Jim Brown, Michelle Boucher, and I got an introduction to Canvas GFX and its Envision product for interactive work instructions in a recent briefing. The question I, as the manufacturing analyst had, was: Can a system for model-based interactive work instructions really be easy enough for non-engineering users to embrace? Canvas GFX says yes, and…
- Manufacturing process instructions
- SOPs
- Technical documentation or manuals
- employee training
- MRO or field service repair guides
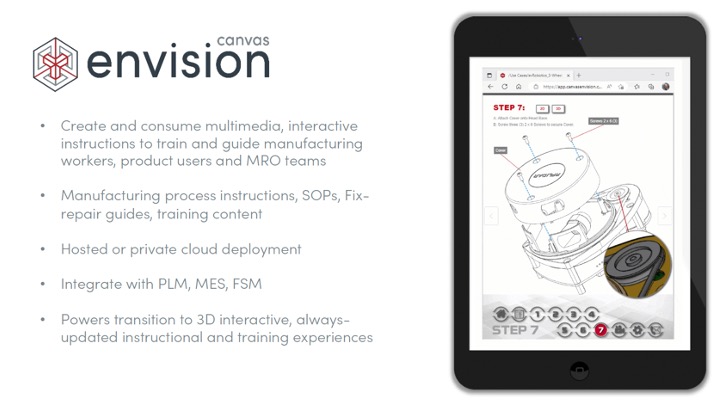
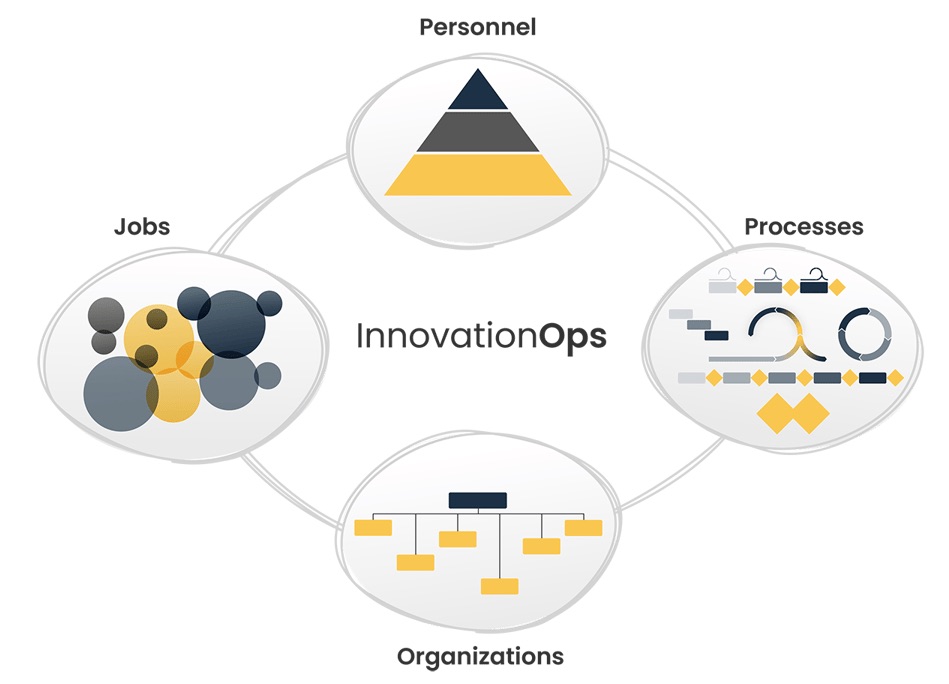
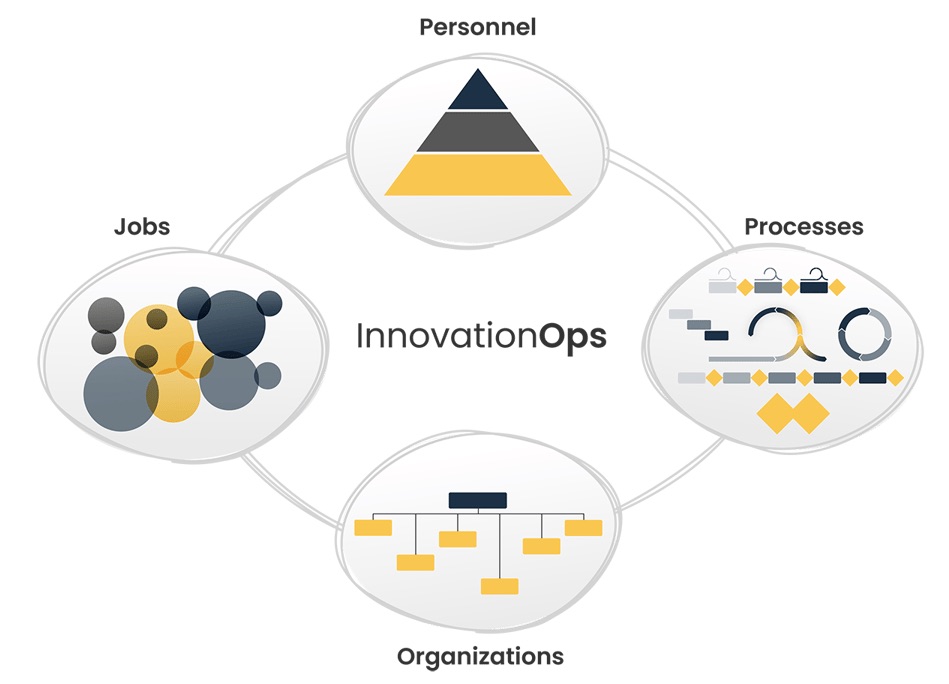
- CalcuQuote: Purchasing automation software for electronics manufacturing service companies or contract manufacturers based in Dallas, TX, USA
- camLine: MES and advanced SPC-based quality for semiconductor and high tech industries that originated in Germany
- TenForce: Environmental health and safety (EH&S) software company out of Belgium that is strong in chemicals
- sedApta: Supply chain planning, execution, and intelligence solutions with strength in food and beverage and customers in process, batch, and discrete industries out of Italy has Elisa as a minority owner
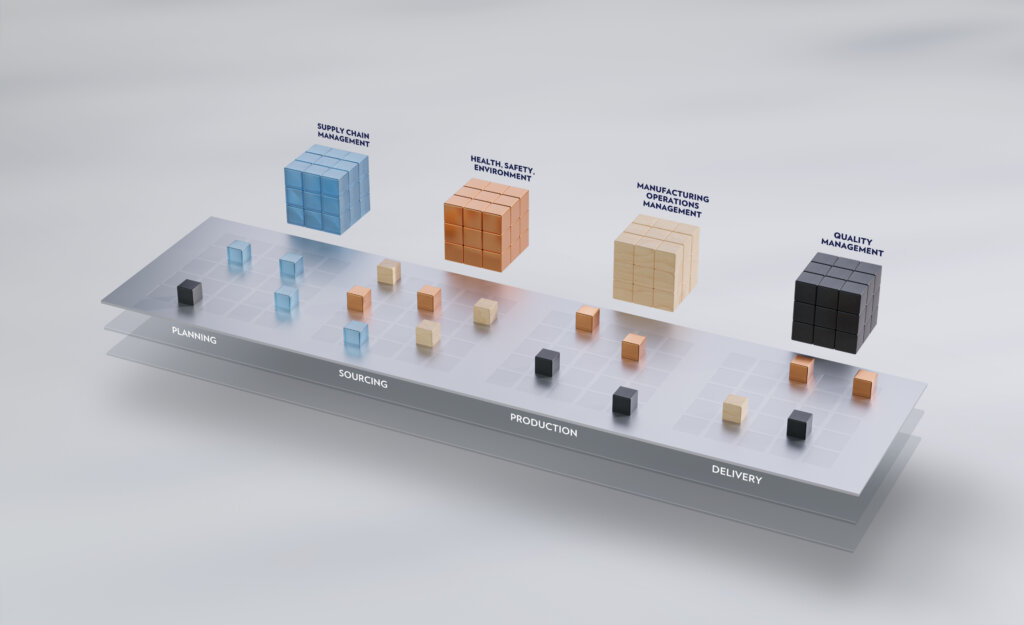
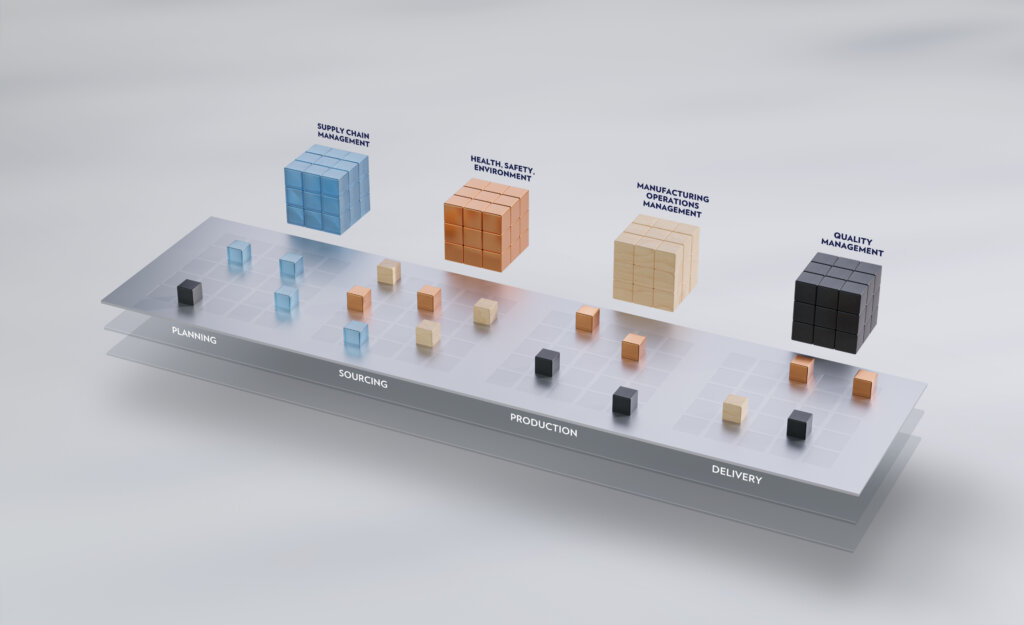
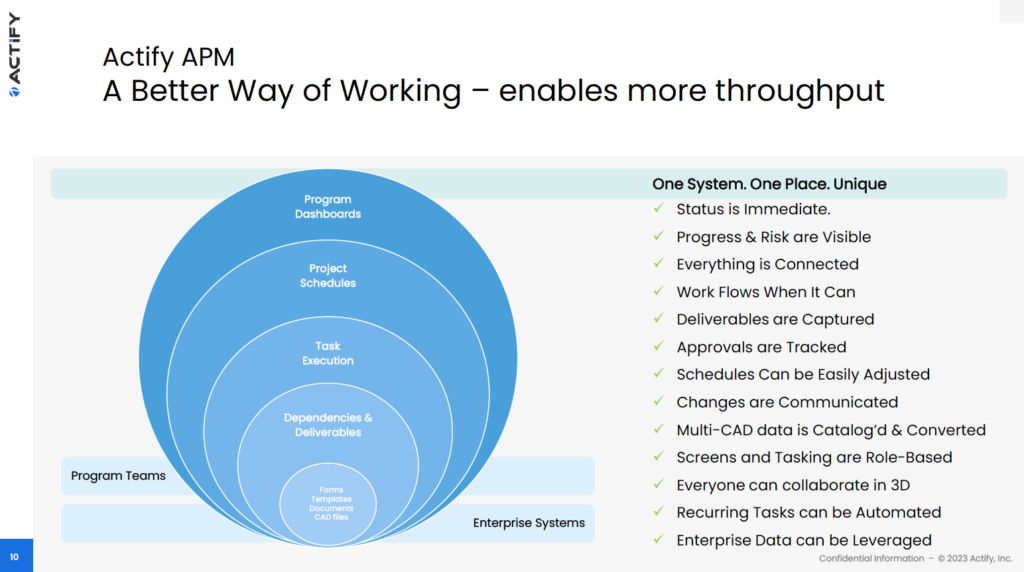
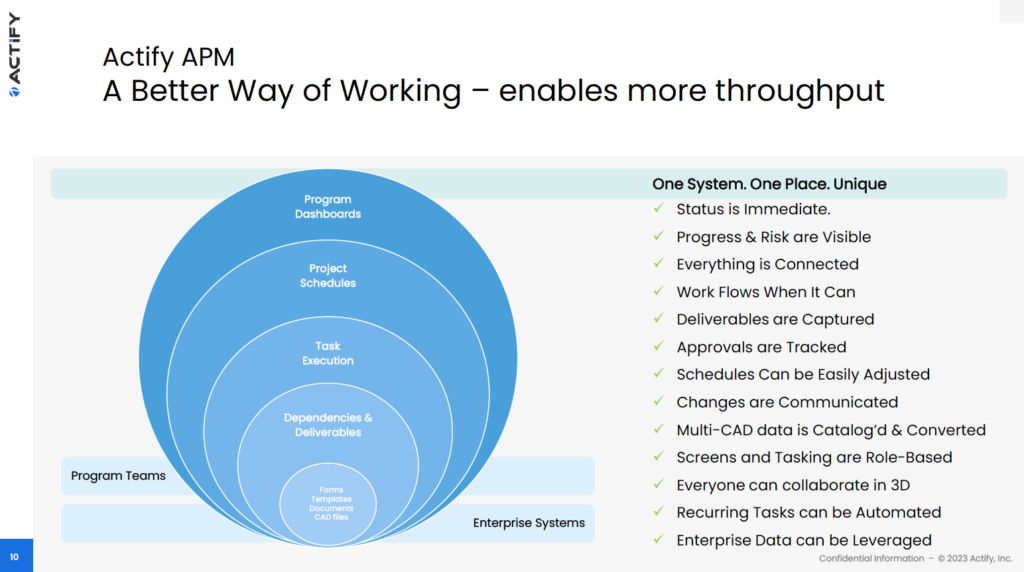
- How digital twin of operations and MES support rapid innovation while ensuring high-quality, compliant, and cost-effective operations
- Why manufacturing matters through the lifecycle of life sciences products starting in R&D and clinical trials
- How digital twin and MES support the data-driven Quality by Design (QbD) approach regulators demand
- Benefits of recognizing issues earlier in the cycle
- Specific benefits of virtual and real views that stay in sync
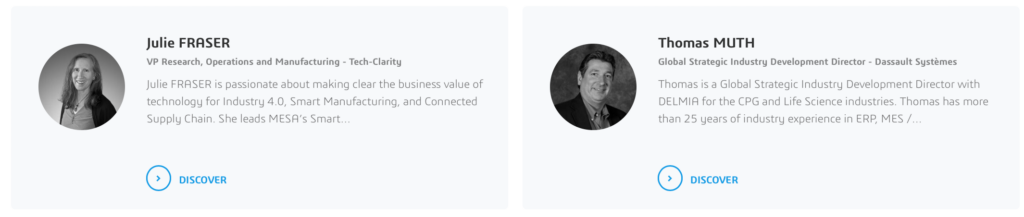
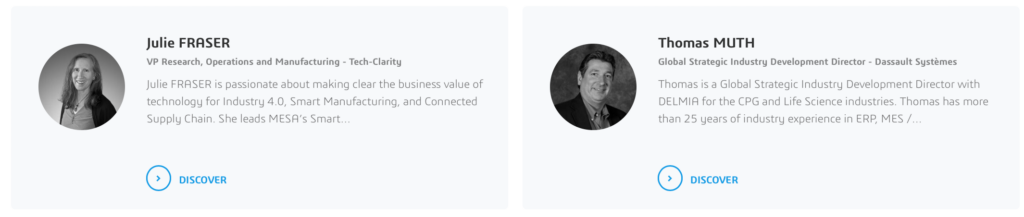
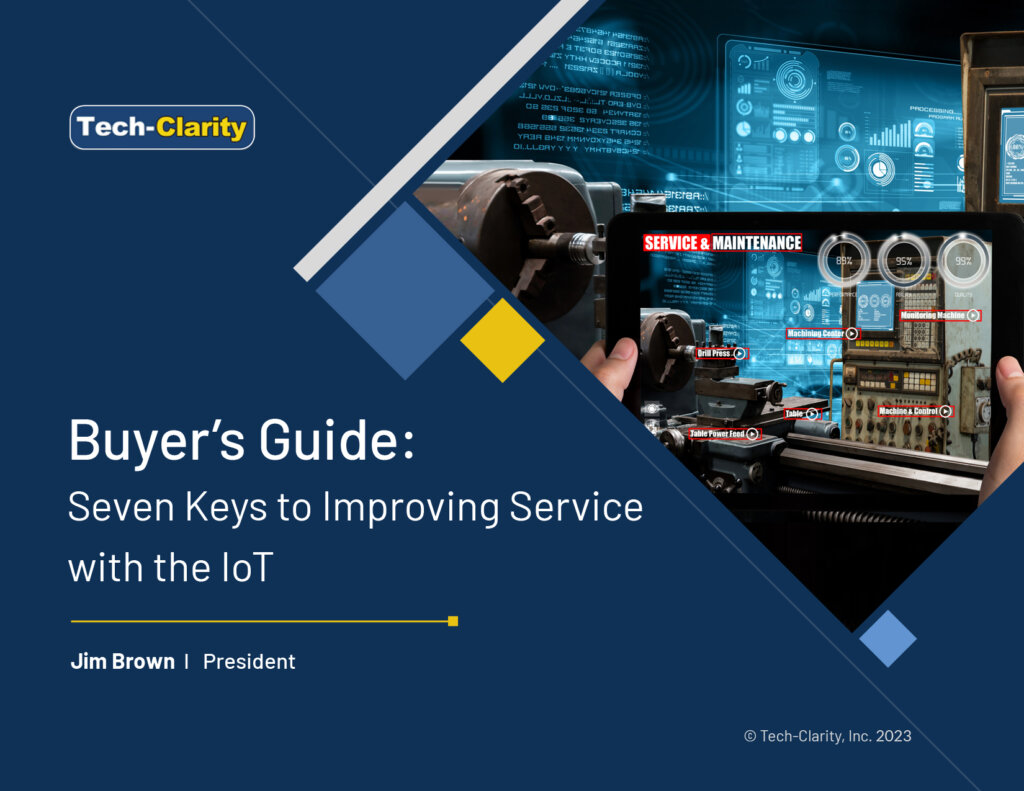
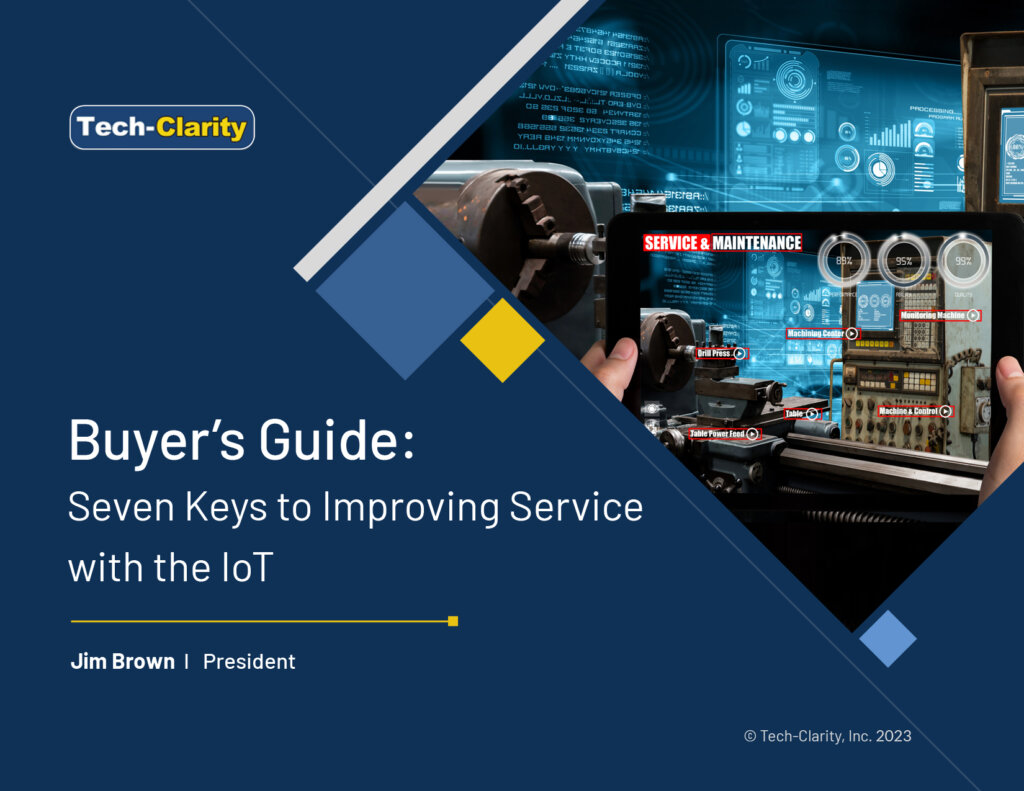
Table of Contents
- Improving Service Profitability with Condition Monitoring
- Begin the Condition Based Monitoring Journey
- Set Your Business Targets
- Access Equipment and Equipment Data
- Communicate with Equipment
- Transform Data to Increase Value
- Analyze Data to Create Service Intelligence
- Share Actionable Service Information
- Implementation and Adoption
- Selecting a Strategic Partner
- Next Steps
- Buyer's Guide Checklist
- Acknowledgments
Condition Based Monitoring Drives Improvements
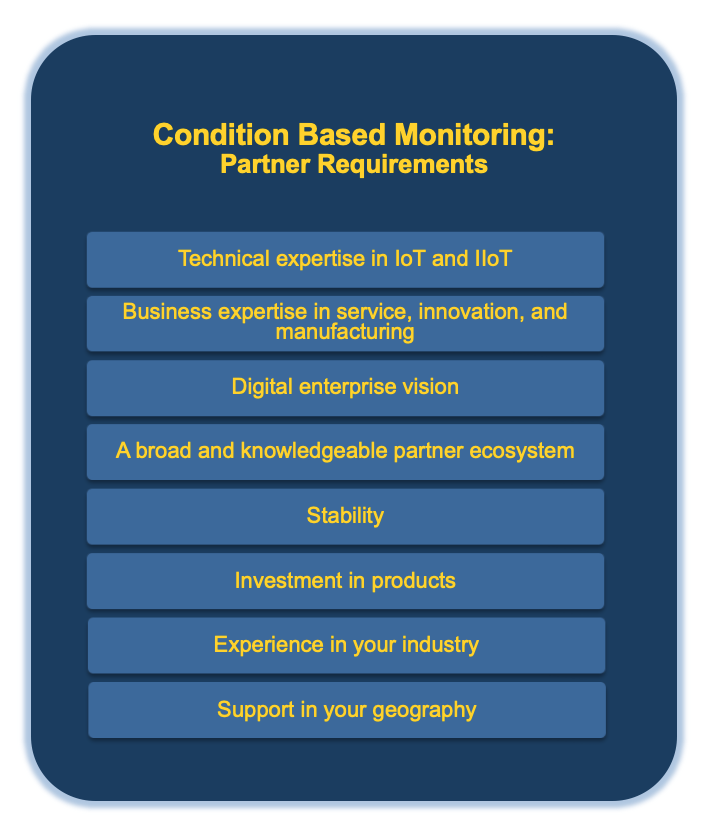
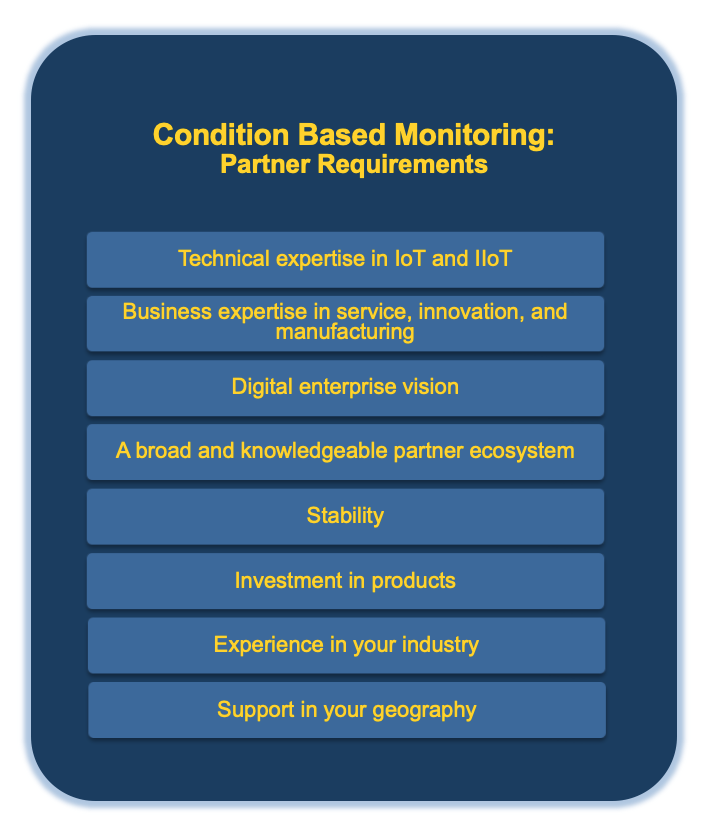
Improving Service Profitability with Condition Monitoring
