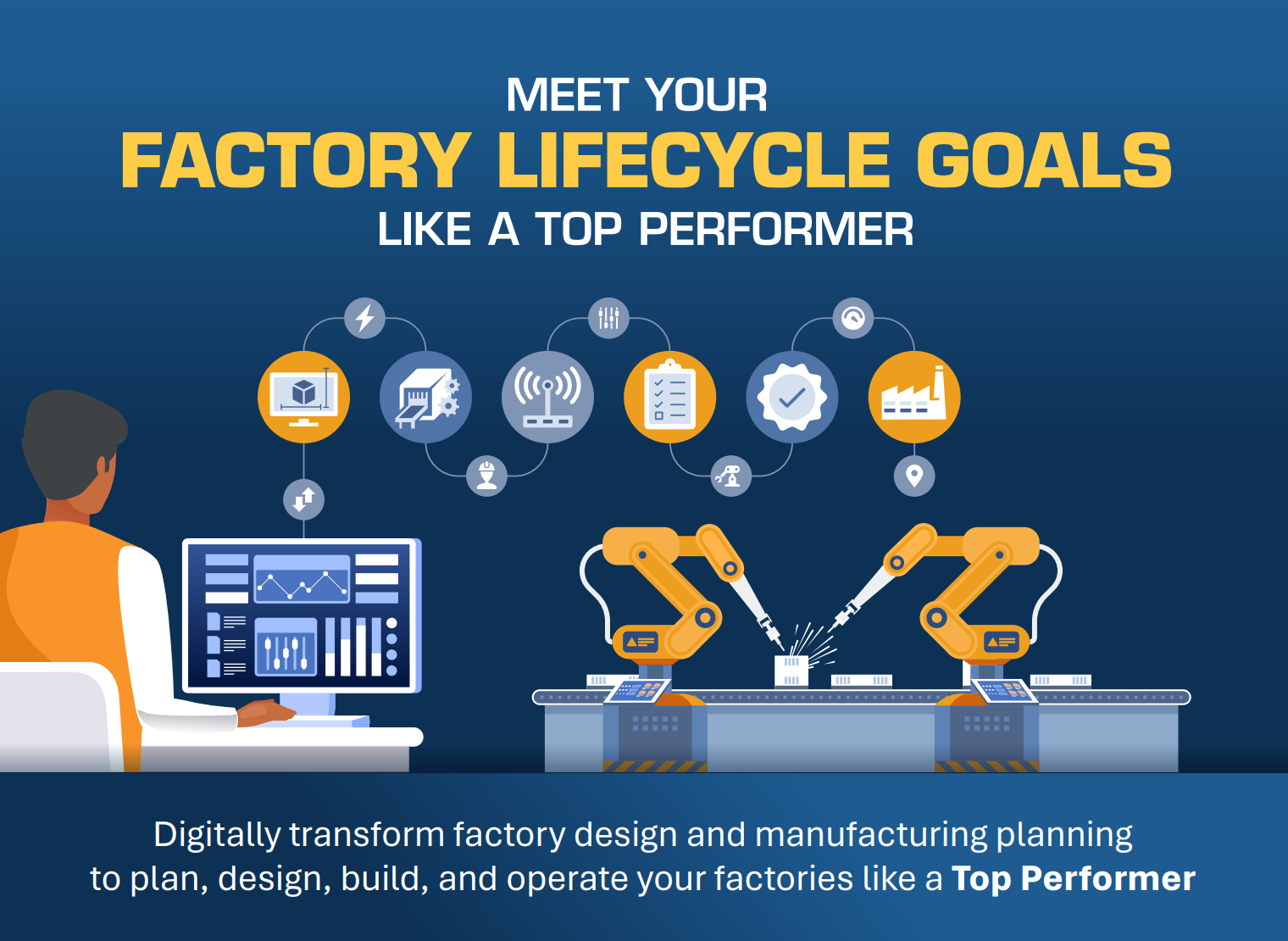
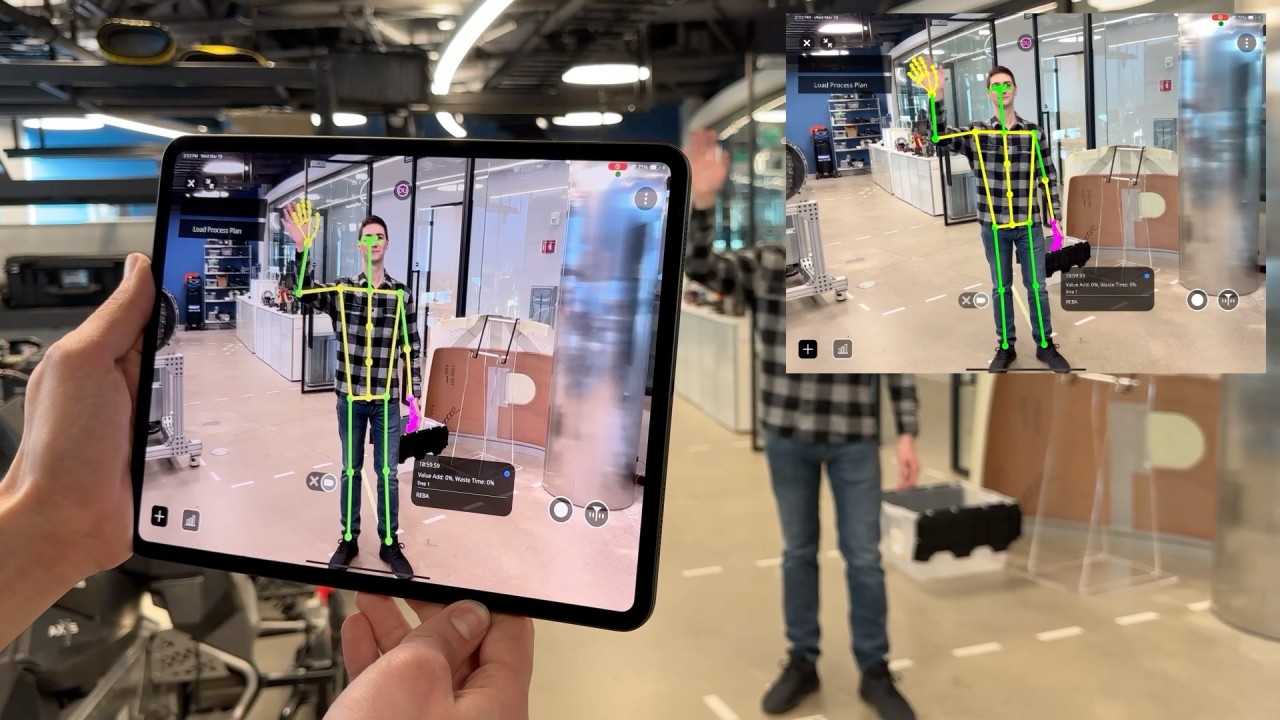
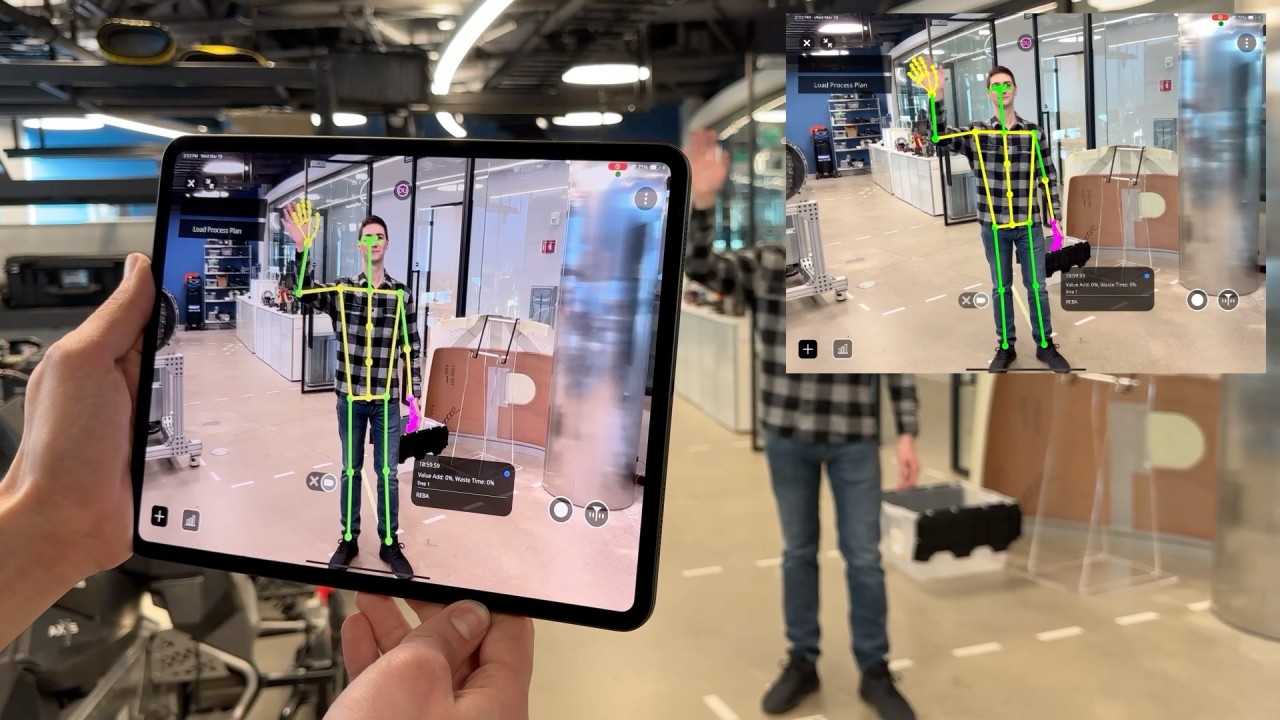
Why hasn’t Augmented Reality (AR) had a greater uptake in the manufacturing market? Maybe it had not found the best use. Data Time Space believes they may have found the killer app for AR: speeding continuous improvement (CI) and freeing CI experts to do the analysis, not the data collection. This young company enables manufacturers to use AR in new ways on mobile devices to collect real-time data over time in 3D space.
Spatial-Context Data Collection for CI and More
Data Time Space has developed a collaborative AI-powered spatial computing platform that collects data within a 3D video scan from a mobile device. The platform’s data model and AI capture, store, normalize, and put in context spatial data. The platform is inherently designed to connect to the Internet of Things (IoT) and track human movement. All computing in the platform is 3D space-related.
The company is initially aiming it at measuring ergonomics and safety, conducting time-and-motion studies, and gauging how people and processes are performing. The common thread for these applications is that they need data with spatial context to succeed. Seeing how a worker performs in 3D space is one thing. Capturing all of the data in context, based on an actual video scan of any part of a factory, and normalizing it is what Data Time Space is offering. The resulting type of dataset is foundational for all of these issues. The accurate, unbiased, contextualized data set has been complicated for most CI teams to assemble until now.
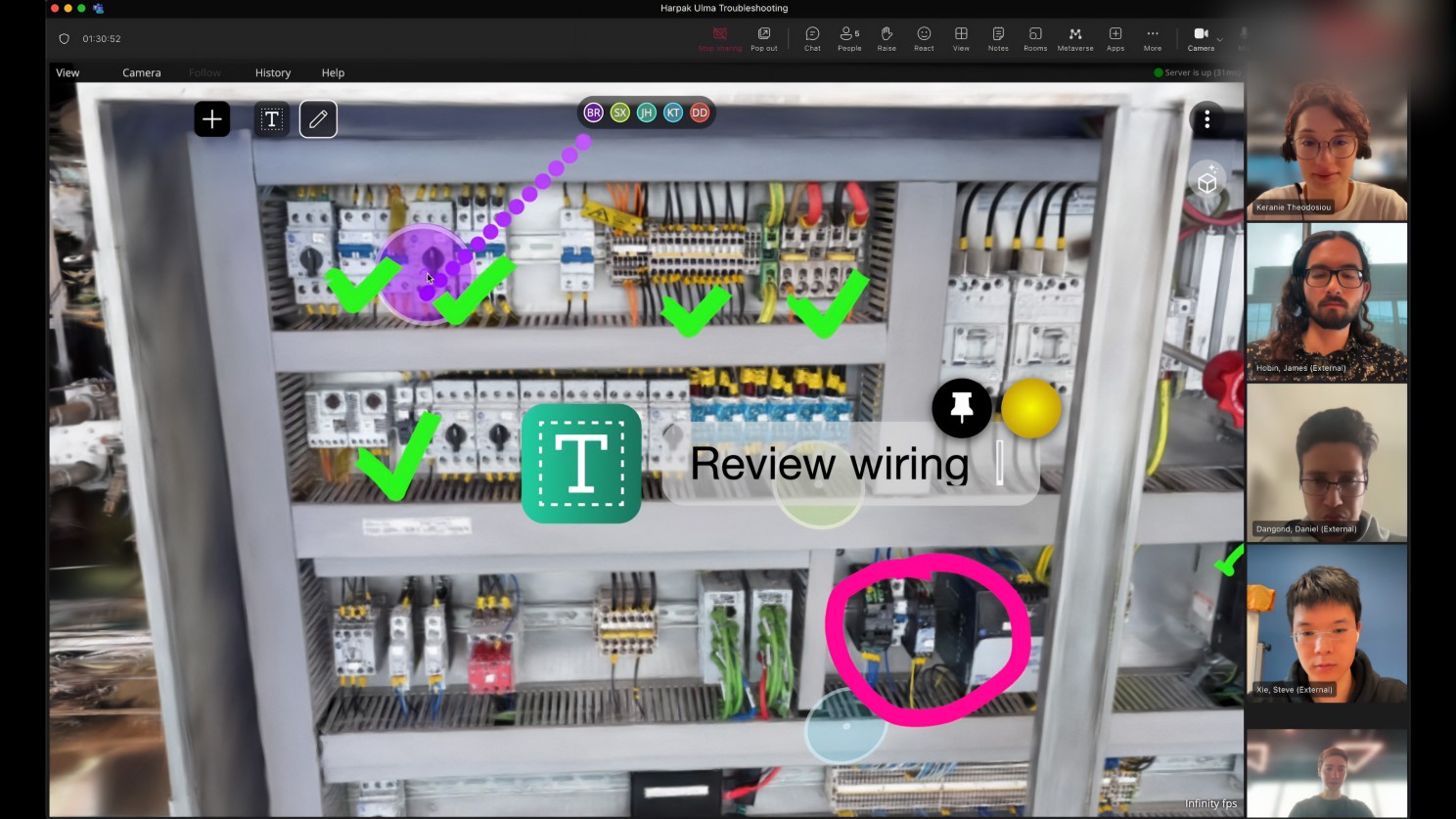
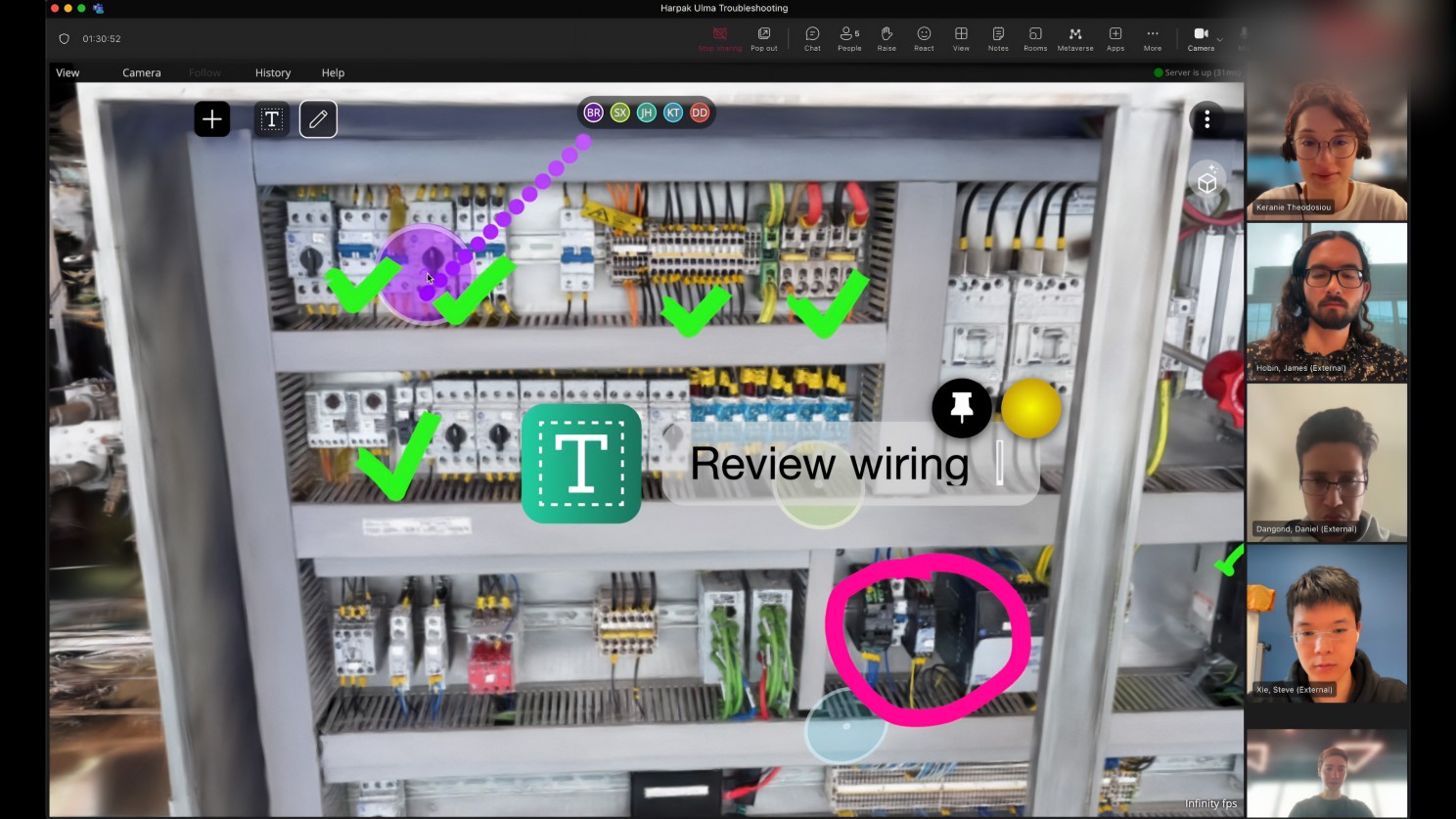
Mobile and 3D
Many AR applications’ hardware is based either on headgear or fixed cameras. Headgear can be uncomfortable, and cameras are inflexible and intrusive if always on in a work area. Data Time Space uses tablets or mobile phones. They point out that mobile devices can now be located within a few centimeters, with accurate LiDAR depth perception for precise signal localization in the camera. Signals are object locations or movement deltas. This spatial accuracy and the flexibility of using it where and only when needed could significantly improve AR's spatial-context data's accuracy, comfort, and privacy.
