Jim Brown contributed a guest post to the Siemens PLM Community blog discussing the opportunity for food and beverage companies to leverage digitalization and the digital enterprise to combat market disruption from new, innovate companies that are challenging current industry leaders. The post offers several ways that consumer packaged goods (CPG) companies can get started…
- Product and organizational complexity drive them beyond basic PDM capabilities
- A full-featured PLM implementation may feel out of reach
Get Started with the Right PLM Solution
Core PLM can quickly add value to midsized high-tech companies by helping them combat complexity, improve productivity, and innovate faster to meet market needs. Recognize the potential value of a fully featured PLM with all of the bells and whistles, but be honest with yourself about how much time and effort your company can afford to get there (at least right away). Don’t take on too much. Start with the basics and get value quickly, but recognize the shortcomings of simple file sharing solutions that fall short for the complex, multi-discipline products and product development environments common to midsize high-tech companies. Look for a solution that allows you to design in the context of your products in real time, but also in the context of processes and product development projects. In addition, look for PLM that incorporates automation including automatic project updates to keep engineers focused on innovation instead of managing files. Finally, make sure to leave your company room to grow as your business and business needs grow, using the initial implementation as a foundation for greater improvements. *This summary is an abbreviated version of the eBook and does not contain the full content. A link to download the full eBook is available above. If you have difficulty obtaining a copy of the research, please contact us using the "Contact" link below. [post_title] => Finding PLM to Fit Mid-Sized High-Tech Companies (ebook) [post_excerpt] => [post_status] => publish [comment_status] => open [ping_status] => open [post_password] => [post_name] => plm-midsize-ht [to_ping] => [pinged] => [post_modified] => 2022-11-14 22:28:04 [post_modified_gmt] => 2022-11-15 03:28:04 [post_content_filtered] => [post_parent] => 0 [guid] => http://tech-clarity.com/?p=6177 [menu_order] => 0 [post_type] => post [post_mime_type] => [comment_count] => 2 [filter] => raw ) [2] => WP_Post Object ( [ID] => 6216 [post_author] => 2572 [post_date] => 2017-07-18 22:28:54 [post_date_gmt] => 2017-07-19 02:28:54 [post_content] =>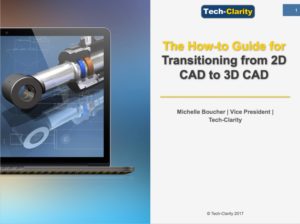
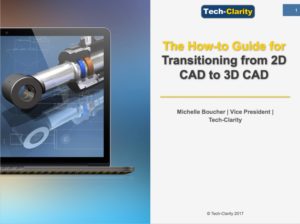
- Transitioning from 2D CAD to 3D CAD
- Migrating from 3D CAD to a new 3D CAD
- Adopting model-based definition (MBD)
Why Change from 2D to 3D?
While 2D offers a lot of simplicity, going to 3D CAD can offer multiple benefits:- Find problems earlier during design by checking for interferences.
- Identify quality problems and improve performance by conducting virtual tests.
- Evaluate more design iterations to arrive at a more innovative solution.
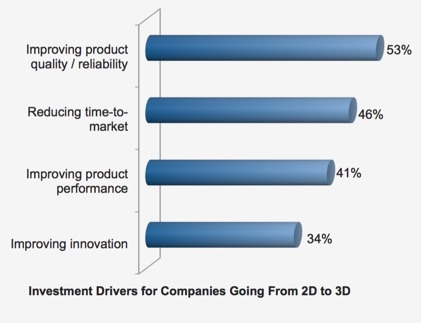
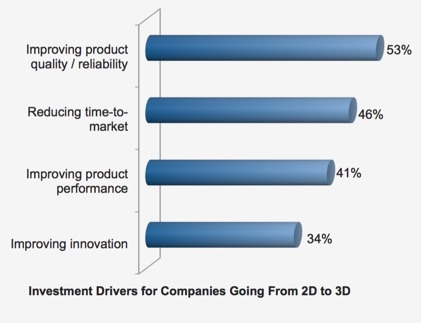
Benefits of Transitioning to 3D
The most exciting part of the results is the number of benefits companies enjoy by transitioning to 3D CAD. Regardless of performance, companies report many benefits, but Top Performers experience even more. Both groups report fewer errors and easier changes. However, Top Performers seem to use their CAD tool more strategically. In addition to using it as a design tool, they also view it as a helpful collaboration tool. Consequently, they get more feedback on the design, and can take advantage of the collective expertise of the product team. This creates more opportunities to catch problems and improve quality and performance.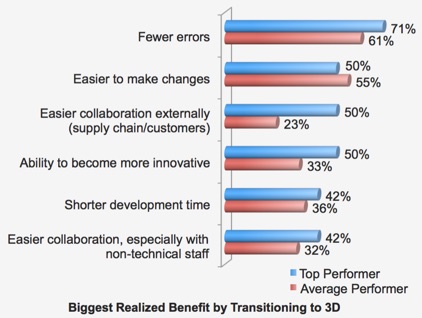
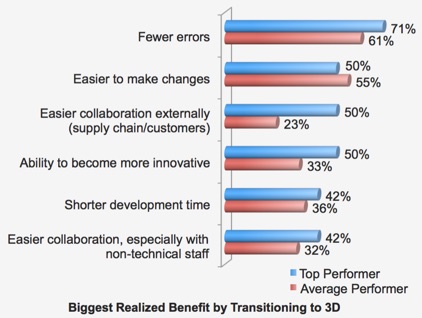
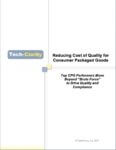
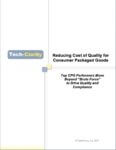
Executive Overview
Quality management is critical to the success and profitability of a Consumer Packaged Goods (CPG) company. According to Tech-Clarity research, Successful Products Begin and End with the Customer, over three-quarters of CPG Companies say higher quality is required to drive competitive differentiation. It’s also clearly important to deliver customer satisfaction, safety, regulatory compliance, corporate responsibility, and overall company profitability.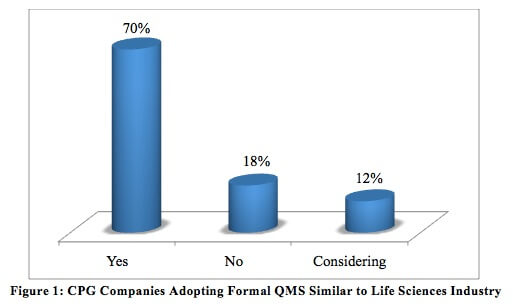
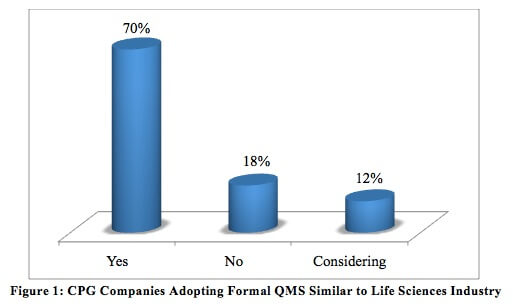
- Take a more integrated approach to quality along geographic, organizational, and product lifecycle dimensions
- Adopt a more digital approach to managing quality, relying less solely on paper and isolated electronic documents
- Enable quality management with more automation and advanced technology, including automated data collection, analytics, and product documentation automation
- Use more integrated solutions to manage quality and pursue a platform approach to quality solutions
Table of Contents
- Executive Overview
- The Quality Imperative
- Managing Quality Carries Enterprise-Level Challenges
- Quality and Mistakes Avoided with Brute Force
- What Sets Apart Top Performers in Quality?
