What is needed for manufacturers to improve the maturity of BOM-related processes to help to manage complexity, improve efficiency, prevent mistakes, and enhance collaboration across departments and the supply chain? Read our buyer’s guide to find out. Please enjoy the summary below. Click here for the full report, thank you to our sponsor PTC. …
- Introducing the Buyer's Guide
- Diagnosing BOM Management Issues
- The BOM Management Status Quo
- The BOM Management Business Case
- Analyze BOM Management Solution Capabilities
- Assess Service Requirements
- Consider Vendor Requirements
- Special Considerations
- Prepare for the Digital Enterprise
- Conclusion
- Recommendations
- About the Author
- About the Research
- Acknowledgments
Introducing the Buyer's Guide
BOM Fundamentals Managing Bills of Material (BOMs) is a fundamental need for any manufacturer. Without effective control of product structures, companies struggle with inefficiency and errors. On the other hand, improving the maturity of BOM-related processes helps manage complexity, improve efficiency, prevent mistakes, and enhance collaboration across departments and the supply chain. Improving the maturity of BOM-related processes helps manage complexity, improve efficiency, prevent mistakes, and enhance collaboration across departments and the supply chain. The resulting benefits can be strategic, leading to increased agility and faster time to market that impact top-line financial performance. This Buyer's Guide is a reference tool for manufacturers selecting a system to improve the maturity of their BOM. It also shares that digital BOM management is critical to support digital transformation initiatives including the digital twin, the Internet of Things (IoT), Virtual Reality (VR), and Augmented Reality (AR).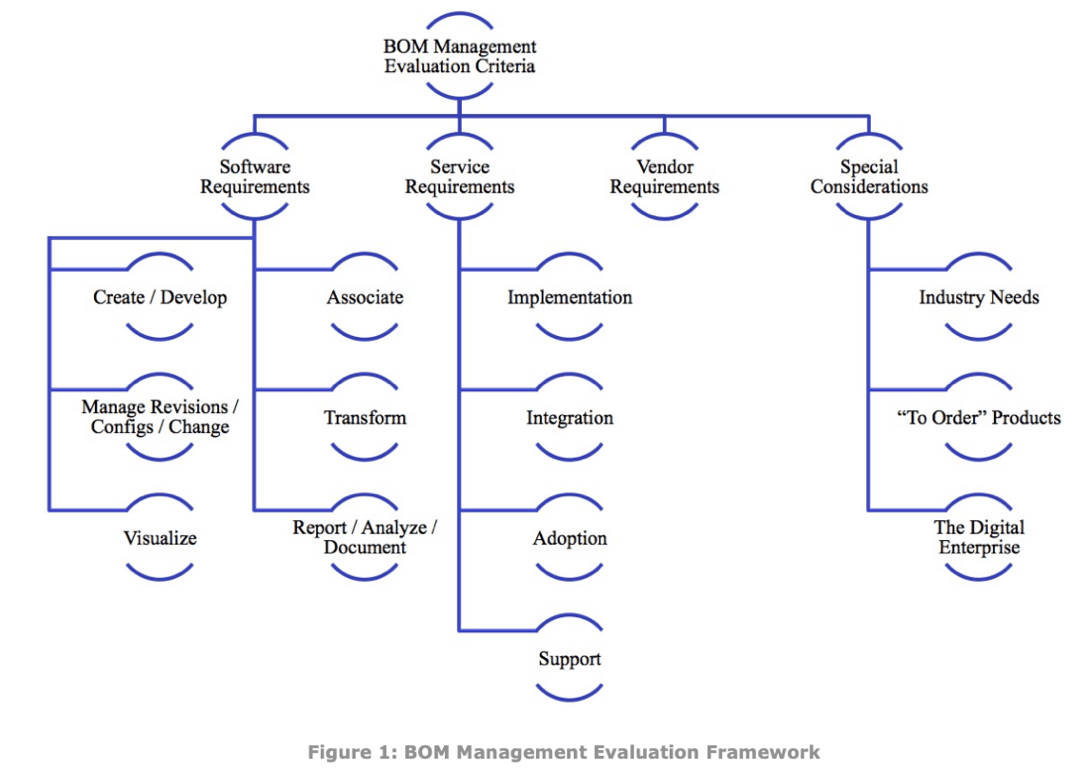
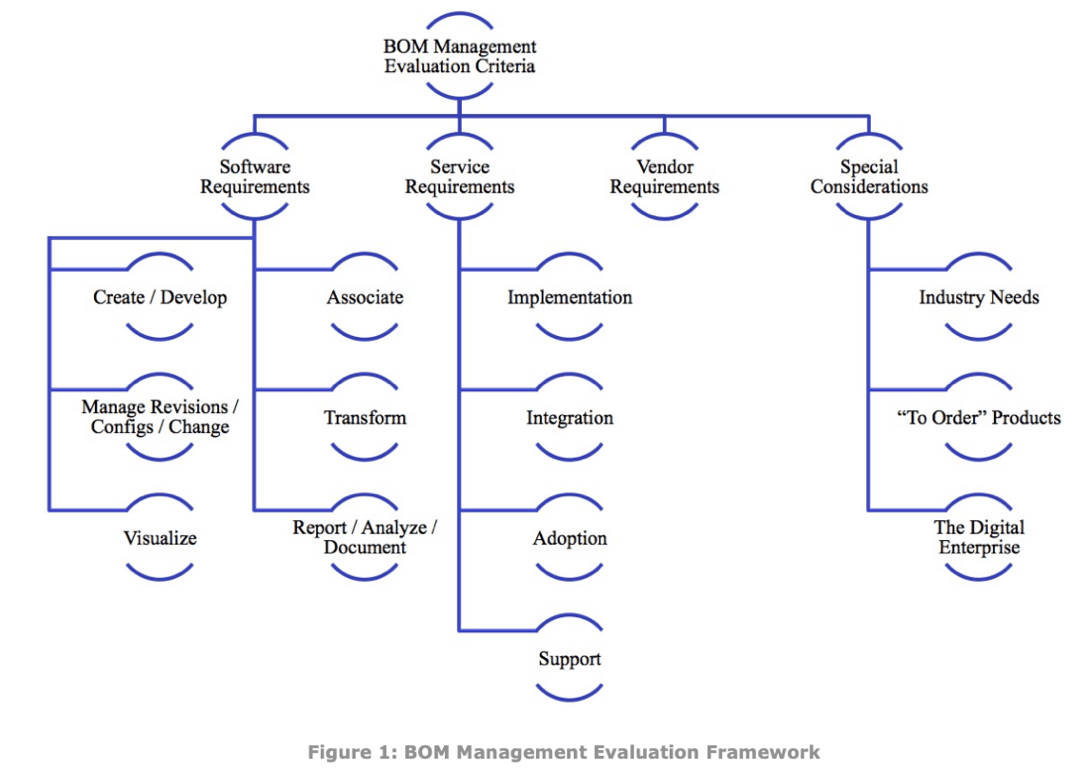
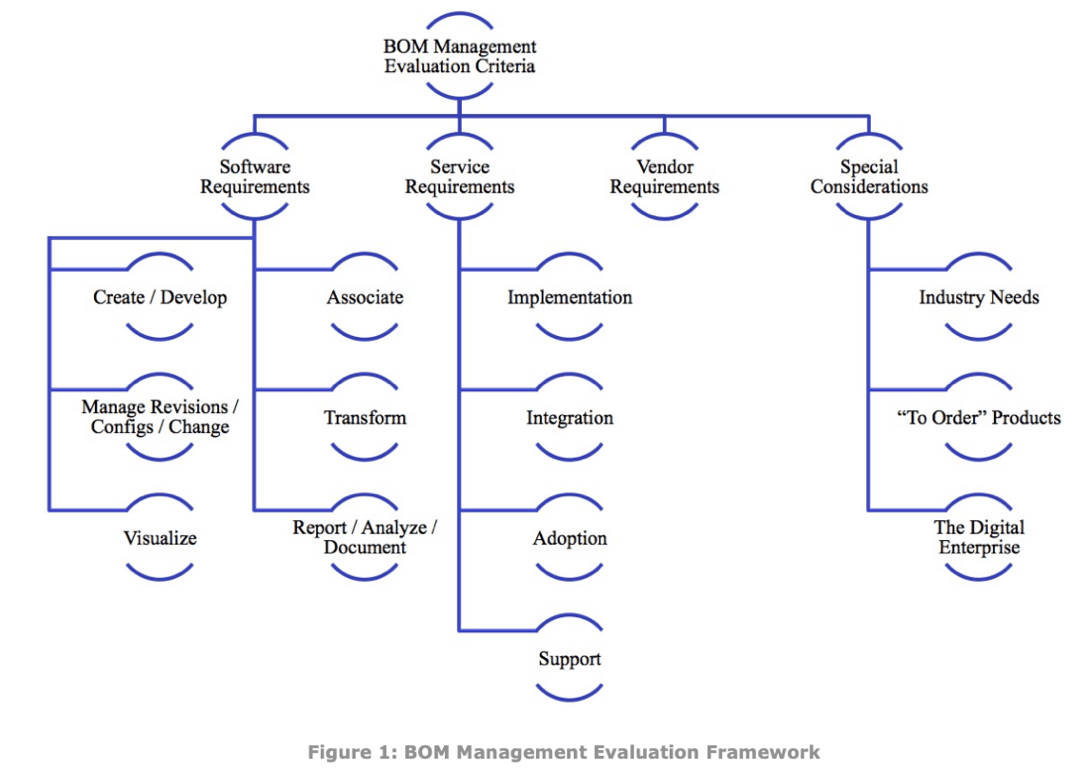
- Errors in manufacturing
- Poor first pass yield
- Ordering the wrong parts
- Delays due to part shortages
- Inability to confidently adopt engineering changes
- Slow time to full volume production
- Late identification of manufacturability or serviceability flaws
- Poor traceability
- Compliance issues or excess effort to comply
- Scrap and rework
- Slow review and approval processes
- Develop Product Structures
- Manage Revisions, Configurations, Change
- Visualize Products
- Associate Information
- Transform BOMs
- Report / Analyze / Document
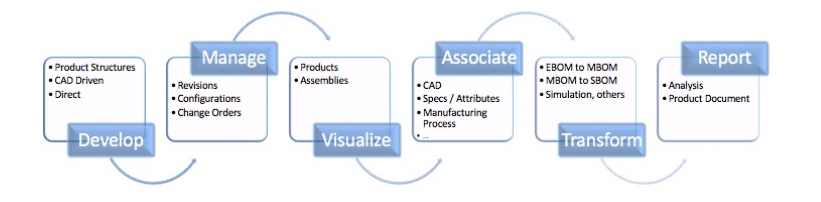
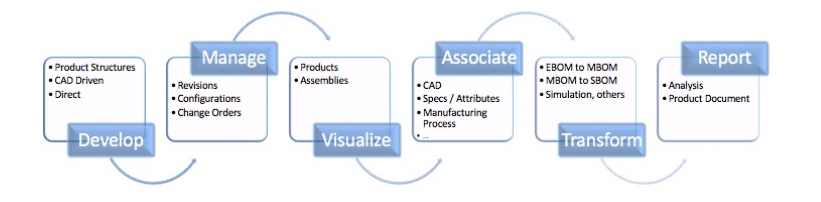
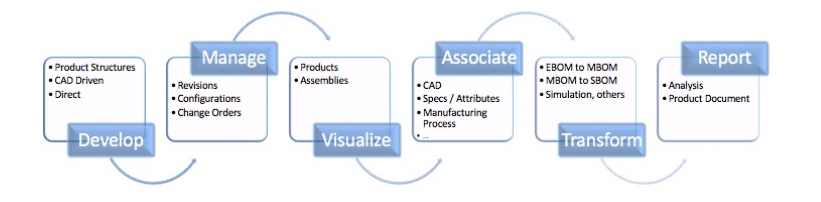
Conclusion
Recommendations
Based on industry experience and research on this report, Tech-Clarity offers the following recommendations:- Think big, but remain agile and take BOM management improvements in steps
- Recognize the importance of accurate, complete, timely, and accessible product structures
- Know your needs
- Understand the value
- Look for functionality, but extend requirements to vendor and service
- Consider any special needs for your business, industry, or geography
- Build the foundation for the digital enterprise, recognizing that BOM management is a key enabler
- Get started
Although manufacturers have started to adopt cloud solutions for many aspects of their business, PLM has lagged behind. Our research shows that over one-half of manufacturers are considering cloud and about one-quarter already leverage the cloud support product innovation and manufacturing. Given the increased interest and adoption, we developed selection criteria to help companies navigate the options and choose the best-suited PLM cloud option for their business.
Please enjoy the summary* below. For the full research, please visit our sponsor PTC (registration required).Table of Contents
- Cloud PLM Adoption Increasing
- PLM Benefits and Business Value
- Increased Value/ROI of Cloud PLM
- Buyer's Considerations
- Choosing the Right PLM
- Considerations for Product Developers
- Considerations for IT
- Considerations for Adoption
- Review Deployment Options
- Evaluate Pricing Options
- Choose the Right Partner
- Special Considerations
- Conclusions and Recommendations
- Acknowledgments
Cloud PLM Adoption Increasing
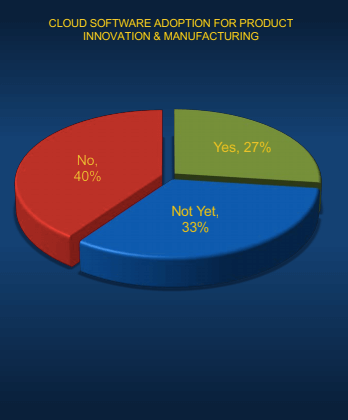
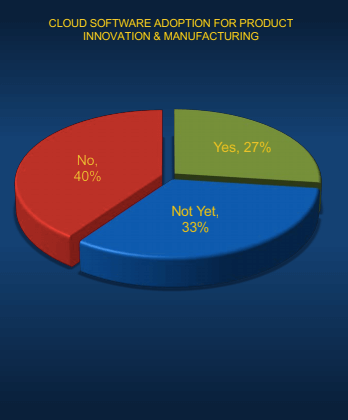
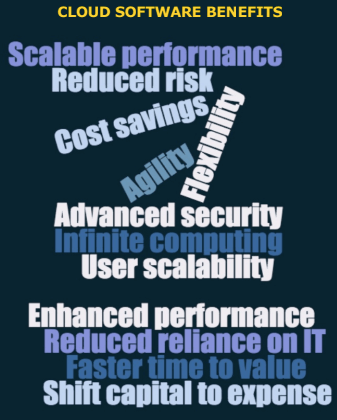
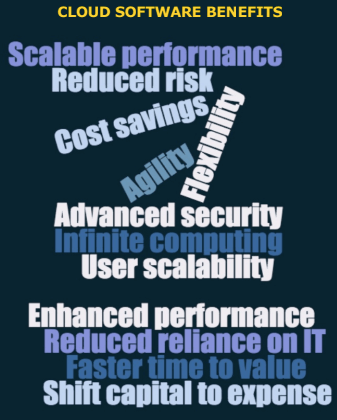
Conclusions and Recommendations
The Cloud Offers Compelling Benefits The cloud makes the significant business value of PLM more accessible and reduces TCO for manufacturers. It offers new opportunities to enhance global reach and collaboration. But there are important things to consider when selecting a cloud PLM system, ranging from deployment options to considerations for certain industries and geographies.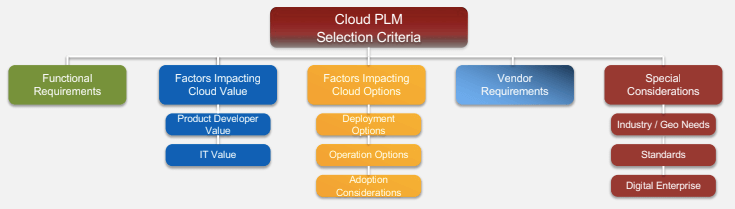
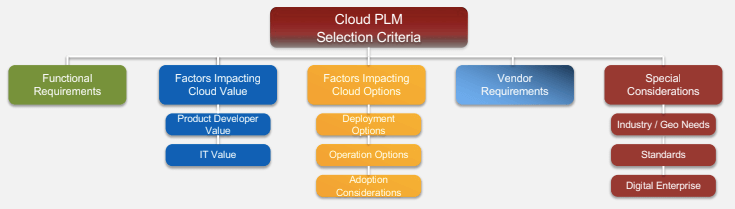
- Evaluate functional solution capabilities first, unless company standards mandate a deployment approach.
- After selecting the right functional solution, evaluate and select optimal deployment and pricing models that give your business the most benefit considering cost, risk, and time to achieve value.
- Consider the strategic value of cloud solutions for global deployments to support “design anywhere, build anywhere” strategies.
- Make sure to consider the future, including the transition to the digital enterprise. We believe that manufacturers that don’t digitalize will be at a competitive disadvantage.
- Narrow down solutions based on these high level criteria to create a smaller list of solutions to evaluate.