Rather than 2D maps and analysis tools, everything starts and stays in realistic 3D. End-to-end 3D eliminates transformations and the delays and possible errors they introduce. It also facilitates understanding and streamlines data gathering and analysis. The model trains on pointing the system at the user or process in question and pushing a button to record the data in 3D in real-time, time series views.
AI’s Role
While the platform is the major differentiator, one of its capabilities that may raise questions is spatial AI. AI helps with input and output to the spatial data model. AI collects spatial and temporal data, understanding what is in front of the camera and localizing it in 3D space. AI also uses and analyzes data in the model. A large language model (LLM) enables queries and processes data stored in the model.
Supporting Experts
It is designed to make the experts’ lives easier. If these professionals have the data collected and analyzed in real time, they can focus on how to best solve the problem. Data Time Space points out that the AI in their platform helps to understand the world and probe the complex data set, but it is human-in-the-loop and data model-centric. So, it has a strong model with logic in the platform and a streamlined, researched human interface.
Another challenge with CI data collection and analysis is bias. Using the Data Time Space system quickly alleviates any concern about that, as everyone sees exactly what happened in the recorded data. The demo is compelling, showing it tracking movement for ergonomics and trace or spaghetti maps for movement and waste reduction.
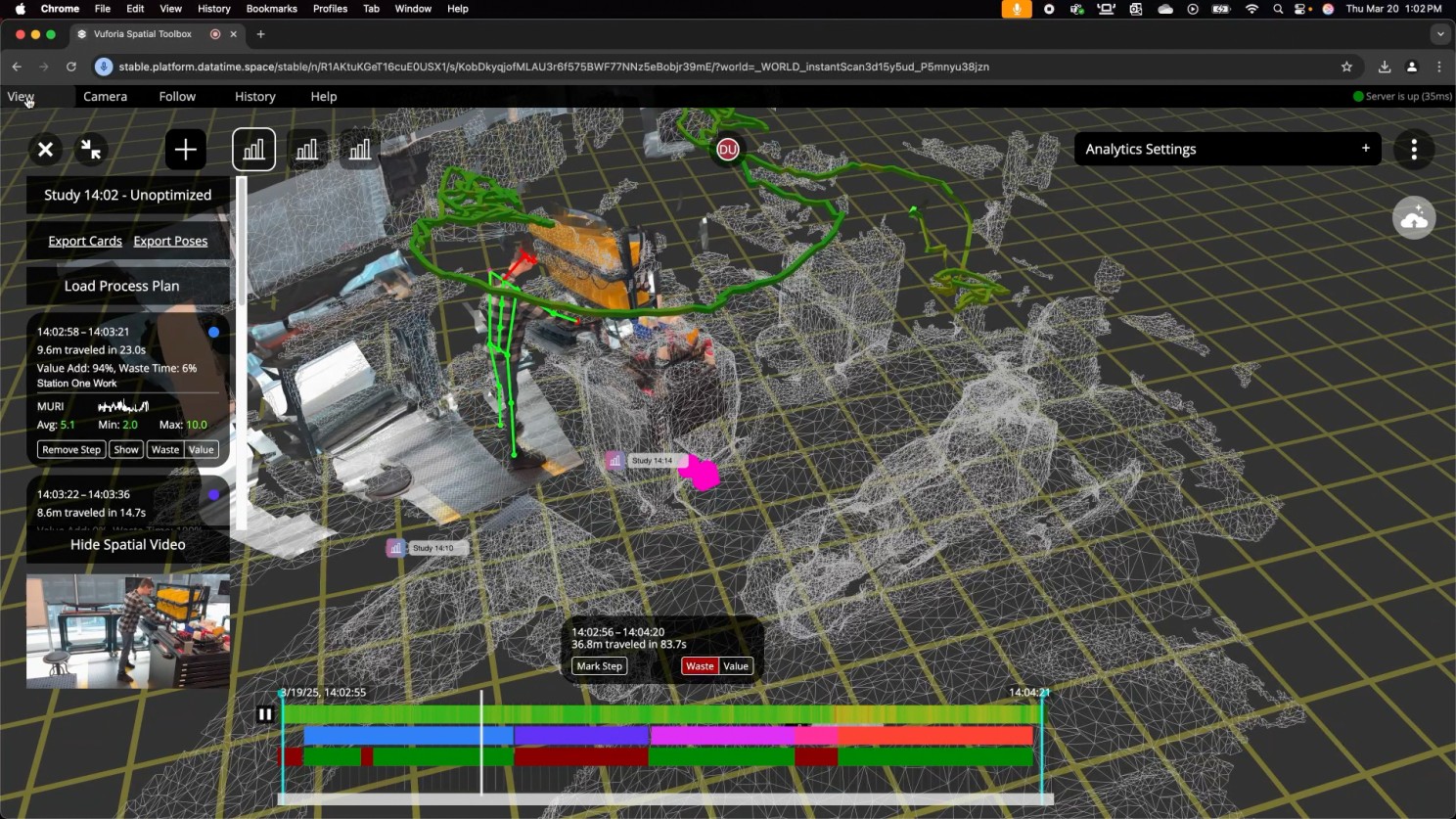
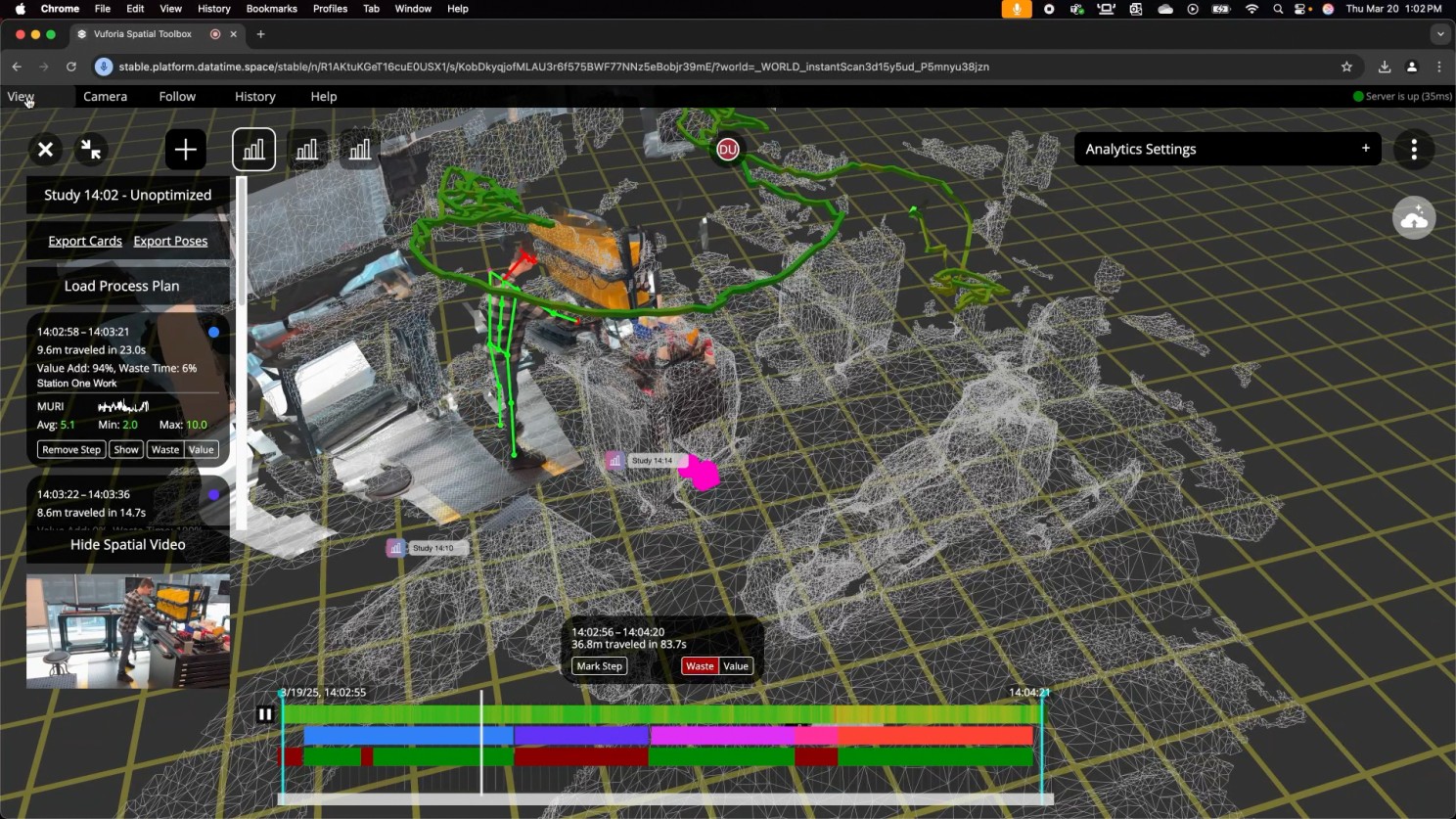
Key Applications
Data Time Space has also created AI-based applications to run on the platform. The main applications are factory analytics for continuous improvement and remote assistance. Factory analytics could compare differences between shifts, workers, or facilities. The focus could be on eliminating wasted movement, ergonomics, or safety. Remote support enables experts to stay in one location and support production teams worldwide, as they see exactly what is happening. The visual nature of the system and its data capture means it can also support employee training and education.
Data Time Space says it has found a way to scale applications that conform to its spatial data model flatly. It expects to build more applications or tools that help users. The applications can play together, enabling a remote expert to perform CI analysis without being physically present, for example.
New Yet Proven and Honed
While Data Time Space is a young company, the founders have been focused on building and enhancing this technology for 12 years. Before this, they worked at PTC, building and honing the Vuforia AR/VR platform. Data Time Space now owns the IP behind this spatial platform, while PTC owns a share of the company. This is a complete spatial data collection and analysis platform, with AI incorporated to understand the spatial data better. The user interface also includes AI. With their deep background, they have quickly begun to offer proofs of concept (PoC) that hold promise.
Looking Forward
CI data collection may well be the killer app for AR. Data Time Space’s next steps will be helping to prepare the data sets for uses beyond the CI team. Thank you, Valentin Heun, for taking the time to explain your approach and technology to us. We look forward to reconnecting and learning more as you make progress in the market.