Service is a Proven Value Driver The most common way that companies gain tangible performance gains from IoT is through improved service. The IoT lets companies transform service to generate more – and more profitable – service revenue. They do this by moving from reactive to proactive to predictive service. Service is an excellent opportunity to leverage advanced technologies like AI, machine learning, and big data analytics. The most common first step is reducing the cost of service through remote, condition based monitoring and is within reach for most companies. In addition, companies can improve performance through new service delivery processes like remote service. Use this Guide to Achieve Results This guide shares the tangible, practical steps companies can take to improve service through IoT condition based monitoring, how IoT platforms help deliver value, and how they can increase benefits with increased maturity. Then, the buyer’s guide focuses on the essential needs companies must consider to ensure a successful initiative. The requirements are intended to help companies frame their search process and efficiently find the right solution. The checklists go beyond software functionality to cover factors important to implementation, adoption, partner choice, and more. These are the factors that drive long-term business success from an IoT initiative.Begin the Condition Based Monitoring Journey
Start with the Basics Before looking at requirements, it’s critical to understand that improving service profitability is a journey. Condition based monitoring value starts with the basics of connecting equipment and collecting data. The first step in many companies’ journey is simply accessing equipment to understand its current location and status. Then, they can expand their benefits by gathering more complete machine data feeds to analyze performance metrics. “We learned you can’t just magically get to predictivity. You have to grow data maturity from descriptive to predictive to prescriptive. But you can get far more value from asset monitoring right away than you thought possible just based on alerts for above or below thresholds,” shares Todd Earls, VP IT for Digital Design and Manufacturing at Eaton. Grow Maturity over Time Expanding on the basics, companies can adopt advanced analytics to gain service intelligence to improve service operations by moving through increasing maturity levels. For example, one tangible objective is to recognize that there’s a problem before the customer or operator does. The key is to identify an issue, or a potential issue, in time to intervene to reduce the severity and impact of the problem. Grow Beyond Issue Identification to Remote Service It’s important to get started and then continuously improve over time. Then, as companies increase their service maturity, they can extend the value by remotely servicing equipment to further increase uptime and service margins.Next Steps