- Recognize that any solution selection process will require tradeoffs and understand which types of requirements are the most important to your company’s success and profitability
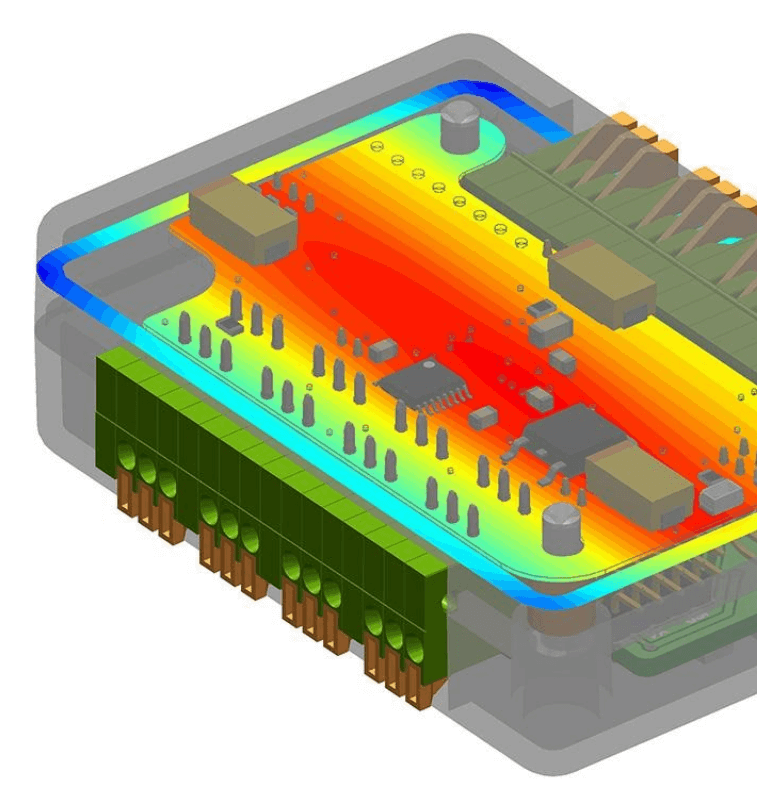
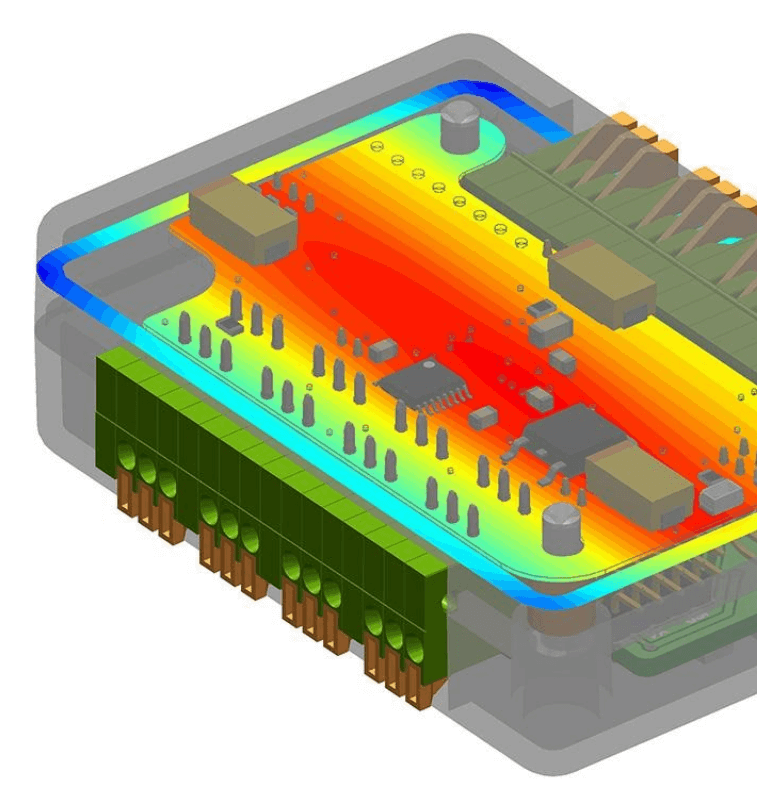
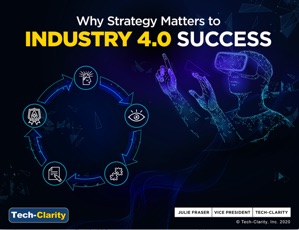
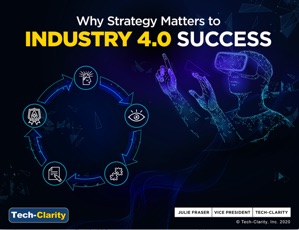
Table of Contents
- Making Industry 4.0 Pragmatic
- Industry 4.0 Transformative Benefits
- Making Industry 4.0 Approachable
- Why Disconnected Efforts are Insufficient
- Mindsets for Success
- Continuous Improvement for Industry 4.0
- Enterprise Needs
- Enterprise Technology
- Making it Scalable and Repeatable
- Build an Enterprise Industry 4.0 Approach
- Strategy to Accelerate Progress
Making Industry 4.0 Pragmatic
Small Steps Need Firm Ground in Strategy How can manufacturers take realistic steps to pursue Industry 4.0? The obvious answer is: get started with small projects. Yet, that may not be the best answer. Research shows that half of industrial internet of things (IIoT) projects are failing. It appears something is missing. According to research, that missing step is often setting an enterprise strategy for the transformation. Industry 4.0 is far broader than the manufacturing plant’s operations and processes. Every department plus the ecosystem of suppliers, distributors, and partners are involved. Only with an enterprise-level transformational strategy can manufacturers design, prioritize, and execute projects with assurance that they will build toward Industry 4.0. Companies must rely on what’s working, but also expand their view into the realm of what might be possible, even if it has not been to date.Strategy to Accelerate Progress
Foundation for the Future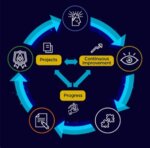
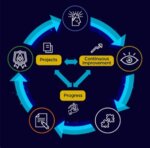
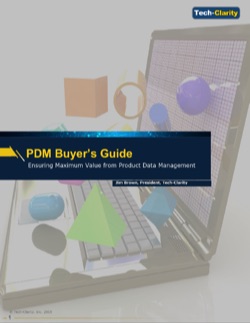
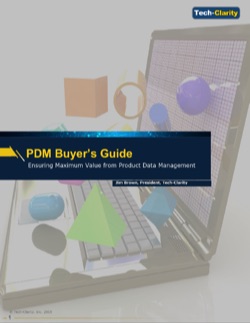
Table of Contents
- Introducing the PDM Buyer’s Guide
- The Product Data Management Imperative
- Analyze PDM Capabilities
- Assess Service Requirements
- Consider Vendor Requirements
- Identify Unique Company Needs
- Prepare for the Digital Enterprise
- Conclusion
- Recommendations
- About the Author
Introducing the Product Data Management Buyer’s Guide
Product Data Management (PDM) is an important tool to help manufacturers overcome the complexities of designing, developing, producing, and supporting today’s products and product development processes. Manual and ad-hoc approaches such as shared folders, Dropbox, and hard drives are simply not good solutions to manage critical, complex product information. These approaches may work for very small organizations, but quickly falter as organizations grow and must share information beyond a few core engineers. These techniques also fail to manage data relationships and complex file structures common to 3D CAD systems. PDM systems are purpose-built to address these issues. PDM is a structured, collaborative solution that helps manufacturers control, access, and share crucial product data. Selecting the right PDM system for your business has a large impact on productivity, product success, and profitability.- Getting files under control so people can find the right revision with confidence
- Making sure concurrent updates don’t overwrite each other to avoid “the last save wins” syndrome
- Making information easily accessible and consumable to teams outside of Engineering for reviews and downstream processes
- Safely sharing information with customers, partners, and the supply chain
- Ensuring intellectual property (IP) is captured and securely accessible regardless of who stored it
- Getting away from complicated shared drive structures that lead to errors
- Making sure people don’t manufacture or purchase against the wrong drawing
- Providing “one version of the truth” versus multiple copies of designs
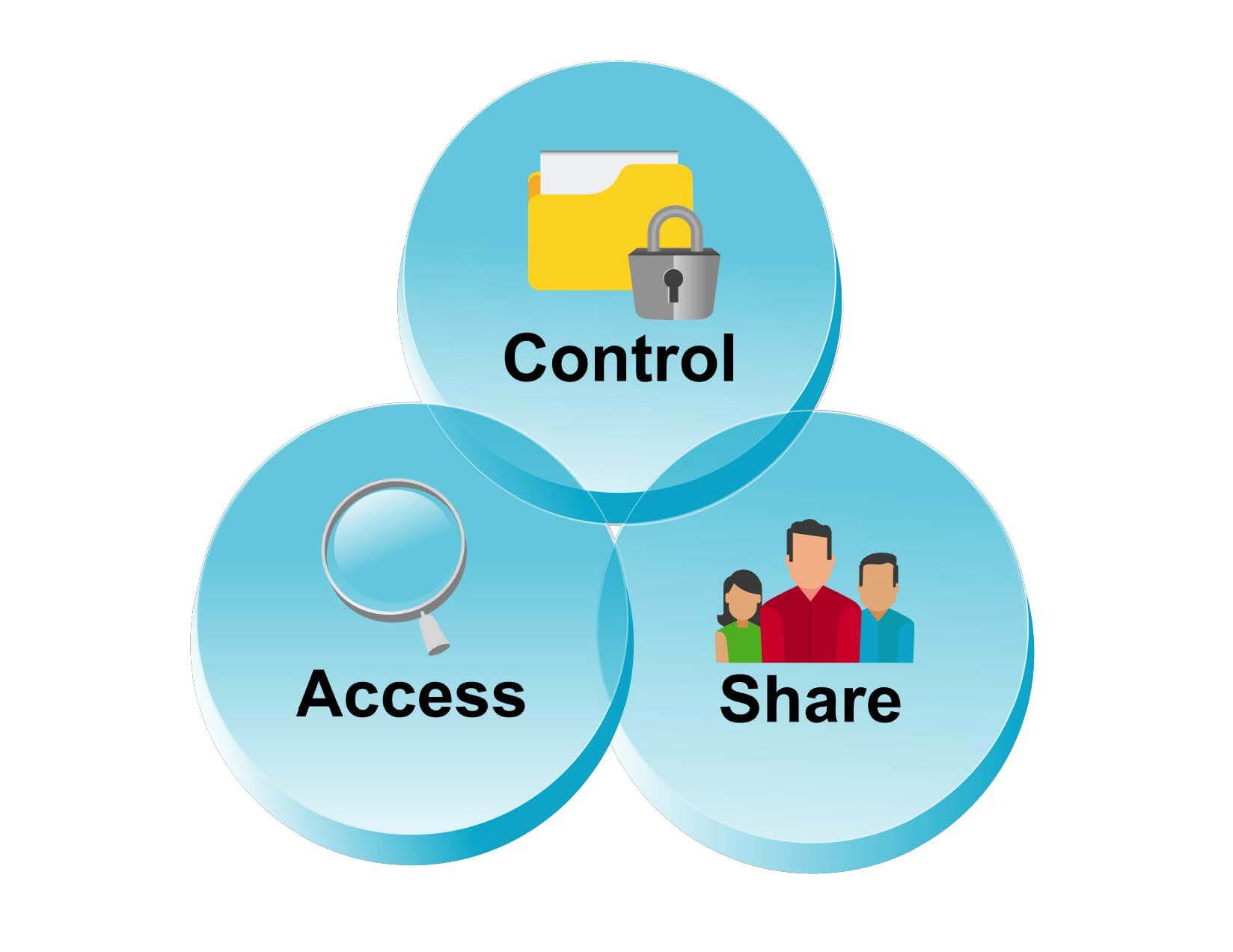
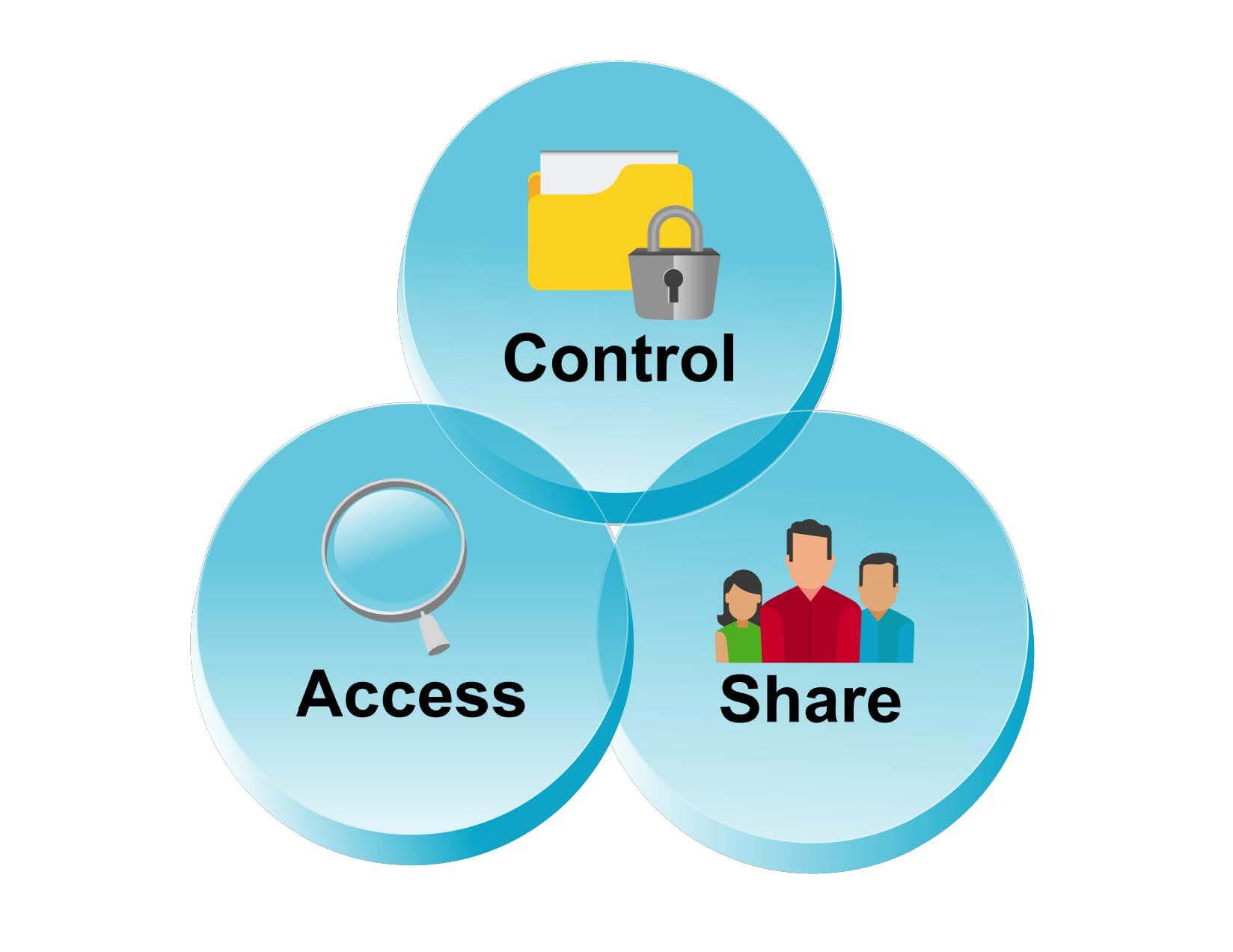
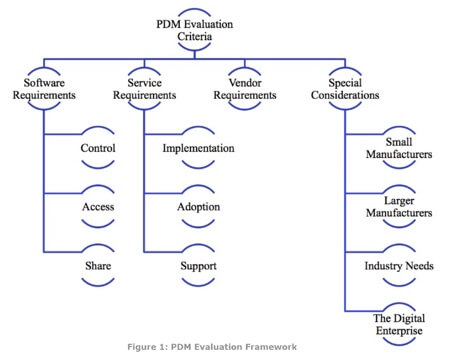
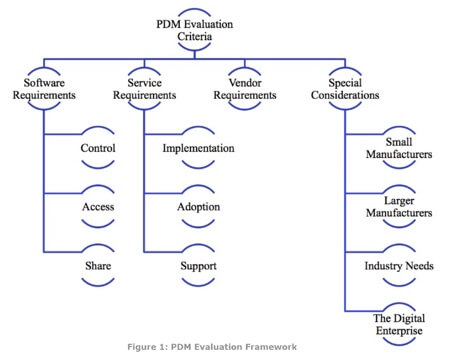
Conclusion
PDM helps manufacturers address market complexity and improve business performance. As Tech-Clarity’s Managing Engineering Data concludes, “Product data management is the fundamental building block of any engineering software strategy and helps companies get the most out of their precious engineering resources.” When evaluating PDM, manufacturers need to take into account:- Product requirements
- Implementation, adoption, and support requirements
- Vendor / business requirements
- Special requirements based on company size (particularly for very small or very large organizations)