[post_title] => Data Time Space: Is CI the Killer App for AR? [post_excerpt] => [post_status] => publish [comment_status] => open [ping_status] => open [post_password] => [post_name] => killer-app-for-ar [to_ping] => [pinged] => [post_modified] => 2025-07-24 14:01:47 [post_modified_gmt] => 2025-07-24 18:01:47 [post_content_filtered] => [post_parent] => 0 [guid] => https://tech-clarity.com/?p=22375 [menu_order] => 0 [post_type] => post [post_mime_type] => [comment_count] => 0 [filter] => raw ) [9] => WP_Post Object ( [ID] => 22225 [post_author] => 2574 [post_date] => 2025-07-09 10:00:02 [post_date_gmt] => 2025-07-09 14:00:02 [post_content] =>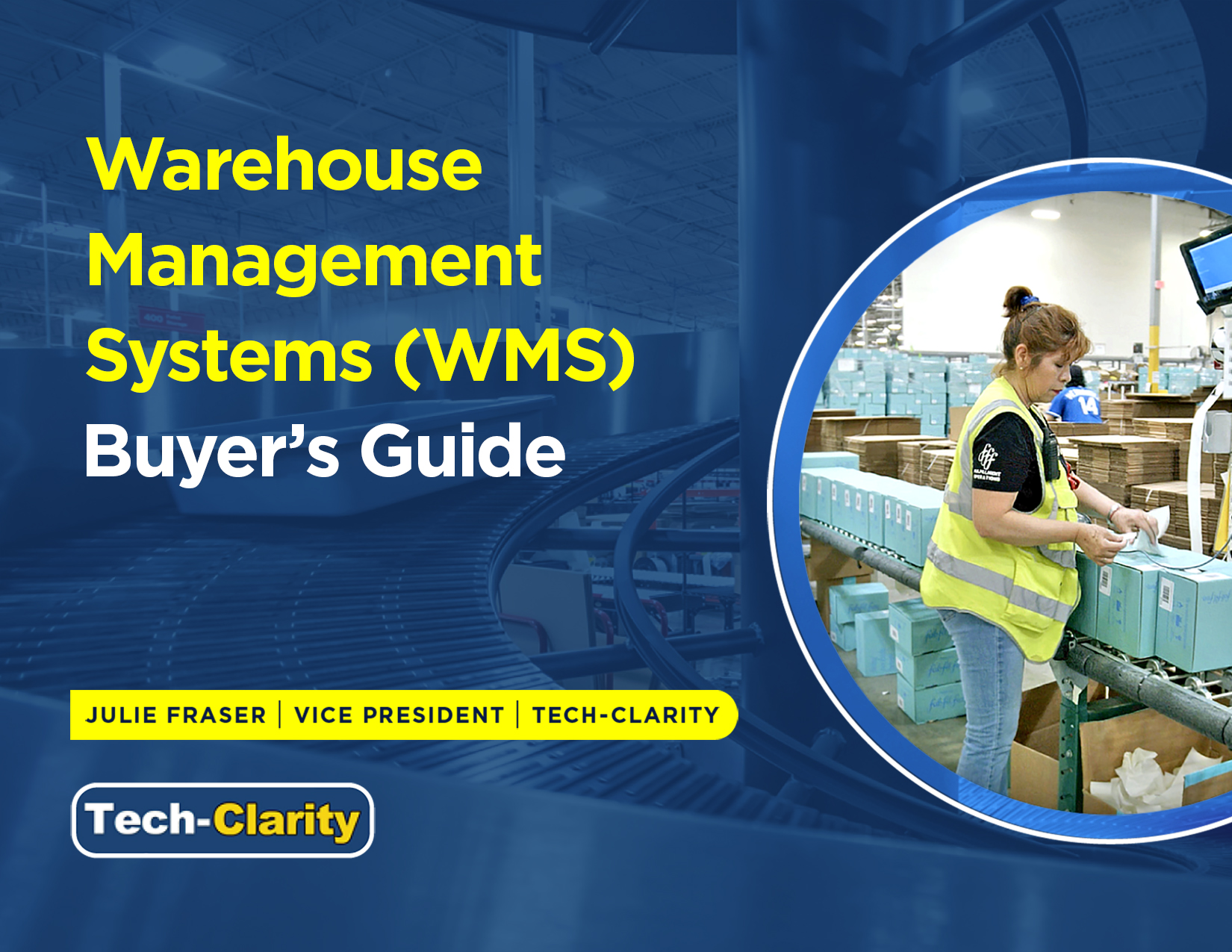
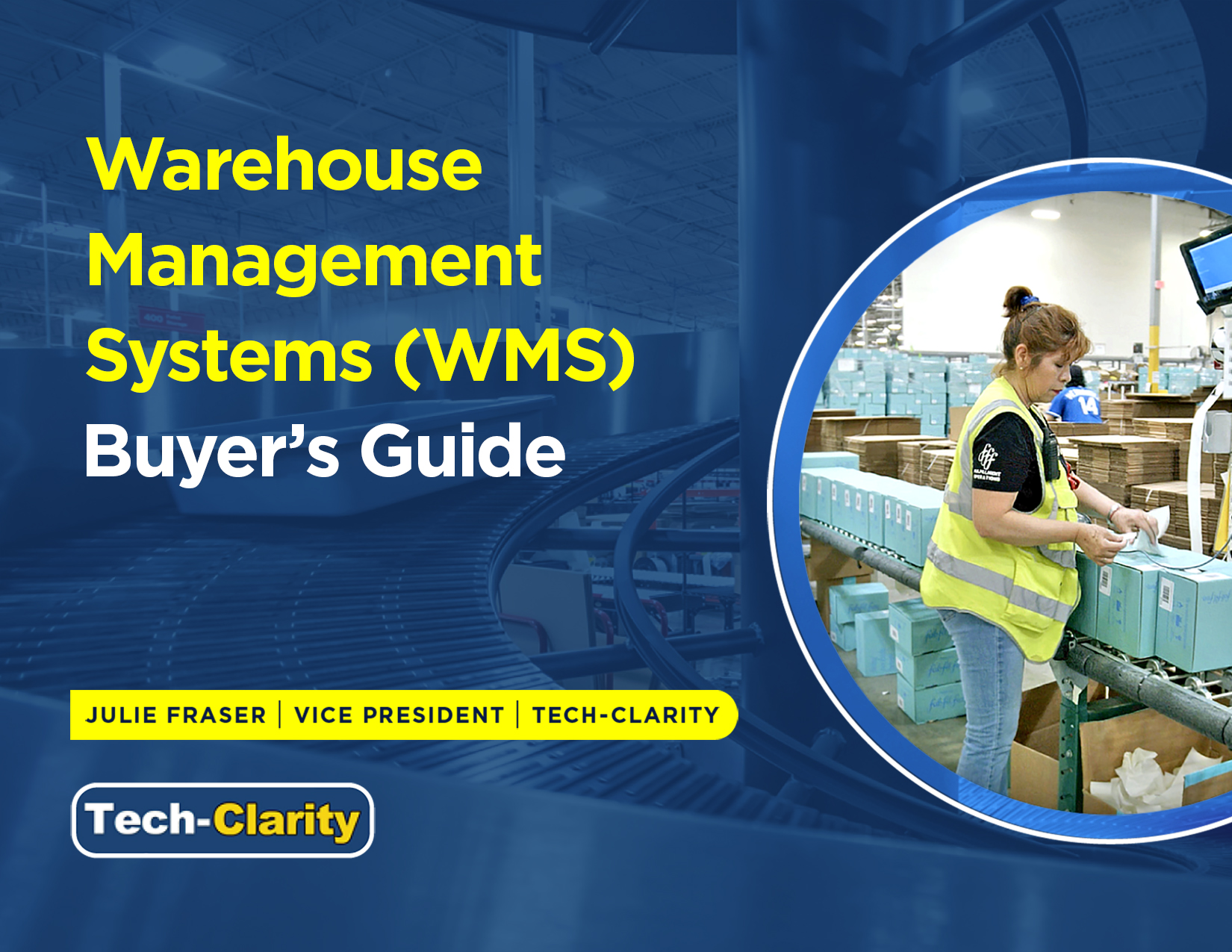
Table of Contents
- Introducing the Buyer's Guide
- Flexible Flows to Meet Enterprise Needs
- Enterprise-Capable
- Enterprise-IT Capable
- Functionality
- Visibility and Optimization
- Software Technology
- Vendor Requirements
- Implementation and Service Criteria
- Optimize and Reoptimize
- Acknowledgments
Introducing the Buyer’s Guide
Perfect Orders in a Changing World Every industry has been suffering from disruptions and radical changes in supply, demand, and business realities. As a result, supply chain responsiveness for perfect orders is often top of mind, and enterprise warehouse management systems (WMS) are foundational to achieving that. Warehouse performance is crucial, not only for wholesale and distribution enterprises but also for retailers, e-tailers, producers, and manufacturers. Structure of the Guide This buyer’s guide describes the needs of larger enterprises to transform and continue to improve their business. It then lays out a set of critical considerations for selecting a WMS that will support the strategy now and into the future. Functionality is just the beginning of the considerations. Technology is also crucial and needs to be future-ready as the digital transformation continues. Even if the software is good, the solution provider partner or vendor plays many vital roles. To gain business value with an excellent total cost of ownership, implementation, and the ongoing relationship matter also.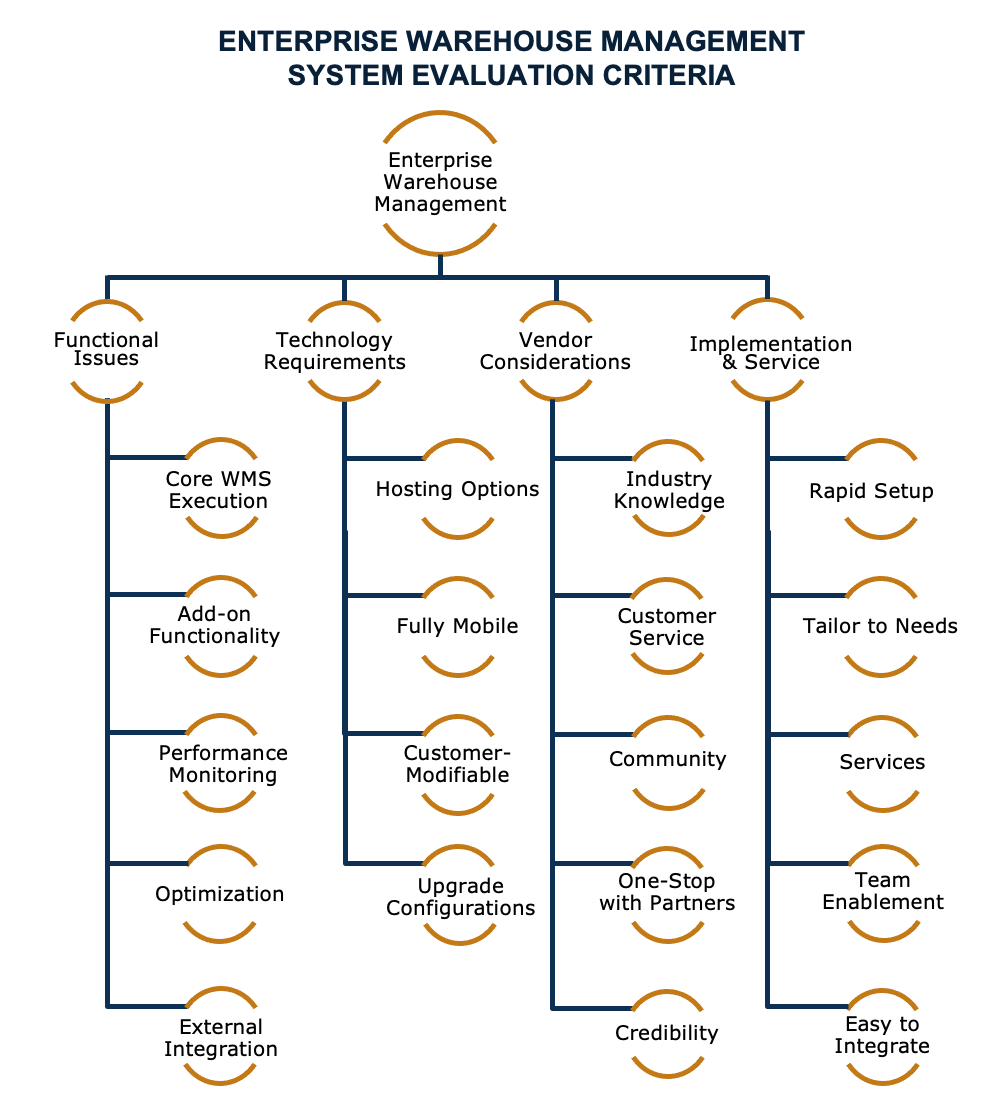
Enterprise-Capable
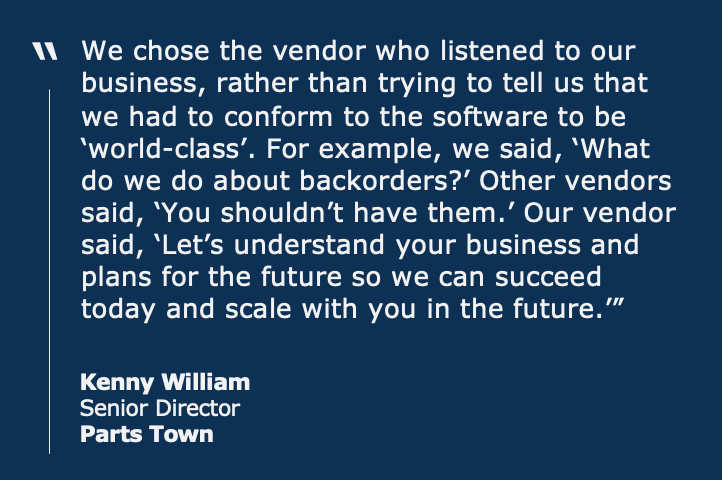
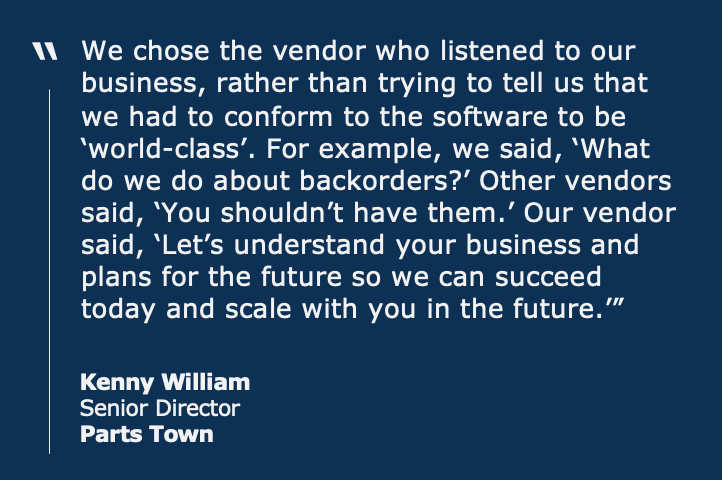
Visibility and Optimization
Performance Monitoring Disciplined metrics are the foundations of most enterprises’ ability to stay competitive. Look for a WMS with robust performance reporting. Common key performance indicators (KPIs) include order lead time, perfect orders, carrying costs, turnover, inventory-to-sales, inventory accuracy, and shrinkage. Yet, many enterprises have company-standard KPIs and formulas for calculating them. So, this functionality must be extensible to allow monitoring and reporting the way your company expects it. Ideally, this also includes pivot-style analytics to drill down into the data and review performance by customers, suppliers, products, facilities, or areas. Optimization Seek to go beyond execution and reporting to optimize the warehouse or DC. This points to a WMS with simulation and predictive analytics. These advanced capabilities can model the facility to promote a deeper understanding of the impact of possible changes. This is a strong foundation for continuous improvement. Optimization also helps improve agility to make sure a response to changing conditions is still productive, safe, and profitable.Optimize and Reoptimize