- Top Performers Take a More Integrated Approach to Quality
- Top Performers Extend Data and Processes to More Functions
- Top Performers Use More Automation, Advanced Technology
- Top Performers Enable Quality Digitally
- Top Performers Enable Quality with a Platform Approach
- Conclusion
- Recommendations
- About the Author
- About the Research
- About the Sponsor
Conclusion
Quality Management is crucial for CPG companies, but they face significant challenges. Although CPG companies report they are relatively effective at preventing significant issues, they face excess Quality Management related costs. Top Performers, on the other hand, are able to achieve better quality results from both quality and cost perspectives. They appear to have broken out of the paradigm of “better quality or lower cost, choose one.” They do this by taking a more holistic approach to quality, using more advanced tools like analytics, and leveraging more automation. Beyond the individual tools they use to manage quality, Top Performers take a much more integrated approach to organization, processes, and systems. They are more likely to have integrated data and processes, integrated systems, and pursue a platform approach for Quality Management. Our conclusion is that an integrated, digital approach to Quality Management in the CPG industry drives better business results from both quality and cost perspectives.Recommendations
Based on industry experience and research for this report, Tech-Clarity offers the following recommendations:- Take a holistic view and approach to quality
- Move away from brute force Quality Management practices
- Adopt automation for more current, trusted data
- Adopt advanced tools like analytics to improve quality
- Move to a digital approach
- Integrate quality systems