- Special considerations to meet industry needs
- Future requirements as business continues to digitalize
Recommendations
Based on industry experience and research for this report, Tech-Clarity offers the following recommendations:- Identify and weigh PDM requirements based on company needs, company size, industry, and any unique company needs
- Use high level requirements such as the ones in this guide to evaluate solutions based on business fit before engaging in detailed evaluations
- Consider using more simple, commodity technical solutions like cloud or managed services solutions for smaller companies, companies that wish to move quickly, or those with limited IT resources
- Take user adoption into account, including simplified access and increased visualization for non-engineering resources
- Consider using more full-featured, scalable solutions for larger organizations that have more demanding process and scalability needs and can afford the IT resources required to support capabilities such as site synchronization
- Take into account long-term business and process growth needs including digitalization and IoT initiatives
- Consider the potential to expand to a more capable extended PDM or PLM system, but start small and get value along the way during implementation
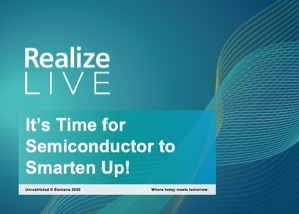
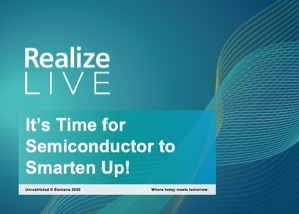
Key take-aways
Many new applications for semiconductors in the smart, connected world also lead to exceptional pressures on both fabs and backend operations. Julie will discuss a few of the concepts that many semiconductor companies have not yet leveraged to full advantage. In this session, you will hear how digital twin, modern comprehensive MES with integrated scheduling and quality, and advanced analytics can accelerate operations’ improvement efforts. [post_title] => Its Time for Semiconductor to Smarten Up! (presentation) [post_excerpt] => [post_status] => publish [comment_status] => open [ping_status] => open [post_password] => [post_name] => semiconductor-smarten-up-srl [to_ping] => [pinged] => [post_modified] => 2022-11-14 22:26:26 [post_modified_gmt] => 2022-11-15 03:26:26 [post_content_filtered] => [post_parent] => 0 [guid] => https://tech-clarity.com/?p=8976 [menu_order] => 0 [post_type] => post [post_mime_type] => [comment_count] => 0 [filter] => raw ) [6] => WP_Post Object ( [ID] => 8945 [post_author] => 2572 [post_date] => 2020-05-15 13:33:41 [post_date_gmt] => 2020-05-15 17:33:41 [post_content] =>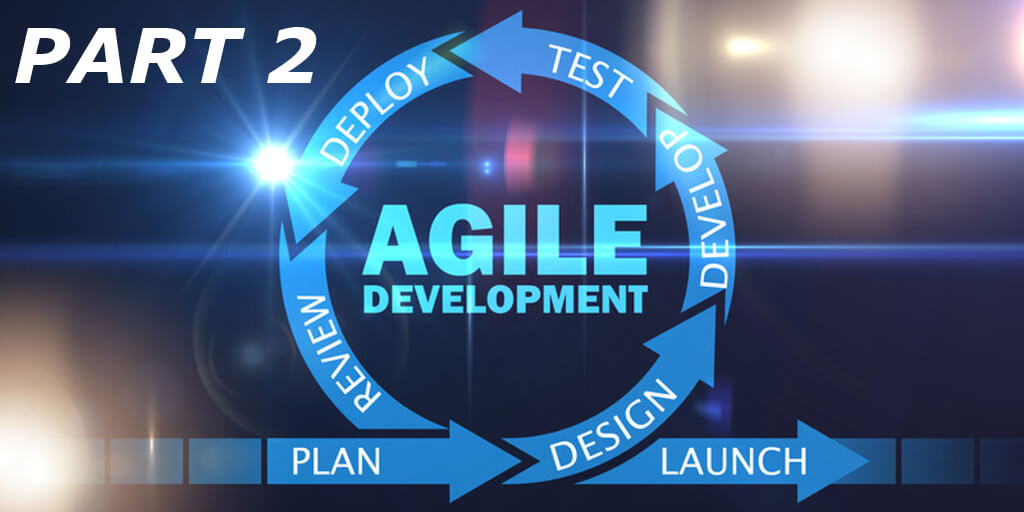
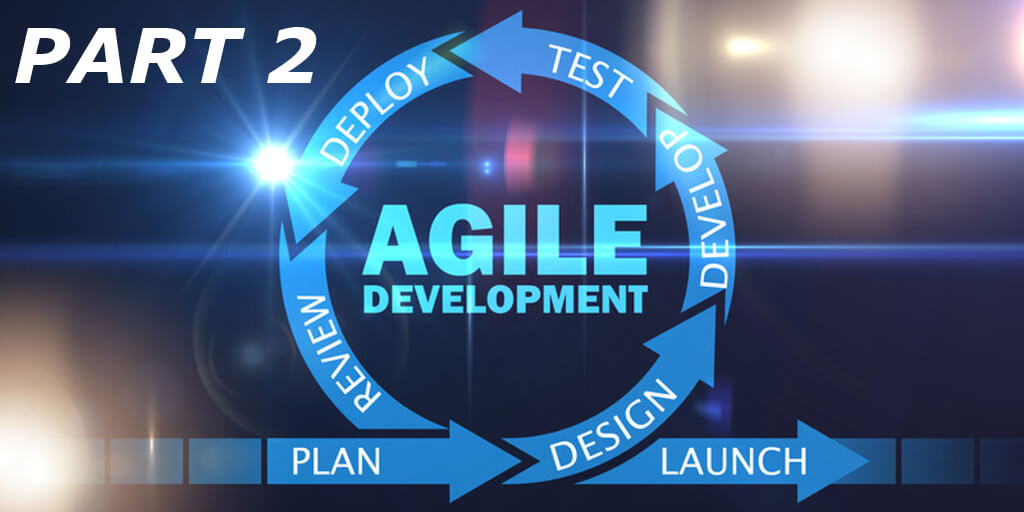
- Find Problems Sooner
- Tap into the Expertise of the Complete Team
- It Doesn’t Mean There Are No Requirements
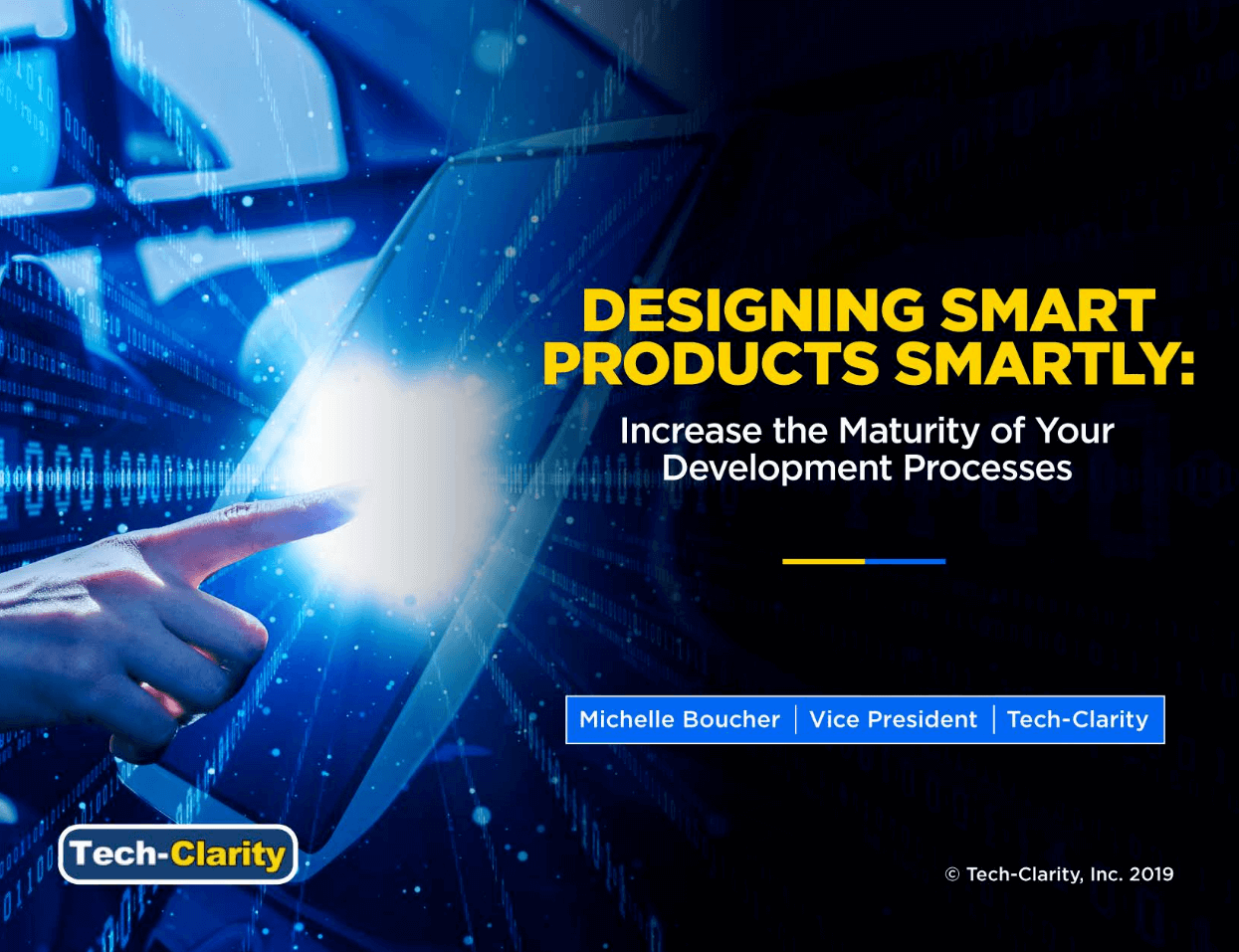
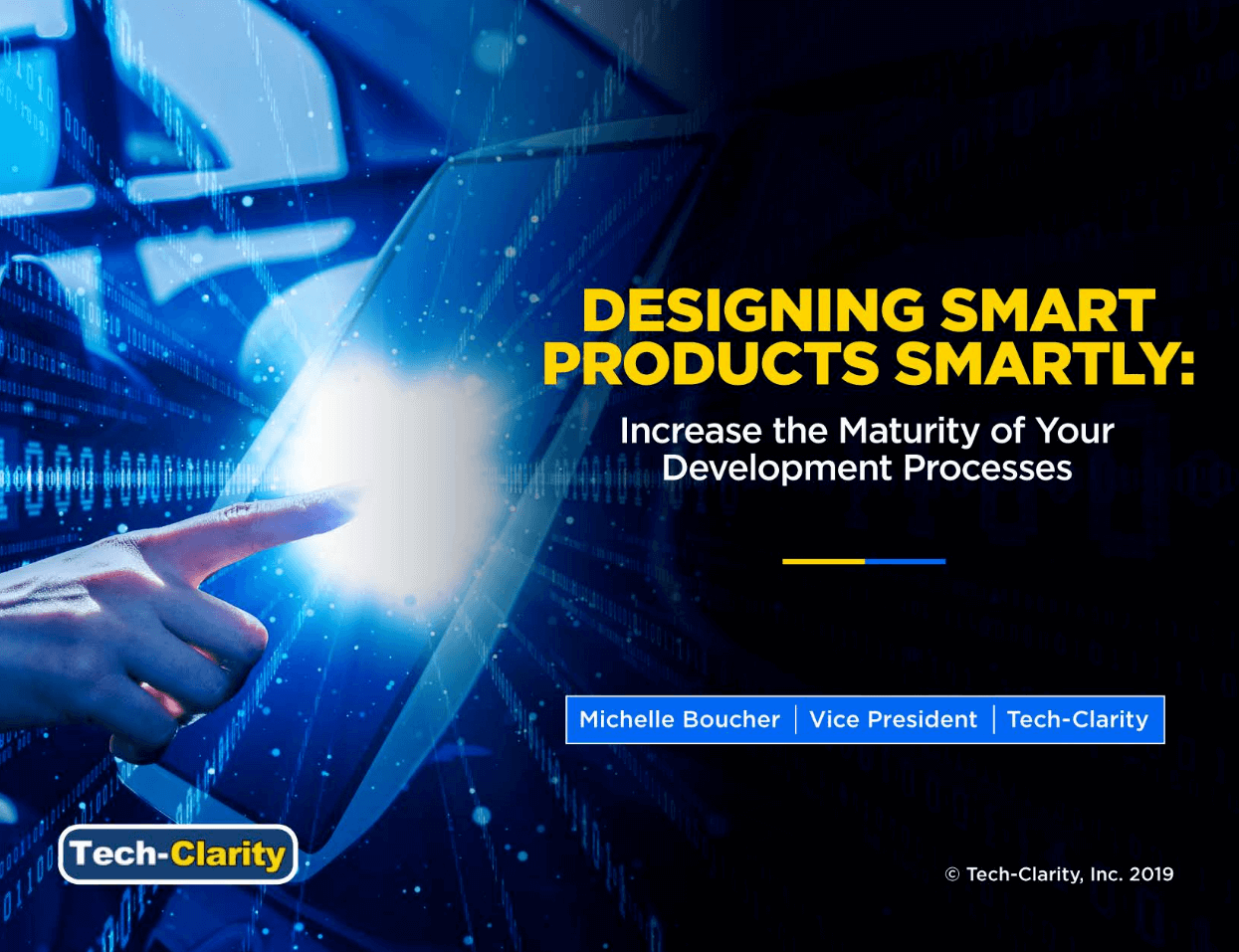
Table of Contents
- Improve Smart Product Development Maturity
- Define the Target
- Plan the Product
- Validate Early and Often
- Design by Discipline and Validate to Interfaces
- Effectively Manage Change
- Enable an Integrated Lifecycle View
- Conclusions and Recommendations
- Acknowledgment
Improve Smart Product Development Maturity
The Opportunities for Smart Products Customers in nearly every industry find smart products compelling. It’s hard to compete with a car that drives and parks itself or a clothes washer that senses and adjusts to water conditions, fabric types, and dirt levels and schedules service when needed. Likewise, a medical device that monitors patient health and notifies a doctor when needed offers significant value. Benefits will increase even further as smart products become more aware and communicative as companies adopt strategies to support the Internet of Things (IoT) and technologies like 5G create even more opportunity for connectivity.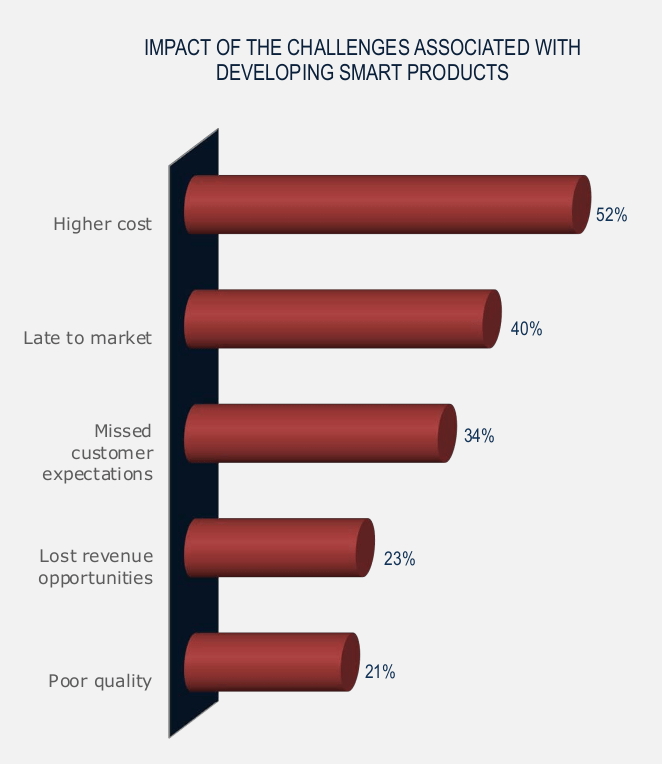
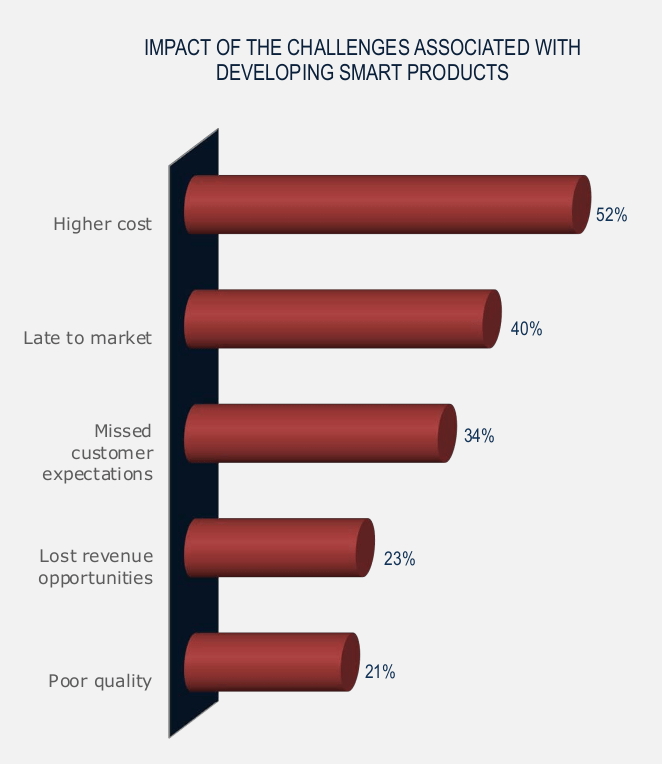
Conclusions
Create a Competitive Advantage To beat competitors with smart innovations, companies must raise the maturity of their development processes and tools. This report suggests best practices for requirements management, systems design, simulation, interface management, and change management. There are others as well, but these processes are proven and can provide significant value today.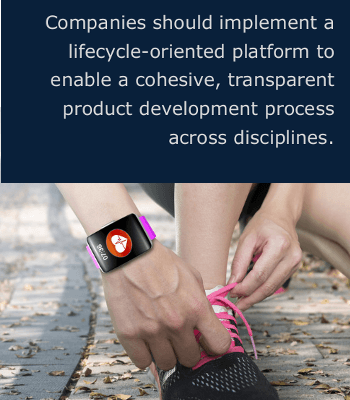
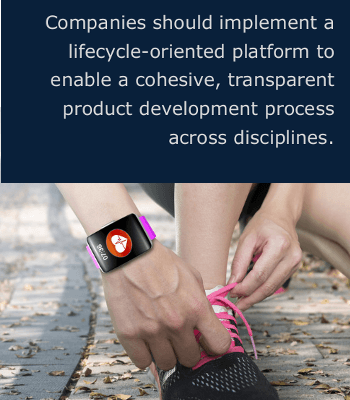
Recommendations
Based on industry experience and research for this report, Tech-Clarity offers the following recommendations:- Follow proven best practices for developing smart products:
- Create a single source of truth for requirements
- Plan the product starting with architecture and develop a system model