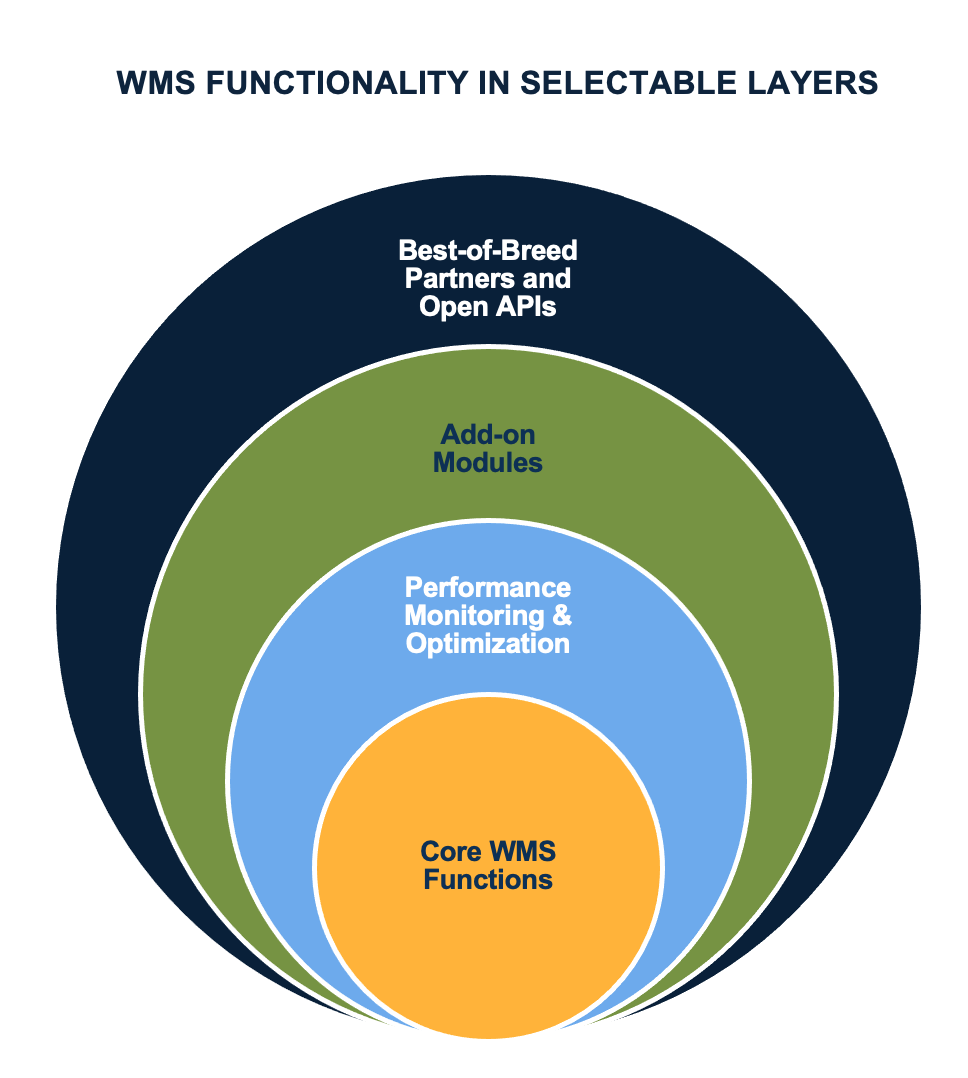
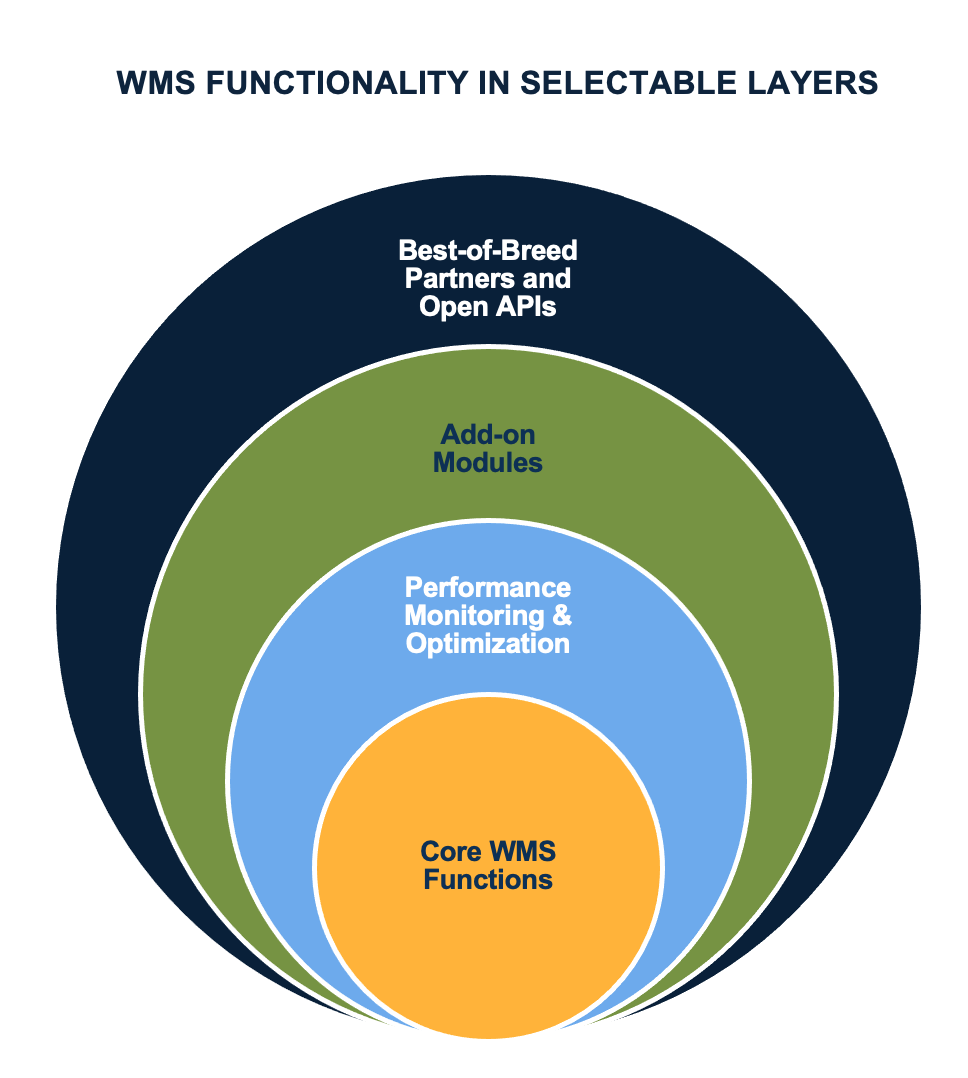
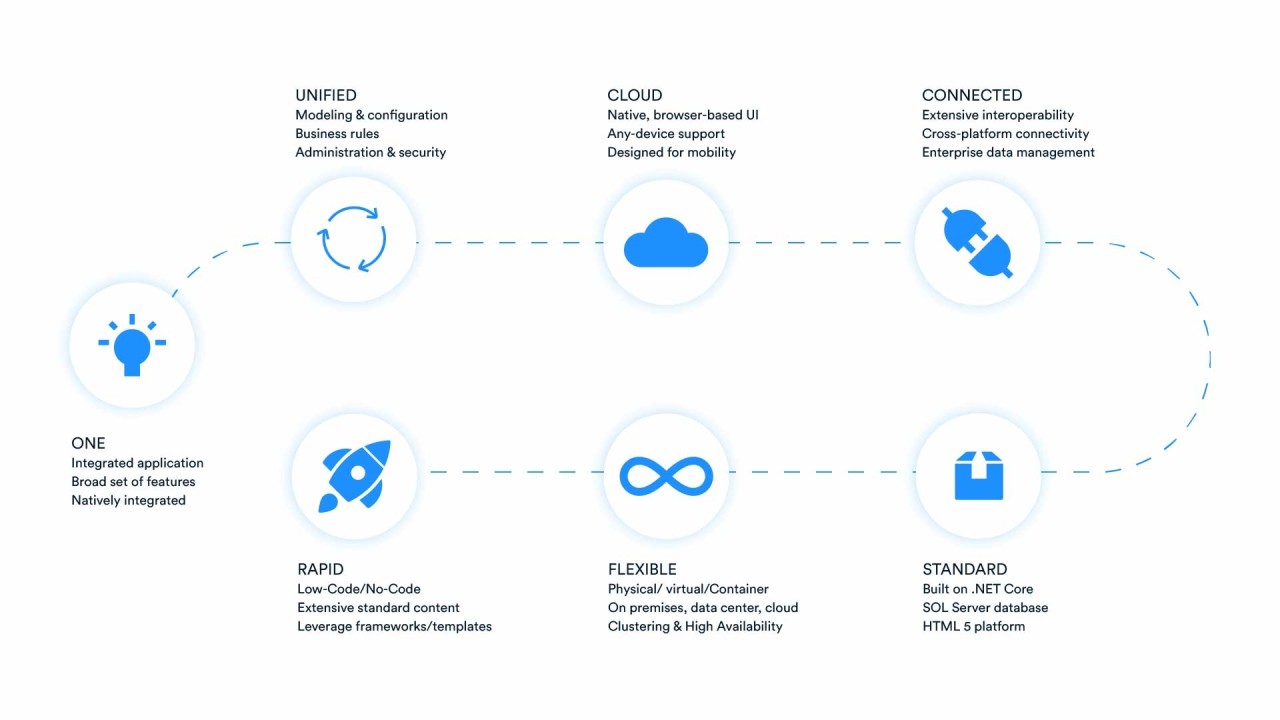
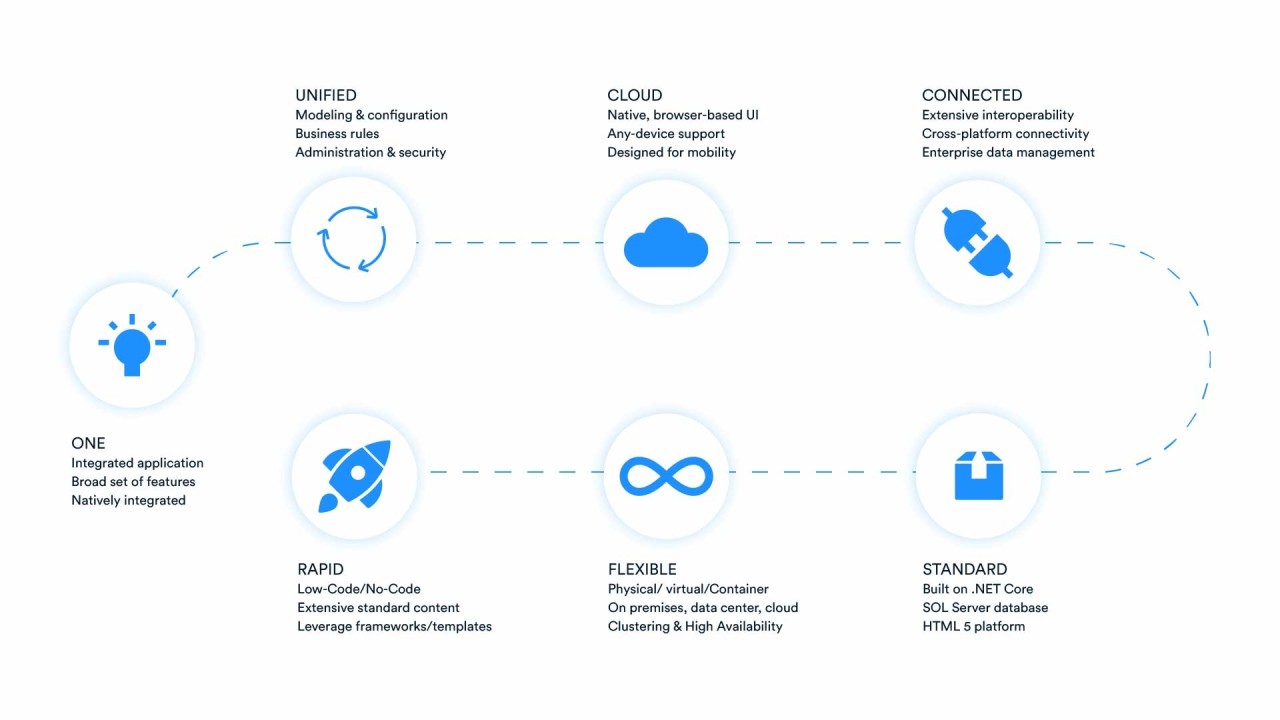
What might batch industry manufacturers still desire in their enterprise-grade MES? Maybe simpler ways to configure, roll out, and manage the system. TrakSYS MES V13 features major upgrades in solution creation and templates. It also prepares for cloud deployment, expands containerization, includes MQTT, and maintains a clean user interface— the kind of UI that has made them a customer favorite for decades.
Impressive Growth
TrakSYS has been on the market since 2001 and has recently been growing revenue by 20% annually. Its workforce has increased by 30% each year over the past two years, following strategic investment from partner BVP Forge. With deployments in over 100 countries, this well-established company continues to grow rapidly in all regions, with accelerated growth in APAC. This extensive geographic reach is rare in the MES market for companies of Parsec's size, demonstrating the global acceptance of TrakSYS and the worldwide partner network it has built.
Its focus remains on leading manufacturers in food & beverage, pharmaceuticals, CPG, and chemicals, though it serves other industries as well.
Parsec’s growth reflects the rising demand for adaptable and scalable MES solutions across sectors. Powered by V13, TrakSYS is set to transform how manufacturers pursue operational efficiency, offering an unmatched blend of flexibility and advanced technology.
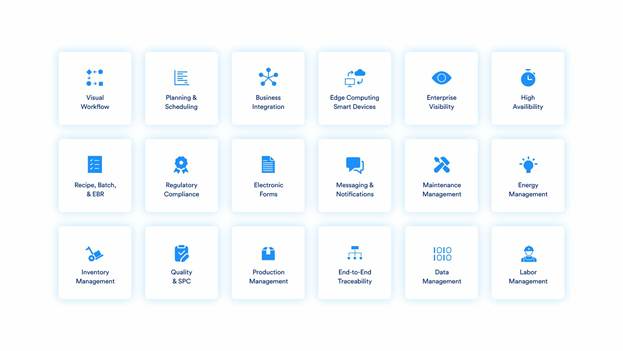
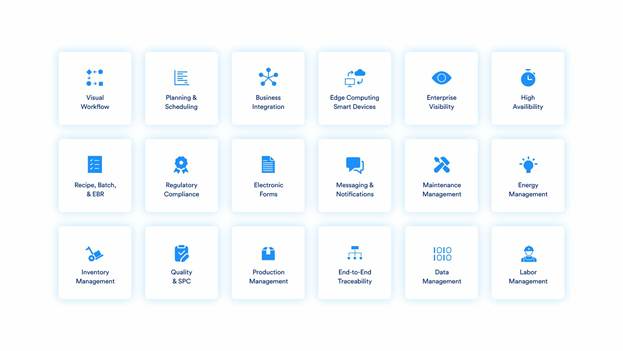
Keys to Success - Platform
TrakSYS was originally built on the Microsoft .NET platform. Unlike its larger MES competitors, which have assembled solutions by acquiring multiple software offerings, all TrakSYS modules (27 and counting) are developed on the same platform and use the same database. This standardization has allowed Parsec to unify communication, integrations, and the user interface, facilitating a quick transition from on-premise or data center deployment to the cloud by leveraging capabilities such as .NET Core, SQL Server, HTML5, and other Microsoft Azure tools for migration.
Currently, only 15% of their client base remains on-premise, 30% are in a corporate data center, and 55% are deployed in the cloud. Additionally, 90% of these cloud deployments are single instance multi-site (SIMS). Parsec’s largest SIMS deployment is with a food and beverage manufacturer supporting 46 sites from a single instance.
Keys to Success - Solution Creation using Function Blocks & Templates
TrakSYS features a core framework for solution creation, with pre-built Function Blocks for common MES functionalities like SPC. These can significantly reduce service time in project implementation. Users can quickly create new SPC overview pages using existing data definitions, aiming to expand function blocks across various MES use cases.