- Leverage a platform of solutions to enable more holistic, integrated quality to improve quality without increasing cost, or reduce cost and maintain quality
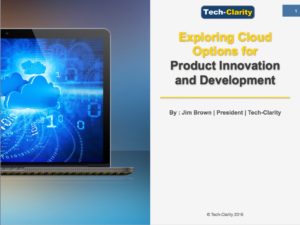
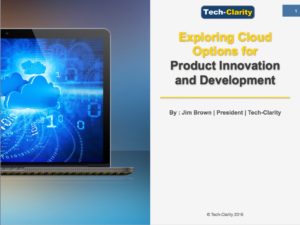
The Cloud Opportunity for PLM
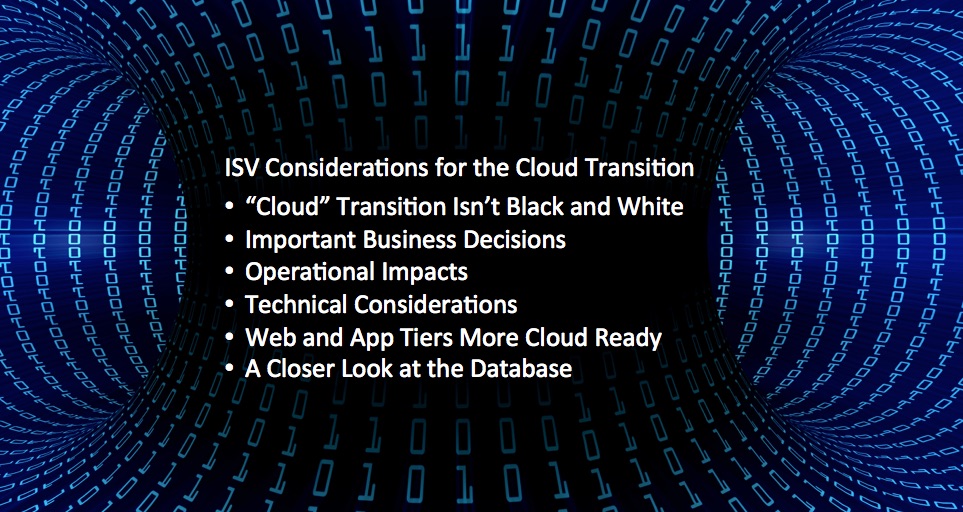
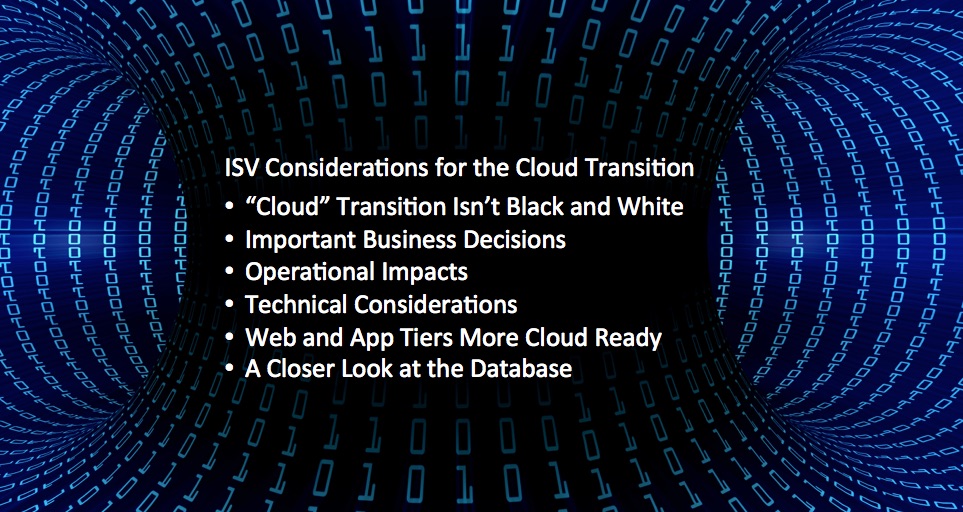
Conclusion and Recommendations
For PLM, the move to the cloud has begun. Whether a vendor is moving all of their applications to the cloud, some of them, or offering a hybrid solution, it’s an evolution that requires a lot of decisions. After all, shifts in computing infrastructure and paradigms have historically resulted in major disruption for vendors, leading to major shifts in the competitive landscape as new players emerge and older players fade into the sunset. PLM vendors can, and are, making the transition to the cloud. They key considerations in this eBook are a guide to help identify the implications of the change. PLM vendors considering shifting to the cloud should:- Recognize that the cloud opportunity for customers is compelling
- Understand the impacts on them as an ISV
- Develop a strategy – even if it’s not to move solutions to the cloud
- Create a business plan to support the strategy and educate customers and investors about it
- Understand and address likely operational impacts, considering a DevOps approach
- Recognize and address technical issues
- Look for an architecture that provides cloud benefits to customers as well as the ISV (scalability, lower total cost of ownership) and room to grow over time
- Don’t underestimate the role of the database. Look for a DBMS aligned to your business needs and don’t force your business or application to radically change to fit the choice
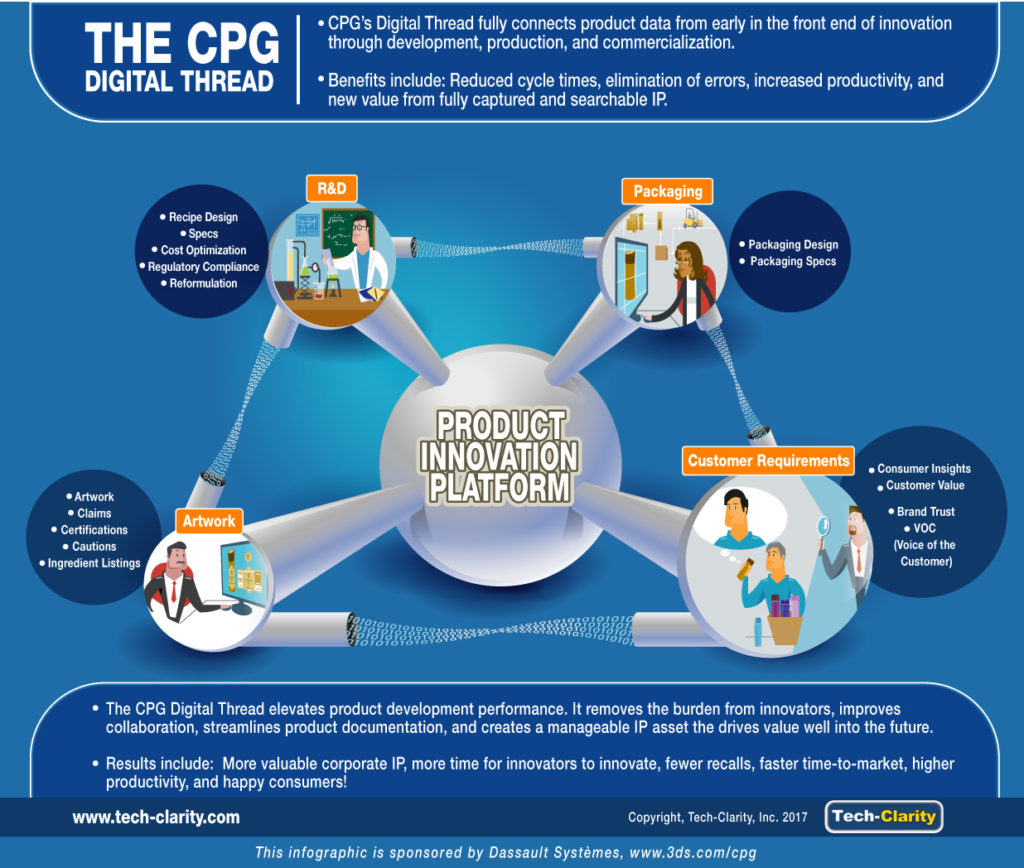
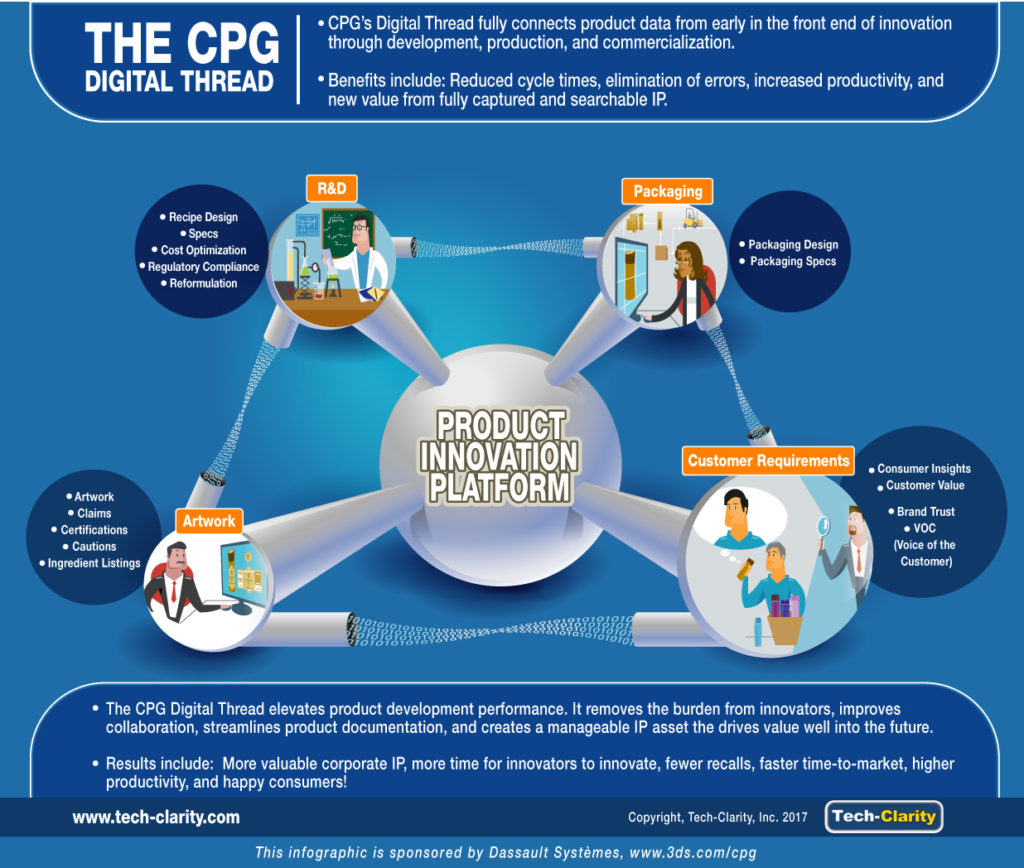
Click the image for a closer look!