- Use multi-physics simulation early and often at both the system and component level to optimize and validate the design
- Develop a common product definition with interfaces
- Manage change by starting with an impact analysis across all disciplines
- Leverage product innovation platforms to create an integrated lifecycle view
- Implement the right tools to enable design, including simulation and systems design tools
- Leverage lifecycle-oriented systems to integrate the various processes, people, and deliverables required to efficiently develop high quality, smart products.
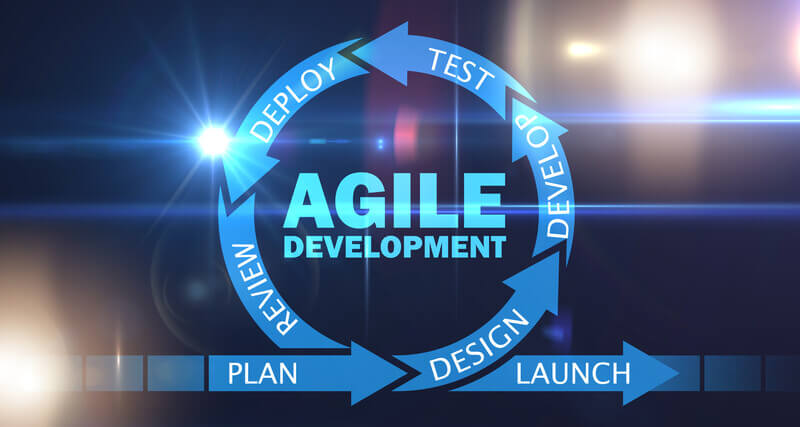
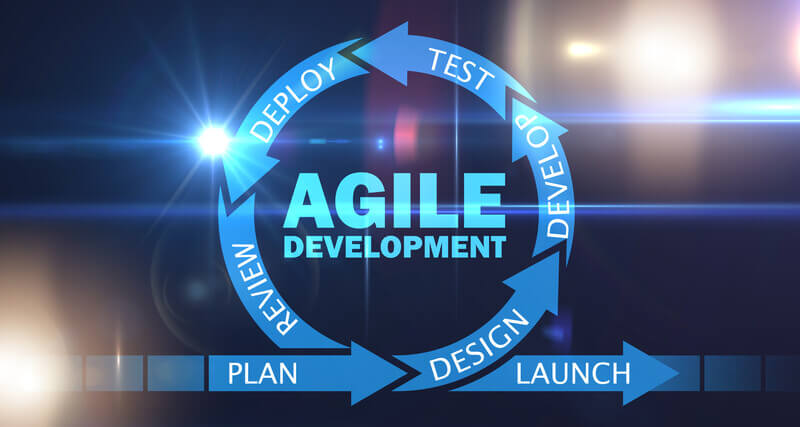
- Support Evolving Requirements
- Meet Customer Needs
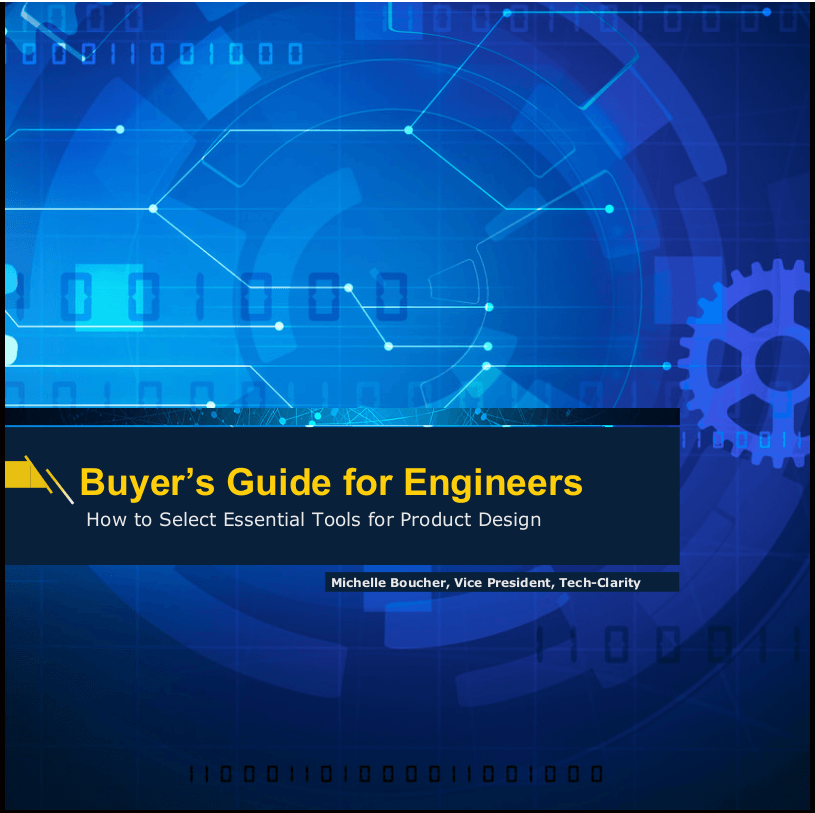
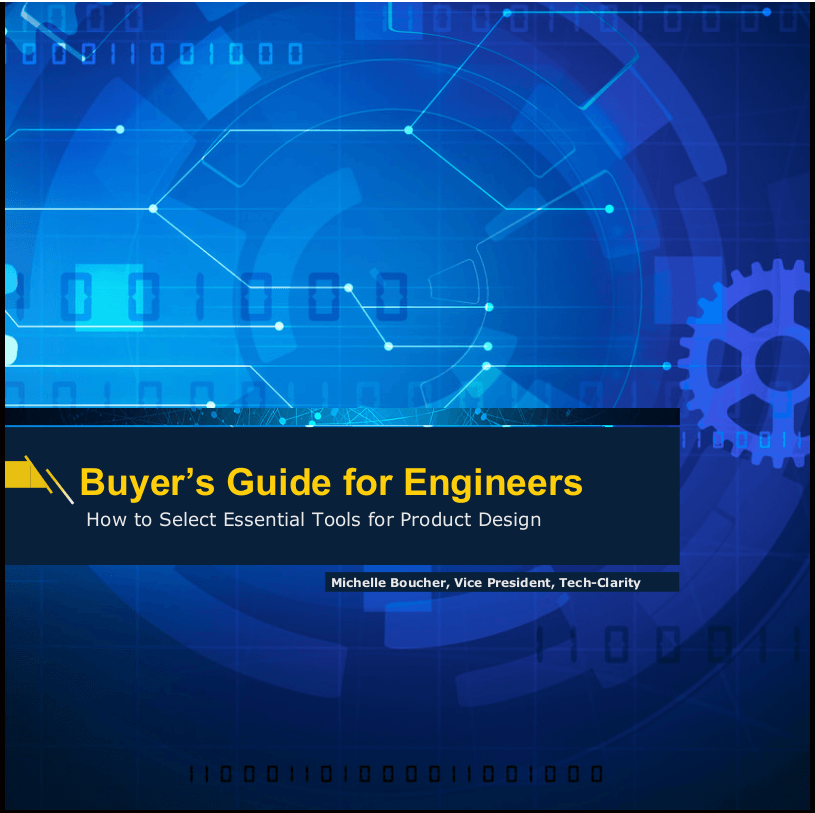
TABLE OF CONTENTS
- Executive Overview
- The Business Value of Investing in Engineering
- Support End-to-End Processes with an Integrated Solution
- Mechanical Design
- Electrical and Electronic Design
- Simulation
- Manufacturing
- Technical Publications
- Design Data Management
- Service Requirements
- Vendor Requirements
- Identify Unique Company Needs
- Conclusion
- Recommendations
- About the Author
- Acknowledgments
Executive Overview
Global competition, including low-cost providers, makes it hard to compete in today’s market. It is impossible to compete on price when competitors come from geographic regions with low employment costs. Consequently, companies must compete in other ways, such as with better, high quality products, more personalization, improved services, greater innovation, or lower cost of ownership. Achieving this requires improving efficiency, catching problems sooner, and making better decisions to lower product development costs and increase product quality. Consequently, teams must be agile enough to quickly respond to market shifts and customer demands. Products have to get to market as fast as possible to maximize the window of opportunity before low-cost providers can undercut prices with competing offerings.The Value of Digitalization
Efficiencies achieved through digitalization accelerate the development process and improve quality by creating a digital thread across the entire product development cycle. As a result, all information stays up to date, changes are propagated, and there is less risk of errors. However, it can be hard to know where to start, especially for a small or mid-size company. Smaller companies share many of the same challenges as larger companies, but lack the budget of a big OEM. The right software solution can help, but it must have the right capabilities, at an affordable price that will be manageable for a small company.Selecting the Right Solution
With so much to consider, how do you choose the right software solution to support your product life-cycle? This buyer’s guide serves as a guide to help you pick the right solution for your company. This guide covers requirements for a complete integrated product development suite. It has four major sections covering software functionality, service requirements, vendor attributes, and unique company considerations (Figure 1). Each section includes a checklist of key requirements to investigate when selecting software tools. This guide is not an all-encompassing requirements list. It provides a high-level overview.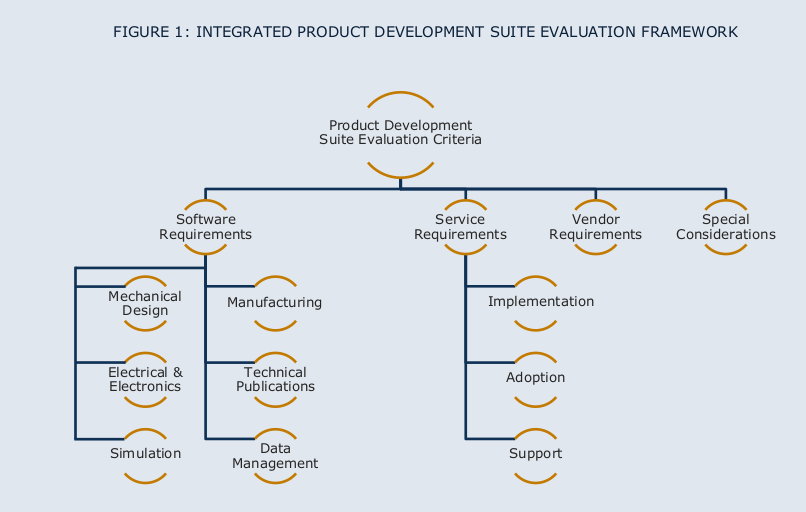
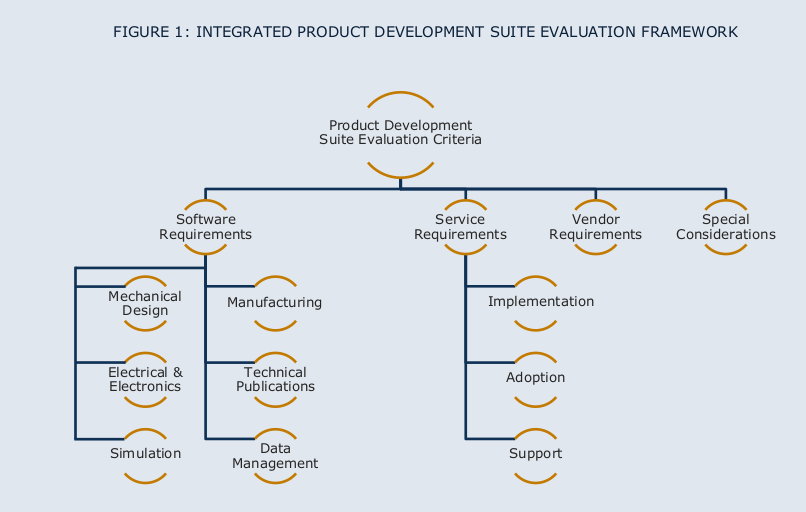
RECOMMENDATIONS
Based on industry experience and research for this report, Tech-Clarity offers the following recommendations: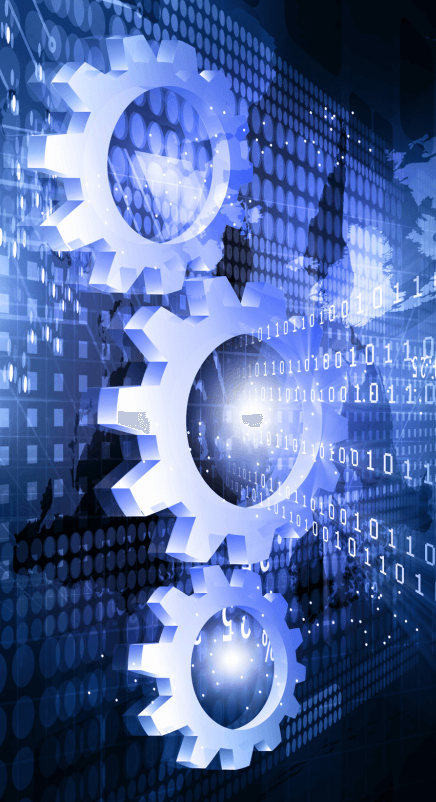
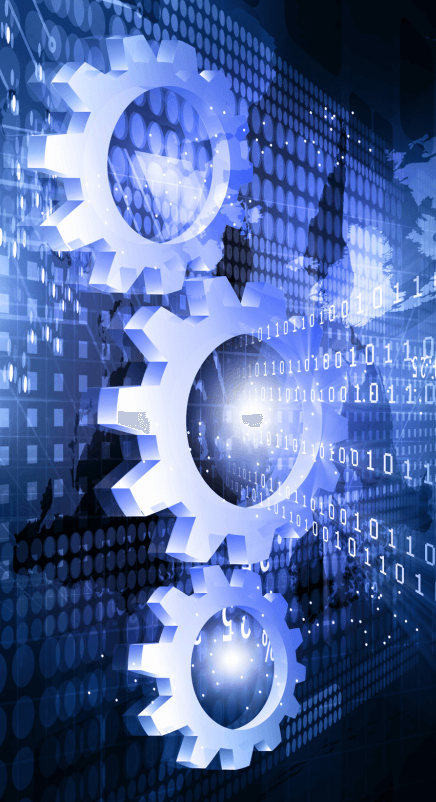
- Create a digital thread across your development process with an end-to-end integrated product development suite
- Consider solutions that support mechanical design, electrical design, simulation, manufacturing, technical publications, and design data management.
- Ensure you have traceability across the entire lifecycle of your product
- Do not compromise on ease of use
- Support collaboration across the development lifecycle
- Work off a single high-fidelity model to support your digitalization strategy and create a single source of truth
- Ensure your solution will have the support behind it to make it a success at your company.
- Select a vendor who will be a good partner.
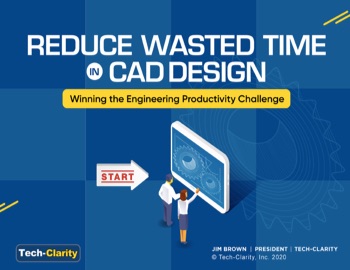
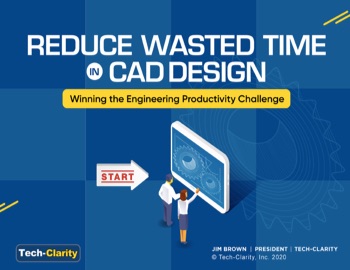
Table of Contents
- Reducing Non-Value-Added Time in CAD Design
- Engineers Don’t Have Time to Waste
- Time Waster 1 - Can’t Find and Reuse Data
- Time Waster 2 – Lost CAD Designs
- Time Waster 3 – Preparing Data for Others
- Time Waster 4 – Managing Complexity
- Time Waster 5 – Managing Change