Users can combine tables, menus, pages, charts, and lists to create custom visual elements and interactive pages with buttons and web service calls. They can also modify screens by accessing the parts viewer, dragging components from the parts gallery, and configuring their properties.
Other Product Updates
Parsec Smart Devices are now in their third generation, with enhanced capabilities like responses and indicator lights. Parsec supports both OPC UA and MQTT, with the Sparkplug B protocol expected to be available by the end of 2025.
This new release includes updates to the workflow builder, including the ability to create nested workflows for complex automation processes. A newly released SVG editor allows customers to interact with shop floor schematics within TrakSYS, enabling features like clicking on parts or dynamic visual indicators.
Future Directions
TrakSYS Cloud will be a new SaaS offering, serving as a command layer that complements existing cloud deployments. It will help with backups and data transfer across TrakSYS instances. TrakSYS Cloud aims to enable quick startup, license visibility, simplified installations, and hosted non-production environments, with a planned release by the end of the year. The process includes creating templates for custom pages and managing their versions for deployment to different sites. A development area is designated for template creation, and a QC area connects to relevant data sources. The database transfer tool moves configurations between environments without affecting data. TrakSYS Cloud oversees the template management system, allowing categorized templates to be deployed to specific sites.
TrakSYS IQ Assistant, an AI chat feature being added to the product, utilizes Azure Open AI. This will let users ask questions about their TrakSYS data and get insights, charts, and tables in return. It will support multiple languages and allow actions like creating pie charts or adding trend lines. Discussions are ongoing about role-based access control to protect data security within the AI assistant. Regional data governance is also being explored, with a prototype currently in private-preview with select customers.
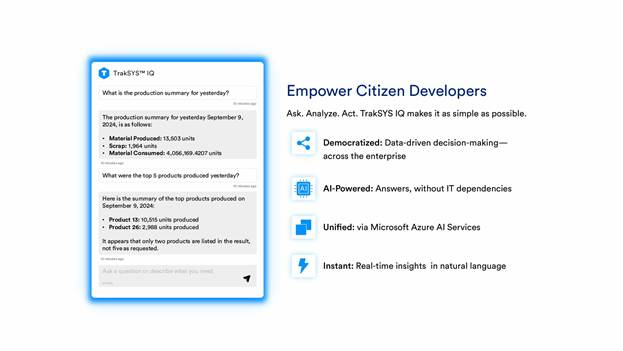
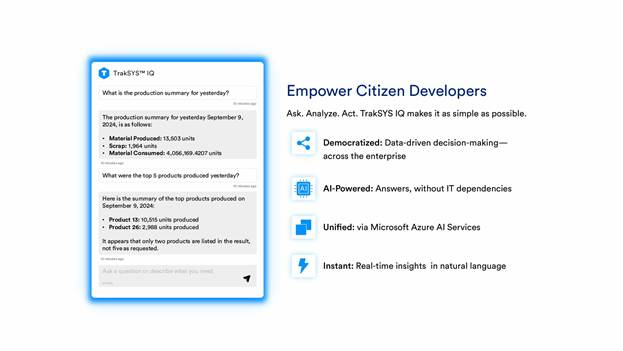
Thank you, Ryan McMartin, for the detailed briefing and demo for Tech-Clarity's Rick Franzosa and Julie Fraser.
[post_title] => Parsec Keeps Growing, TrakSYS Gets Easier to Fit & Scale [post_excerpt] => [post_status] => publish [comment_status] => open [ping_status] => open [post_password] => [post_name] => parsec-traksys [to_ping] => [pinged] => [post_modified] => 2025-07-24 13:38:37 [post_modified_gmt] => 2025-07-24 17:38:37 [post_content_filtered] => [post_parent] => 0 [guid] => https://tech-clarity.com/?p=22363 [menu_order] => 0 [post_type] => post [post_mime_type] => [comment_count] => 0 [filter] => raw ) [11] => WP_Post Object ( [ID] => 22184 [post_author] => 2574 [post_date] => 2025-07-02 01:08:48 [post_date_gmt] => 2025-07-02 05:08:48 [post_content] =>Where can you meet senior manufacturing leaders who are taking strides toward digital transformation and learning from one another? One venue is the Manufacturing Leadership Council’s (MLC) annual Rethink conference. In addition to a packed two-and-a-half-day conference, the program included an MLC member meeting and an awards banquet.
The MLC’s mission is “to help senior executives define and shape a better future for themselves, their organizations, and the industry at large by focusing on the intersection of critical business and technology issues that will drive growth today and in the future.” This conference, held at the JW Marriott beach resort on Marco Island, FL, on June 16-18, 2025, did that well.
Power Panel
Tech-Clarity’s Julie Fraser was on the Power Panel: Handicapping the Global Digital Transformation Race. David R. Brousell MLC’s founder, moderated the discussion. Other analysts were Bob Parker of IDC, Craig Resnick of ARC, and Matthew Littlefield of LNS. It was a lively discussion. Each firm’s research and perspectives led to some areas of agreement and also some divergent views. In aggregate, the research from these companies shows progress in digital transformation in the US and worldwide.
Manufacturing Case Highlights
This conference was rich in examples of manufacturers undertaking aggressive digital transformation.
- The top award-winner was Celanese, which has developed and implemented JO.AI as the user interface and copilot across the company. SVP Global Manufacturing Jon Mortimer presented this as Accelerating Celanese’s Digital and AI Transformation for 10X Manufacturing Value. They started building this system on GenAI, collaborating with Radix and Cognite, in 2022, and have some 70 citizen developers. It was eye-popping to see it parse an entire plant’s scanned P&ID, work orders from ERP, and work with vision systems to spot and troubleshoot issues.
- Enersys’ Raphael Germe, Senior Director of Global EOS and OPS Engineering, captured the company’s continuous improvement core and explained how AI and digital approaches support this core EOS way of working.
- Jabil's Michal Wierzchowski discussed how integrating AI can help optimize old and new systems. Jabil held a supplier summit to trigger partnerships based on each company’s strengths. It worked with Arch Systems to deploy agentic factory experts to read dashboards, interpret context, and prescribe action.
- A panel with P&G and Cytiva focused on autonomous operations. P&G’s Alberto Gomez talked about interconnecting people and work systems, extreme automation, and digital to operate by exception. He pointed to a better employee experience as a result. Kevin Seaver of Cytiva talked about the balance of where people and automation come together for worker safety.
- Eaton’s VP of Industry 4.0, Craig Sutton, shared how they are Scaling Digital on Eaton’s Path for Growth. He shared their focus on governance, process, people and skills, technology stack, and scale out. Working with Deloitte, they boiled down to eight primary use cases and started in five lighthouse plants. They see KPI and balanced scorecard improvements for every plant.
- Many more manufacturers, large (Coca-Cola, IPG, etc.) and small, presented or spoke on panels and showed significant progress in digital transformation, automation, and AI programs.
Expert Views
In addition to the highlights from manufacturers, experts took the stage as well. Gregory Daco, the Chief Economist of EY, kicked off the conference with a mixed bag of encouraging and discouraging news; uncertainty reigns. A managing director in software from Goldman Sachs, Jack Anstey, discussed How Wall Street Views Digital Transformation in Manufacturing. They love the high-margin recurring revenue of SaaS offerings but look for margin expansion.
Solution Provider Support
The exhibit hall was rich with support. The solution providers supporting this event included
- Broad-based software leaders in PLM, CAD, and manufacturing software, Dassault Systèmes and PTC
- Broad-based ERP, SCM, and beyond providers Infor and Oracle
- MES- and frontline worker-focused providers, Dozuki and Forcam Enisco GmbH
- To specialized software such as Arch Systems (AI and actionable insight in production), Canvas GFX (3D work instructions), Celonis (process mining), Ease.io (shop floor quality and audit), Laserfiche (document management), MaintainX (EAM), Tacton (CPQ), and Zebra Technologies (data collection and management hardware, software, and services)
- To a variety of services: ArcBest(a 3PL with fascinating ways to speed logistics like loading from all four sides of a trailer at once), AT&T Business and Verizon Business (network infrastructure including private 5G), EY , NTT DATA , Rockwell Automation / Kalypso: A Rockwell Automation Business , and Forvis Mazars Group and RSM for tax and consulting.
We also heard from some solution providers directly:
- The President and CEO of Siemens USA, Barbara Humpton, encouraged the audience to repurpose and update our current US facilities. She pointed out how various Siemens business units address issues like AI's power consumption, robots stepping in where workers can’t be hired, and software-defined everything.
- Some of the executives of these sponsors were on panels or presented with their customers. Many also hosted demos of their software.
Thank You, and Looking Forward
The awards gala was dazzling – hundreds of manufacturing professionals in evening gowns and tuxedos. Thank you to Julie’s long-time business friend, David R. Brousell, emcee Lauren Bisset, and the MLC team for the invitation and well-executed event. We hope to join you in Scottsdale, Arizona, June 21-24, 2026, for the next Rethink!
[post_title] => Powerful Connections and Realities at Rethink 2025 [post_excerpt] => [post_status] => publish [comment_status] => open [ping_status] => open [post_password] => [post_name] => mlc-rethink-2025 [to_ping] => [pinged] => [post_modified] => 2025-07-03 01:12:10 [post_modified_gmt] => 2025-07-03 05:12:10 [post_content_filtered] => [post_parent] => 0 [guid] => https://tech-clarity.com/?p=22184 [menu_order] => 0 [post_type] => post [post_mime_type] => [comment_count] => 0 [filter] => raw ) [12] => WP_Post Object ( [ID] => 22209 [post_author] => 2574 [post_date] => 2025-07-01 16:02:15 [post_date_gmt] => 2025-07-01 20:02:15 [post_content] =>How can innovative manufacturers improve their operational performance? With coherent, modern software to run the operation. First Resonance's ION Factory Operating System is designed for manufacturers in space tech, new energy, and other breakthrough products ready to craft fresh manufacturing processes. They have added agentic AI, an updated user experience (UX), and a partner marketplace to showcase ION partners.
ION Intelligence
First Resonance’s ION has long had AI functionality baked into it. With the introduction of ION Intelligence, they have added semi-autonomous workflow agents, which use the power of modern large language models (LLMs to leverage datasets from business operations. These new agents each specialize in specific tasks and domains. Beyond automating data search and retrieval, they keep production and its information flowing without manual handoffs. The initial agent focus is on improving the workflows for how customers have been using ION already.
ION Intelligence can also provide action recommendations. We saw these agents on screen. They showed the various alternative recommendation options and the system’s confidence levels for each recommendation. This can significantly speed up the time to decision and confident action in the plant. As with other LLM-based AI, First Resonance reports that ION Intelligence is improving rapidly, even before launch and wider customer use.
First Resonance integrates data into ION Intelligence using the new but increasingly widely accepted Model Context Protocol (MCP) standard. We see more and more companies using MCP for integration beyond their own set of agents. The benefit is that MCP standardizes communication with APIs and other data sources, becoming a common, consistent language for every AI tool, desktop app, and data source to connect intelligently.
Upgraded UX
User Experience (UX) is crucial to any manufacturing plant floor software. It must serve the operators, technicians, engineers, and supervisors without distracting them from the primary focus of making products. The new UI uses best practices such as choosing dark or light modes, voice capture, OCR, etc.
While the user interface (UI) is part of the upgrade for a clean look and the AI agents on screen, there’s more. The new ION experience also speeds load times for processes that need large quantities of data. Based on how customers have used ION over the past five years, First Resonance made UX changes to address some priority needs in real-world situations.
ION Marketplace
First Resonance has long had partners in PLM, PDM, Finance, Procurement, and more. It has pre-built integrations to 16 systems, and even more through their partnerships with integration platforms like Violet Labs. Their customers use integrations with many ERP systems and other common software platforms. They also have integration and services partners to support customers with developing integrations. The ION Marketplace initially helps ION customers find and connect with these companies. It may evolve for deeper interactions and become a place for customer- or partner-developed extensions in the future.
Market Focus
First Resonance’s target market is quality-critical manufacturers. To date, many have been forward-thinking companies emerging into production for breakthrough products. It is designed for companies that are willing to depart from traditional working methods. Because First Resonance ION includes MES and other capabilities, it might also overlap with existing ERP, SCM, and analytics systems. We suspect traditional A&D, energy, medical device, and robotics makers could learn from the First Resonance approach and streamline data flows beyond traditional operating siloes.
Looking to the Future
We are excited to hear how well First Resonance supports its customers in growing their businesses with sound factory information and guidance. The combination of new items in this release is ambitious, and we agree it’s an excellent fit for what manufacturers need today. Innovation-centered manufacturing companies can benefit from ION’s new AI, UX, and easy ecosystem access.
Thank you, Ron Close, for the advance materials and briefing for Julie Fraser and Rick Franzosa. The launch webinar was also very informative; thank you to Karan Talati, Allan Cutler, and Manav Sanghvi for explaining the news. We look forward to tracking First Resonance’s progress in the market.