Recognize the Potential Leveraging the IoT can help companies improve service for themselves and their customers by reducing cost and transitioning to proactive and predictive service. Condition based monitoring allows companies to identify and resolve issues remotely, providing faster service and increased uptime for the customer while reducing the cost of truck rolls and putting service technicians on site. It can go beyond cost savings to improve sustainability or create new revenue from paid upgrades or remotely “unlocking” enhanced capabilities via a subscription. Get Started Now, more than ever, it’s critical to get started. Challenging financial markets make service profitability and increased asset lifecycles strategic. Service transformation has gone beyond the early adopters and is now becoming necessary to compete. Companies have to avoid “paralysis through analysis” and make tangible progress. As Danny Jackson of Autoliv advises, “Done is better than perfect, start doing some things. We lost some time trying to do it perfectly, then made more progress by doing things and learning from them.”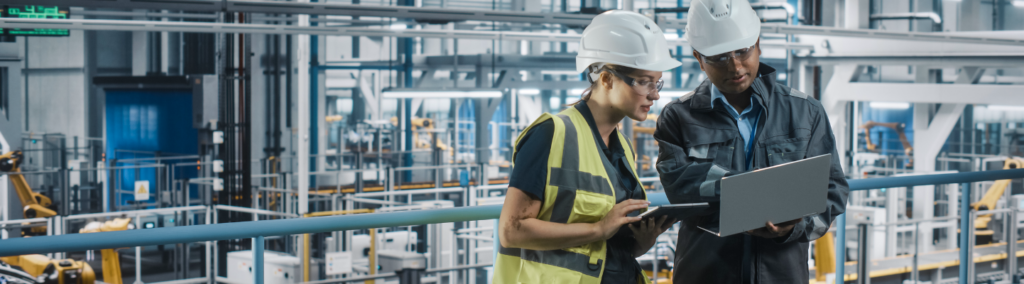
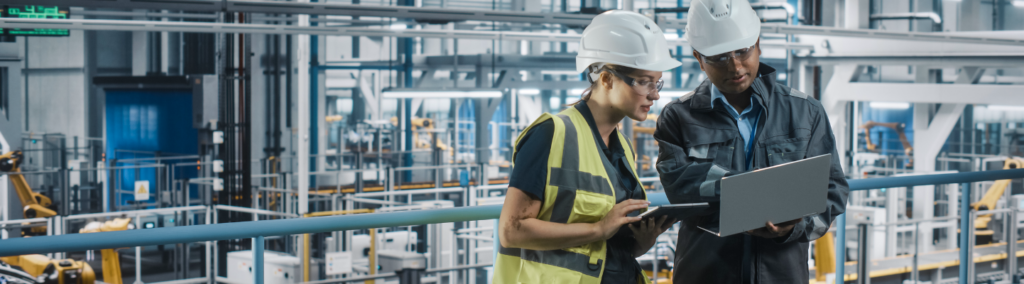
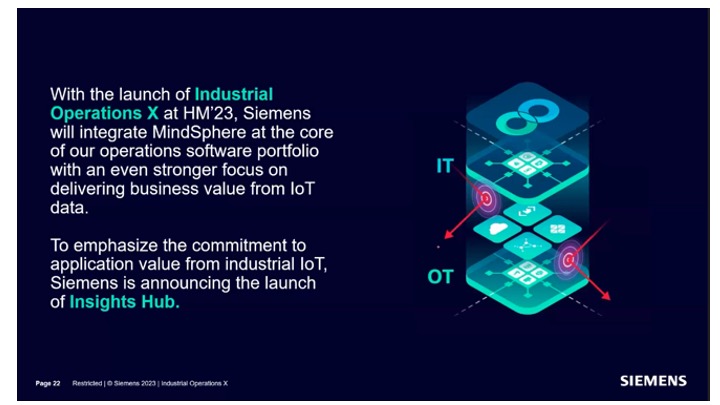
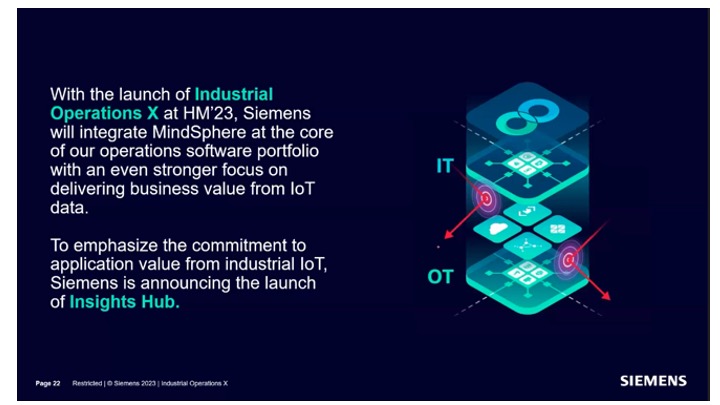
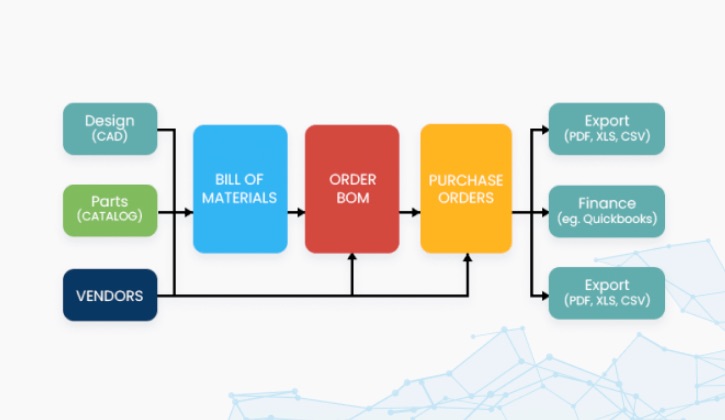
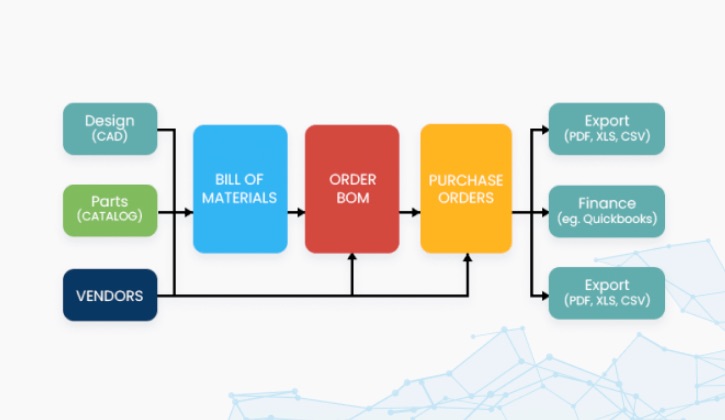
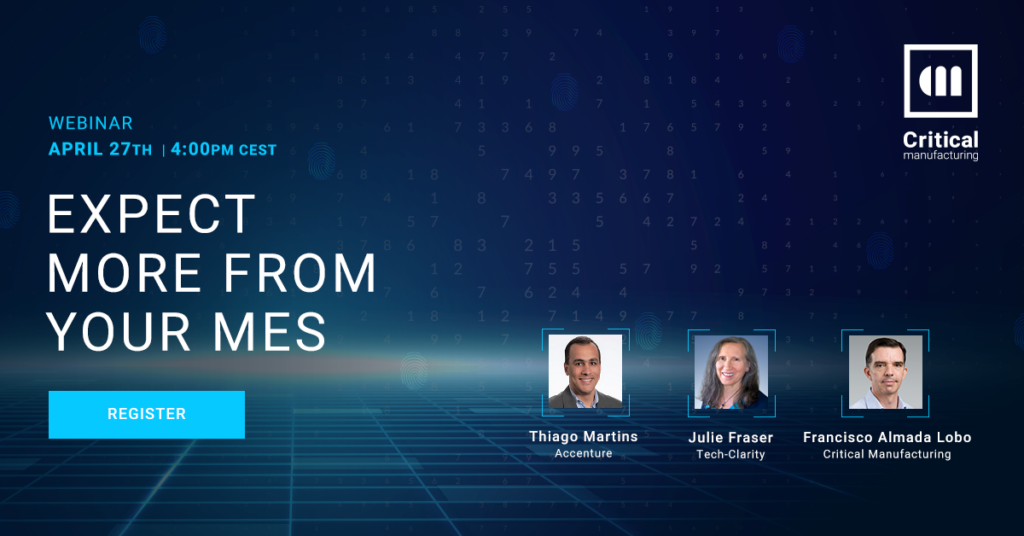
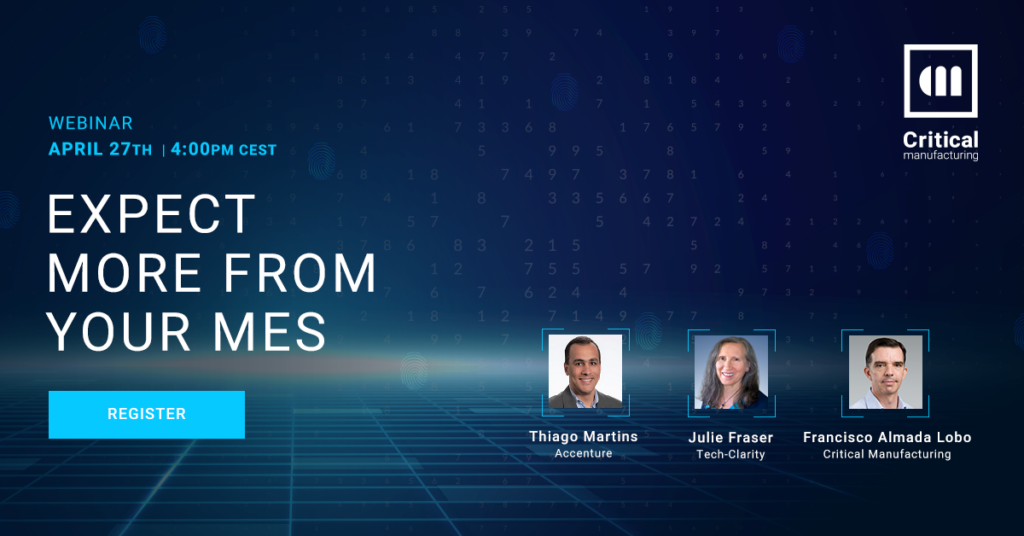
- Pre-publication highlights of a new survey on AI for Decision-Making in Manufacturing including the use and perception of MES.
- How MES can support a manufacturer in winning new customers, new contracts, and staying a preferred vendor.
- How technologies such as the industrial internet of things (IIoT), artificial intelligence (AI), and digital twins can enhance MES.
- What MES can offer to streamline frontline work for experienced and new employees.
- What is required for MES to keep up with ever-changing products and order mix.
- How integrated adaptive scheduling can improve OEE, on-time delivery, and cycle times to boost your standing as a supplier.
- The role of Low-Code and DevOps technologies in enterprise rollout and ongoing MES success.
- How much progress manufacturers are making on the many aspects of IT and OT data management required to use and analyze production data effectively.
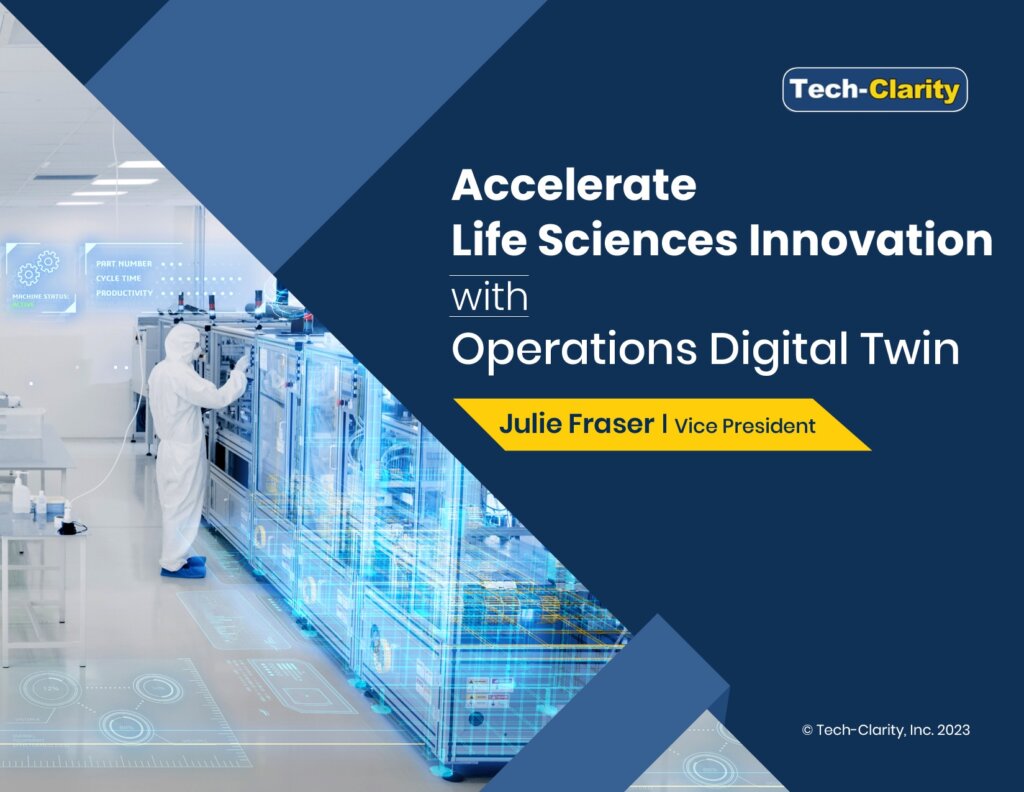
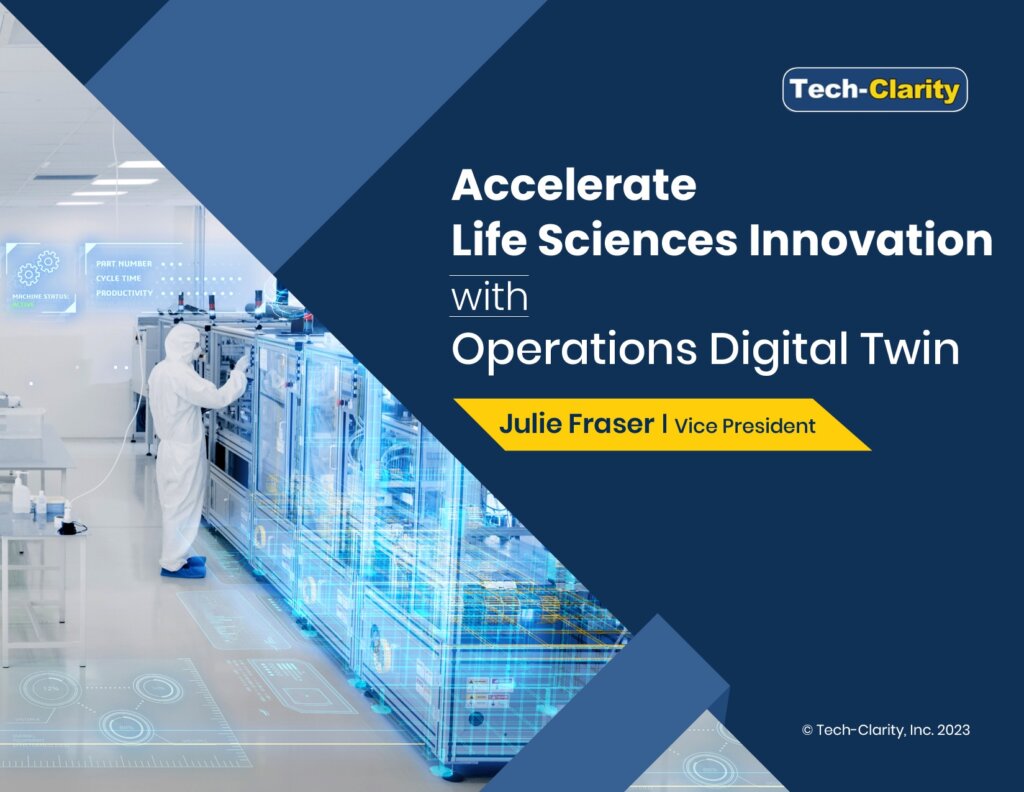
Table of Contents
- Rapid Life Sciences Innovation
- New Realities and Opportunities
- Manufacturing Must Keep Pace
- Digital Twins: Marrying Virtual and Real
- Operations Digital Twin Examples
- Digital Twin of Operations Accelerates Progress
- Twin Benefits in Operations