- Conclusions and Next Steps
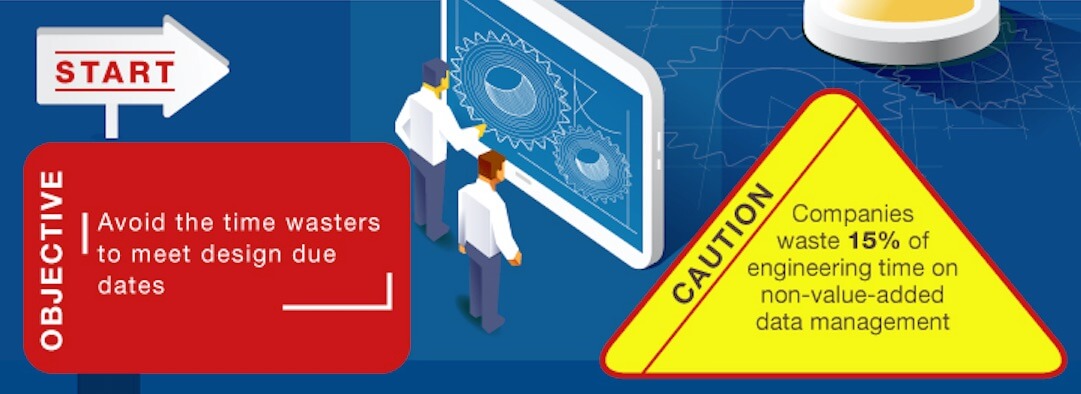
Engineers Don't Have Time to Waste
Too Much Spent Time on Non-Value-Added Data Management Product and product development complexity have increased while time-to-market goals have become more aggressive. The combination of these two trends puts a significant squeeze on the time available for engineers and designers to design and document their inventions. Unfortunately, companies waste an average of 15% of their engineers’ time on non-value-added data management tasks. Almost one-third of these companies spend over 25% of their engineers’ time this way. That’s one out of every four days wasted on data management efforts that could be better spent innovating. Design Data Management Maturity Relieves the Pressure What if companies could give that wasted time back to their technical personnel? That’s exactly what leading companies do. Our research shows that Top Performing companies – those that are better able to quickly and efficiently design high quality, innovative products – spend 25% less time on nonproductive data management tasks. What enables these companies to perform better than their competitors? These leaders are more likely to have adopted more mature data management capabilities1 and use more structured, collaborative data management solutions including Product Data Management (PDM) and Product Lifecycle Management (PLM). Let’s take a look at how these solutions help engineers avoid wasting precious design time by allowing them to control, access, and share design data.Conclusions and Next Steps
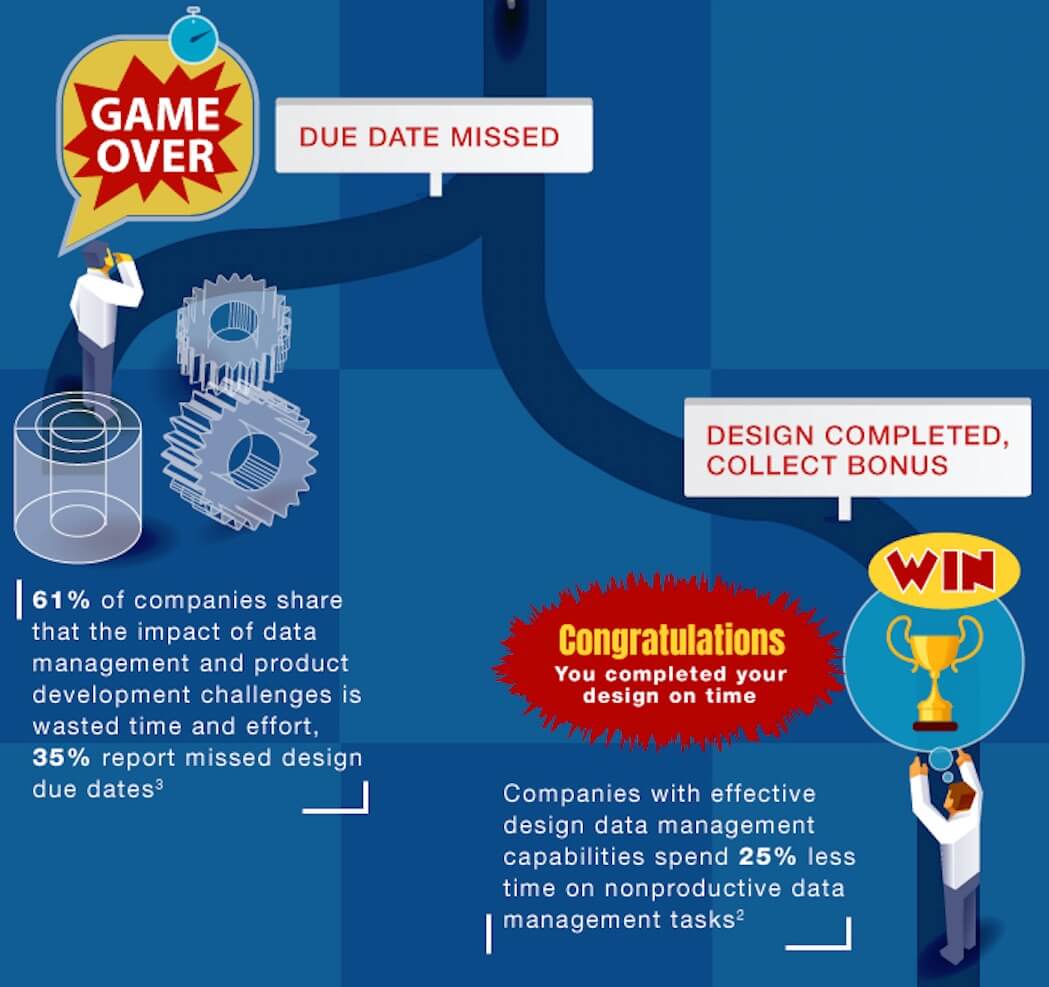
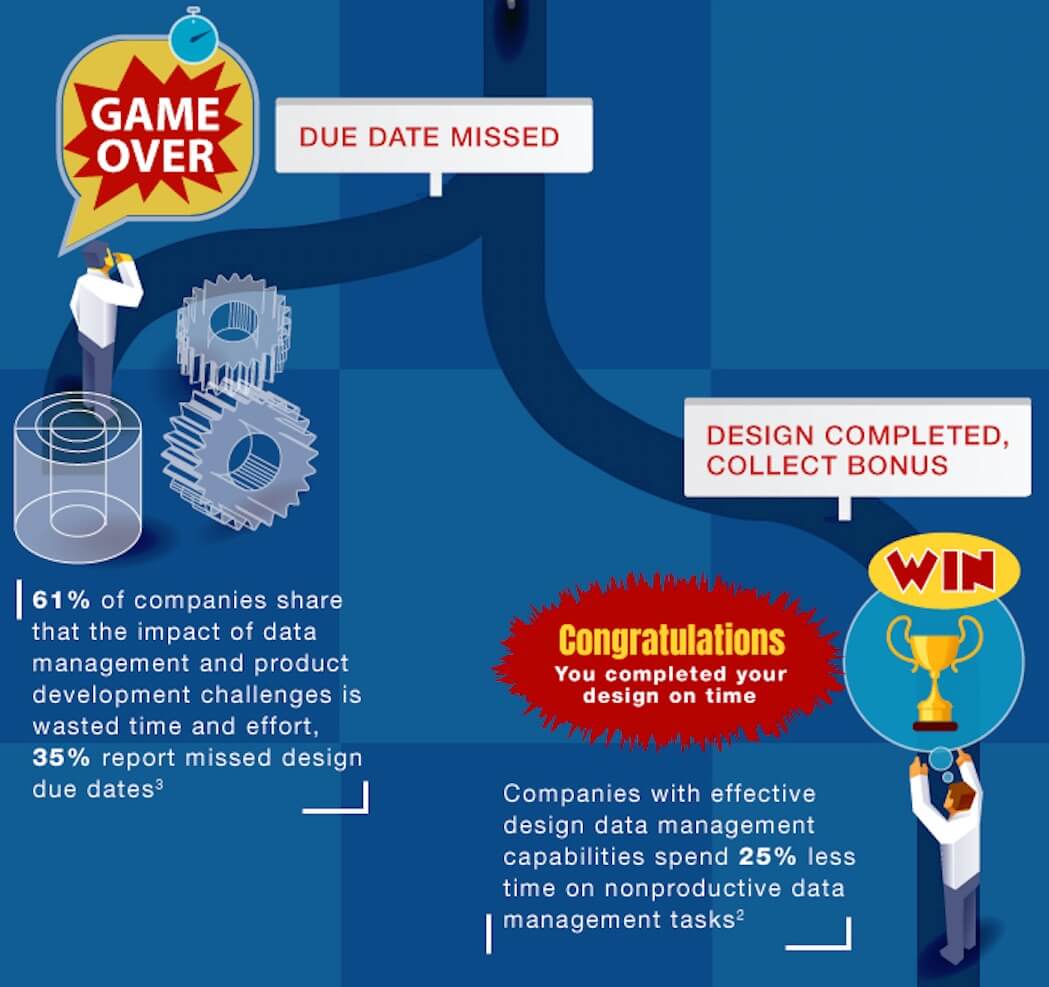
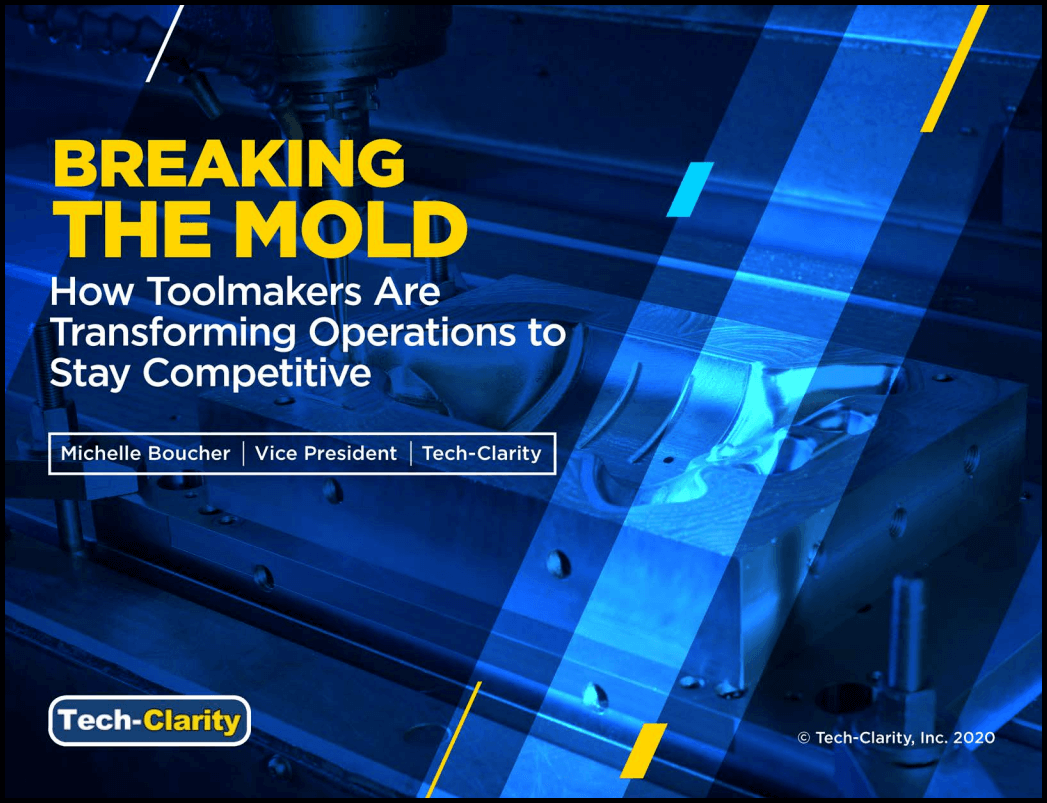
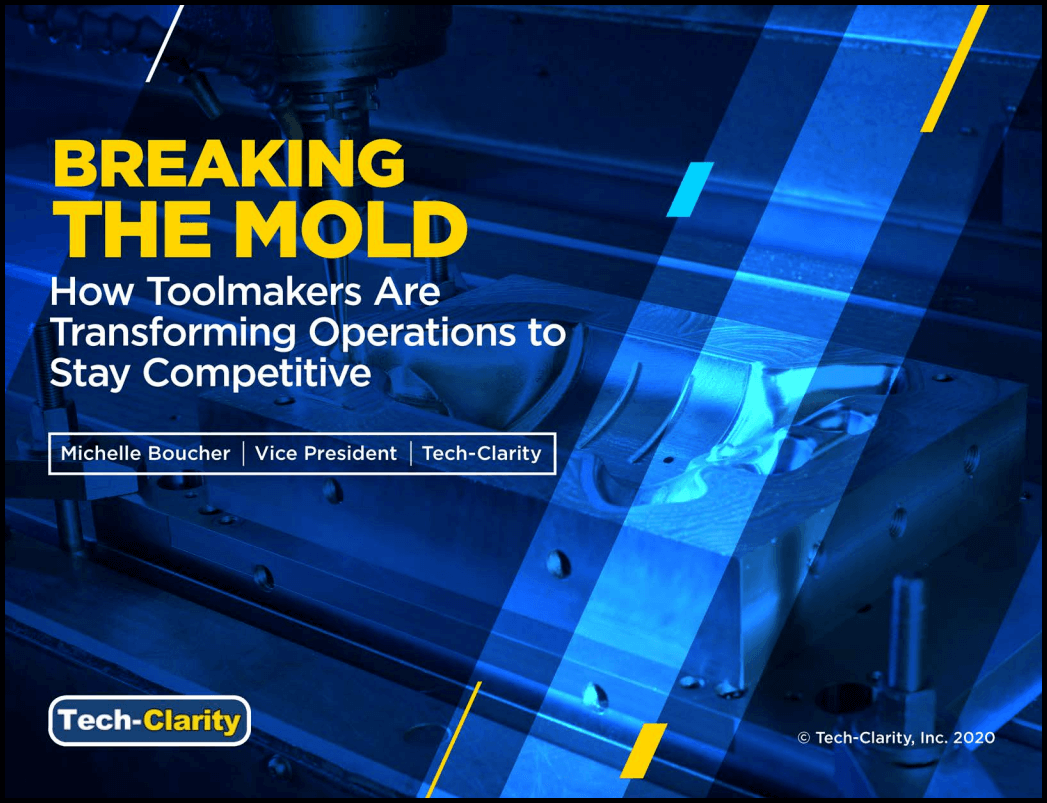
TABLE OF CONTENTS
- What It Takes to Be Competitive
- Challenges that Hold Mold Makers Back
- Identifying Best Practices
- Strategies to Overcome the Challenges
- Challenges with the End-to-End Process
- Supporting the End-to-End Process
- Streamline Bidding
- Support Collaboration During Tool Design
- Ensure Quality by Verifying Manufacturability
- Optimize Cycle Time
- Automate Production Planning
- Support Quality Verification Processes
- Use an Integrated Solution
- Looking to the Future
- Recommendations and Conclusions
- About the Research
- Acknowledgments
What It Takes to Be Competitive
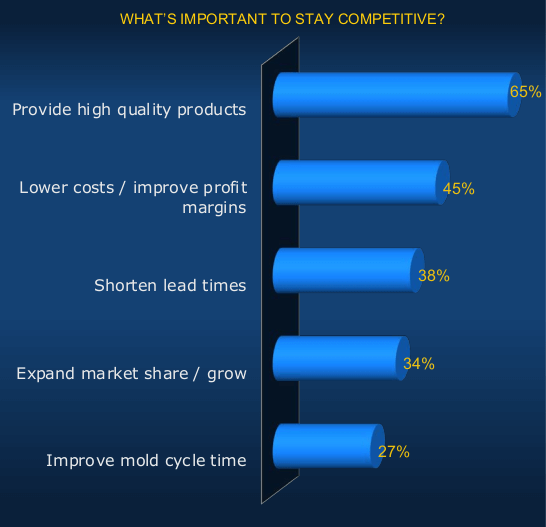
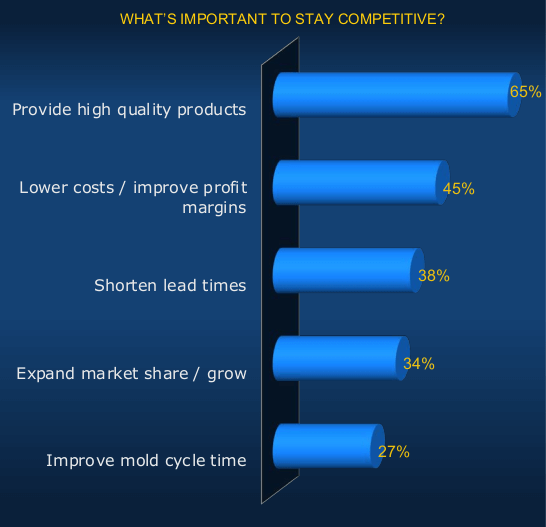
Conclusions
The Opportunity for Mold Makers Mold makers need to keep customers happy to stay competitive. Consequently, they need to ensure the quality of the mold, the parts it produces, manage costs, and meet delivery dates. Unfortunately, several challenges make meeting their objectives difficult. Global competition is fierce, skilled workers are hard to find, and margins continue to thin. To overcome this, Top Performing mold makers support an end-to-end process with better collaboration and improved hand-offs between the different phases of the group. When looking at the end-to-end process, most toolmakers struggle with process bottlenecks and managing changes. By creating a digital thread across the entire process, there is traceability across the complete life-cycle. Design details can then be reused from one phase to the next, saving time by avoiding duplication of efforts, improving quality by reducing risks for introducing human error, and saving costs by catching problems sooner.Recommendations
Recommendations and Next Steps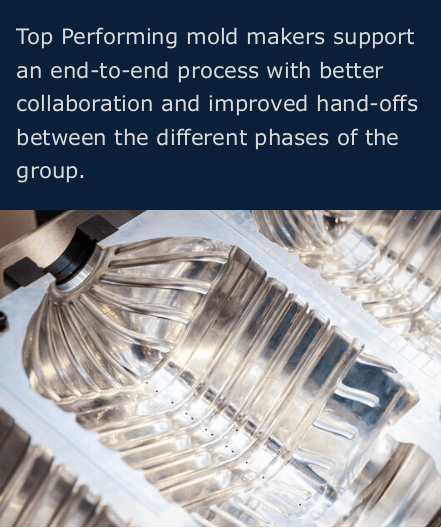
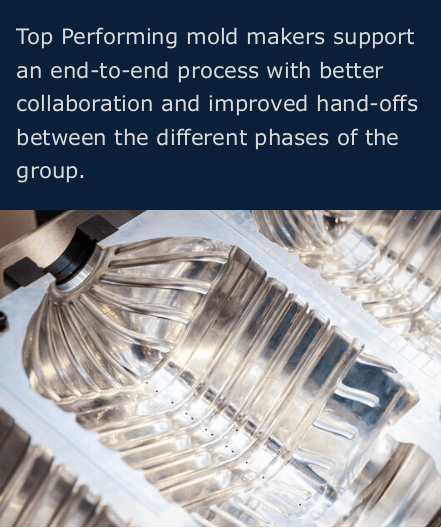
- Streamline bidding
- Support collaboration during tool design
- Ensure quality by verifying manufacturability
- Optimize cycle time
- Automate production planning
- Support quality verification processes
- An integrated platform can help
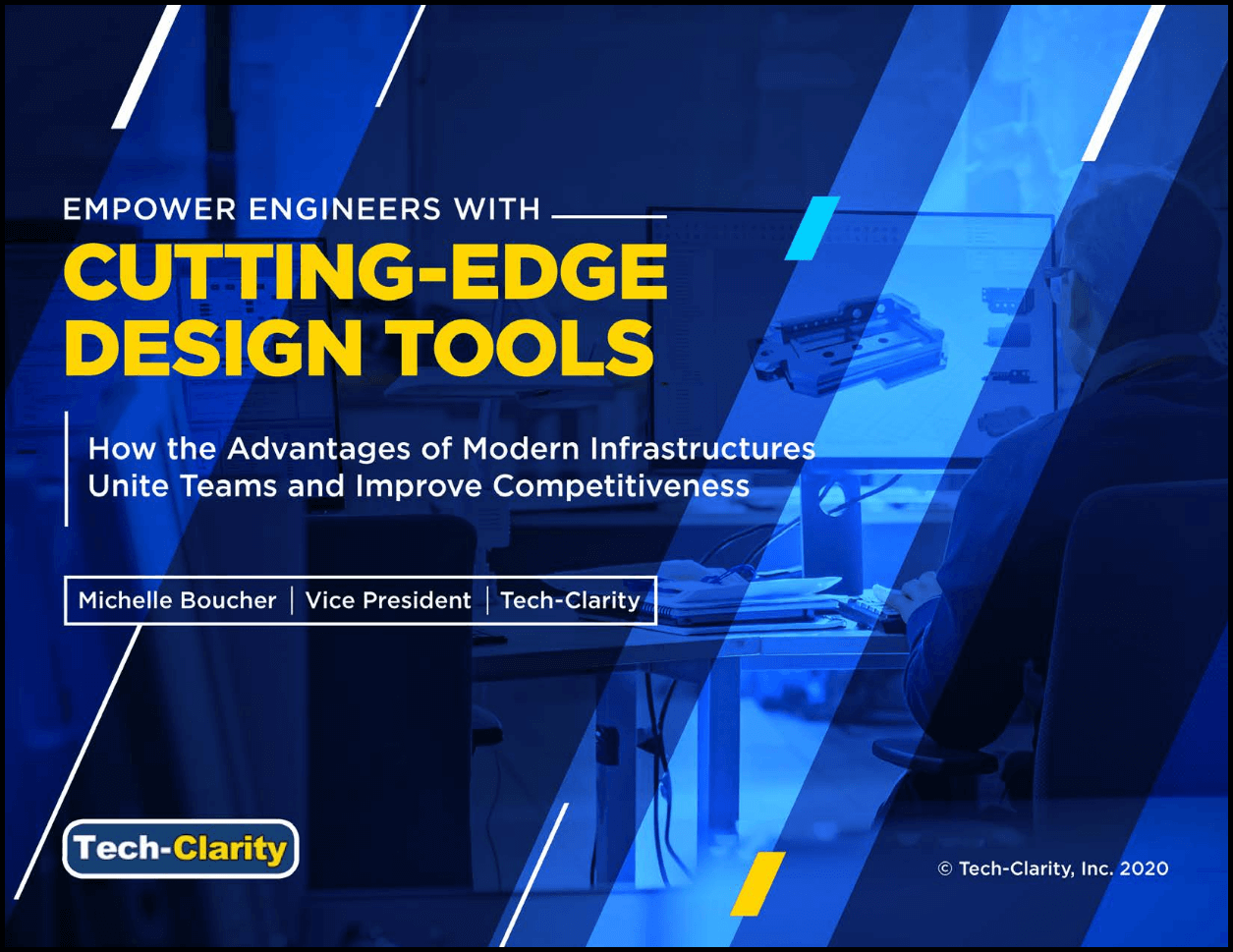
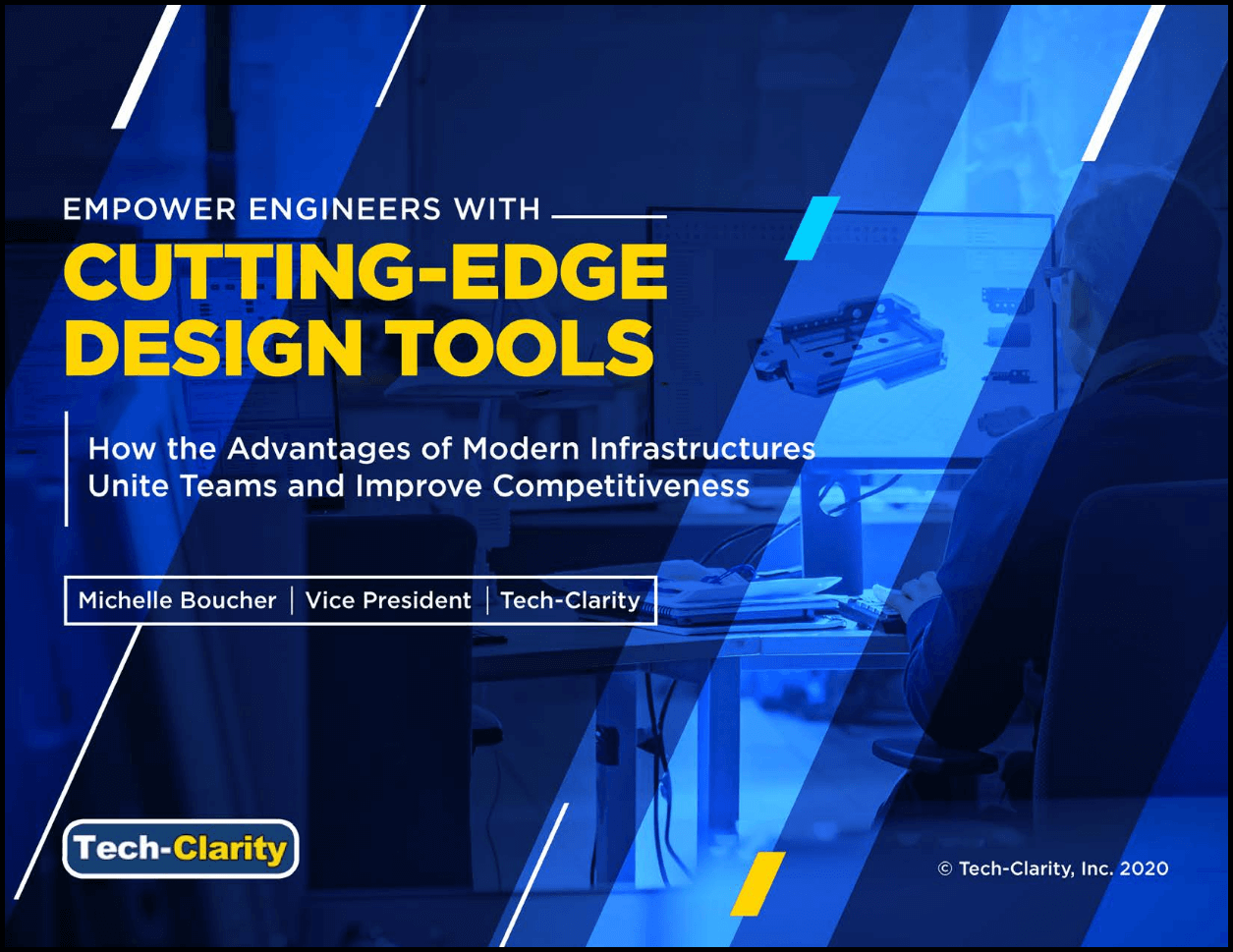
TABLE OF CONTENTS
- The Reality of Today’s Product Development Environment
- Understand Collaboration Needs
- Silos Create a Barrier to Collaboration
- Understand Bottlenecks
- Impact of Bottlenecks
- Explore Solutions to Overcome Bottlenecks
- Use Technology to Solve the Problem
- CAD on the Cloud
- Do Not Underestimate Security Concerns with Existing Infrastructure
- Conclusions
- Recommendations
- About the Research
- Acknowledgments
The Reality of Today’s Product Development Environment
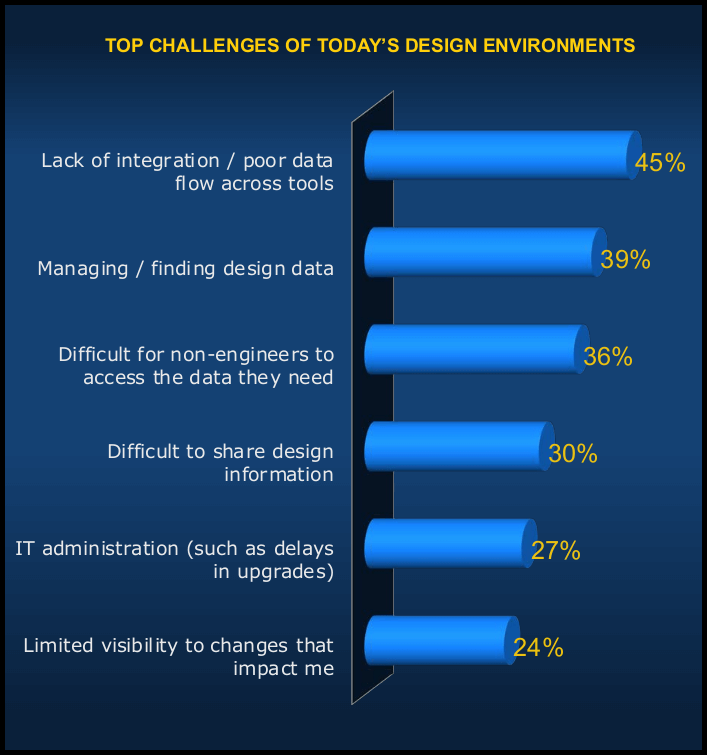
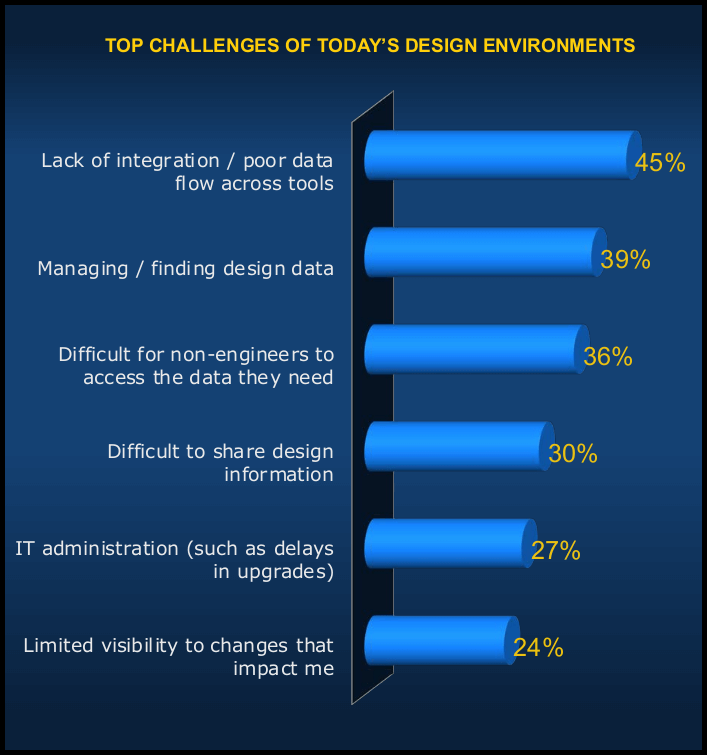
RECOMMENDATIONS
Next Steps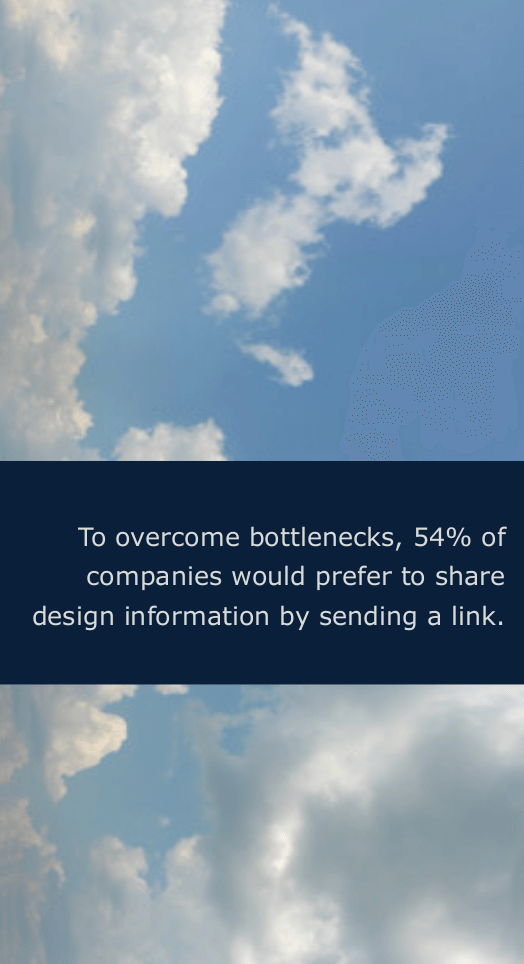
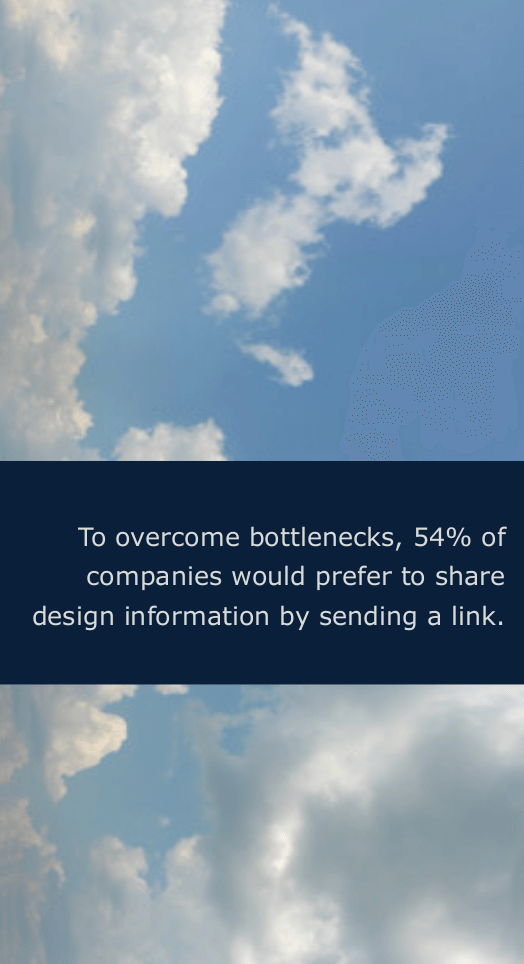
- Invest in product development to improve competitiveness and boost profitability.