[post_title] => First Resonance Updates ION with Agentic AI, UX Improvements, Marketplace [post_excerpt] => [post_status] => publish [comment_status] => open [ping_status] => open [post_password] => [post_name] => ion-ai-ux-marketplace [to_ping] => [pinged] => [post_modified] => 2025-07-03 16:06:41 [post_modified_gmt] => 2025-07-03 20:06:41 [post_content_filtered] => [post_parent] => 0 [guid] => https://tech-clarity.com/?p=22209 [menu_order] => 0 [post_type] => post [post_mime_type] => [comment_count] => 0 [filter] => raw ) [13] => WP_Post Object ( [ID] => 22145 [post_author] => 2572 [post_date] => 2025-06-26 10:07:58 [post_date_gmt] => 2025-06-26 14:07:58 [post_content] => What should Automotive companies consider when integrating ALM and PLM? In today’s automotive industry, software is a critical differentiator. From advanced driver assistance systems (ADAS) to infotainment and over-the-air updates, software brings much opportunity for innovation. As we move toward software-defined vehicles, it is critical that hardware and software development become as integrated as possible. Yet, software is often managed in Application Lifecycle Management (ALM), while hardware remains in Product Lifecycle Management (PLM). This separation creates silos that slow development, increase risk, and hinder innovation. As vehicles become more connected, autonomous, and software-driven, and regulatory requirements tighten, it’s more important than ever to integrate ALM and PLM to establish a digital thread across the entire vehicle lifecycle. In this 20-minute video, Michelle Boucher and PTC’s Meg Folcarelli discuss key considerations for Automotive companies to support the co-development of hardware and software. They cover:- Current product development trends affecting Automotive companies
- The challenges and impacts these trends pose for the industry
- Best practices to tackle these challenges
- What to prioritize when integrating ALM and PLM
- Implementation advice
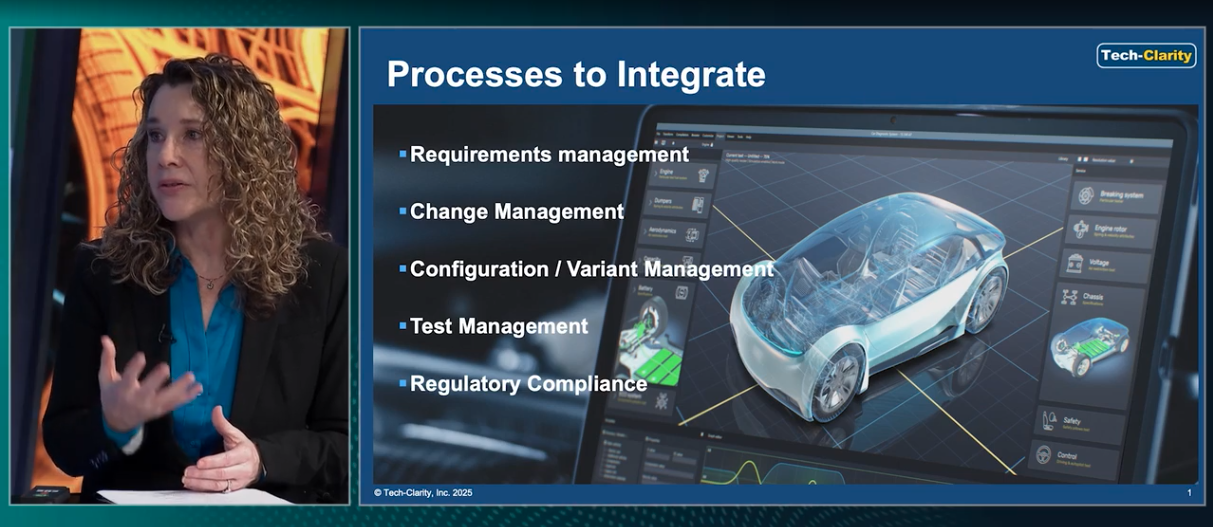
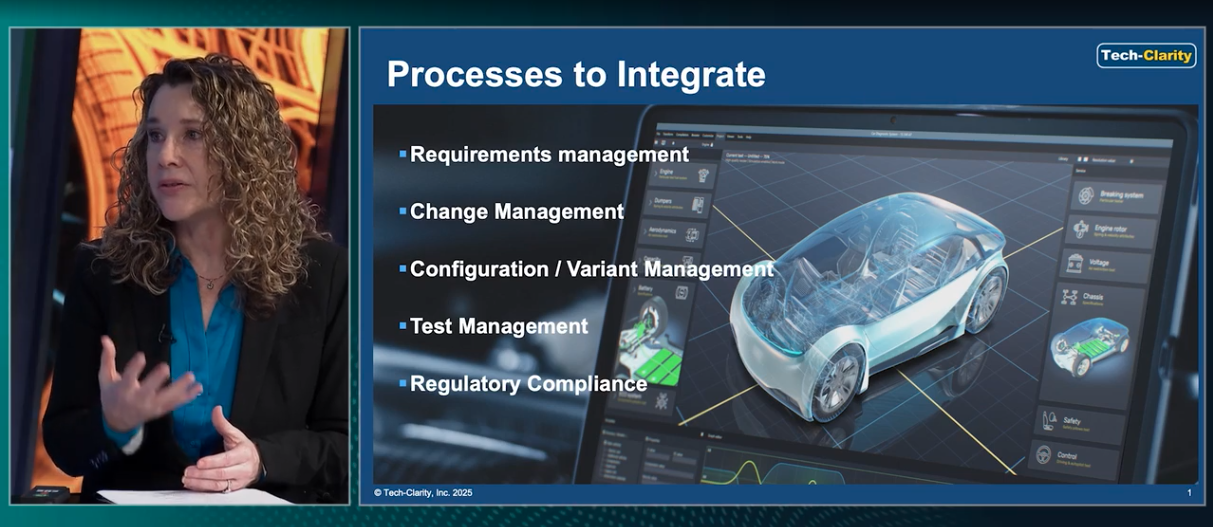
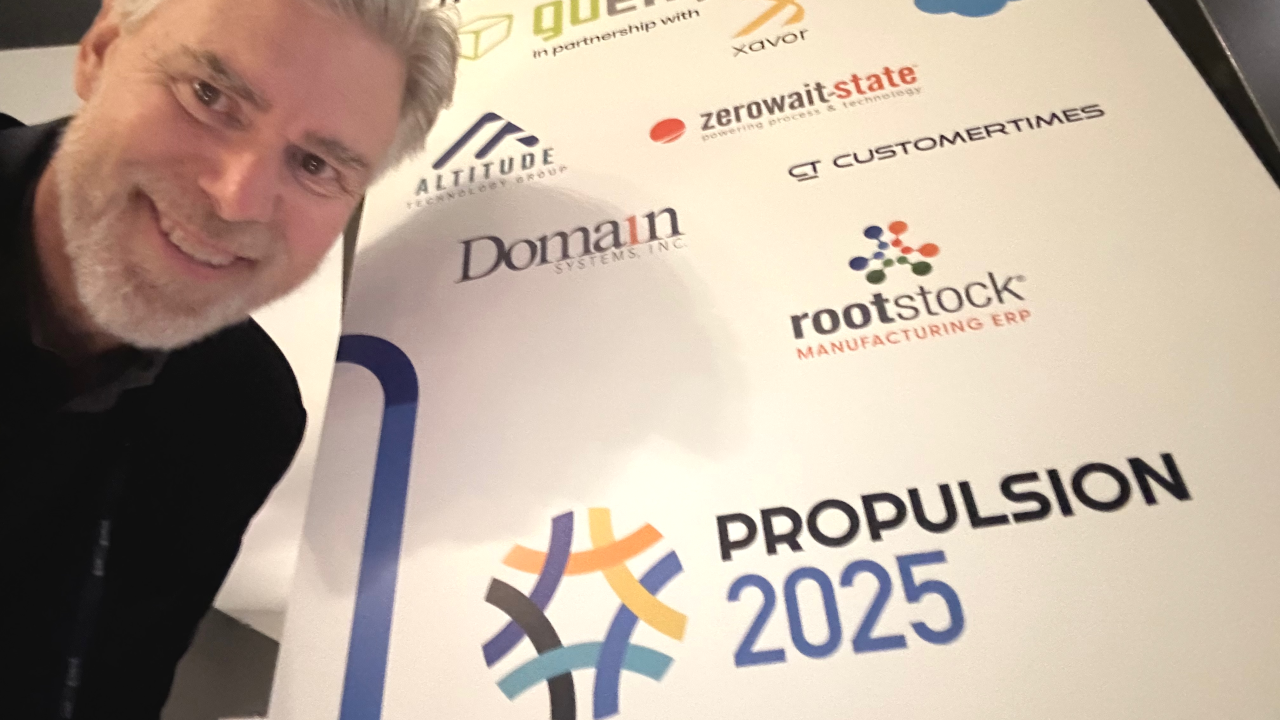
Propulsion 2025
Tech-Clarity’s Jim Brown had the opportunity to join Propulsion 2025, Propel Software’s sixth annual user event and its second in-person conference. It was exciting to share in the energy from the manufacturers using Propel as they gathered to learn from Propel leaders, partners, and especially their fellow customers.
Propel continues to grow in both core PLM capabilities and further their unique Product Value Management (PVM) strategy under the leadership of CEO Ross Meyercord. In addition, they continue to leverage the capabilities of the Salesforce platform to bring new value to their product and customers. This year, Propel announced significant plans for AI with a robust approach that would likely be out of reach for most vendors their size, but is accessible to Propel and their customers through their relationship with Salesforce.
What Makes Propel Special
Let’s step back to discuss Propel’s unique scope. Their PVM (Product Value Management) platform integrates elements of Product Lifecycle Management (#PLM), Quality Management Systems (#QMS), and Product Information Management (#PIM). We’ve written about PVM before and believe it’s a compelling approach for companies looking to better streamline product innovation, product development, and product commercialization. Salesforce also provides the ability for Propel to extend into the product service lifecycle.
Beyond the functional strategy, Propel is interesting because they inherit extremely robust and capable technology underpinnings from the Salesforce platform. Because of this, Propel was cloud-native from the start and can take advantage of Salesforce’s product roadmap investments. This showed up at Propulsion this year with the introduction of #AgenticAI.
The Strategic, Transformative Power of AI
To get people thinking strategically about AI, Propel brought in Ray Wang of Constellation Research, Inc. Ray gave an energetic, well-researched presentation on how companies can leverage AI to redefine and transform their businesses. He discussed examples where new technology opened the door for brand new business models, using CocaCola and Sam’s Club as examples. His talk set the bar for strategic changes similar to what Amazon did to redefine buying experiences as the internet and the world wide web gained traction. It was great food for thought.
Practical and Accessible AI
Following Ray’s talk about strategic, fundamental shifts that are possible by rethinking business were other presentations about how AI can help with more everyday, practical tasks. There was an interesting contrast in the presentations. Because the audience at the event was not necessarily those who could fundamentally change the business, we were encouraged that the following use cases presented by both Salesforce and Propel were approachable, practical, and achievable for the participants.
VP Solutions Marketing Kevin Crothers and Senior Product Marketing Director Jill Mueller demonstrated some of Propel’s current AI offerings such as extracting engineering specs to create PIM data, reading through product documentation to create quiz questions for field service teams, and summarizing product thread information about a serialized asset to create a unified digital thread from engineering and service data. These may not reinvent the business, but they can certainly improve efficiency, quality, and time to market. Although these tactical changes taken individually may seem small, they are achievable, can add value quickly, and in aggregate they provide very strategic improvements.
The Strategic Value of Salesforce’s Agentforce
Salesforce also presented practical examples, including asking questions in Spanish for AI to find and summarize information from English documentation, proactively noticing errors on an asset using real-time data, and providing a 24x7 agent on the website. These capabilities from Salesforce come from Agentforce, Salesforce’s AI platform. Propel is embedding Agentforce capabilities into their platform to create their AI offering, Propel One. Propel currently has two agents available on Salesforce App Exchange: Propel One for Product Engineering and Propel One for Product Information, and plans to ship a series of packaged agents with Propel One, and also allow customers to modify them or create their own to meet their unique needs.
Senior Product Manager Steve Toukmaji and Jill Mueller also presented on AI advancements. They shared Propel’s guiding principles that data is secure, humans stay in the loop, and they will focus on high value “jobs to be done.” They also went into detail about the Agenforce Trust Layer, a very mature approach to managing AI inherited from Agentforce. It’s another example of where Propel gains significant value from Salesforce R&D investments.
Furthering PLM Capabilities
Propel is what we typically call a supply-chain-centric PLM solution as opposed to an engineering-centric PLM. In this way, it serves manufacturers in fast-moving markets who typically procure elements of their product, such as high-tech, electronics, MedTech, consumer goods, and other related industries. Deep CAD integration, in this form of PLM, is a lower priority. Having said that, Propel’s customers are asking for more and Propel is responding. Propel plans to release DesignHub this fall with integration to 10 mechanical and electrical CAD solutions.
Chief Product Officer Eric Schrader shared further product roadmap plans, including demonstrations by Kevin Crothers and Director of Technical Product Marketing Michael Prom. These included trace matrix enhancements, visual communication improvements, and component insights to evaluate BOMs with help from their partner SiliconExpert. One of the more interesting concepts highlights the comprehensive nature of the combined Propel Salesforce offering, connecting product and customer thread in a holistic “Product Graph” that extends fully into the service lifecycle. There is much more than we could cover here, but the key takeaway is that Propel continues to invest across their PVM footprint in addition to introducing a robust AI strategy.
A Unique Opportunity with Agile Customers
There were a number of customer presentations, too many for us to detail here. We do want to mention one interesting trend we heard across the presentations. Several customers mentioned transitioning from Agile. As Oracle is no longer supporting Agile, many diehard companies are being forced to choose a new solution. Given the shared history and deep Agile expertise through Founder and Chairman Ray Hein and Eric Schrader, it’s no surprise they see Propel as a logical replacement option. Propel is not the only choice, nor the only vendor offering a safe haven to these manufacturers. But they are a logical consideration based on the history of the company, the PVM approach, the QMS capabilities built with traceability and compliance in mind, and the customer base.
Key Takeaways
Propel put on an energetic event and customers gained a lot from it. They highlighted key advancements in the product as well as their AI strategy. We look forward to following Propel’s progress and growth.
Thank You
Thank you Propel for including me in your user event. It was educational and enjoyable. We really appreciate events like this where you can see the enthusiasm of the customers and see them eager to learn from their vendor and fellow customers.
Thanks to Erin Keefe and Tom Shoemaker for helping me attend the event, to Michelle Stone , Steve Toukmaji, and Jill Mueller for formal and informal product updates, and to Ross Meyercord and Eric Schrader for strategic updates. It was great to see other PLM friends as well including Ray Hein, Gregory Yow, Nate Brown, and Mike Prom, among others.
[post_title] => Propel Furthers Unique PVM Solution with Agentic AI [post_excerpt] => [post_status] => publish [comment_status] => open [ping_status] => open [post_password] => [post_name] => product-value-management [to_ping] => [pinged] => [post_modified] => 2025-07-03 16:03:55 [post_modified_gmt] => 2025-07-03 20:03:55 [post_content_filtered] => [post_parent] => 0 [guid] => https://tech-clarity.com/?p=22198 [menu_order] => 0 [post_type] => post [post_mime_type] => [comment_count] => 0 [filter] => raw ) [15] => WP_Post Object ( [ID] => 22177 [post_author] => 2 [post_date] => 2025-06-17 00:49:56 [post_date_gmt] => 2025-06-17 04:49:56 [post_content] =>We’ve been excited to get briefed by Makersite over the last two years, and we’ve been impressed. Now, we’re happy to share what we’ve learned. They’re a small company that has big customers, and they’re helping those companies make significant gains on compliance, cost, sustainability, and supply chain risk. Given the impact of today’s global political and economic disruption on manufacturers, these improvements are crucial to success.
Product Lifecycle Intelligence
Makersite is addressing the dirty little secret about sustainable design and DFX in general. Engineers simply don’t know the impact of their decisions on factors like carbon footprint. If manufacturers analyze the impacts after the fact, it’s often too late to impact their design decisions. Makersite plans to change this paradigm by providing engineers with trusted data in the context of their product digital twin during design. If engineers have the right information, they can make better decisions to improve the impacts of their decisions and speed up product development by preventing design rework to meet cost, compliance, sourcing, or sustainability issues. Further, having the right information – what Makersite calls “Product Lifecycle Intelligence” – speeds up time to market by automating product documentation like LCAs (lifecycle assessments), product compliance, and company Scope 3 reporting, among other use cases.
Makersite believes that delivering Product Lifecycle Intelligence will help manufacturers source smarter, design greener, collaborate faster, and build more resilient supply chains. We respect their approach, which addresses sustainability in the broader context of product profitability.
Putting Product Lifecycle Intelligence into Practice
Our recent executive survey shows that manufacturers are facing increased calls for product transparency, for example, through product passports. It also shows that current economic conditions demand effective cost management and that trade wars and tariffs are making already challenging supply chains riskier. Makersite’s timing to offer Product Lifecycle Intelligence couldn’t be better.
Designing products like high tech electronics, which have complex supply chains, demands design tradeoffs that must be optimized early in design. Makersite’s Product Lifecycle Intelligence SaaS platform is based on a digital twin data model created from engineering BOMs. These data models, graph models that customers can refine, serve as both a visual representation of the product and the backbone on which to make LCA decisions.