To learn more, please see The CPG Digital Thread Overview (free of charge, no registration required) or download the full The CPG Digital Thread eBook from our sponsor Dassault Systèmes (free or charge, registration required).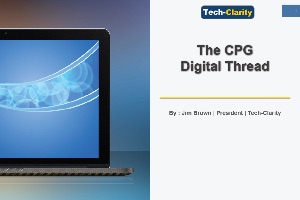
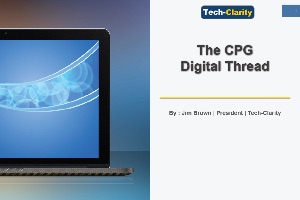


Hear Michelle Boucher's interview with David Wolf from PTC on medical devices. They focused on key topics for medical device companies, including the Case for Quality.
During the discussion, Michelle shared research on medical device industry trends. She also discussed the implications for the Case for Quality and offered advice to efficiently manage regulatory compliance. Throughout the discussion, she asked David Wolf for his thought's and how PTC is supporting key trends in the medical device industry. Access the recording from this event as well as other health care webcasts and content here.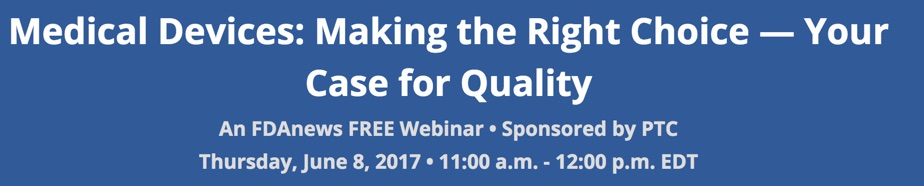
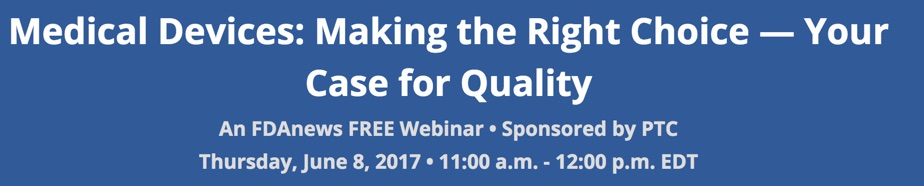
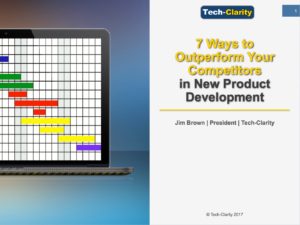
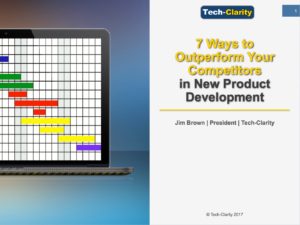


- Focus on market speed
- Compete on innovation at multiple levels
- Plan for success with better portfolio processes and requirements
- Go beyond product excellence to market excellence
- Adhere to their product development process
- Adopt a more integrated, holistic view of NPDI
- Enable innovators with more collaborative, agile systems
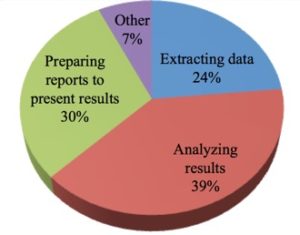
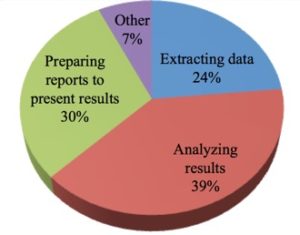
- Common challenges during the postprocessing phase
- Best practices to overcome those postprocessing challenges
- Case studies demonstrating the benefits of efficient postprocessing
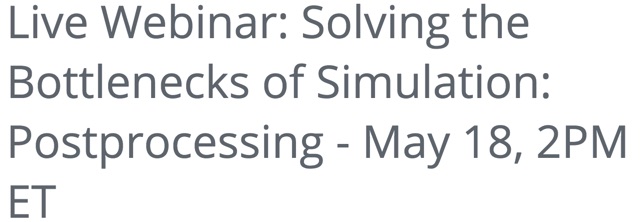
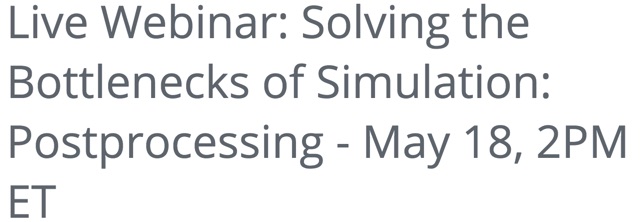
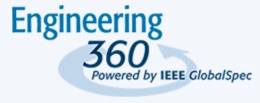
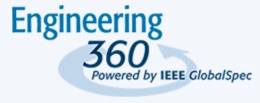
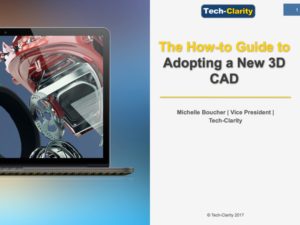
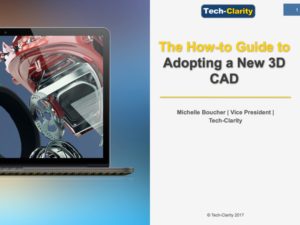
- Transitioning from 2D CAD to 3D CAD
- Migrating from 3D CAD to a new 3D CAD
- Adopting model-based definition (MBD)
Why Change to a New 3D CAD Tool?
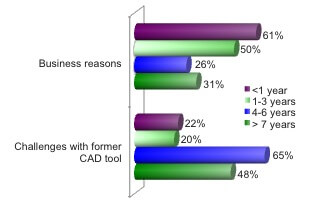
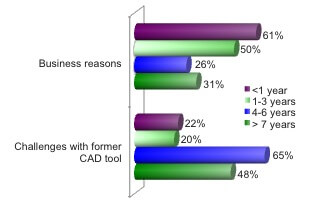
Benefits of a 3D-to-3D Transition
Since implementing their current 3D CAD tool, companies report several improvements. By following best practices to support their transition to a new 3D CAD tool, Top Performing Implementers realize even more benefits. The table shows the respective improvements reported by each group.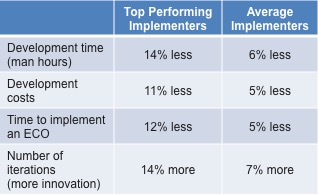
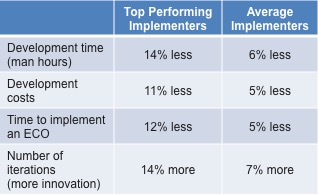


- If you already completed the survey –> please share with a colleague or on social media using the “Share/Save” buttons above.
- If you haven’t taken the survey –> please:
CLICK HERE TO TAKE THE SURVEY NOW!