- Virtual Uses through Validation
- Virtual Uses Post-Approval
- Benefits of Virtual to and from Real
- Closing the Virtual-to-Real Loop
- Considerations for Useful Virtual
- Enterprise Transformation
- Clearing the Way for Acceleration
- Recommendations
- Acknowledgments
Rapid Life Sciences Innovation
Speed to Market Innovation has always been at the heart of life sciences companies’ success. Being quick to market helps both profits and patients. Of course, fast is relative, with most drugs and biologics taking 10-15 years from Phase I to approval, and medical devices taking three to seven years from concept to approval. The question is: Can life sciences companies accelerate this innovation process and make it more reliable? We have seen that they can by using current software and methods. It’s important to remember that innovation and supporting software serve not only R&D but also operations. Quality by Design Every aspect of innovation must increasingly aim for Quality by Design (QbD). For drugs, the EMA website defines it: “Quality by design is an approach that aims to ensure the quality of medicines by employing statistical, analytical and risk-management methodology in the design, development, and manufacturing of medicines.” Modeling and simulation allow a virtual test of a design against quality and regulatory requirements. This can result in improved product quality and patient safety before physical prototypes are built. In short, ensuring data-driven approaches early on can generate better outcomes at every stage of the product lifecycle. The chart below shows that concept. Figure 1. Accelerating Innovation Has Profits Benefits Throughout the Life Sciences Lifecycle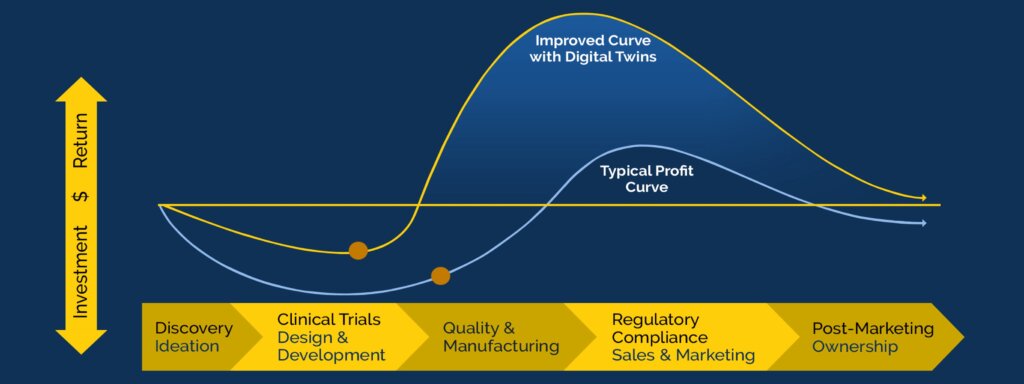
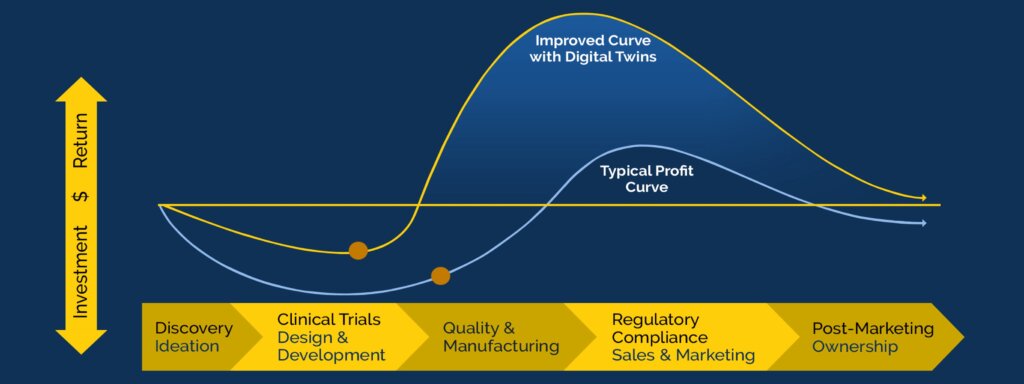
Recommendations
Recommendations and Next Steps Based on this research and our experience, we recommend that Life Sciences companies in biologics, pharmaceuticals, or medical devices:- Treat this as a transformational operations innovation acceleration initiative, not an IT project.
- Educate and create a vision everyone shares for a more agile manufacturing operation that accelerates innovation.
- Distinguish operations twinning from a Metaverse or gaming approach: it is for running the business, not training or purely visual representation.
- Carefully review your options to ensure the digital twin platform will support the organization now and in the future.
- Get started with twinning high-impact areas and build on the success to get maximum value and momentum.
- If you don’t have enterprise-capable manufacturing planning, scheduling, S&OP, and execution software, be sure those investments are in the plan.