From there, Makersite offers algorithms to help manufacturers map their digital twins to relevant data from a wide variety of sources. While they can use APIs to pull information from customers’ systems, such as ERP, PLM, or CAD, they also provide their own rich dataset. Makersite is not just an integration and calculation engine. They provide their own “decision-ready” data, including deep-tier supply chain information. They claim to provide the “world’s largest supply chain database” with over 150 external and verified databases.
Mapping this information to the digital twin creates the intelligence needed to make the right decisions and do so on a timely basis. We were assured that the data can be trusted because it is not a black box. Makersite offers a confidence score on their data and explained that transparency remains a cornerstone of Makersite’s approach. The platform allows customers to trace data sources, understand how the data impacts the modeling, and explore alternative options.
LCA Meets AI
Without diving too deeply into the technology, it’s important to understand the role artificial intelligence (AI) and machine learning (ML) play in Makersite’s ability to create a contextually rich digital thread mapping. Makersite refers to their platform capabilities as “AI powered Product Lifecycle Intelligence.” AI is a natural fit to map data from a variety of sources and formats into something meaningful. Makersite explained that their automation and AI capabilities ensure the most accurate and granular mapping for supply chain models, while continuously learning from user-driven changes to validate and refine the product models and reflecting those updates in future runs.
Customers
We mentioned that Makersite has an impressive customer list, with many in consumer electronics. They also shared that they have success in the construction and chemicals industries. But they are applicable elsewhere, as well. Some notable customers they list on their website include Barco, Schaeffler, Cummings, 3M, and Lenovo. One customer, Microsoft, jointly shared a case study with Makersite. The results were impressive, including a 30% reduction in carbon footprint in design for the Surface Pro, in addition to making it more energy efficient in use. They also leveraged digital twins to source better materials. They then applied this approach to other Microsoft consumer products and their data centers.
Our Take
Makersite is serving a valuable role at a time when manufacturers need it. Their ability to model product digital twins from customer data and enrich it with additional information from customer systems, third-party data, and Makersite’s own dataset makes it compelling. Their use of AI to contextually map data is a unique approach and solves quite a few of the challenges companies have faced in initiatives like LCA in the past. We’re excited to see their further success and adoption in the industry.
Thank You
Thanks to Nicolás Artímez Wetz for the briefings and Vaqais Hussain for initiating the conversations.
[post_title] => Makersite Delivers Product Lifecycle Intelligence [post_excerpt] => [post_status] => publish [comment_status] => open [ping_status] => open [post_password] => [post_name] => product-lifecycle-intelligence [to_ping] => [pinged] => [post_modified] => 2025-07-03 00:50:25 [post_modified_gmt] => 2025-07-03 04:50:25 [post_content_filtered] => [post_parent] => 0 [guid] => https://tech-clarity.com/?p=22177 [menu_order] => 0 [post_type] => post [post_mime_type] => [comment_count] => 0 [filter] => raw ) [16] => WP_Post Object ( [ID] => 22124 [post_author] => 2572 [post_date] => 2025-06-11 07:25:01 [post_date_gmt] => 2025-06-11 11:25:01 [post_content] => What are your thoughts on the state of product development?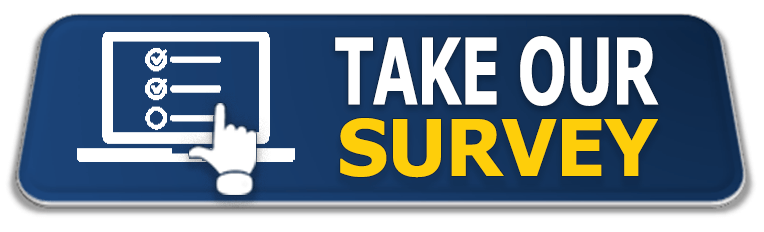
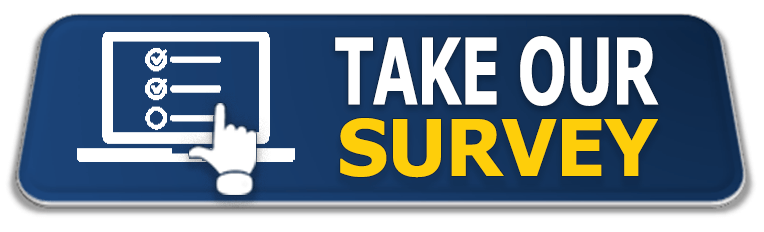
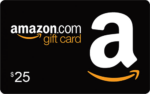
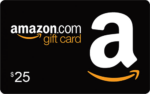
ComplianceQuest made some significant announcements at its recent ConQuest customer conference. The first was to identify the space where they play, as a platform and integrated software suite to clean up the messy “middle office.” They also continued to add more agentic AI to the platform to support the people using the applications sitting on it. The other key news came before the event: the release of SupplierQuest, which reaches beyond supplier quality to supplier management, onboarding, collaboration, and performance management.
Cleaning Up the Middle Office
ComplianceQuest has named its vision the Connected Middle Office Platform. Think about how ERP long ago integrated back-office data and workflows, such as HR, Finance, and Supply Chain, for greater efficiency. Since then, CRM has helped optimize the front office activities, including sales, marketing, and service. What’s in the middle? ComplianceQuest says core operations, and they are fragmented, manual, and lack a way to collaborate among functions.
With a proven platform and multi-module solutions for QMS, EHS, Supplier Management, and PLM, ComplianceQuest has a strong story for this middle office. Our research supports the ComplianceQuest view. In our Making Manufacturing Analytics and AI Matter survey, manufacturers’ top investment aim is gaining easy access to high-quality, timely, and complete plant data. Today, many struggle to share operations data, put it in context, and use it to make sound decisions. The ComplianceQuest platform, with its single database, enables collaboration and closed-loop processes across these disciplines and data sets. Consider how a DFMEA can be connected to complaints, CAPAs, and regulatory reports.
AI Agents
AI agents to assist humans in this middle office work are trained only on each customer’s data. ComplianceQuest has incorporated its years of experience in developing these agents. CQ AI agents focus on activities such as generating content, finding and connecting relevant data across the system, forecasting future outcomes, leveraging chat to intake information and create records , and communicating with suppliers through intelligent emails that turn into actionable records . This reduces redundant and duplicated data, enhances worker productivity, and augments data-driven decisions.
ComplianceQuest has been releasing AI since 2022, primarily as categorization and prioritization and retrieve and relate capabilities. Predictive AI is already embedded and is part of the quality maturity index, supplier performance, and safety incidents functionality. AI is a top priority on the CQ roadmap to improve efficiency and costs and mitigate risk with predictions. All of this is embedded in the platform, not separately licensed, as are the advanced analytics.
Supplier Management
In March, ComplianceQuest introduced its SupplierQuality suite, expanding beyond supplier quality to encompass more aspects of supplier relationship management. Examples include:
- Enabling onboarding with collaboration between quality and procurement
- First article inspection to qualify a supplier, pulling the specs and BOM from PLM.
This expansion leverages the collaborative platform and other solutions and adds capabilities to foster greater success with suppliers during a time of supply chain change.
Looking Forward
ComplianceQuest has always leveraged the Salesforce platform for connectivity. As the company builds out its middle office platform and suite, we will continue to watch for new releases, additions, and improvements. Thank you, Nikki Willett, for catching us up on the latest news from ComplianceQuest.
[post_title] => ComplianceQuest Claims Middle Office and Adds Agents [post_excerpt] => [post_status] => publish [comment_status] => open [ping_status] => open [post_password] => [post_name] => compliancequest-middle-office [to_ping] => [pinged] => [post_modified] => 2025-06-05 10:14:29 [post_modified_gmt] => 2025-06-05 14:14:29 [post_content_filtered] => [post_parent] => 0 [guid] => https://tech-clarity.com/?p=22080 [menu_order] => 0 [post_type] => post [post_mime_type] => [comment_count] => 0 [filter] => raw ) [18] => WP_Post Object ( [ID] => 21935 [post_author] => 2574 [post_date] => 2025-05-29 07:00:58 [post_date_gmt] => 2025-05-29 11:00:58 [post_content] => Is AI just a shiny object, or is AI delivering value in manufacturing? Our latest infographic exposes five practices that our research shows Top Performers are using to ensure value for their company. Walk through this infographic to learn a few things you can do to move AI from being a distraction or shiny object to delivering significant value, often in a very short time. Due to the interest in AI and its ability to deliver value quickly, many manufacturers have already invested. That means everyone else needs to move quickly. This infographic shares ways to move with greater confidence that you’ll end up with strong business value from leveraging AI with complex manufacturing data sets. Yes, every company will need to invest to get the value - at least time and energy to plan for projects and experiment. Yet some of the other practices are things any company can do for greater success without buying new software. Others might require new technology, depending on your current solution set and data stack. Walk through the infographic - and up the ladder - to achieve the value your company deserves from its AI efforts. Learn a few tips to get a positive impact quickly for your company! This is based on the recent research Making Manufacturing Analytics and AI Matter Tech-Clarity conducted with thanks to MESA International for partnering with us. Special thank you also to the program's sponsors, Aegis Software, Arch Systems, Epicor, and GE Vernova. It was a collaborative effort, and we appreciate everyone's inputs.

Last week, we had a chance to attend the Hitachi Digital Services Analyst & Advisor event in Dallas. The gathering offered compelling insights into the company’s strategic direction and differentiated capabilities. Through a series of thought-provoking presentations and fireside chats, one theme emerged with clarity and consistency: Hitachi Digital Services’ deep-rooted engineering expertise sets it apart. This foundational strength enables the company to understand its customers’ complex challenges and validate solutions across Hitachi’s diverse industrial ecosystem and co-innovate with clients to drive real business outcomes. Since we focus a lot on #digitaltransformation in product design, innovation, and manufacturing, we found several relevant takeaways worth highlighting.
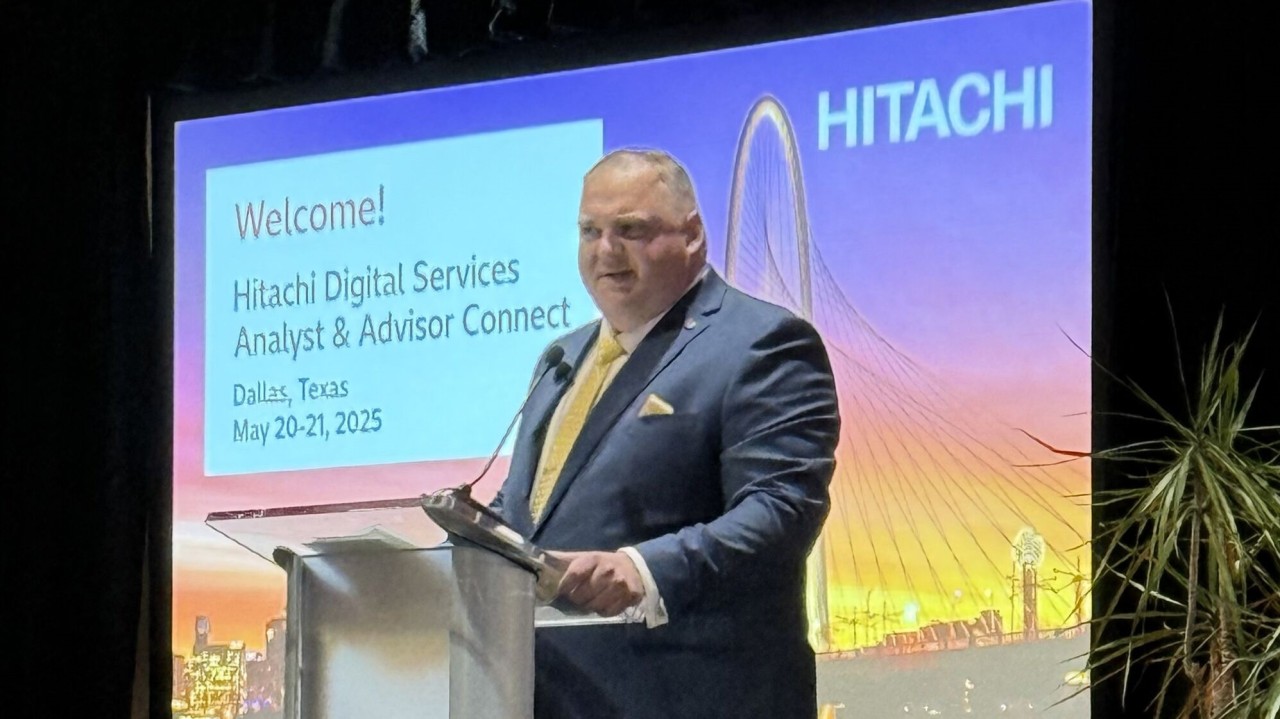
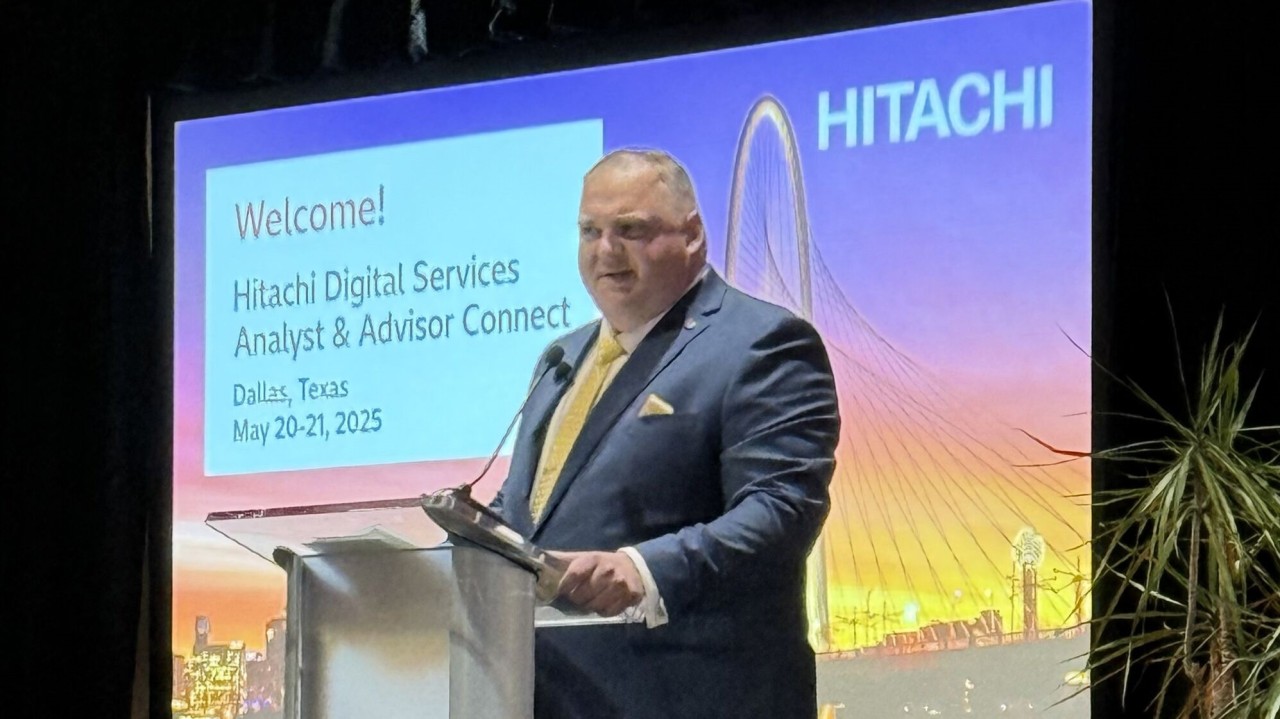
Transform Manufacturing by Enabling the Digital Thread
Digital transformation in manufacturing is no longer optional but an urgent imperative. Industry leaders recognize that embracing this shift is essential to sustaining profitability by eliminating inefficiencies, unlocking new revenue streams, and navigating an increasingly complex environment shaped by product complexity, regulatory pressures, and geopolitics. A foundational step in this journey is establishing a robust digital thread by integrating data across diverse software systems and physical equipment. This is where Hitachi Digital Services stands out. Leveraging deep engineering expertise honed through collaboration with sister companies renowned for their manufacturing excellence, Hitachi Digital Services brings a practical understanding of product development processes. Coupled with their PLM and MES implementation capabilities, they are uniquely positioned to help manufacturers drive digital transformation across the value chain.