Rules
To be eligible for this offer, you must complete the survey and be a professional with job responsibilities related to or supporting the development, release, or manufacture of smart products. Vendors and consultants who sell software, solutions, or services to support product development are not eligible. Students without relevant professional work experience are also not eligible. A valid work email is required to receive the gift card. To verify eligibility, your work email must include the domain of your place of employment. Email addresses will be kept confidential and will not be used for any direct sales or marketing purposes. Duplicate responses will be disqualified. Winners will be notified when the survey is closed.
[post_title] => Transforming Product Design for Today’s Smart Products (survey invite) [post_excerpt] => [post_status] => publish [comment_status] => open [ping_status] => open [post_password] => [post_name] => smart_products [to_ping] => [pinged] => [post_modified] => 2022-11-14 22:27:52 [post_modified_gmt] => 2022-11-15 03:27:52 [post_content_filtered] => [post_parent] => 0 [guid] => http://tech-clarity.com/?p=6076 [menu_order] => 0 [post_type] => post [post_mime_type] => [comment_count] => 4 [filter] => raw ) [13] => WP_Post Object ( [ID] => 6063 [post_author] => 2 [post_date] => 2017-04-25 12:37:57 [post_date_gmt] => 2017-04-25 16:37:57 [post_content] => Jim Brown joins Autodesk's Michael Vesperman during this Engineering Live panel discussion moderated by Janine Mooney, Editor in Chief at Advantage Business Media. Jim and Michael share insights from recent survey results and customer experience in an interactive discussion on NPDI. They share NPD best practices and technology including 7 things that Top Performers in NPDI do differently than the rest. Watch the on demand replay now!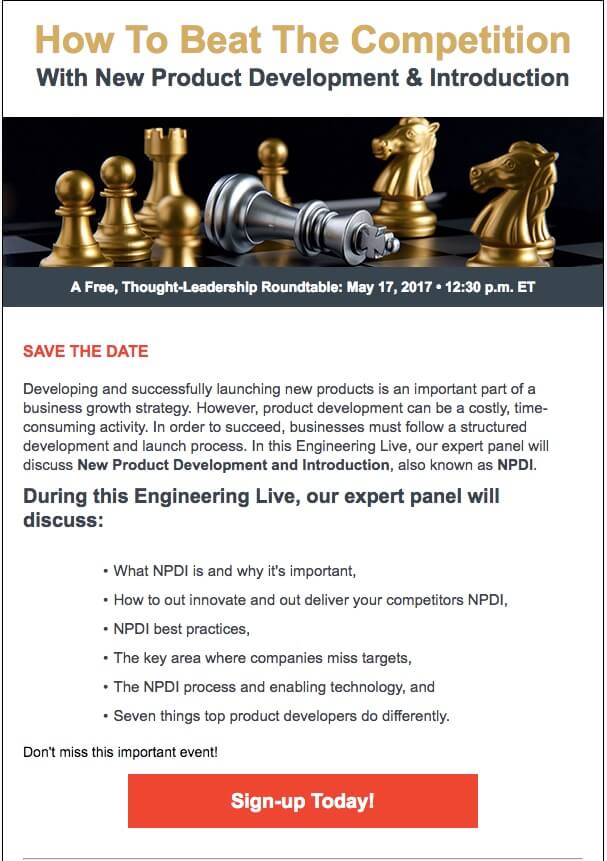
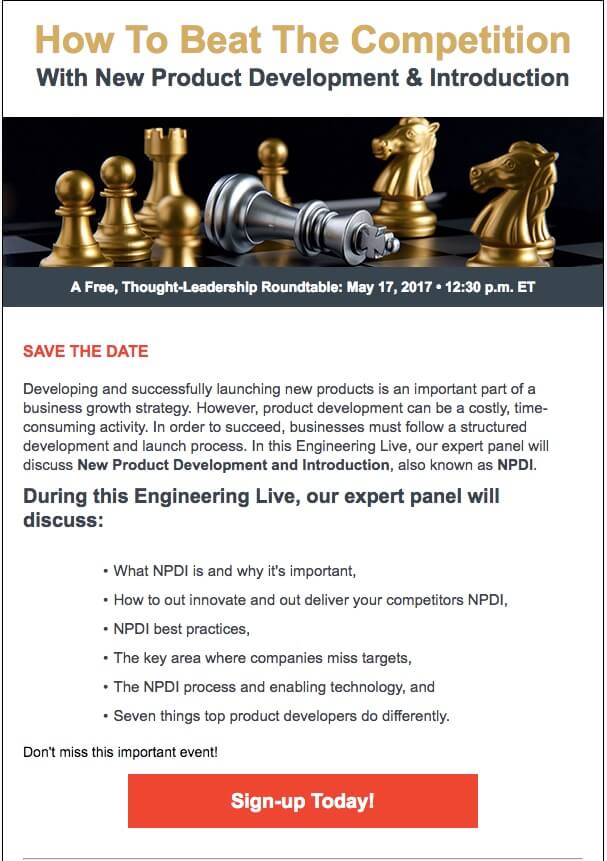
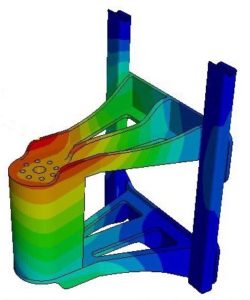
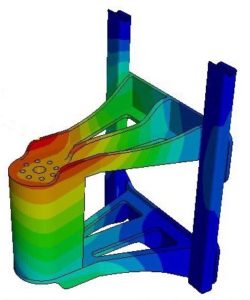
- The top improvement areas you should focus on to get even more value from simulation
- Common challenges during the preprocessing phase
- Best practices to overcome those preprocessing challenges
- Case studies demonstrating the benefits of efficient preprocessing
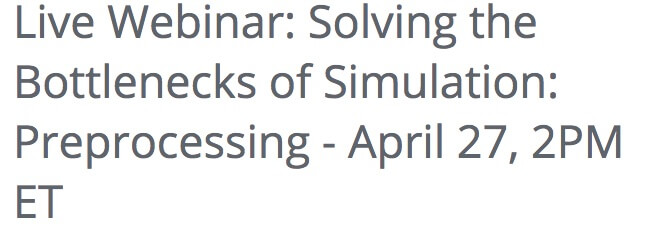
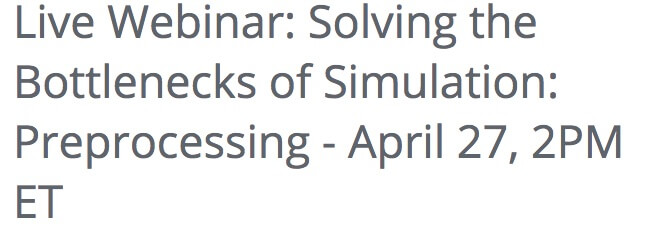
Please enjoy the summary below, or click the report or title to download the full PDF (free of charge, no registration required thanks to our sponsor, Siemens PLM).