- Be sure the top executive team sponsors and fully resources the program – including dedicating some of your best people and incenting everyone.
- Set an expectation that the twin will become a crucial aspect of daily operations: you will see what happens as things change and conduct what-ifs to gain speed and confidence in decisions.
- Keep the end in mind: virtual and real, constantly driving quality, innovation, improvement, and speed.
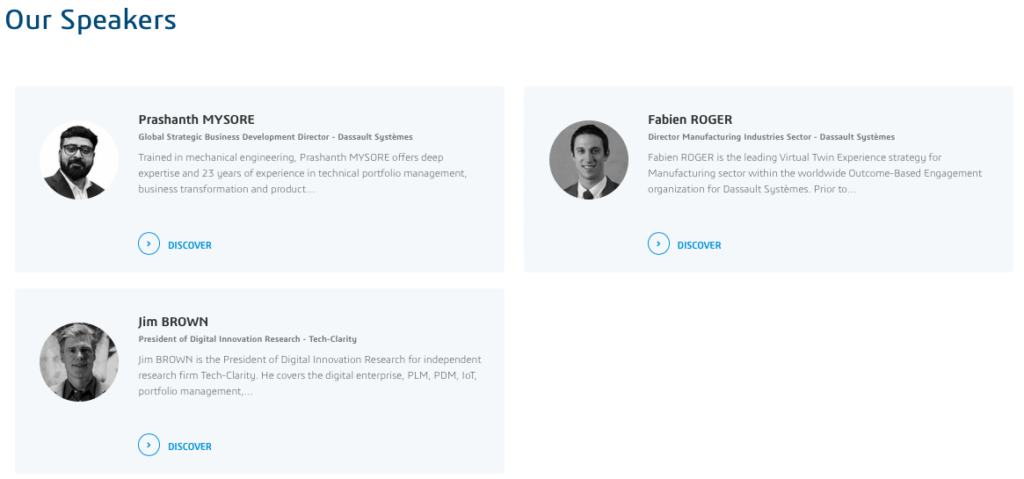
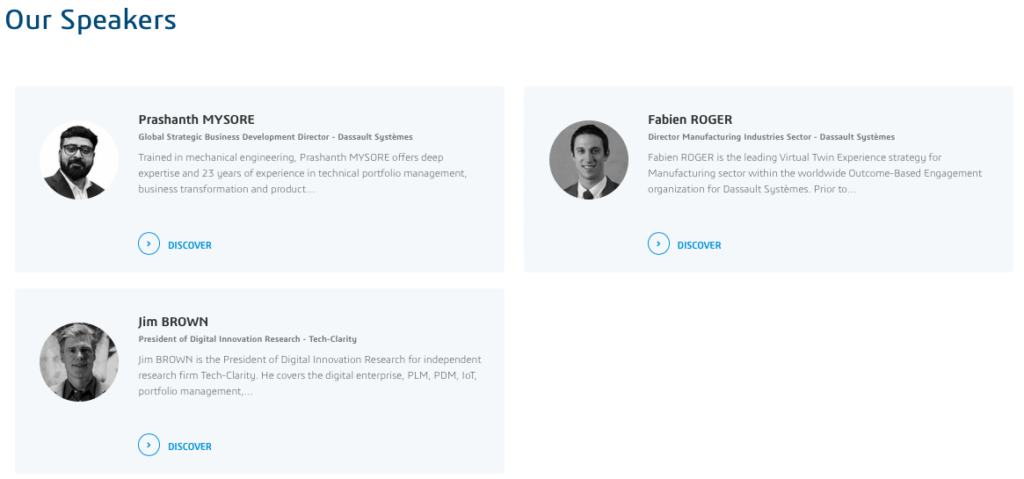
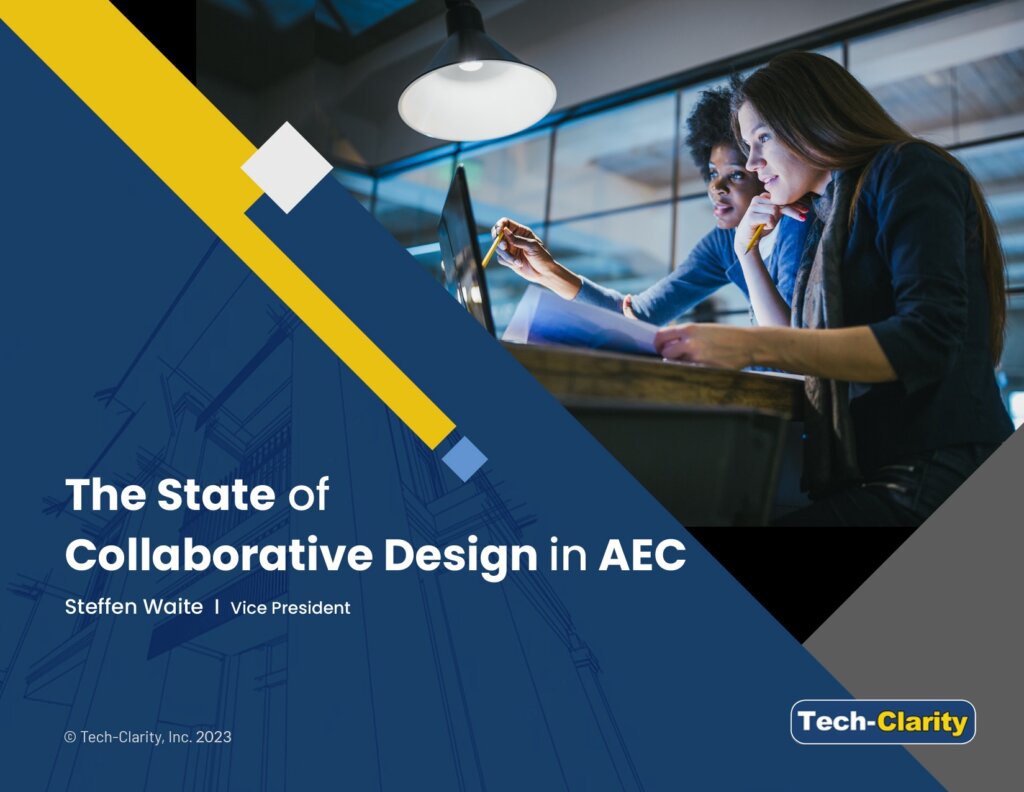
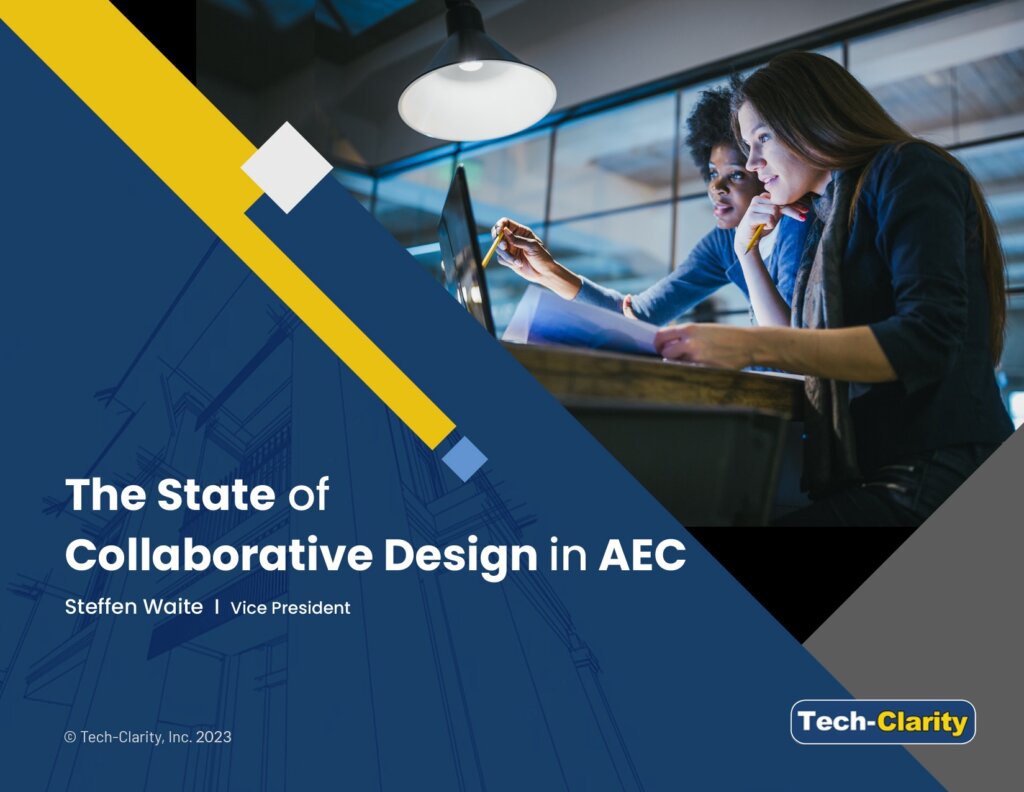
Table of Contents
- Profitability Demands Compelling Yet Efficient Design
- Communication and Complexity are Top Challenges
- Design Complexity is Growing
- Complexity Requires Multidisciplinary Collaboration
- Current Collaboration Has Room to Improve
- Importance of Design Integration
- Integration Approaches are Insufficient
- BIM as a Solution for Design Integration
- BIM is Maturing to Become the System of Record
- Importance of Design Integration Approaches
- Companies are Adopting Multidisciplinary Design
- Multidisciplinary Design Provides Valuable Benefits
- Perspectives on Multidisciplinary Design
- Multidisciplinary Design Faces Challenges
- Challenges Lead to Business Impacts
- Value of a Single BIM Authoring Environment
- Views on a Single BIM Authoring Environment
- IPD is Growing and Requires Multidisciplinary Design
- Fear of Trading off Capabilities
- Conclusions
- About the Research
- Acknowledgments
Executive Summary
Collaboration Design in AEC Our survey investigated the current state of collaboration and multidisciplinary design in the AEC community. The research focused on current approaches to collaboration, the readiness to adopt advanced design tools, and how these factors impact project success and profitability. The study focused primarily on the design and design coordination phase of the full built-project lifecycle and does not significantly include the experience of the construction community. About three-quarters (72%) of the research respondents are architects and the vast majority of companies offer architectural and/or engineering services.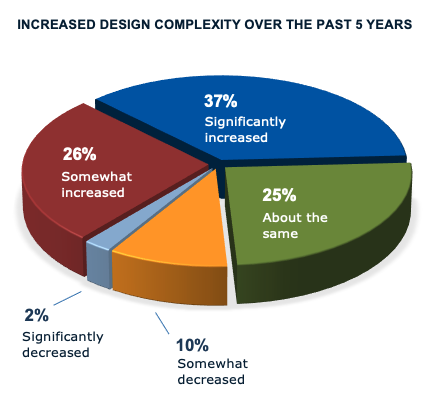
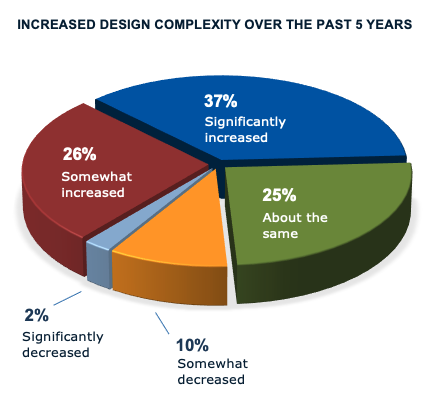
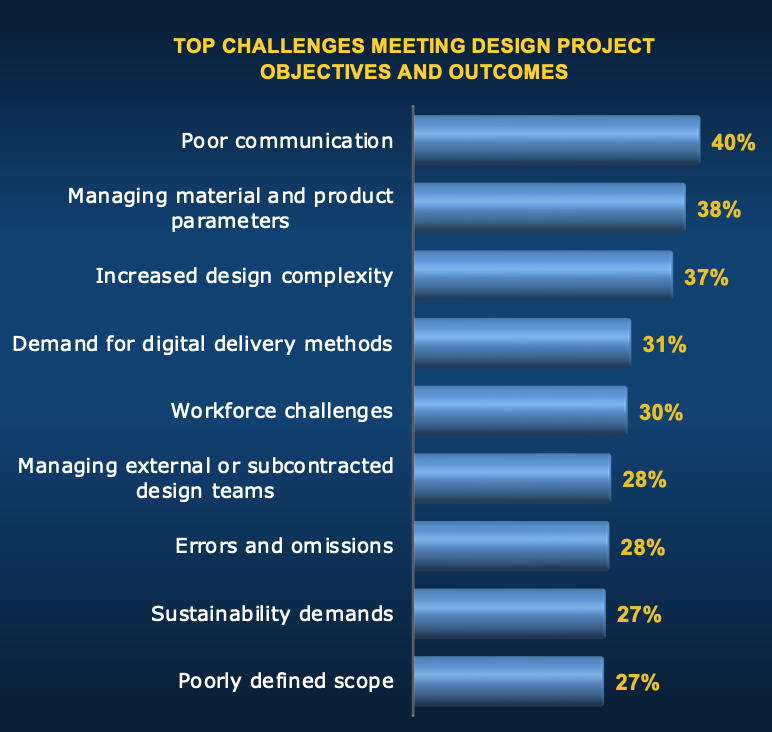
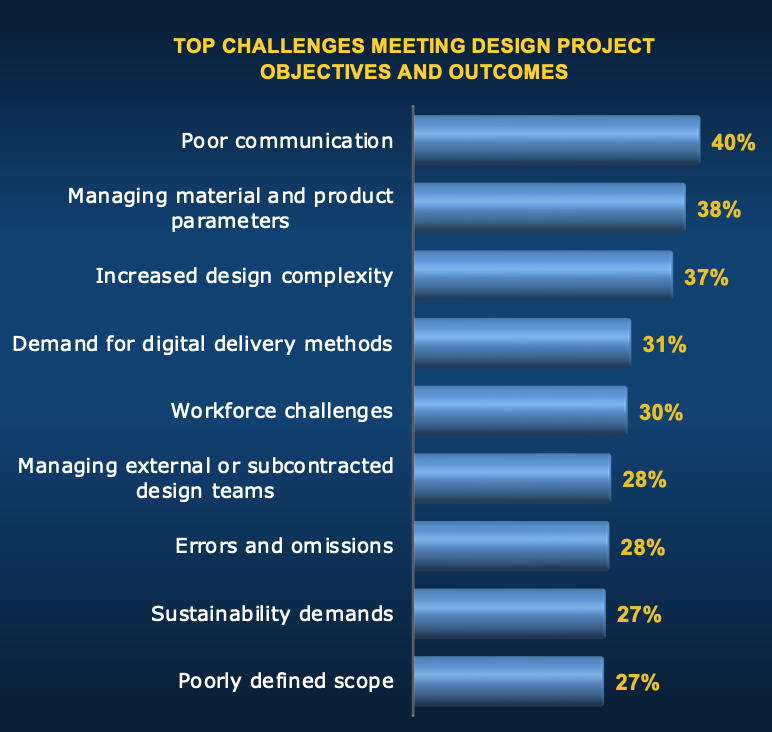
Conclusions
Communication is the Biggest Challenge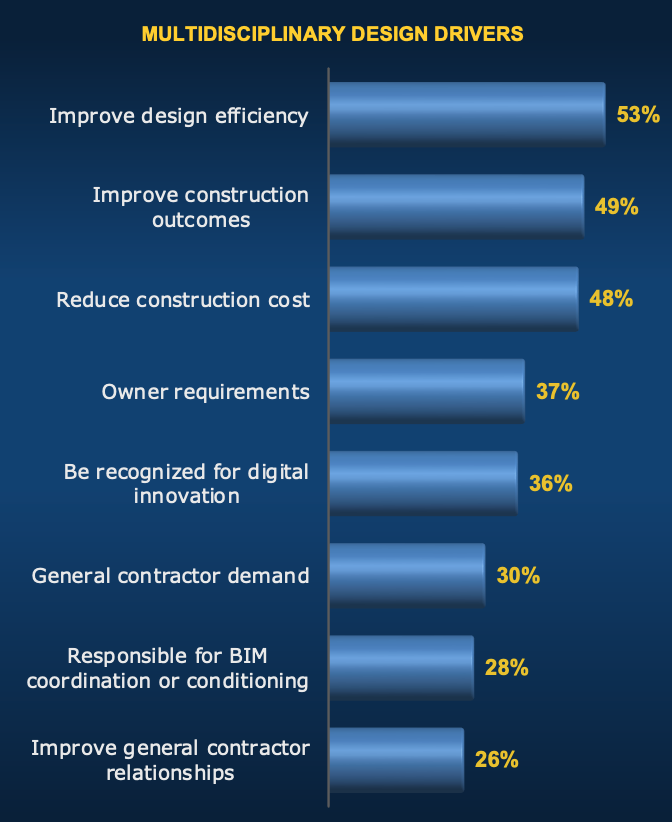
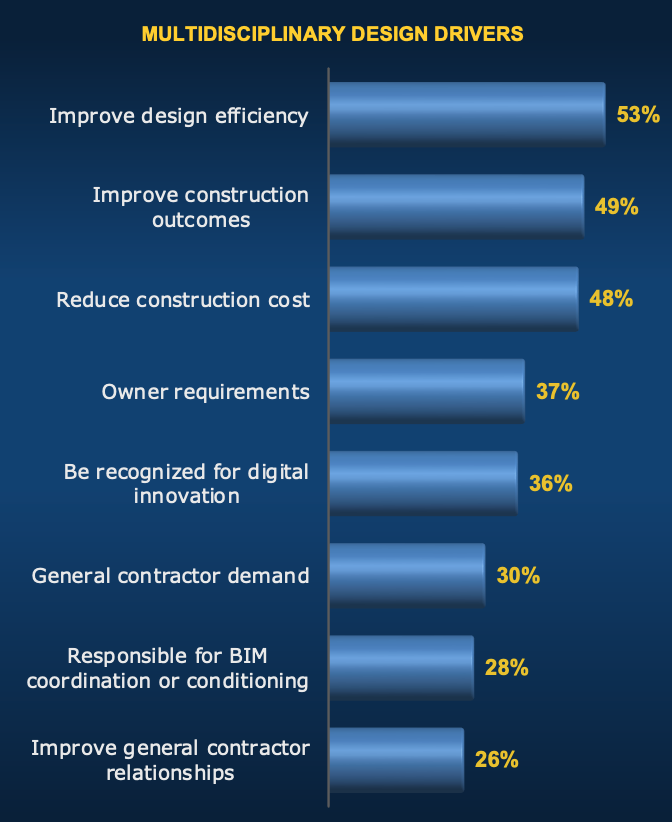
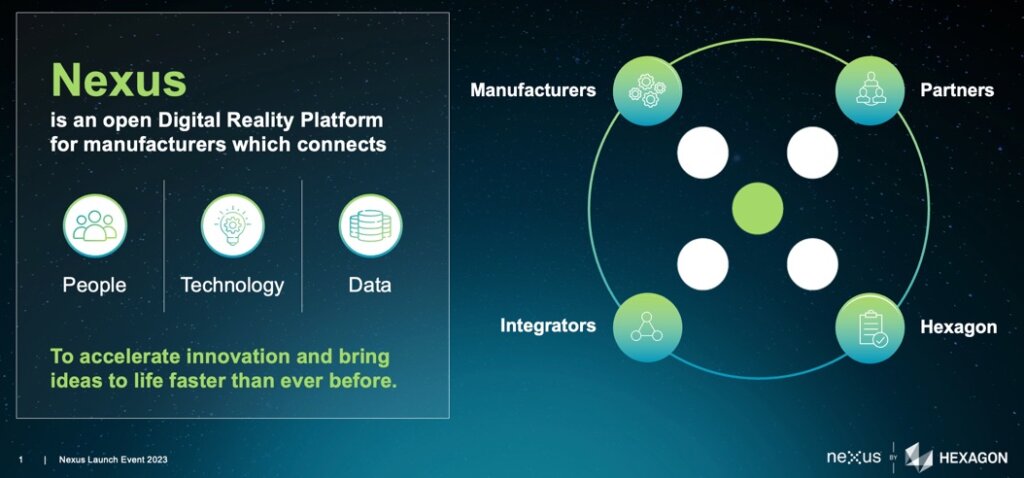
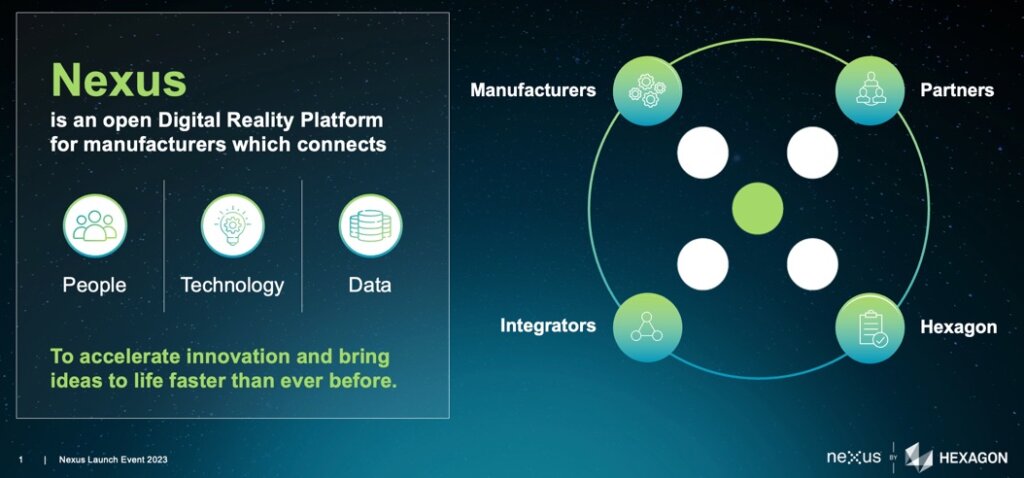
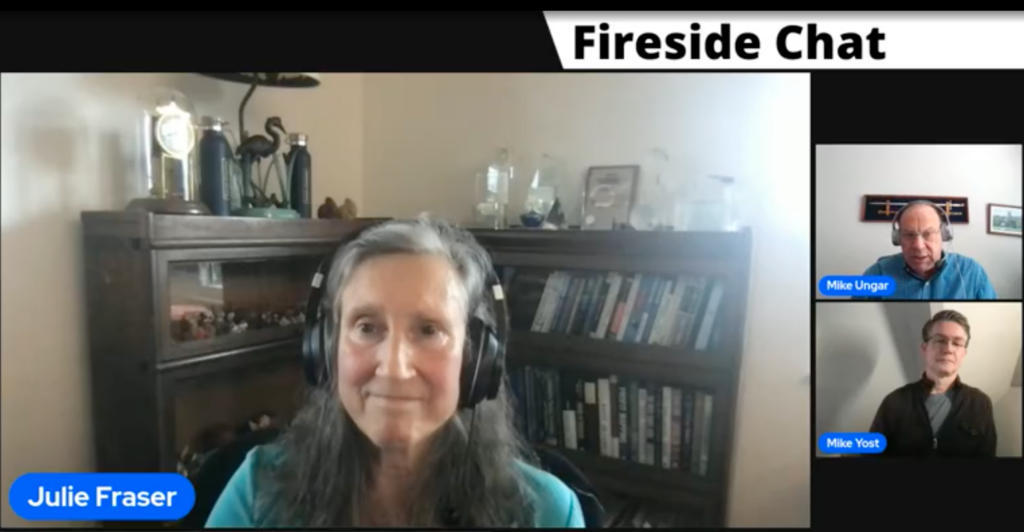
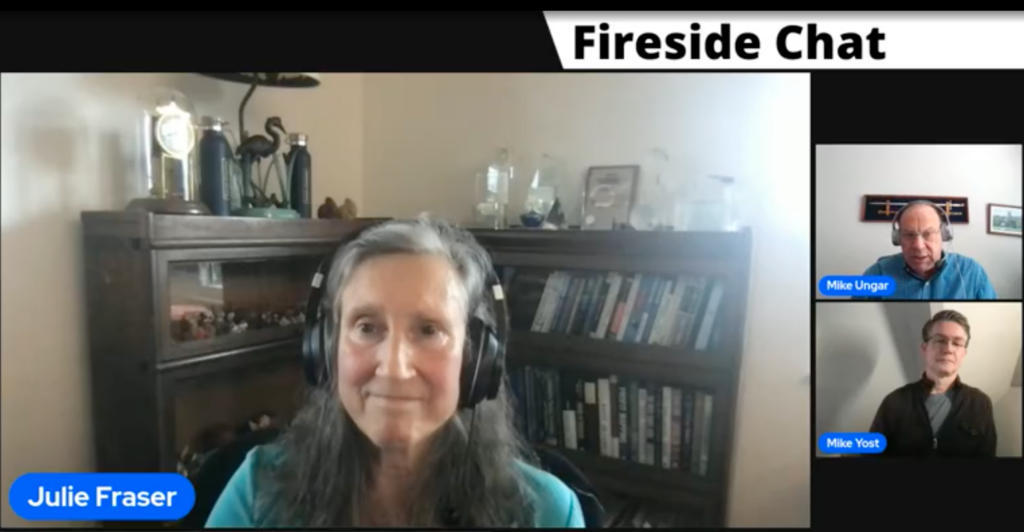
- Plant floor logistics with two-way communication to AGVs and AIVs is much-needed in the increasingly automated plant floors iTAC serves.