- Understand how challenges in the design environment contribute to collaboration challenges and bottlenecks.
- Do not underestimate the business cost of collaboration challenges.
- Consider options that allow design data to be shared via a web browser and on any device as a way to improve collaboration.
- Consider a CAD solution on the cloud as a way to overcome design bottlenecks and improve collaboration.
- Do not underestimate security risks in your existing infrastructure. A cloud solution may offer greater security protection.
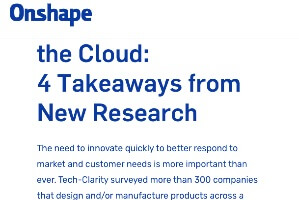
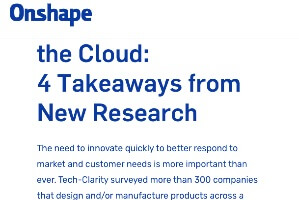
Webcast Announcement
The Cloud: 4 Takeaways from New Research The need to innovate quickly to better respond to market and customer needs is more important than ever. Tech-Clarity surveyed more than 300 companies that design and/or manufacture products across a wide range of industries to find out how the cloud can help manufacturers improve their product development to drive higher levels of profitability. In this webinar, you will learn how cloud-native tools enable companies to reduce time wastage and production delays caused by product development challenges. Tech-Clarity’s research lead and an Onshape co-founder will provide some commentary and expand on the more surprising results. [post_title] => Faster Product Development on the Cloud (webcast) [post_excerpt] => [post_status] => publish [comment_status] => open [ping_status] => open [post_password] => [post_name] => faster-product-development [to_ping] => [pinged] => [post_modified] => 2022-11-14 22:27:01 [post_modified_gmt] => 2022-11-15 03:27:01 [post_content_filtered] => [post_parent] => 0 [guid] => https://tech-clarity.com/?p=8812 [menu_order] => 0 [post_type] => post [post_mime_type] => [comment_count] => 0 [filter] => raw ) [14] => WP_Post Object ( [ID] => 8776 [post_author] => 2572 [post_date] => 2020-04-21 11:30:19 [post_date_gmt] => 2020-04-21 15:30:19 [post_content] =>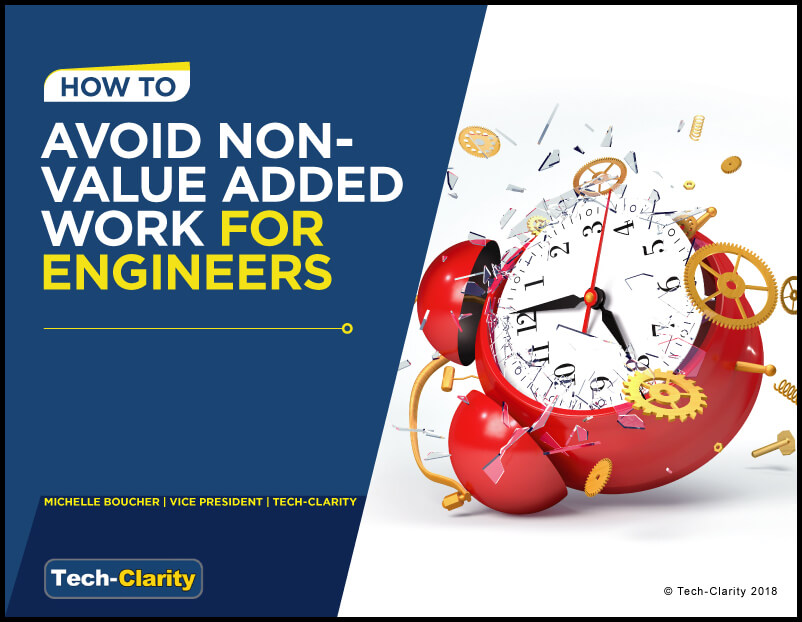
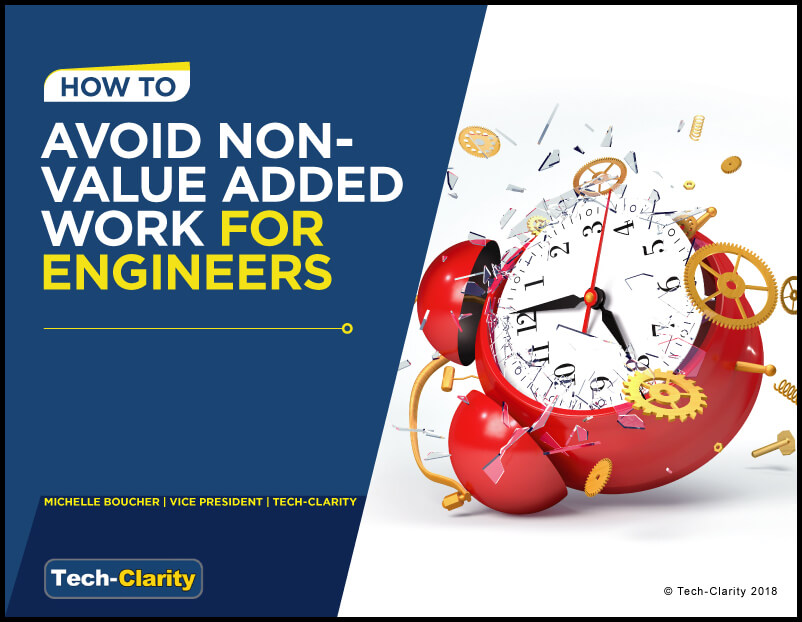
TABLE OF CONTENTS
- Identify Bottlenecks
- Assess Non-Value Added Time
- Business Value of Eliminating Non-Value Added Work
- Recognize the Time Required for Check-ins
- Outdated Information Impacts Engineering Changes
- The Impact of Outdated Information on Collaboration
- Identifying the Top Performers
- Technology As a Collaboration Solution
- Consider the Security Risks of Email
- The Benefits of Real-Time Data Updates
- Recommendations
- About the Research
Executive Overview
Engineering Is Key to Competitive Differentiation Today's market is so competitive; it is hard to stand out. To be successful companies must empower their engineering teams to differentiate products on innovation, quality, performance, and cost. While balancing all those criteria can be a challenge, it is made even harder as engineers report they waste a third of their time on non-value added work. Even worse, 20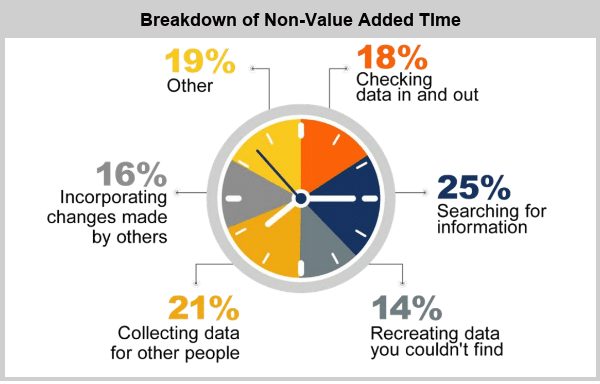
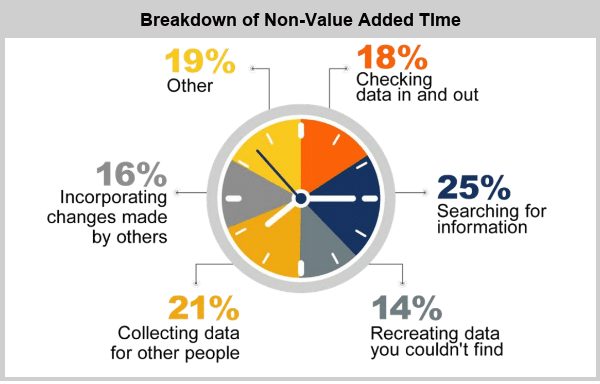
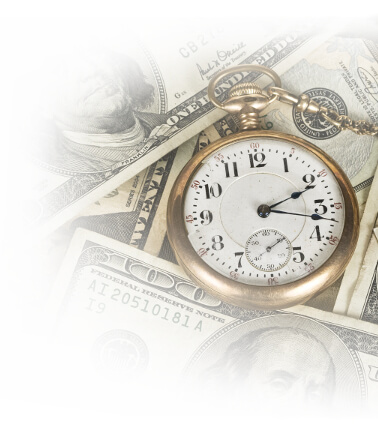
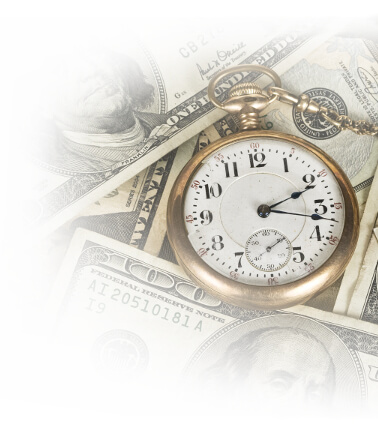
RECOMMENDATIONS
Next Steps Based on industry experience and research for this report, Tech-Clarity offers the following recommendations:- Understand how engineers spend their time and improve processes to minimize time wasted on non-value added work
- Consider solutions such as PLM or PDM to centralize design information and support change management and collaboration
- Evaluate options to design in the context of the assembly to improve collaboration and understand the impact of changes
- Consider real-time updates to keep CAD data up-to-date while minimizing or eliminating check-in times
- Establish means for secure, real-time collaboration with third parties to minimize delays in getting updated CAD data from them
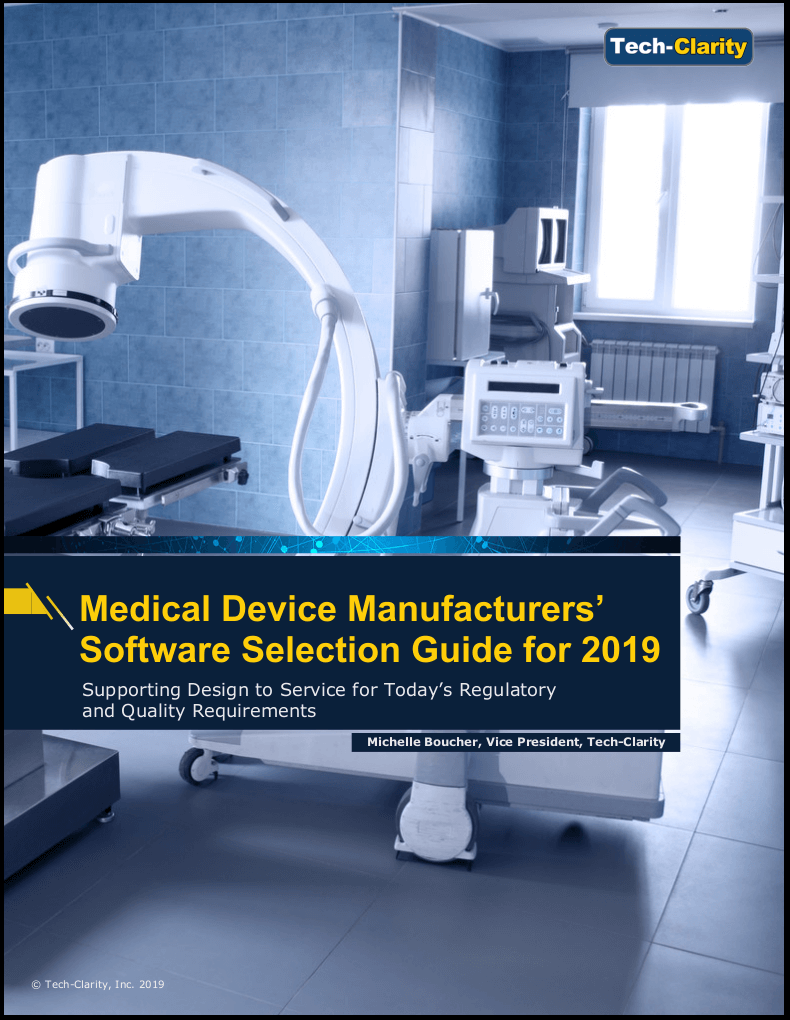
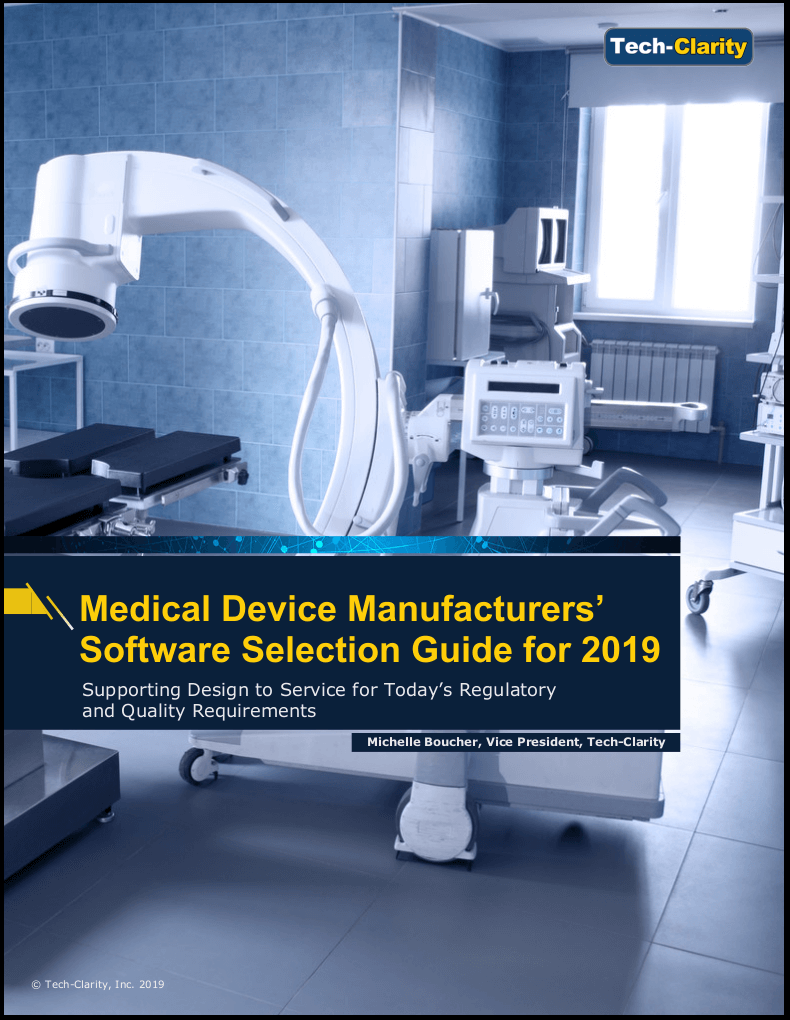
- Software capabilities
- Implementation
- User adoption
- Support
- Vendor characteristics / attributes
- Unique business needs
TABLE OF CONTENTS
- Executive Overview
- Identify Your Challenges
- Transition from Document Centric to Product Centric
- Consider the Complete Lifecycle
- Manage the Product
- Manage Requirements (Customer Needs to Regulatory)
- Support Product Development for Hardware
- Support Software Development
- Enable Smart and Connected Products
- Ensure Regulatory Compliance
- Support Quality Management
- Plan for Manufacturing
- Control Suppliers
- Plan for Service
- Assess Implementation Requirements
- Consider Vendor Attributes
- Identify Specific Needs for your Company
- Conclusion
- Recommendations
- About the Author
- About the Research
- Acknowledgments
Executive Overview
The Opportunity for Medical Device Companies It’s an interesting time for medical device companies. Initiatives such as the FDA’s Case for Quality and new regulations like the European Union Medical Design Regulation (EU MDR) are shifting the traditional focus of regulatory compliance from a documentation driven approach to one that requires a greater focus on device quality and effectiveness. As discussed in Tech-Clarity’s Preparing for EU MDR – Product Submissions: A Sustainable Approach, while the changes may be challenging in the short term, in the end they can also create opportunity through more efficient processes that result in better devices and improved patient outcomes. In many cases, medical device companies will need to adopt new approaches. These new approaches may be an adjustment, but medical device companies that implement the right technology to support these new methods should find themselves at an advantage. The challenge is figuring out which technology to select. Let’s start with the fundamental goal for medical device companies. They are in the business of making people’s lives better. As Joel Hembrock, Senior Designer and CAD Administrator at Medtronic says, “Our patients are the people who benefit from our products. Restoring life is our main focus. [We want] to be giving people their lives back, restoring their health, allowing them to actually live again and not have their disease or any other ailment keep them from being able to live.” Technology advancements have opened up new and exciting opportunities that have the potential to further this mission. On top of this, an aging Baby Boomer population will create additional demand for medical devices. Consequently, the industry should see significant growth. In fact, the Evaluate MedTech World Preview 2018, Outlook to 2024 [1] report forecasts a 5.6% growth rate every year for the next five years. There Are Challenges to Overcome However, it will be the companies who can overcome the unique challenges in the industry who will be best positioned to take advantage of this growth. With lives at stake, patient safety is of the utmost importance. As such, the industry faces heavy regulations. Compliance is so critical that if medical device companies do not adhere to FDA, EU and other worldwide standards and regulations, they will not be profitable. However, so much time, effort, and cost go into compliance documentation; it takes resources away from innovating and ensuring high quality products. As a result, it is harder to take advantage of opportunities that will boost profitability. On the other hand, medical device companies who adopt practices focused on high quality devices can expect greater patient satisfaction, improved competitiveness, and higher profits. In fact, McKinsey estimates that firms who embrace quality focused best practices can increase profits by 3% to 4% of revenues. They predict the revenue increase alone could be a $3.5 billion opportunity for the industry [2] and this doesn’t even factor in the profitability improvements of avoiding costly quality issues. Unfortunately, for the industry, quality has been getting worse, not better. The FDA’s Medical Device Recall Report FY 2003 to FY 2012 found that recalls nearly doubled over the decade, showing a striking 97% increase in the number of recalls. Since 2012, the Stericycle Recall Index has continued to track regular increases on a quarterly basis in medical device recalls seeing a 39% increase in just four years from 2013 to 2017 [3]. To reverse this trend, medical device companies should adopt new approaches that enable a greater focus on quality. Shift from Document Centric to Product Centric One way to achieve this is by shifting from a document centric process to one that is product centric. This shift enables more focus on high quality, innovative products that meet patient needs. The good news is that this is possible with investments in the right software solutions. Software solutions can reduce manual, time intensive reporting processes to a push of a button. Rather than structuring processes around documentation, software solutions can allow you to focus on developing the right products and services that will meet patient needs. For these reasons, some medical device manufacturers integrate quality processes into their core product lifecycle management activities. By integrating quality processes throughout the product design and delivery lifecycle, companies can improve efficiency. With this approach, instead of wasting efforts searching for compliance supporting documentation and reporting, companies can use that valuable time for quality and innovation. The result will be higher profitability. Enabling Outcome-Based Healthcare Other