Executive Overview
Our previous report, Best Practices in Managing Design Data, showed that “Companies with world-class performance are more likely to have very effective data management capabilities.” Now, we’ve extended that earlier research with new survey data to take a fresh look at data management challenges and best practices. We also take a deeper dive into product complexity, explore whether companies still suffer from non-value-added time managing data, and quantify the impact of improving design data management. Survey results indicate that data management is still a big business challenge. Complexity has continued to grow, resulting in poor productivity even for smaller companies. Almost one-third of companies surveyed report their technical resources spend more than 25% of their time on non-value-added data management tasks! The survey also uncovers that data management is evolving, including significant growth in the use of cloud-based file sharing tools. It appears that the adoption of these tools may be making it easier for companies to share their designs, but making it more difficult to effectively control design data. The prior report makes suggestions on how to improve data management and resulting productivity, which still hold true. It shows that some companies are more effective at data management and are “more likely to use structured, collaborative design data management technology, 30% more likely to use PDM or PLM.” It also finds that these companies spend 25% less time on nonproductive data management tasks. This survey furthers the research and finds that companies with the highest product development performance, the Top Performers, have higher data management maturity. They:- Use more collaborative design data management capabilities
- Leverage their design data management solutions for more functions
- Have tighter integration between their design tools / CAD and data management
- Couple data management tightly with cloud file sharing (if they’re using cloud)
Table of Contents
- Executive Overview
- Effective Data Management Improves Productivity, Performance
- Design Data Management Continues to be a Struggle
- Data Management Challenges Continue to Impact Productivity
- Complexity on the Rise
- Identifying Data Management Practices of the Top Performers
- Top Performers have Greater Data Management Usage Maturity
- Top Performers have Greater Collaboration Maturity
- Emergence of Cloud Highlights another Dimension of Maturity
- Quantifying Design Data Management Impact on Profitability
- Design Data Management is a Foundation to Grow On
- Conclusion
- Recommendations
- About the Author
- About the Research
- References and Links
Conclusion
Product and product development complexity are on the rise, bringing with it significant reductions in design productivity for companies small and large. The leaders are combatting this complexity with design data management. Top Performers have been shown to use more structured, collaborative solutions including PDM and PLM. This research shows that even if these tools are not within reach, companies can improve their design data management maturity and achieve a productivity and business performance advantage. Companies can extend their design data management in several ways. The first is to follow more formal data management processes. The second is to use their CAD tool to help manage designs if they are using less formal design data management capabilities like network drivers or cloud file-sharing. “The combination of cloud file sharing with some sort of data control is a great solution for smaller companies,” concludes Bird Technologies’ Winter. “As soon as our vendor made this available it was a no-brainer and we jumped on it right away.” Finally, companies can improve performance by increasing their design usage maturity, leveraging their design data management solution to support more tasks. There is always room to improve. The Top Performers are extending their design data management maturity in multiple ways, and are more able to leverage their design data management foundation to gain higher benefits over time.Recommendations
Based on industry experience and research for this report, Tech-Clarity offers the following recommendations:- Understand the complexity is a larger driver of design data management issues than company size
- Recognize the impact of increasing product complexity and improve design data management maturity to mitigate the risk
- Use formal data management tools such as PDM or PLM, if accessible
- If formal systems aren’t available and you’re using network or cloud file management, at a minimum improve maturity through better processes
- For greater levels of performance, leverage your CAD tool’s capabilities to help manage complexity
- Extend the usage maturity of design data management to continually improve and raise the bar on productivity and business performance relative to the competition
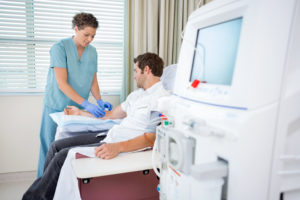
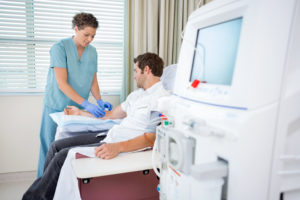


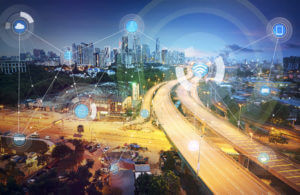
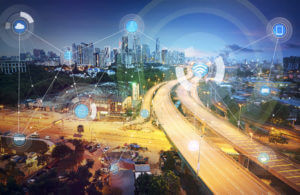


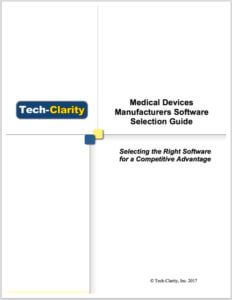
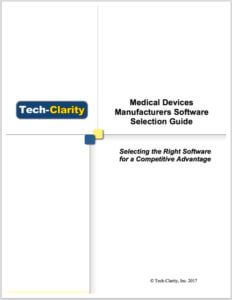
- Software capabilities
- Implementation
- User adoption
- Support
- Vendor characteristics / attributes
- Unique business needs
Table of Contents
- Executive Overview
- Identify Your Challenges
- Transition from Document Centric to Product Centric
- Consider the Complete Lifecycle
- Manage the Product
- Manage Requirements (Customer Needs to Regulatory)
- Support Product Development for Hardware
- Support Software Development
- Enable Smart and Connected Products
- Ensure Regulatory Compliance
- Support Quality Management
- Plan for Manufacturing
- Control Suppliers
- Plan for Service
- Assess Implementation Requirements
- Consider Vendor Attributes
- Identify Specific Needs for your Company
- Conclusion
- Recommendations
- About the Author
Executive Overview