- Data analytics are designed to work with iTAC’s #IIoT or other IoT platforms. The IIoT.Edge and SMT. Edge products offer AI-based analytics at the edge using algorithms iTAC offers but are also open for customers to develop or use their own algorithms.
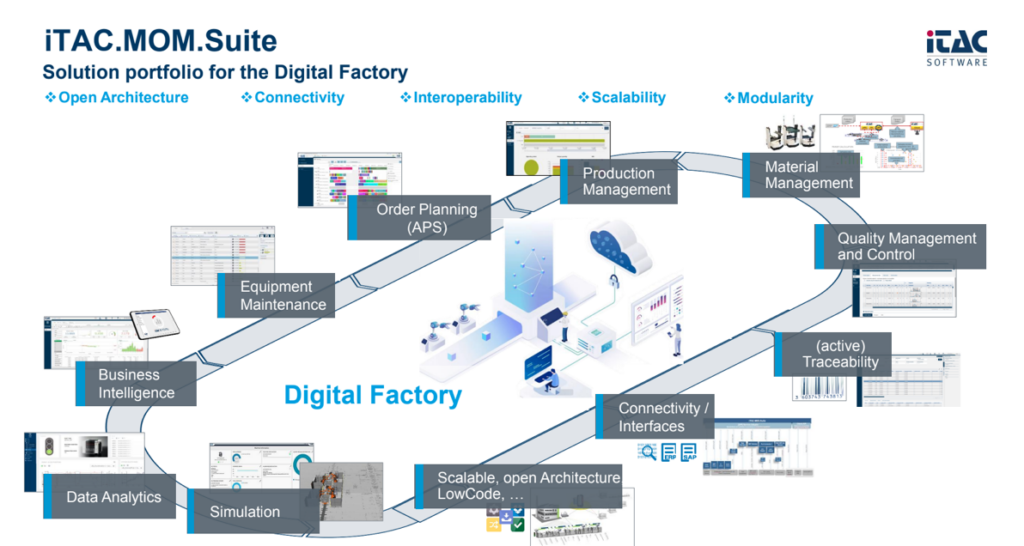
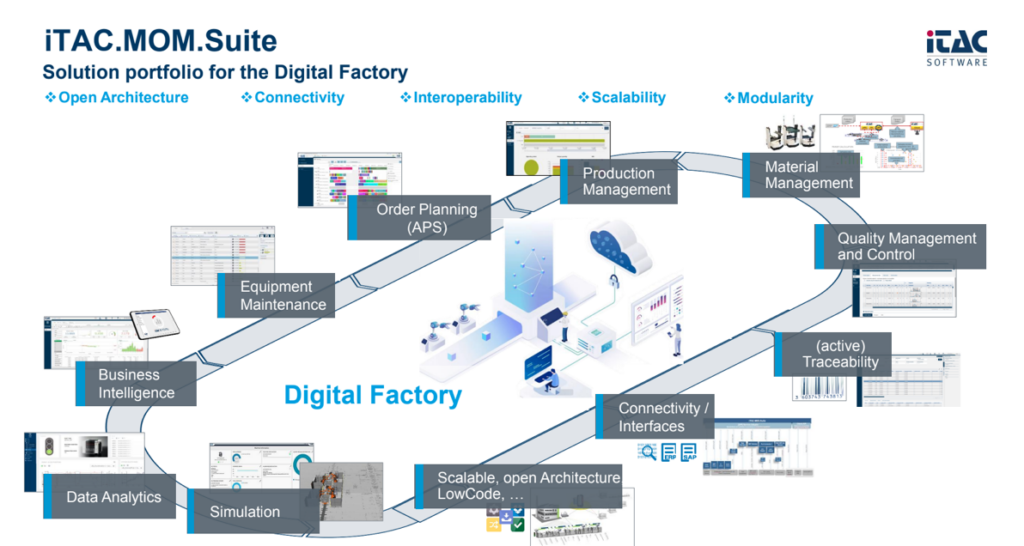
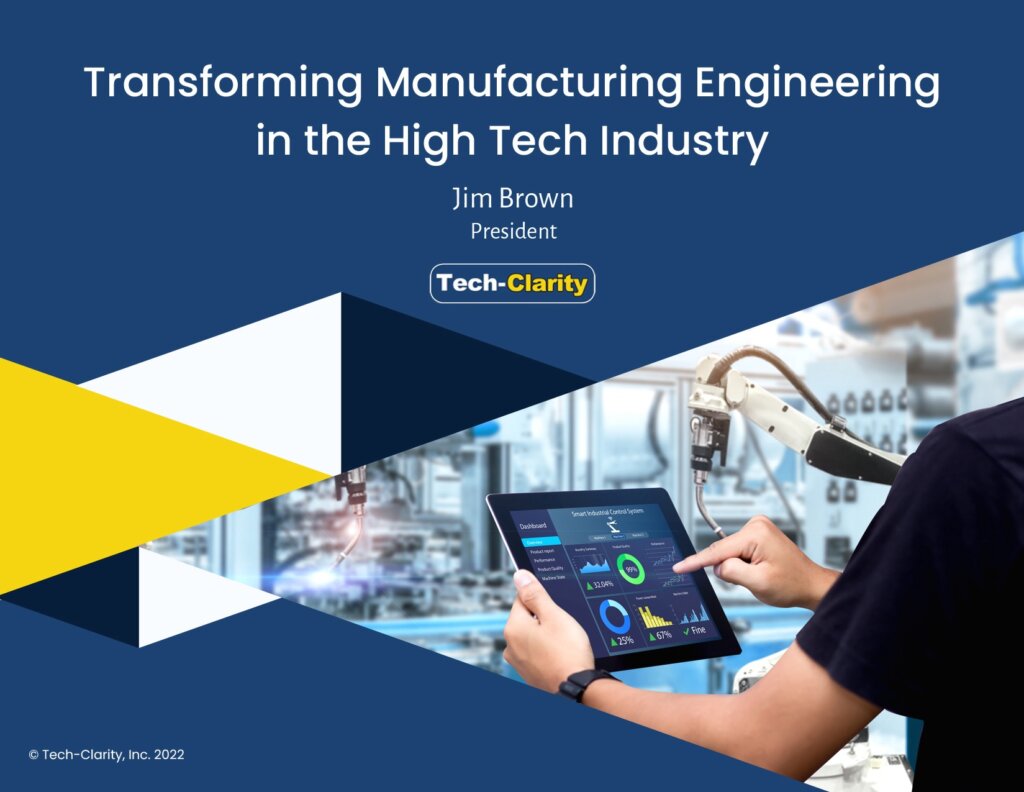
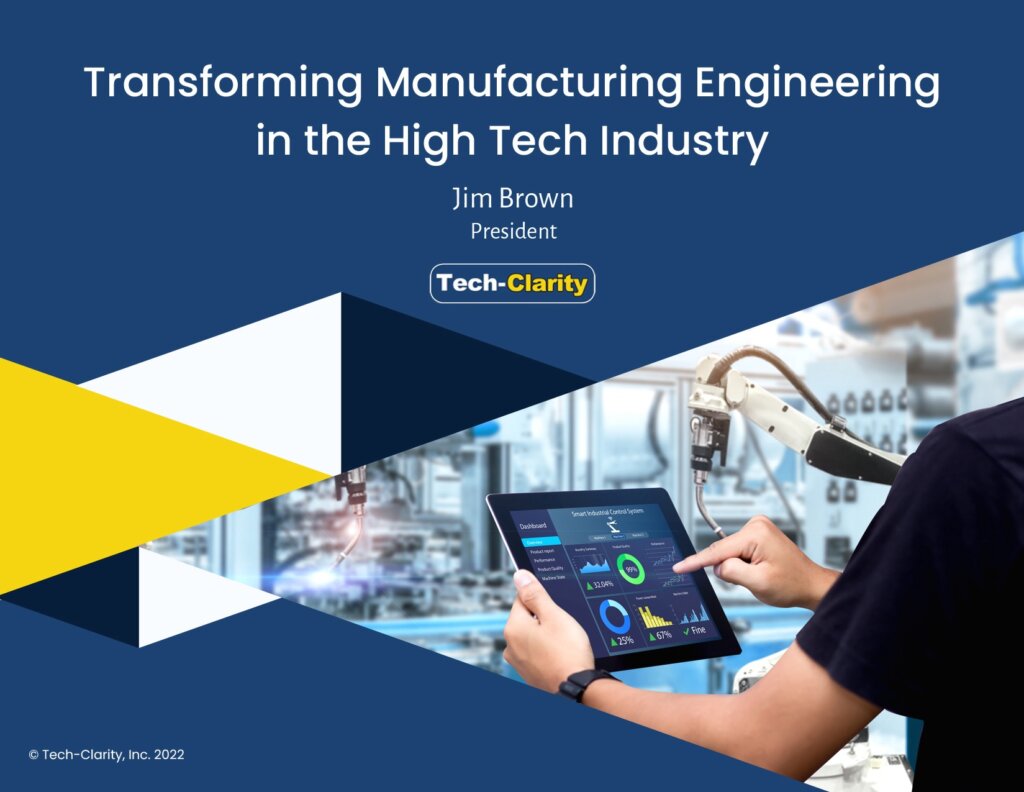
- Visibility to manufacturing capabilities
- Untimely design data
- Visualizing assembly processes
- Predicting impacts on sustainability
Table of Contents
- Improve Manufacturing Engineering to Increase Profitability
- Address Process Designer Challenges
- Recognize the Opportunity
- Quantify the Potential
- Identify Performance Drivers
- Find Issues Earlier in Design
- Use more 3D and Simulation
- Leverage More Integrated Solutions
- Use More Advanced Communication and Collaboration
- Top Performers Show the Way
- Recommendations and Next Steps
- About the Research
- Acknowledgments
Improve Manufacturing Engineering Performance
Improve Performance in the Face of Complexity How can high tech manufacturers improve manufacturing engineering? We surveyed 177 people directly involved with manufacturing engineering and found that modernizing processes and technology drives higher manufacturing engineering productivity and performance. These improvements are crucial to profitability as customers demand high quality, more personalized products at increasingly faster time to market; all despite rising product and manufacturing complexity. Modernize Manufacturing Engineering Survey results show that Top Performers (see definition in eBook) in manufacturing engineering have increased maturity in the way they plan, validate, and communicate manufacturing operations. These leading companies waste less time on non-value-added activities, find issues sooner, and spend less on physical prototypes. They accomplish this through best practices, including:- More advanced collaboration and communication methods
- Increased use of 3D and simulation to plan and validate manufacturing operations with virtual, digital twins
Recognize the Opportunity
Manufacturing Engineering is Ready for an Upgrade It’s time for change. Manufacturers must digitalize production planning to reduce cycle times, increase efficiently, and deliver quality. High tech companies need to adopt new techniques to validate manufacturing earlier in the process, in parallel with product design.