changes in the medical device industry come from recent trends such as the transition to outcome-based healthcare in the US. In some cases, to be compensated, medical professionals must show positive patient outcomes. A way to accomplish this is to take advantage of innovation enabled by the Internet of Things (IoT). For example, IoT combined with software capabilities can be used to meet requirements for Unique Device Identifiers (UDIs) that will provide new levels of traceability and communication to demonstrate device effectiveness. The right software solution must be in place to effectively manage it. While UDIs present one possible use case for IoT, the potential opportunities for IoT go even further. IoT and other technological advancements such as augmented reality (AR) and 3D printing, create new opportunities for profitable new business models by enabling services that align with customer and patient needs. However, companies stuck following traditional document centric workflows may struggle to find the bandwidth to innovate with these new technologies. Meanwhile, competitors who can devote the resources to innovation will be well positioned to capture a leading market position. This situation makes it an ideal time to invest in a software platform that enables a product centric approach for the entire lifecycle of your device. Plan for the Right Software Platform As you evaluate your current needs, think through how your business needs may evolve due to the impact of technological advances in medical devices. For example, designing for connectivity may require new approaches to design. You will now need to consider things like sensors, ecosystems, and new IT development roles that will play a critical part of product development. Ensure your software platform will be able to meet both current and future needs as your product portfolio evolves. While you consider investments in software solutions, leverage existing systems that are working well. The new solution should use a platform that will leverage and extend the investments made in existing solutions, such as Manufacturing Execution Systems (MES), Enterprise Resource Planning (ERP) and Product Lifecycle Management (PLM) if you are happy with them. However, the platform should support traceability across all systems to support compliance reporting and so that documentation can be updated once after changes without worrying about conflicting documentation that will put compliance at risk. Learn More By Downloading the Buyer's Guide With so much to consider, how do you select the right software technology to support the lifecycle of your devices? This buyer’s guide will serve as guidance to help you choose the right solution for your company. This guide consists of four major sections covering software tool functionality required for medical device companies, implementation requirements, vendor attributes, and unique company considerations (Figure 1). Each section includes a checklist of key requirements to investigate when selecting software tools. This guide is not an all-encompassing requirements list. It provides a high-level overview. [1] “Evaluate MedTech World Preview 2018, Outlook to 2024,” Evaluate, September 2018 (http://www.evaluate.com/thought-leadership/medtech/evaluatemedtech-world-preview-2018-outlook-2024). [2] Ted Fuhr, Katy George, Janice Pai, “The Business Case for Medical Device Quality,” McKinsey Center for Government, McKinsey & Company, October 2013 [3] “Number of Medical Device Recalls in the U.S. from 2013 to 2017,” Statista, https://www.statista.com/statistics/618125/medical-device-recalls-in-the-us-by-number/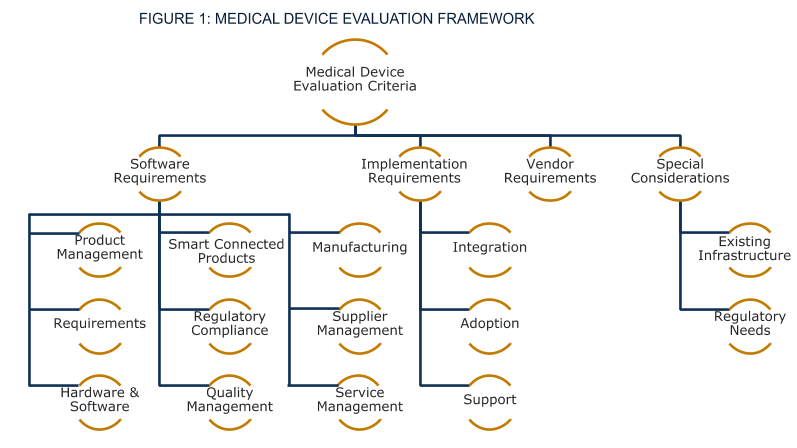
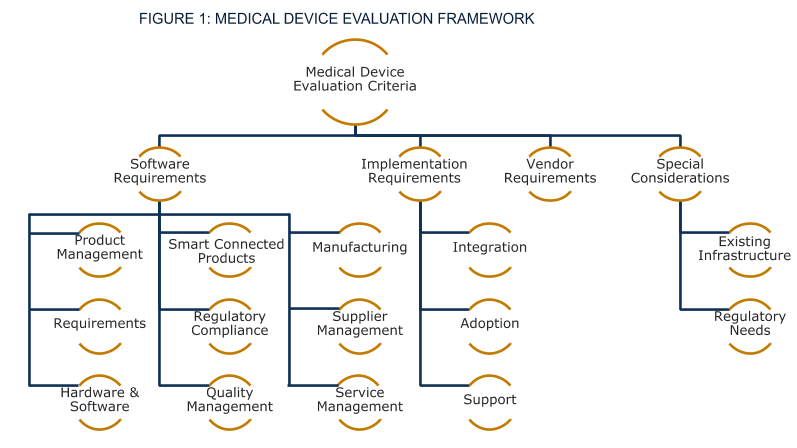
Conclusion
The Cost of Poor Quality Medical device companies looking to improve profitability should shift their focus from a document centric process to a product centric process that will enable them to concentrate on quality. The cost of poor quality can be significant. In fact, McKinsey estimates that non-routine quality events cost the industry up to $5 billion. On the other hand, companies that focus on high quality enjoy a significant advantage with a potential increase in profits of 3% to 4% of revenues, according to McKinsey. The FDA has also concluded that a greater focus on quality is required. For example, they have found recalls have increased by 97%, with design errors being the leading cause. With the Case for Quality initiative, quality should become an area of heightened focus, which a product centric approach supports. Unfortunately, making this shift, while still meeting regulatory requirements is hard. However, with the right technology, companies can make it much easier. The Right Solution The right solution should consider all aspects of the product lifecycle from requirements, through design, testing, manufacturing, and service. It should streamline the regulatory process and automate as much as possible. With traceability across the lifecycle and all deliverables, it will be much easier to provide regulatory compliance documentation. That traceability should also extend to suppliers. The right software solution can make it much easier to bring the right, high quality medical device to market, providing a competitive advantage. This will also support the additional data requirements of the EU MDR for product submissions. When making such a significant investment, you should also anticipate how your requirements will evolve to remain competitive in the future. Technological advancements such as IoT, AR, and 3D printing create opportunities for very profitable new business models that can increase the quality of patient care considerably. Features such as predictive and remote service offer flexibility around downtime to minimize the impact on patient health. These technologies can help medical device companies advance their mission of making people’s lives better.Recommendations
Based on industry experience and research for this report, Tech-Clarity offers the following recommendations:- Identify the top challenges your company needs to solve when bringing medical devices to market.
- Consider a solution that can support the entire lifecycle of your product, from patient needs and requirements to, design, test, manufacturing, and service.
- Look at solutions that will support the Case for Quality. A product centric approach and an integrated PLM and Quality Management System can help keep the focus on quality throughout the entire lifecycle and will also make it easier to comply with the EU MDR.
- Use a vendor who is familiar with medical device regulatory requirements and has the technology to reduce the manual effort required to comply with regulations.
- Ensure you can manage the device and all associated documents, design details, and changes while having traceability across everything.
- Support requirements with a solution that will work across all disciplines and has traceability across all stages and deliverables to support changes and compliance.
- Empower each team member including design, quality, procurement, manufacturing, and service with tools that work for them, while still ensuring a single source of truth for product information.
- Support quality management with traceability from requirements to test and reporting tools to ensure monitoring of trends that impact quality.
- Ensure tight controls on suppliers so as not to put compliance at risk.
- Select a solution that will support manufacturing so that you produce devices as designed and meet regulatory requirements.
- Think about medical device service requirements and use a solution that will support current and future service models such as predictive and remote service.
- Select a vendor who can integrate with your existing solutions while implementing new solutions where needed.
- Consider future needs for potential revenue streams and future needs for technologies such as IoT, 3D printing, and Augmented Reality.
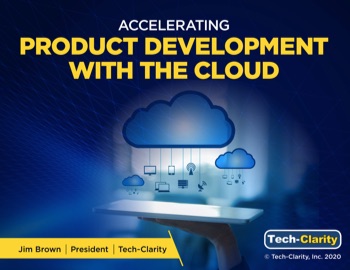
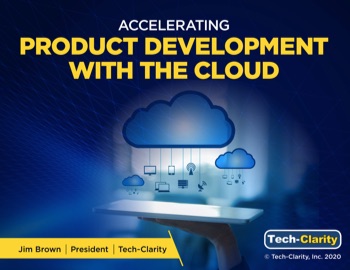
The Cloud Improves Product Development Speed and Collaboration
Researchers discovered that product development speed drives profitability, but that today’s status quo hampers time to market because product development resources waste too much time on non-value-added activities. On the other hand, companies that use the cloud for product development find it easier to collaborate, waste less time, and are less likely to report missing due dates due to product development challenges. Please enjoy the summary* below. Access the full eBook from our sponsor, Onshape (registration required).Table of Contents
- Profitability Demands Product Development Velocity
- Companies are Wasting too Much Development Time
- Wasted Time Leads to Costly Errors and Delays
- Increased Reliance on Others will Increase Wasted Time
- Benchmarking Product Development Performance
- The Cloud Enhances Product Development
- The Cloud Fuels Collaboration
- Cloud Benefits for Product Development
- Conclusions
- About the Research
- Acknowledgments
Profitability Demands Product Development Velocity
The Need for Speed Let’s start with the business in mind. Product development is critical to a profitable manufacturing company. Manufacturers must innovate quickly to respond to market and customer needs. Responding companies confirm this, with over one-half selecting product development speed as a driver of their business success and profitability over the next three years, making it the most prevalent factor.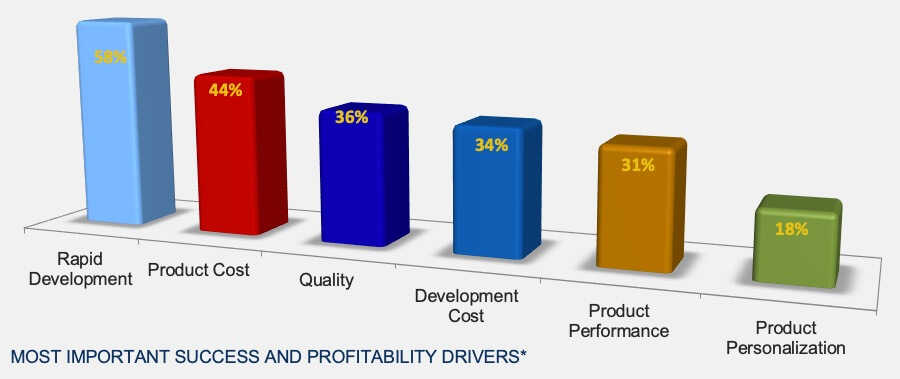