Medical device companies are in the business of making people’s lives better. As Joel Hembrock, Senior Designer and CAD Administrator at Medtronic says, “Our patients are the people who benefit from our products. Restoring life is our main focus. [We want] to be giving people their lives back, restoring their health, allowing them to actually live again and not have their disease or any other ailment keep them from being able to live.” With lives at stake, patient safety is of the upmost importance. As such, the industry faces heavy regulations. Compliance is so critical that if medical device companies do not adhere to FDA, EU and other worldwide standards and regulations, they will not be profitable. However, so much time, effort, and cost goes into compliance documentation, it takes efforts away from innovating and ensuring high quality products. Consequently, it is harder to take advantage of opportunities that will boost profitability. On the other hand, medical device companies who adopt practices focused on high quality devices can expect greater patient satisfaction, improved competitiveness, and higher profits. In fact, McKinsey estimates that companies who adopt quality focused best practices can increase profits by 3% to 4% of revenues. They estimate the revenue increase alone could be a $3.5 billion opportunity for the industry and this doesn’t even factor in profitability improvements by avoiding costly quality issues. To achieve this, companies need to be empowered to shift from a document centric process to one that focuses on high quality, innovative products that meet patient needs. The good news is that with investments in the right technology, this is possible. Technology can reduce manual, time intensive reporting processes to a push of a button. Rather than structuring processes around documentation, technology can allow you to focus on developing the right products and services that will meet patient needs. For these reasons, some medical device manufacturers are integrating quality processes into core product lifecycle management activities. By integrating quality processes throughout the product design and delivery lifecycle, companies can improve efficiency. With this approach, time spent searching for compliance supporting documentation and reporting, can instead be invested in quality and innovation. The result will be greater profitability. Other changes in the medical device industry are coming from recent trends such as the transition to outcome-based healthcare in the US. In some cases, to be compensated, medical professionals must show positive patient outcomes. One way to accomplish this is to take advantage of innovation enabled by the Internet of Things (IoT). This along with requirements for Unique Device Identifiers (UDI’s) can provide new levels of traceability and communication that can demonstrate device effectiveness. However, to take advantage of this and manage it, the right technology must be in place. While many of these issues may require new investments in technology, existing systems that are working well, should be leveraged. Working solutions such as Manufacturing Execution Systems (MES), Enterprise Resource Planning (ERP) and Product Lifecycle Management (PLM) should be considered when selecting a complete solution to manage medical devices. The new solution should use a platform that will leverage and extend the investments made in existing solutions. With so much to consider, how do you know what will be the right technology? This buyer’s guide will serve as guidance to help you select what is right for your company. This guide consists of four major sections covering software tool functionality required for medical device companies, implementation requirements, vendor attributes, and special company considerations (Figure 1).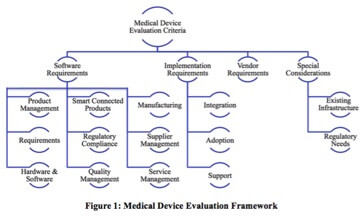
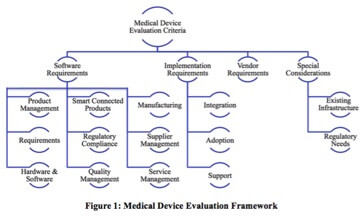
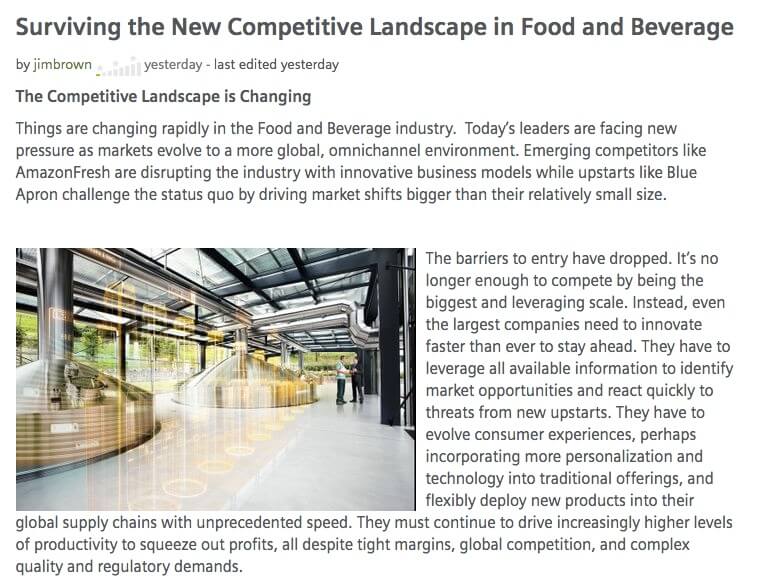
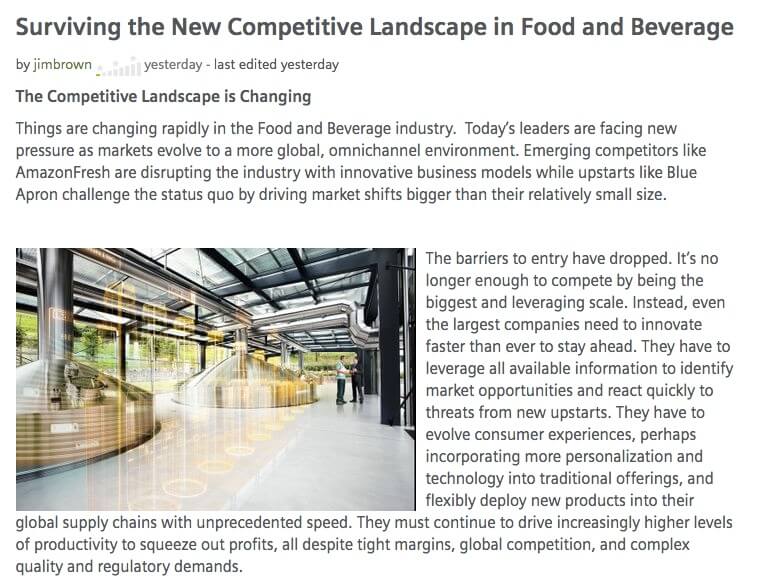
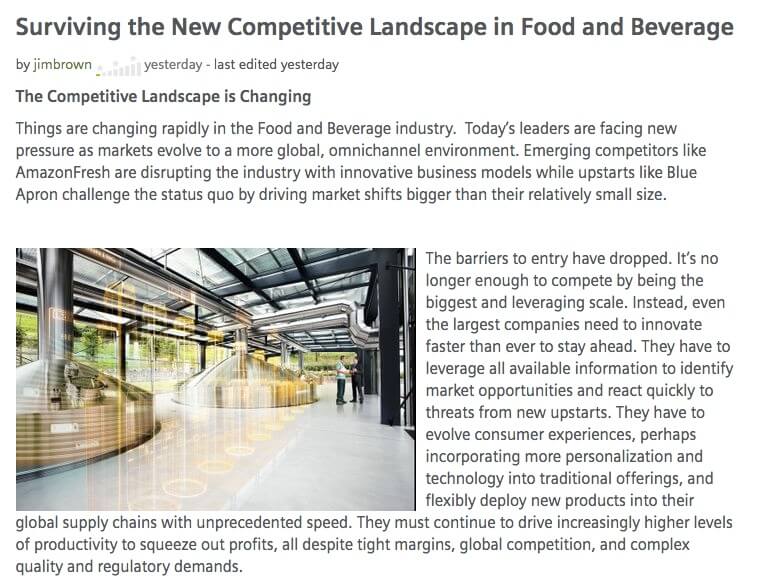
All Results for "All"
Finding PLM to Fit Mid-Sized High-Tech Companies (ebook)
The Finding PLM to Fit Mid-Sized High-Tech Companies ebook explains how smaller companies in the high technology industry find themselves stuck between full-featured Product Lifecycle Management (PLM) systems that feel out of reach and less capable solutions including cloud-based file sharing or very basic data management applications. They know they can’t afford the errors and inefficiency inherent to…
Best Practices for Going from 2D to 3D CAD (eBook, survey findings)
The How-to Guide to Transitioning from 2D CAD to 3D CAD shares best practices for moving from 2D to 3D. The guide shares the reasons you should consider going from 2D to 3D, common challenges to avoid, and benefits enjoyed by other companies who gone to 3D. The guide then shares advice to make your switch…
Reducing Cost of Quality for Consumer Packaged Goods (survey report)
The Reducing Cost of Quality in CPG report shares perspectives from a survey of over 175 CPG companies to determine how Top Performers manage consumer packaged goods quality. The research finds that these leading companies are able to achieve better quality results with lower internal costs. The report analyzes their processes, organizational structures, and enabling…
Cloud Considerations for PLM Software Vendors (eBook)
This eBook takes a look at the cloud opportunity for PLM from the vendor perspective. It highlights the fact that although customers are rewarded with lower complexity and risk by moving to the cloud, vendors often face higher complexity and risk. It reviews the options ISVs have to move existing solutions to the cloud and…
The CPG Digital Thread (infographic)
This infographic shares the importance of developing a cohesive digital thread when developing formulated products in the consumer packaged goods industry. The digital thread should be driven by customer requirements and incorporate the recipe / formulation, specifications, packaging design, compliance information, claims, cautions, ingredients, labeling, artwork, and more to provide a full view of the product…