Recommendations and Next Steps
Make a Strategic Improvement Today’s product, manufacturing process, and market complexity demand new ways of working. The Top Performers are transforming manufacturing engineering through digitalization, better collaboration, 3D, and simulation allowing them to overcome efficiency, quality, and cost challenges. Using virtual, digital twins offers manufacturing engineers both the ability to improve their own performance and a strategic opportunity to increase overall product development profitability. These leaders spend 17% less time on non-value-added activities in manufacturing engineering, directly reducing development cycle times. Improve Time to Market Survey respondents report that they can reduce time to market by 37% by using 3D and simulation to plan and validate manufacturing operations. This is done, in part, by increasing efficiency, reducing time-consuming physical prototyping, and lowering rework by finding issues sooner in product development. This is critical in the high tech industry where time to market drives market share and products have such short lifecycles. Reduce Cost Survey respondents share that they can eliminate 36% of their prototypes by increasing manufacturing engineering maturity, leading to significant cost savings per product. They do this by shifting validation and issue identification sooner in the product development process so they need fewer physical prototypes.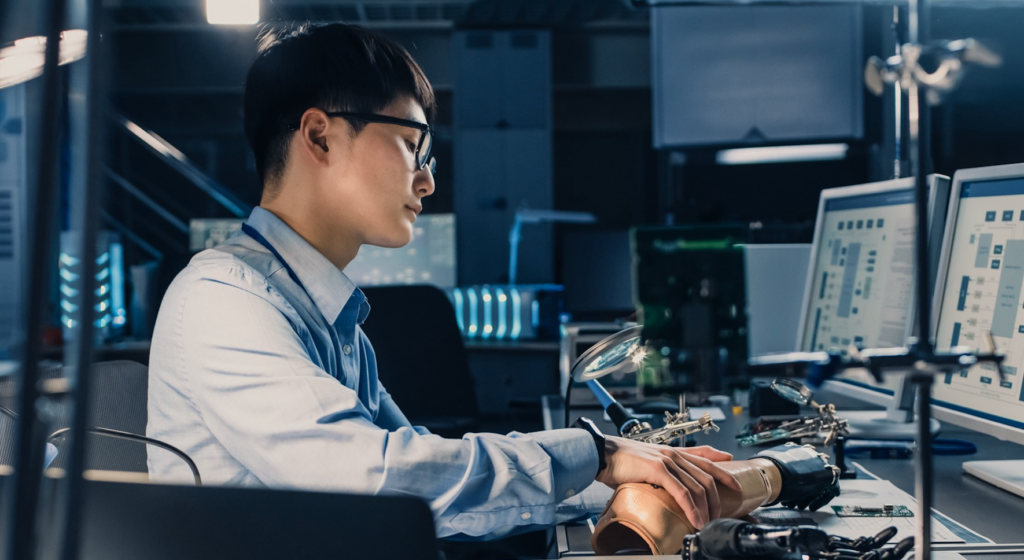
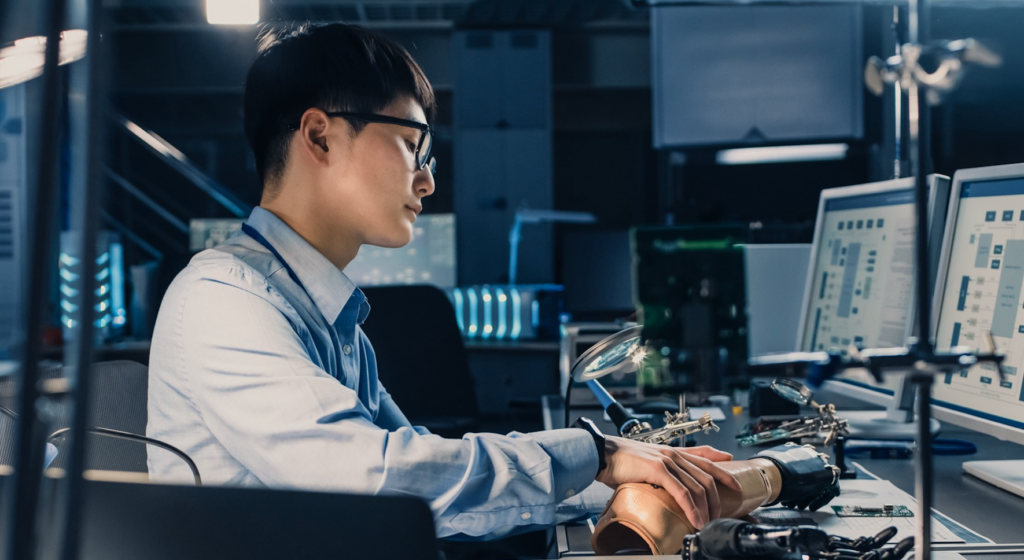
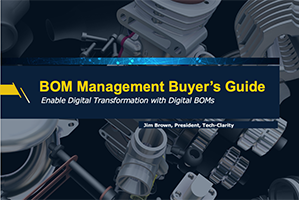
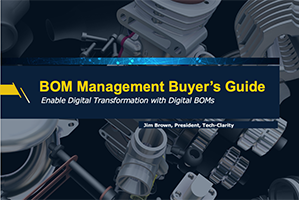
Table of Contents
- Introducing the Buyer's Guide
- Diagnosing BOM Management Issues
- The BOM Management Status Quo
- The BOM Management Business Case
- Analyze BOM Management Solution Capabilities
- Assess Service Requirements
- Consider Vendor Requirements
- Special Considerations
- Conclusions
- Recommendations
- Acknowledgments
- About the Author
Introducing the Buyer's Guide
Managing Bills of Material (BOMs) is a fundamental need for any manufacturer. Without effective control of product structures, companies struggle with inefficiency and errors. On the other hand, improving the maturity of BOM-related processes helps manage complexity, increase product personalization, improve efficiency, prevent mistakes, and enhance collaboration across departments and the supply chain. The resulting benefits can be strategic, leading to increased innovation, agility, and faster time to market that impact top-line financial performance. BOM management is now essential as the foundation for the digital enterprise and serves as the backbone of the digital twin. Effective BOM management is also critical for manufacturers to confidently change products to adapt to market challenges like chip shortages and supply chain disruption.

Analyzing BOM Management Solution Capabilities
Perhaps the most obvious place to start when evaluating new software solutions is functionality. This section covers multiple types and uses of product structures, including Engineering BOMs (EBOM), Manufacturing BOMs (MBOM), Service BOMs (SBOM), and others such as those used for simulation or compliance analysis. For the purposes of this analysis, we’ve broken BOM management into seven main focus areas:- Developing product structures
- Managing revisions and change
- Supporting product variability
- Associating information
- Transforming BOMs
- Visualizing products
- Reporting, analyzing, documenting
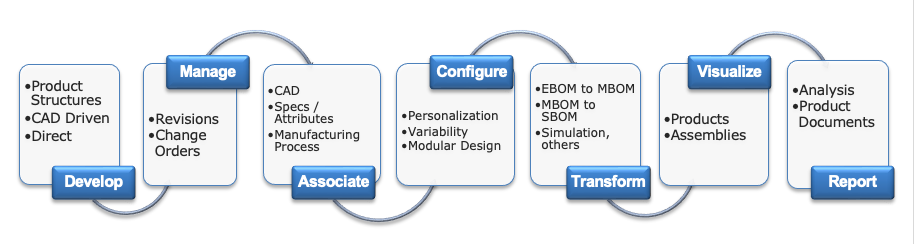
- Controlling and securing product-related data
- Quickly finding and reusing information
- Sharing product knowledge with other departments (and beyond enterprise boundaries)
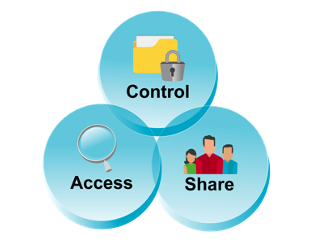
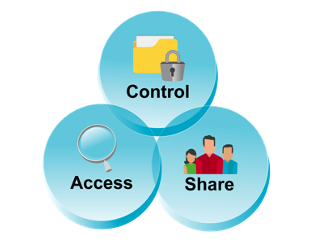
Conclusion
BOM management helps manage complexity and streamline operations. It provides an important, foundational element that serves as the backbone for all engineering, manufacturing, and service activity. An accessible, trusted source of product structure information is valuable and improves traceability and control. Effective BOM management provides enterprise-level benefits, improving business performance and alleviating disconnects across the business. The net result is efficiency and cost gains combined with revenue improvement from better collaboration and faster time to market, making BOM management an essential operational tool and a key driver of improved profitability. Supporting BOM management at the enterprise level requires the right solution. Companies should develop a requirements list that helps encourage a holistic decision encompassing software functionality, service-related needs, vendor requirements, and any special considerations based on their industry, size, and product strategy. Finally, the plan should look beyond current needs to support the digital future where the Digital Twin, Digital Thread, AR, VR, and IoT rely on sound BOM information.Recommendations
Based on industry experience and research for this report, Tech-Clarity offers the following recommendations:- Think big, but remain agile and take BOM management improvement in steps
- Recognize the importance of accurate, complete, timely, and accessible product structures
- Develop a comprehensive, multidiscipline, and multi-CAD BOM management capability
- Look for functionality, but extend requirements to vendor and service considerations
- Look for a Cloud / SaaS solution to reduce risk, ease adoption, and ensure vendor market competitiveness
- Consider any special needs for your business, industry, or geography
- Provide the foundation for the digital enterprise to compete today and into the future
- Get started
Product Updates in Onshape
David also shared an overview of some of their key product releases over the last year, including: PCB Studio: Supports concurrent ECAD and MCAD design.- Render Studio: Offers photorealistic imagery
- Onshape Simulation: Gives design engineers easy access to structural analysis during design
- Frames: Enables quick design of structural frames
- Variables Studios: Provides a way to define and modify common variables across parts and assemblies
Agile Product Development
Jon Hirschtick shared his perspective as well. He stressed that they see much interest from companies looking to apply the Agile Methodology they use for software development to hardware (see graphic below). He cited trends driving this interest include:- Product development tools have evolved
- The new generation workforce wants to work in a more agile way
- The pace of change is so significant, companies need new methodologies to allow them to quickly adapt and pivot
Simulation in Onshape
I believe their approach to simulation could also be a key enabler for Agile. With it, design engineers do not have to worry about translating or meshing their model, and the software already understands assembly constraints. Consequently, design engineers, including those unfamiliar with simulation, can apply loads and view the results. Our research consistently shows that the activities involved with preprocessing, particularly defining the mesh, are one of the biggest bottlenecks for design engineers’ use of simulation. Onshape’s approach automates much of this, making it easier to adopt. Since Onshape Simulation is cloud-based, the processing is done on the cloud, without slowing down the engineer’s workstation. Another engineer can pull up the model and make changes, and the engineers can work together to evaluate the results. With this approach, the potential for supporting the Agile Methodology during short sprints of design, prototype, and test looks very powerful. I look forward to seeing the new developments in 2023. Thanks to Coray Thibaut de Maisieres and the Onshape team for putting on a great event.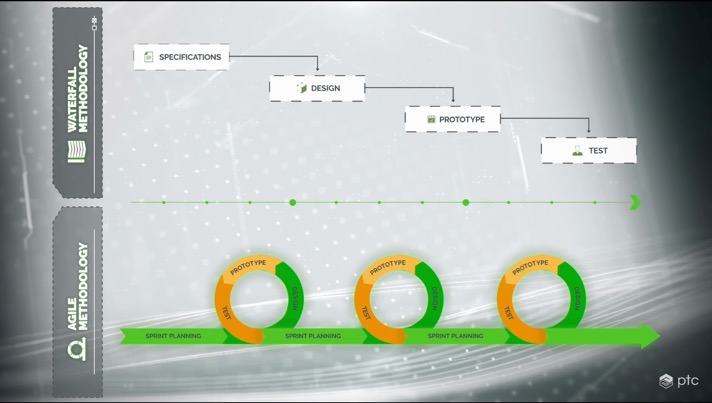
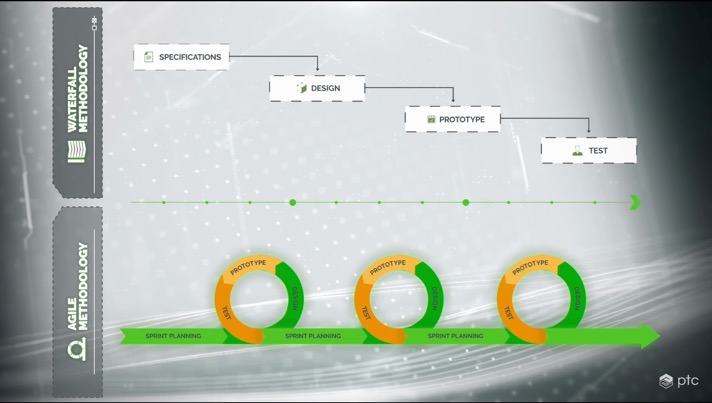
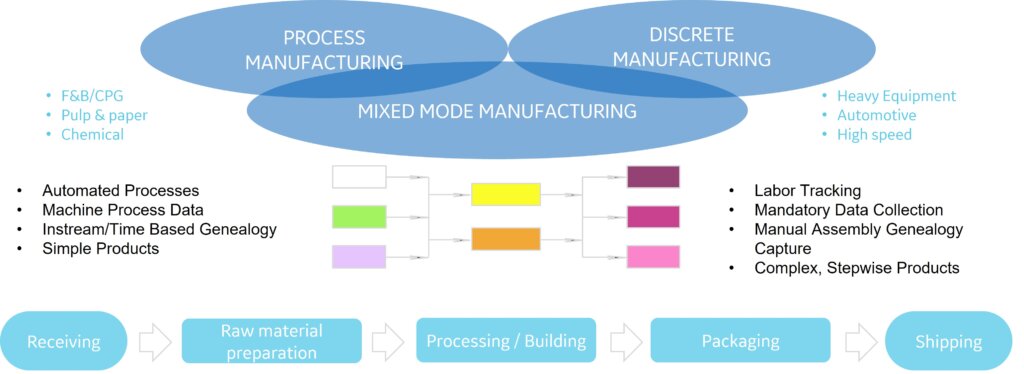
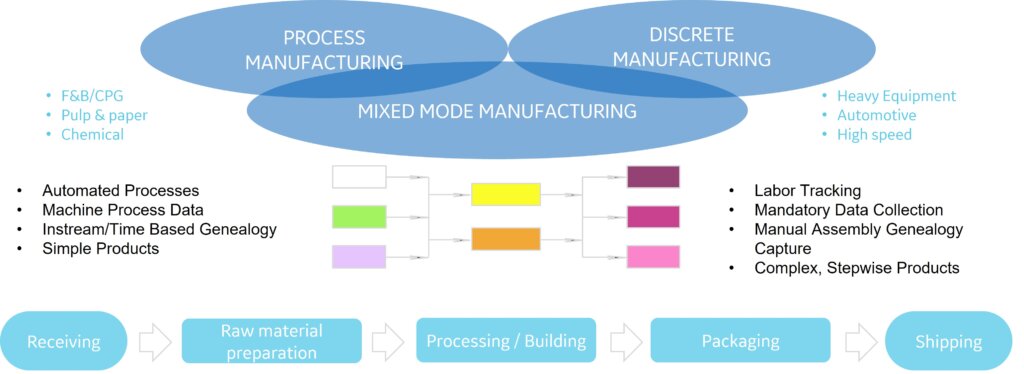
[post_title] => GE Enhances Cloud MES for TCO, Flexibility (Insight) [post_excerpt] => [post_status] => publish [comment_status] => open [ping_status] => open [post_password] => [post_name] => cloud-mes-insight [to_ping] => [pinged] => [post_modified] => 2023-03-13 15:54:34 [post_modified_gmt] => 2023-03-13 19:54:34 [post_content_filtered] => [post_parent] => 0 [guid] => https://tech-clarity.com/?p=17938 [menu_order] => 0 [post_type] => post [post_mime_type] => [comment_count] => 0 [filter] => raw ) [19] => WP_Post Object ( [ID] => 17895 [post_author] => 2 [post_date] => 2023-02-23 09:00:57 [post_date_gmt] => 2023-02-23 14:00:57 [post_content] =>
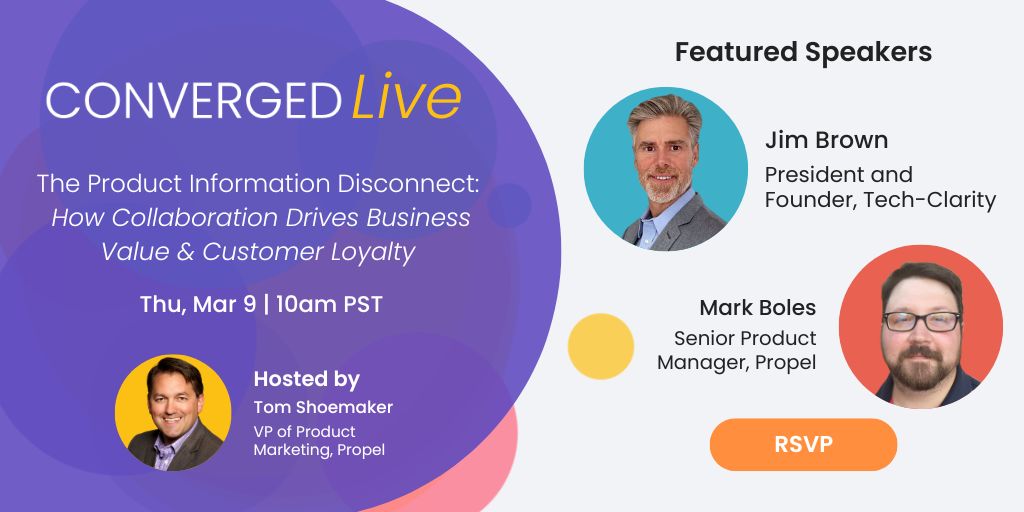