Unlock Value through AI and Manufacturing Analytics
Manufacturers are increasingly prioritizing investments in AI and analytics. As highlighted in Tech-Clarity, Inc.'s research by Julie Fraser, Making Manufacturing Analytics and AI Matter, early adopters are already realizing significant gains, ranging from cost reduction and productivity improvements to enhanced quality, error-proofing, and better delivery performance. This space is a natural fit for Hitachi Digital Services, which showcased powerful use cases such as a rail application where edge computing in the train enables real-time data analysis from sensors monitoring track conditions and overhead power lines, directly enhancing safety outcomes. With modern factories generating massive volumes of data, Hitachi Digital Services is ideally positioned to help manufacturers harness this information to optimize energy usage, drive quality, and maximize overall equipment effectiveness.
Secure IT-OT Convergence
The convergence of Information Technology and Operational Technology is a strategic enabler for manufacturers seeking to enhance operational efficiency, reduce costs, improve decision-making, and drive innovation. However, the path to IT-OT integration is often hindered by legitimate #cybersecurity concerns. Cyber threats, including data breaches, IP theft, ransomware, and operational disruptions, pose significant risks to brand reputation and profitability. To fully capitalize on the promise of IT-OT convergence, cybersecurity must be embedded as a core foundation. Hitachi Digital Services brings deep cybersecurity expertise through its partnership with Hitachi Cyber, offering tailored protection strategies and best-practice implementations. Their ability to integrate security seamlessly into digital transformation initiatives, along with providing managed security services, makes them a trusted partner in securing the connected factory of the future.
Our Takeaways on Hitachi Digital Services
In conclusion, the Hitachi Digital Services Analyst event provided valuable insights into leveraging its deep engineering heritage and cross-division expertise to drive impactful digital transformation for its manufacturing customers. Their capabilities in enabling the digital thread, deploying AI and analytics, and securing IT-OT convergence align closely with the critical needs of manufacturers. We were especially impressed by their practical, field-tested approach and commitment to co-innovation. These strengths position Hitachi Digital Services as a trusted partner in helping manufacturers unlock efficiency, resilience, and innovation. We thank Patrick Corcoran and Mahesh Hanumanthu for the opportunity to participate in this event.
[post_title] => Hitachi Digital Services Analyst & Advisor Connect: Three Key Takeaways for Manufacturers [post_excerpt] => [post_status] => publish [comment_status] => open [ping_status] => open [post_password] => [post_name] => hitachi-digital-services-analyst-advisor-connect-2025 [to_ping] => [pinged] => [post_modified] => 2025-06-05 10:23:11 [post_modified_gmt] => 2025-06-05 14:23:11 [post_content_filtered] => [post_parent] => 0 [guid] => https://tech-clarity.com/?p=22088 [menu_order] => 0 [post_type] => post [post_mime_type] => [comment_count] => 0 [filter] => raw ) ) [post_count] => 20 [current_post] => -1 [in_the_loop] => [post] => WP_Post Object ( [ID] => 22414 [post_author] => 2578 [post_date] => 2025-07-31 12:02:15 [post_date_gmt] => 2025-07-31 16:02:15 [post_content] =>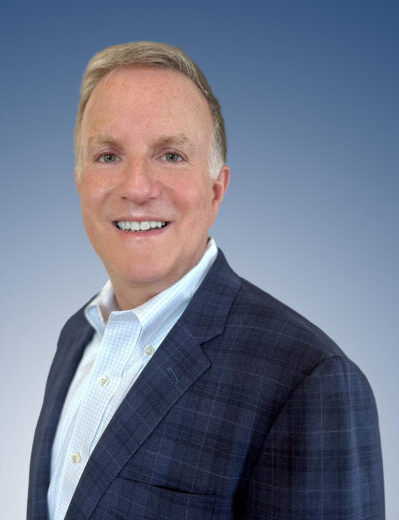
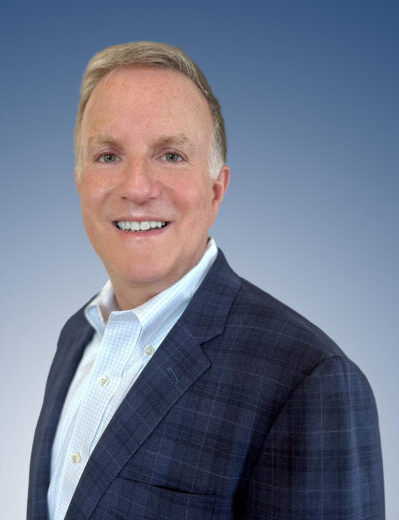
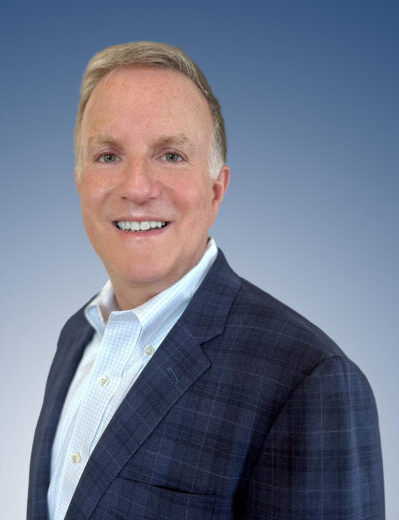
Howie Markson is the Director of Research for Digital Innovation at Tech-Clarity, where he covers digital innovation across product design, simulation, PLM, PDM, SLM, IoT, AI, and other product development solutions for manufacturing and industrial companies. Howie has over 25 years’ experience as an engineer, software product manager, and technology marketing professional. He brings a deep understanding of the needs of manufacturing organizations and how technology can help address their business challenges. Howie enjoys engaging with other industry leaders, manufacturers, and technology users to share in practical ways the value of digital transformation to improve business performance.
Previously, Howie served as Global Offer Marketing Director at Dassault Systèmes, where he led the Brand Offer Marketing teams for design, simulation, PLM, data science, life sciences,and manufacturing applications. Prior to Dassault Systèmes, Howie held senior-level marketing, product marketing, and product management positions at several successful startups and leading technology companies, including PTC, Cisco Systems, and SpaceClaim Corporation (now ANSYS). He began his career as a mechanical engineer at Raytheon Corporation (now RTX). Howie holds a BS in Mechanical Engineering from the University of Colorado and an MBA from Northeastern University.
Howie enjoys being active outdoors no matter the weather, and is currently learning to play the guitar. No concert date has been set.
[post_title] => Howie Markson [post_excerpt] => [post_status] => publish [comment_status] => closed [ping_status] => closed [post_password] => [post_name] => howie-markson [to_ping] => [pinged] => [post_modified] => 2025-07-31 17:28:24 [post_modified_gmt] => 2025-07-31 21:28:24 [post_content_filtered] => [post_parent] => 24 [guid] => https://tech-clarity.com/?page_id=22414 [menu_order] => -14 [post_type] => page [post_mime_type] => [comment_count] => 0 [filter] => raw ) [comment_count] => 0 [current_comment] => -1 [found_posts] => 762 [max_num_pages] => 39 [max_num_comment_pages] => 0 [is_single] => [is_preview] => [is_page] => [is_archive] => [is_date] => [is_year] => [is_month] => [is_day] => [is_time] => [is_author] => [is_category] => [is_tag] => [is_tax] => [is_search] => [is_feed] => [is_comment_feed] => [is_trackback] => [is_home] => 1 [is_privacy_policy] => [is_404] => [is_embed] => [is_paged] => [is_admin] => [is_attachment] => [is_singular] => [is_robots] => [is_favicon] => [is_posts_page] => [is_post_type_archive] => [query_vars_hash:WP_Query:private] => 2c32b1671fe755f651485a21598d7320 [query_vars_changed:WP_Query:private] => 1 [thumbnails_cached] => [stopwords:WP_Query:private] => [compat_fields:WP_Query:private] => Array ( [0] => query_vars_hash [1] => query_vars_changed ) [compat_methods:WP_Query:private] => Array ( [0] => init_query_flags [1] => parse_tax_query ) )
All Results for "All"
WMS for Uncertain Times: What to Consider
What does it take for WMS software to not only run a complex warehouse operation in uncertain times, but grow and change with the company over many years? Julie Fraser will be joining Kenny William of Parts Town who has done just that and Scott Kramer of Infios, their WMS software partner for about 10…
Dassault Systèmes Shares Updated Strategy: 3D UNIV+RSES
Dassault Systèmes’ Strategic Evolution We recently had the opportunity to attend an invitation-only analyst event in Paris. The event offered general updates on the Dassault Systèmes business, brand news, and industry experiences. Some of the most important discussions, however, revolved around their new business strategy. Although the strategy was announced earlier this year, this was…
Rhize Enables Enterprise Digital Transformation with Ontology-Based Data Hub
Can ISA95 rescue large manufacturers’ digital transformation efforts? Early evidence suggests that it can, when deployed as a knowledge graph, exposed as the schema of a standard data model. The ISA95 standard is the basis for the ontological structure of Rhize Manufacturing Data Hub. This headless, event-driven, real-time system provides a clean, single source of…
CTS Article on Rick Franzosa’s MES Industry 4.0 Summit Presentation
Will AI provide instant intelligence to MES? Not immediately. This is what Tech-Clarity’s Rick Franzosa said in his presentation on June 13th at the MES & Industry 4.0 International Summit in Portugal. His talk was titled “No Turning Back: MES/MOM enters the age of AI” and captured plenty of attention. Mark Venables, the Editor-in-Chief of…
Five Ways to Get more Business Value from PDM
Product Data Management (PDM) is table stakes for today’s manufacturers. Effectively managing design data is mandatory for even small development teams to control, access, and share their product data. These basic PDM capabilities deliver significant operational value by keeping design teams organized and efficient. The PDM backbone, though, is also the foundation for even greater…
TilliT Low-Code MES and APS Soon to Weave into Roima
Can multi-tenant cloud-based low-code software run and optimize production operations? Apparently, some companies are using TilliT for just that. The combination of MES with quality, AI-powered scheduling, analytics, and edge technology serves not just mid-market but also smaller and larger companies. Partners and manufacturers are deploying the system themselves after just a few days of…
Meet Your Factory Lifecycle Goals like a Top Performer
How can manufacturers digitally transform their factory lifecycle to get the most out of their plant investments? As highlighted in Tech-Clarity’s eBook “Digitally Transforming the Factory Lifecycle,” top manufacturers have adopted more digital tools and taken a collaborative, integrated approach across the factory lifecycle. This infographic explains how companies can digitally transform factory designs and…
Data Time Space: Is CI the Killer App for AR?
Why hasn’t Augmented Reality (AR) had a greater uptake in the manufacturing market? Maybe it had not found the best use. Data Time Space believes they may have found the killer app for AR: speeding continuous improvement (CI) and freeing CI experts to do the analysis, not the data collection. This young company enables manufacturers…
Warehouse Management Systems (WMS)
What makes warehouse management software (WMS) work for larger enterprises over the long haul? As uncertain as the economy, supply chain, and labor market are, WMS capabilities and fit can determine long-term business success. Yet many systems are relatively rigid and require custom coding by the solution provider or a partner to make updates. Some…
Parsec Keeps Growing, TrakSYS Gets Easier to Fit & Scale
What might batch industry manufacturers still desire in their enterprise-grade MES? Maybe simpler ways to configure, roll out, and manage the system. TrakSYS MES V13 features major upgrades in solution creation and templates. It also prepares for cloud deployment, expands containerization, includes MQTT, and maintains a clean user interface— the kind of UI that has…
Powerful Connections and Realities at Rethink 2025
Where can you meet senior manufacturing leaders who are taking strides toward digital transformation and learning from one another? One venue is the Manufacturing Leadership Council’s (MLC) annual Rethink conference. In addition to a packed two-and-a-half-day conference, the program included an MLC member meeting and an awards banquet. The MLC’s mission is “to help senior…
First Resonance Updates ION with Agentic AI, UX Improvements, Marketplace
How can innovative manufacturers improve their operational performance? With coherent, modern software to run the operation. First Resonance‘s ION Factory Operating System is designed for manufacturers in space tech, new energy, and other breakthrough products ready to craft fresh manufacturing processes. They have added agentic AI, an updated user experience (UX), and a partner marketplace…
Automotive: ALM and PLM Better Together
What should Automotive companies consider when integrating ALM and PLM? In today’s automotive industry, software is a critical differentiator. From advanced driver assistance systems (ADAS) to infotainment and over-the-air updates, software brings much opportunity for innovation. As we move toward software-defined vehicles, it is critical that hardware and software development become as integrated as possible….
Propel Furthers Unique PVM Solution with Agentic AI
Propulsion 2025 Tech-Clarity’s Jim Brown had the opportunity to join Propulsion 2025, Propel Software’s sixth annual user event and its second in-person conference. It was exciting to share in the energy from the manufacturers using Propel as they gathered to learn from Propel leaders, partners, and especially their fellow customers. Propel continues to grow in…
Makersite Delivers Product Lifecycle Intelligence
We’ve been excited to get briefed by Makersite over the last two years, and we’ve been impressed. Now, we’re happy to share what we’ve learned. They’re a small company that has big customers, and they’re helping those companies make significant gains on compliance, cost, sustainability, and supply chain risk. Given the impact of today’s global…
The State of Product Development Survey
What are your thoughts on the state of product development? We are researching the state of product development, including the challenges, capabilities, and future plans manufacturers have. We are exploring questions such as, what challenges do you face? How well do hand-offs between engineering and manufacturing work? Can you find the skilled workers you need?…
ComplianceQuest Claims Middle Office and Adds Agents
ComplianceQuest made some significant announcements at its recent ConQuest customer conference. The first was to identify the space where they play, as a platform and integrated software suite to clean up the messy “middle office.” They also continued to add more agentic AI to the platform to support the people using the applications sitting on…
Five Practices to Ensure Value from AI in Manufacturing
Is AI just a shiny object, or is AI delivering value in manufacturing? Our latest infographic exposes five practices that our research shows Top Performers are using to ensure value for their company. Walk through this infographic to learn a few things you can do to move AI from being a distraction or shiny object to…
Hitachi Digital Services Analyst & Advisor Connect: Three Key Takeaways for Manufacturers
Last week, we had a chance to attend the Hitachi Digital Services Analyst & Advisor event in Dallas. The gathering offered compelling insights into the company’s strategic direction and differentiated capabilities. Through a series of thought-provoking presentations and fireside chats, one theme emerged with clarity and consistency: Hitachi Digital Services’ deep-rooted engineering expertise sets it…