Cost Effective Quality in CPG (webcast, survey results)
Join Tech-Clarity’s Jim Brown on this webinar sharing recent survey results from almost 200 Consumer Packaged Goods companies, delving into their quality issue and how top performing CPG companies achieve better quality without suffering from excess internal cost. Learn the process, organizational, and technology approaches that Top Performers leverage to overcome their challenges and drive cost-effective quality. This Business…
Live Interview – Achieve the Case for Quality (webcast)
Hear Michelle Boucher’s interview with David Wolf from PTC on medical devices. They focused on key topics for medical device companies, including the Case for Quality. During the discussion, Michelle shared research on medical device industry trends. She also discussed the implications for the Case for Quality and offered advice to efficiently manage regulatory compliance. Throughout the discussion, she asked David…
7 Ways to Outperform Your Competitors in NPD (eBook, survey results)
This eBook shares survey results analyzing companies’ ability to hit new product development (NPD) targets, then offers seven practical tips identified by the research as best practice processes, organization, and technology leveraged by the top performing product developers. The research provides recommendations to companies based on the approaches taken by the Top Performers, those that are able to outperform…
Solving the Bottlenecks of Simulation: Postprocessing (Webcast)
Listen to Michelle Boucher share best practices to improve the efficiency of simulation postprocessing. During this webinar, Shawn Wasserman, simulation editor at ENGINEERING.com, joined Michelle. This webinar reveals: Common challenges during the postprocessing phase Best practices to overcome those postprocessing challenges Case studies demonstrating the benefits of efficient postprocessing Access the recording here.
Quality The Product Driver At Novo Nordisk (webcast)
On Tuesday May 9, 2017 Michelle Boucher conducted a live interview with Lisbeth Sivertsen, expert at Novo Nordisk for product quality strategy. They focused on key topics for medical device companies, including the Case for Quality. During the discussion, Michelle shared research on medical device industry trends. She also discussed the implications for the Case for Quality and offered advice to efficiently manage…
Adopting a New 3D CAD (survey findings eBook)
The How-to Guide to Adopting a New 3D CAD shares best practices for changing from one 3D CAD tool to another. The guide shares the reasons you should consider making a change, potential benefits of making a change, and advice for selecting a new tool. The guide then goes deeper into the steps you should take…
Transforming Product Design for Today’s Smart Products (survey invite)
Are you making your products smarter? Are you feeling pressure to add software and electronics? Please share your experience, thoughts, and lessons learned in this new survey on transforming product design to develop smart products. The survey explores challenges you should be aware of, the impacts of those challenges, and how to avoid them. We will explore…
Beating the Competition with New Product Development and Introduction (webcast)
Jim Brown joins Autodesk’s Michael Vesperman during this Engineering Live panel discussion moderated by Janine Mooney, Editor in Chief at Advantage Business Media. Jim and Michael share insights from recent survey results and customer experience in an interactive discussion on NPDI. They share NPD best practices and technology including 7 things that Top Performers in NPDI…
Solving the Bottlenecks of Simulation Preprocessing (webcast)
Listen to Michelle Boucher share tips to improve the efficiency of simulation preprocessing. During this webinar, Shawn Wasserman, simulation editor at ENGINEERING.com, joined Michelle. This webinar reveals: The top improvement areas you should focus on to get even more value from simulation Common challenges during the preprocessing phase Best practices to overcome those preprocessing challenges Case studies…
Design Data Management Maturity Improves Profitability (survey report)
The Design Data Management Maturity Improves Profitability, Analyzing Best Practices for Managing Designs report shares fresh survey data and interviews. It updates our design data management research to cover new trends like using cloud file sharing applications to manage data. It also drills down on the topics of complexity and non-value added time spent managing design data,…
Four Ways Medical Device Companies Can Become More Profitable – Guest Post on PTC Blog
In this PTC guest post, Michelle Boucher shares Four Ways Medical Device Companies Can Become More Profitable. As companies plan for 2017, medical device companies should consider these four suggestions to help them improve margins. The post touches on topics such as the cost of compliance, the Case for Quality, and considerations for the impact of IoT….
Tips for Designing IoT Products: Use Model-Driven IoT Code – Guest Post on PTC Blog
Michelle Boucher shares tips for designing IoT products and systems by using model-driven IoT code in this PTC guest post. As a result of reading this post, you will have a better understanding of how this can be a helpful step for those looking to incorporate the Internet of Things (IoT) technology in their products. Many products…
Medical Devices Manufacturers Software Selection Guide
Tech-Clarity’s Medical Devices Manufacturers Software Selection Guide helps manufacturers identify the right buying criteria for software solutions to support developing, producing, and servicing medical devices. This buyer’s guide also takes into account unique needs for medical device companies including regulatory compliance and support for the FDA’s Case for Quality. Tech-Clarity’s Buyer’s Guides go beyond software functionality to…