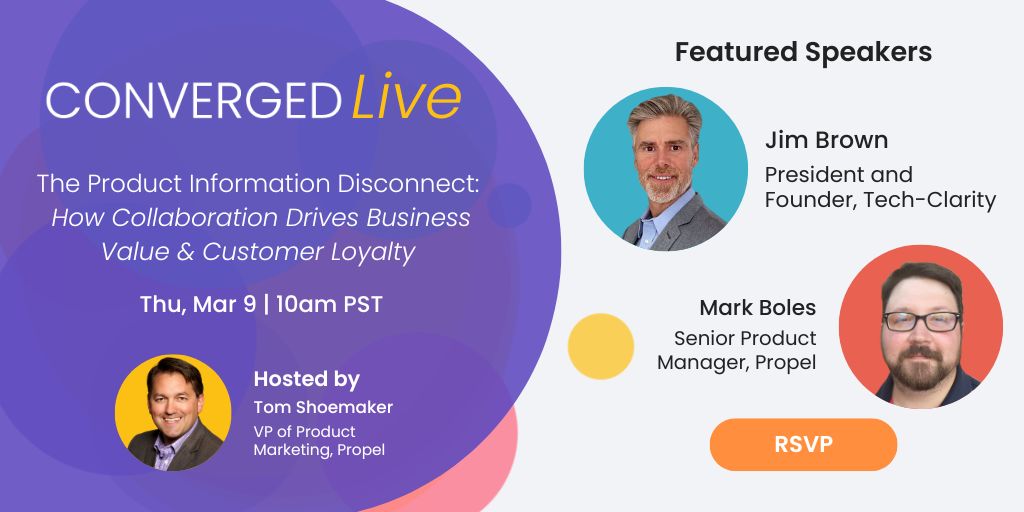
- Learn how disconnected data and processes derail product introduction, leaving time and money on the table
- Find out how using a single digital thread delivers accurate information every time, from design to commercialization
- Discover the fastest, most accurate way to launch quality products across every channel
- Manufacturing process instructions
- SOPs
- Technical documentation or manuals
- employee training
- MRO or field service repair guides
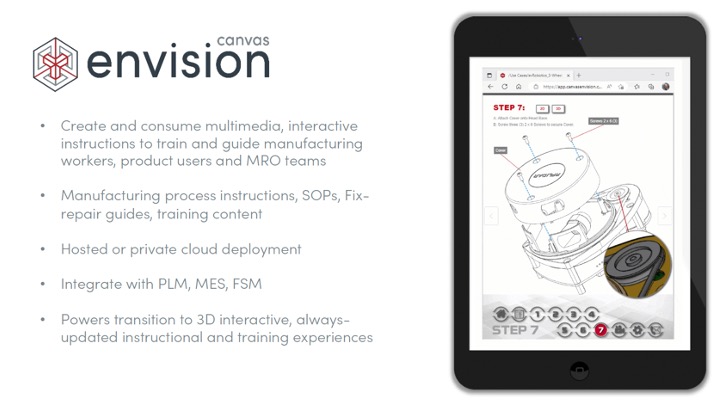
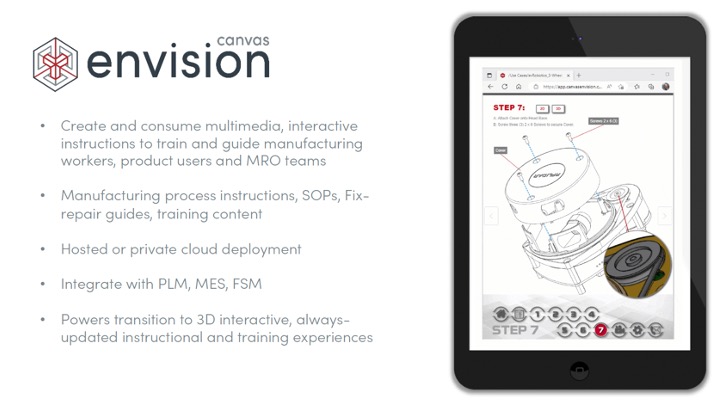
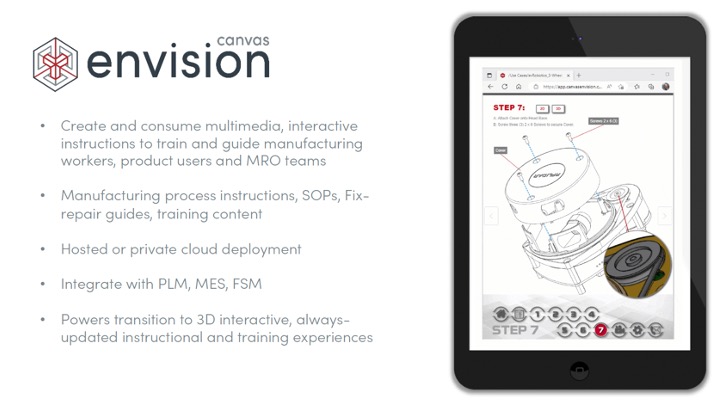
All Results for "All"
Sopheon Champions new InnovationOps Movement
We’ve been talking about operationalizing innovation for some time. It’s a crucial need because, as our research shows, innovation for products and services is among the top factors driving long-term business success. It can’t be left to organic inspiration or luck. It must be targeted and driven to provide a repeatable, scalable market advantage that…
Elisa IndustrIQ Combines Advanced Analytics into Established Applications (Insight)
Jim Brown and I are jazzed up after learning about how Elisa IndustrIQ is combining the data management and analytics of the parent telco to strengthen already successful manufacturing applications. This combination of data structures, analytics algorithms for AI and ML, and applications that serve specific industries’ needs can deliver very high value. Elisa IndustrIQ…
Actify Offers Program Management Solution for Automotive Suppliers (insight)
It’s exciting when you see a company reinvent themselves to take on an important, unsolved problem in the industry. That’s exactly what Actify has done. We’ve been following them from the time of their early, very successful CAD viewer product line SpinFire through their new evolution to create a holistic solution for automotive project management….
Accelerate Manufacturing and Time to Market in Life Sciences
How can life sciences manufacturers accelerate their innovation? One way is by recognizing and creating an operational digital twin that’s connected to MES. We will discuss: How digital twin of operations and MES support rapid innovation while ensuring high-quality, compliant, and cost-effective operations Why manufacturing matters through the lifecycle of life sciences products starting in…
Seven Keys to Improving Service with the IoT
Current economic conditions make service profitability and asset longevity more important than ever. How can service organizations leverage the IoT to transform service and improve service performance and profitability? This Buyer’s Guide offers seven ways that can help companies get started or expand on early efforts, apply lessons learned from initial projects, and drive repeatable…
Siemens Advances IT/OT Convergence with Industrial Operations X (Insight)
Are the next steps of IT/OT convergence at hand? Siemens would say yes. IT and OT are blending more than ever in some new offerings under an umbrella of data-driven manufacturing. Siemens just announced the expansion of their Totally Integrated Automation (TIA) framework into Industrial Operations X. Industrial Operations X includes Industrial IoT, Industrial Edge,…
OpenBOM becomes a Digital Thread Platform (Insight)
I was recently able to catch up with Oleg Shilovitsky for an update on OpenBOM. In addition to his high blogging productivity, he and the OpenBOM team have been even harder at work developing new capabilities and expanding their reach. I’ve enjoyed following OpenBOM’s progress because they take a practical approach to solving manufacturer’s problems,…
Expect More from Your MES
What are realistic expectations for a manufacturing execution system (MES)? Should you expect more from MES? MES has been available for decades. That is good news and bad news. Those with experience of older systems – and even many MES offered today – may have a limited view of what such a system can do….
Accelerate Life Sciences Innovation with Operations Digital Twin
How can manufacturing software accelerate life sciences innovation? By combining MES with an operations digital twin. Please enjoy the summary* below. For the full research, please visit our sponsor Dassault Systemes(registration required). Table of Contents Rapid Life Sciences Innovation New Realities and Opportunities Manufacturing Must Keep Pace Digital Twins: Marrying Virtual and Real Operations Digital Twin…
Is the Digital Twin Attainable?
How can industrial companies achieve value from their digital twin initiatives? Are their goals achievable? We’ve all heard the promises of significant value from digital twins, let’s discuss how to reach that value. Jim Brown will host a webinar with Prashanth Mysore and Fabien Roger of Dassault Systemes to share examples of how companies use…
The State of Collaborative Design in AEC
How well is collaboration working in the AEC industry? We surveyed 393 people whose companies design, engineer, or construct the built environment to find out about collaborative design in AEC, including multidisciplinary design and BIM. Please enjoy the summary* below. For the full research, please visit our sponsor Graphisoft (registration required). Table of Contents Profitability…
Hexagon Launches Digital Reality Platform, Nexus (Insight)
We spoke with Hexagon following a recent event launching their Nexus platform. Hexagon already offers a wide range of solutions supporting the product lifecycle, including design and engineering; production; and metrology and inspection portfolios from its Manufacturing Intelligence division and others including the newly acquired Enterprise Asset Management (EAM) and quality management (QMS, ETQ) solutions….
An Ecosystem Enabling Manufacturers and Industry 4.0 Providers to Flourish with Julie Fraser
What are some keys to success with Industry 4.0? And what does mindfulness have to do with it? Listen to this fireside chat with Julie Fraser, hosted by the Industry 4.0 Club’s Mike Ungar and Mike Yost to start thinking about your ecosystem for success. An ecosystem is the environment in which a variety of…
iTAC MES/MOM Adds Low-Code, Logistics, and Edge Analytics (Insight)
I recently got an update briefing from iTAC Software AG, which was eye-opening. It appears you can now get deep out-of-the-box MES/MOM functionality plus low-code ways to extend the software. This company has offered #MES for many years but has recently expanded on many fronts. The original company philosophy of bidirectional integration with equipment has…
Transforming High Tech Manufacturing Engineering
How can high tech manufacturers improve manufacturing engineering? We surveyed 177 people directly involved with manufacturing engineering and found that modernizing processes and technology drives higher manufacturing engineering productivity and performance. These improvements are crucial to profitability as customers demand high quality, personalized products at increasingly faster time to market; all despite rising product and…
Enable Digital Transformation with Digital BOMs
Why is effective bill of material management critical to digital transformation? What should you look for in a BOM management solution? Our white paper serves as a reference tool for manufacturers selecting a system to improve the maturity of their BOM management practices. Please enjoy the summary* below. For the full buyer’s guide please visit…
Onshape Live 23 Reveals Significant Progress
Onshape, a PTC Technology recently held their Onshape Live 23 virtual event. It was a nice overview of progress over the last year, customer success stories, and previews of what’s coming. Loretta Faluade kicked things off and then introduced David Katzman as the new General Manager of the Onshape business at PTC. David provided an update highlighting their 3 million users, 99.9%…
GE Enhances Cloud MES for TCO, Flexibility (Insight)
There is more exciting news from GE Digital on its newest Proficy MES version. In a previous discussion, we learned that all of the GE Smart Factory Portfolio are becoming available not only on-premises but also on cloud or hybrid. As a fully-hosted managed service for MES-as-a-Service, MES can always be up to date with…
The Product Information Disconnect
How can manufacturers overcome their product data gaps to improve new product introduction and drive product profitability? Jim Brown joined Propel’s Converged Live webinar, The Product Information Disconnect: How Collaboration Drives Business Value and Customer Loyalty, to preview his latest research on the product information disconnect and how to solve it. View the webinar on demand to hear…