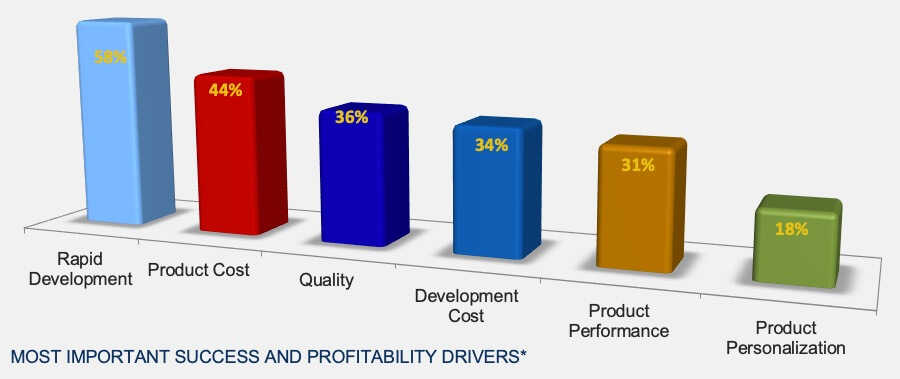
Companies are Wasting too Much Development Time
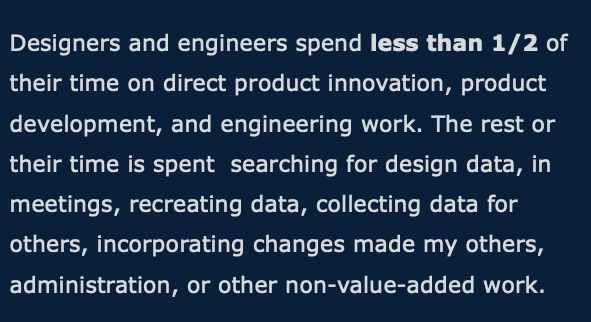
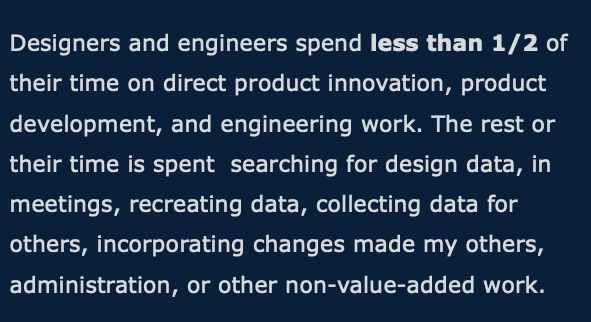
Conclusions
Key Findings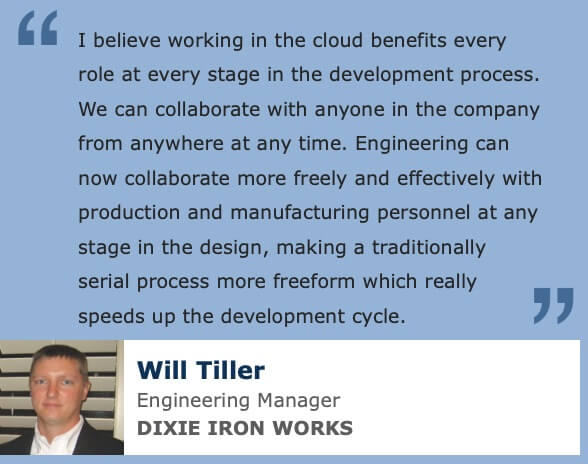
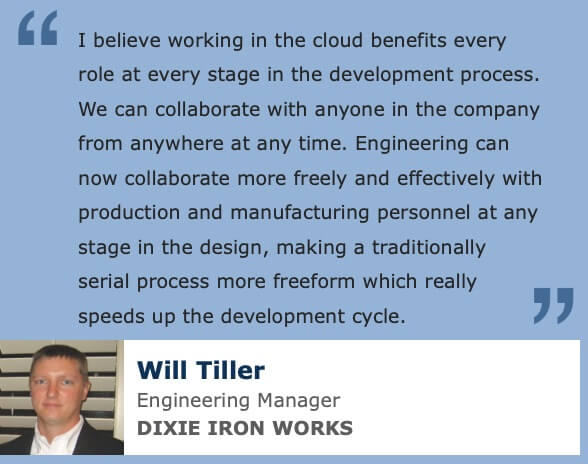
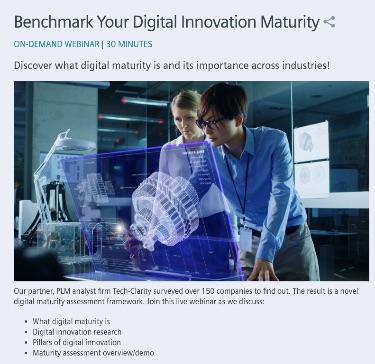
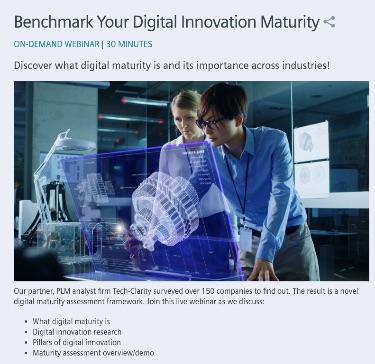
Benchmark Your Digital Innovation Maturity
This webcast shares definitions and details about the four pillars of digital innovation maturity:- Digital Twin
- Digital Thread
- Digital Manufacturing
- Digital Innovation Platform
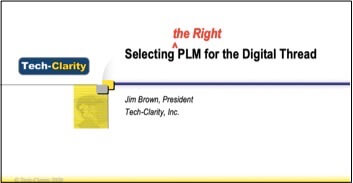
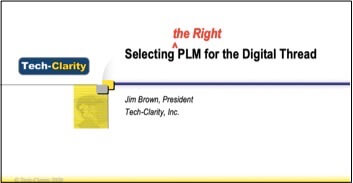
Webcast Announcement
Leading manufacturers are embracing the digital thread to streamline product development and create digital continuity across the product lifecycle. The digital thread is a strategic initiative that provides significant, measurable benefits including, increased engineering efficiency, improved quality, faster time to market, enhanced innovation, and better compliance. The backbone of the digital thread is enterprise PLM. PLM is a key digital enabler according to a recent Tech-Clarity survey, finding that top performing companies are 73% more likely to use PLM to support the digital thread. Join our panel interview hosted by Jim Brown, President of Tech-Clarity and Jeff Zemsky, Senior Director of Product Management, PTC. The panel will share recent survey results on PLM and the digital thread and discuss how to select the right PLM solution to meet digital thread objectives. The webcast covers:- The strategic value of the digital thread
- How to create digital continuity across the product lifecycle
- Key requirements of a supporting solution
- Special considerations for Engineering, Manufacturing, Quality, Service, and IT
- Other requirements critical to achieving digital thread value' is supposed
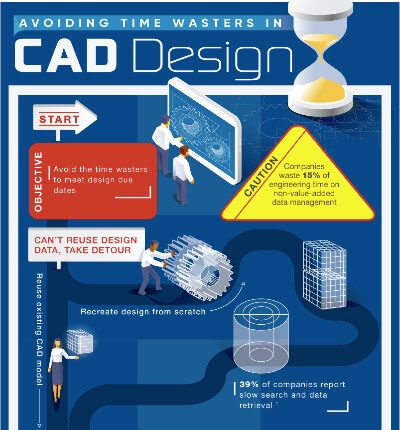
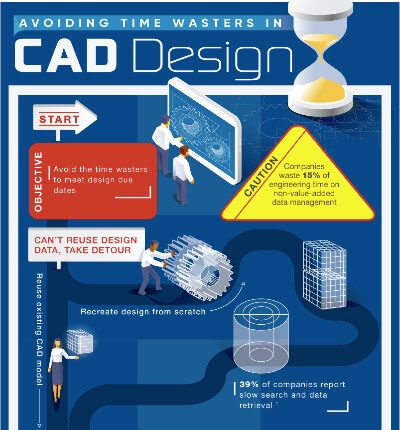
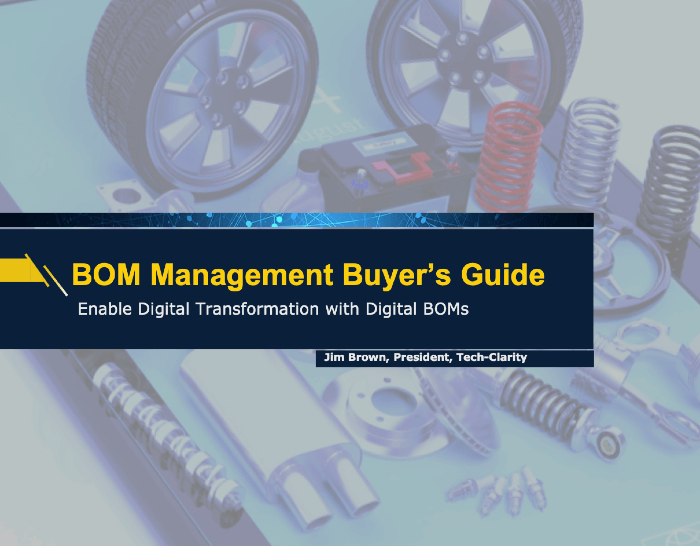
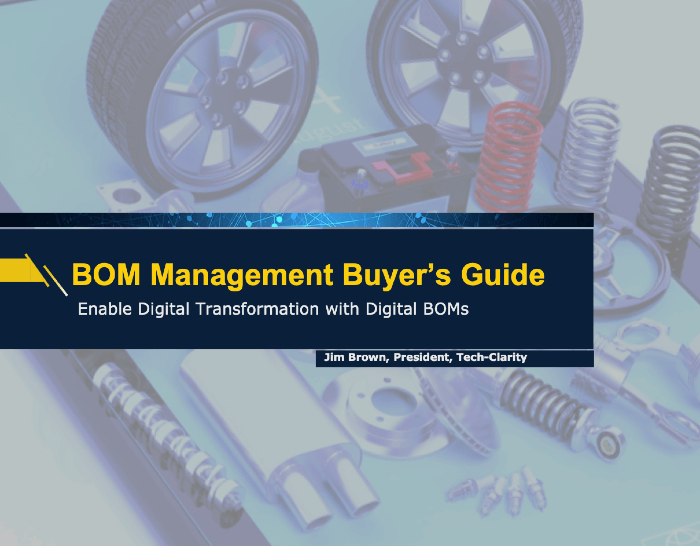
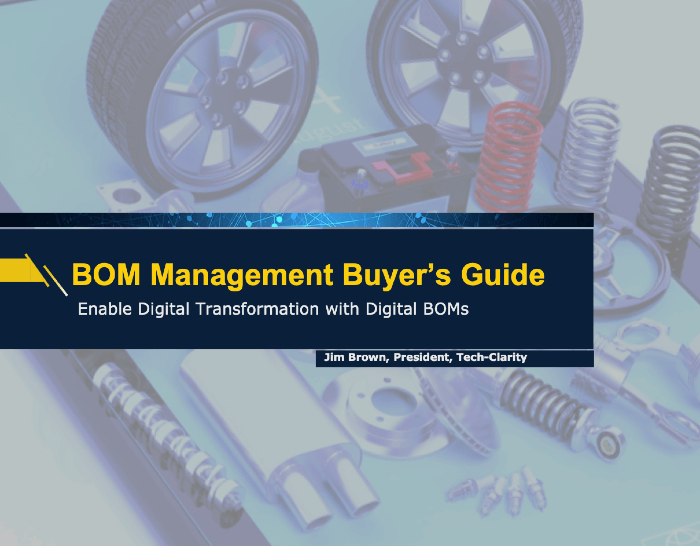
Table of Contents
- Introducing the Buyer's Guide
- Diagnosing BOM Management Issues
- The BOM Management Status Quo
- The BOM Management Business Case
- Analyze BOM Management Solution Capabilities
- Assess Service Requirements
- Consider Vendor Requirements
- Special Considerations
- Prepare for the Digital Enterprise
- Conclusion
- Recommendations
- About the Author
- About the Research
- Acknowledgments
Introducing the Buyer's Guide
BOM Fundamentals Managing Bills of Material (BOMs) is a fundamental need for any manufacturer. Without effective control of product structures, companies struggle with inefficiency and errors. On the other hand, improving the maturity of BOM-related processes helps manage complexity, improve efficiency, prevent mistakes, and enhance collaboration across departments and the supply chain. Improving the maturity of BOM-related processes helps manage complexity, improve efficiency, prevent mistakes, and enhance collaboration across departments and the supply chain. The resulting benefits can be strategic, leading to increased agility and faster time to market that impact top-line financial performance. This Buyer's Guide is a reference tool for manufacturers selecting a system to improve the maturity of their BOM. It also shares that digital BOM management is critical to support digital transformation initiatives including the digital twin, the Internet of Things (IoT), Virtual Reality (VR), and Augmented Reality (AR).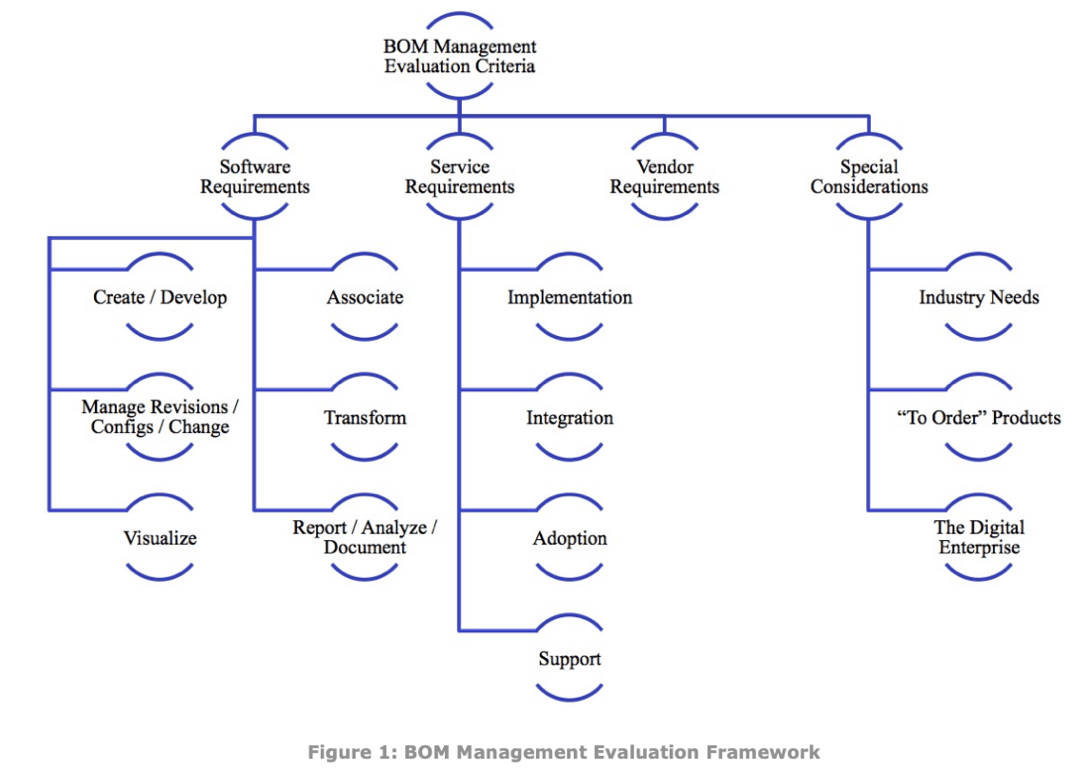
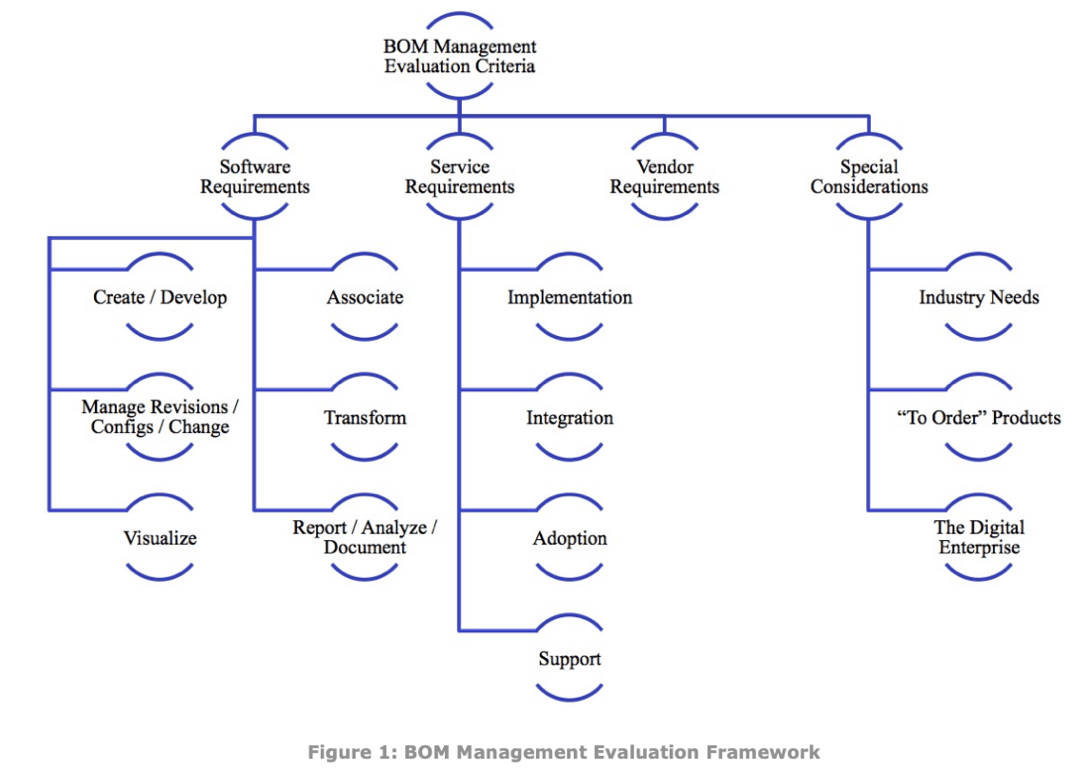
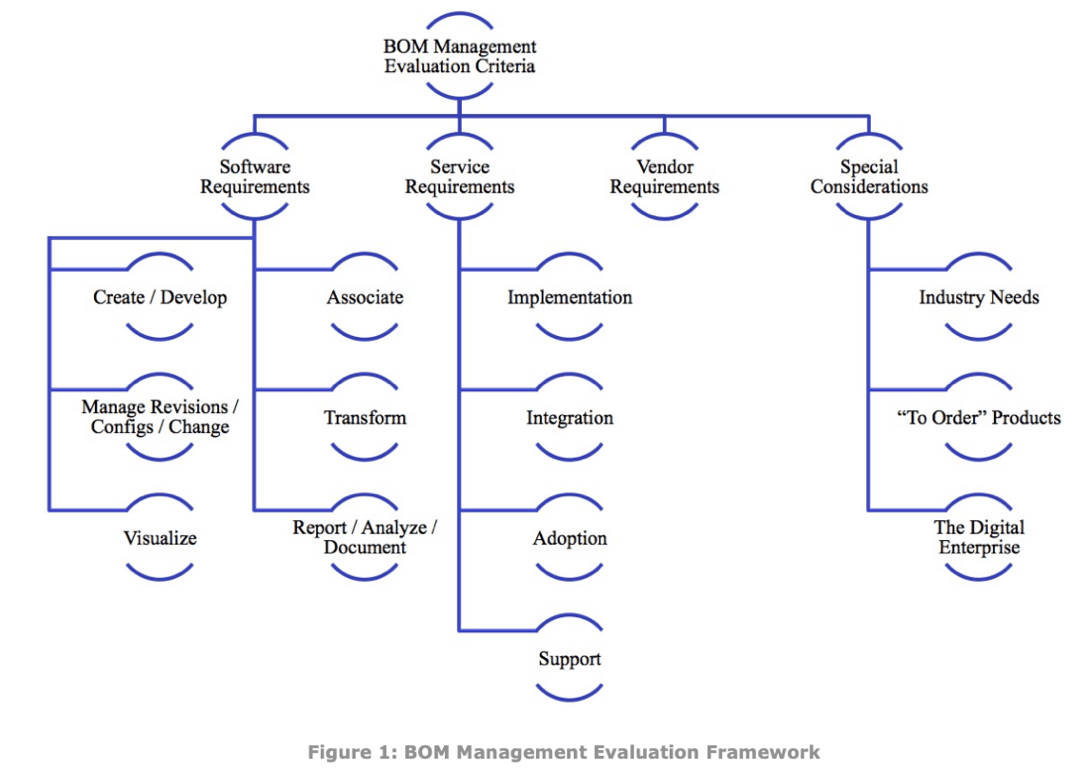
- Errors in manufacturing
- Poor first pass yield
- Ordering the wrong parts
- Delays due to part shortages
- Inability to confidently adopt engineering changes
- Slow time to full volume production
- Late identification of manufacturability or serviceability flaws
- Poor traceability
- Compliance issues or excess effort to comply
- Scrap and rework
- Slow review and approval processes
- Develop Product Structures
- Manage Revisions, Configurations, Change
- Visualize Products
- Associate Information
- Transform BOMs
- Report / Analyze / Document
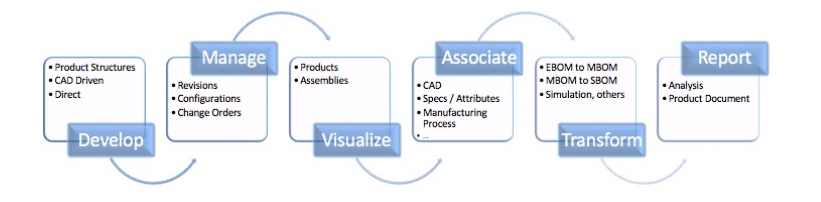
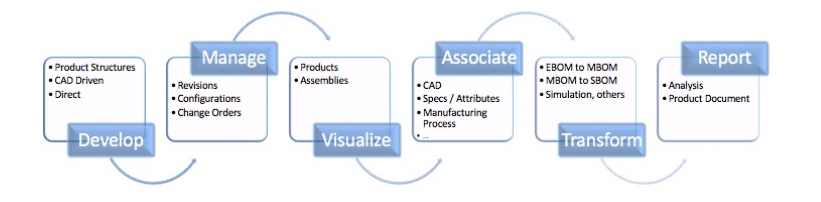
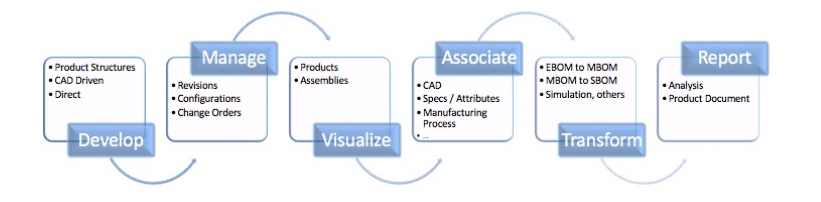
Conclusion
Recommendations
Based on industry experience and research on this report, Tech-Clarity offers the following recommendations:- Think big, but remain agile and take BOM management improvements in steps
- Recognize the importance of accurate, complete, timely, and accessible product structures
- Know your needs
- Understand the value
- Look for functionality, but extend requirements to vendor and service
- Consider any special needs for your business, industry, or geography
- Build the foundation for the digital enterprise, recognizing that BOM management is a key enabler
- Get started
All Results for "All"
Choosing the Right Cloud PLM (buyer’s guide)
What do manufacturers need to know when they select a cloud Product Lifecycle Management (PLM) solution? Although manufacturers have started to adopt cloud solutions for many aspects of their business, PLM has lagged behind. Our research shows that over one-half of manufacturers are considering cloud and about one-quarter already leverage the cloud support product innovation…
Why Should You Use CFD?
Is structural analysis enough or should design engineers use CFD too? This guest post on the Siemens Solid Edge Blog explores this question. With product complexity increasing, it is harder than ever for engineers to make the right decision decisions. Complexity comes from the ever increasing amount of components, configurations, and electronics. Consequently, greater complexity…
Why Strategy Matters to Industry 4.0 Success (eBook)
What step are many companies missing to ensure their Industry 4.0 initiatives succeed? Why Strategy Matters to Industry 4.0 Success discusses the importance of enterprise strategy. The right strategy makes even pilot projects more likely to live up to their potential. This eBook talks about how thinking big for enterprise transformation makes initiatives more pragmatic….
Product Data Management Buyer’s Guide (buyer’s guide)
How can you choose the right PDM system for your business to make sure you achieve your productivity, product success, and profitability goals? The product data management (PDM) Buyer’s Guide is a reference tool to provide direction on what to look for when selecting a PDM system for your company. This guide is composed of…
Its Time for Semiconductor to Smarten Up! (presentation)
Can the most sophisticated manufacturing in the world get smarter? Join Julie Fraser in this session to challenge yourself. Consider what you don’t already know in this session at Siemens Industry Software’s Realize Live virtual user conference. It is based on the paper Smart Manufacturing for Semiconductor she authored prior to joining Tech-Clarity. This session…
5 Ways Agile Improves New Product Development – Part 2
In the second part of this two-part blog series, Michelle Boucher continues to explore the question, should you consider an agile methodology to support new product development, beyond just software? Proceeding from the first part, which explained what agile is and two reasons for using the agile methodology, the second part provides three more reasons…
Designing Smart Products Smartly: Increase the Maturity of Your Development Processes
How can companies mature their processes for designing smart products? Tech-Clarity’s eBook, Designing Smart Products Smartly: Increase the Maturity of Your Development Processes, explores this question. The combination of mechanics, electronics and software into today’s smart products have made them more responsive, adaptable, interconnected and portable than ever before. Incidentally, with customers expecting this type…
5 Ways Agile Improves New Product Development – Part 1
Can agile product development work beyond software? Agile has provided significant benefits to software development teams. Can those benefits be realized for other engineering disciplines too? In a guest post on the Siemens Solid Edge Blog, Michelle Boucher delves into these questions and the reasons you may want to consider using it to your product…
Buyer’s Guide for Engineers: How to Select Essential Tools for Product Design
What software tools do engineers need to support product design? Which capabilities will help engineers develop products that are higher quality, more personalized, more innovative, and lower in ownership cost? These are challenging tasks to achieve that are further complicated due to increasing product complexity, engineering changes, and multiple engineering disciplines. However, with the correct…
Avoid 5 CAD Design Time Wasters (eBook)
How can companies improve data management to avoid the five most common CAD design time wasters and win the engineering productivity challenge? Improving design data management maturity, enabled by PDM and PLM solutions, helps reduce non-value-added time and increase engineering productivity. Please enjoy the summary* below. Please visit our sponsor Siemens for the full research (registration…
Breaking the Mold: How Toolmakers Are Transforming Operations
What does it take for toolmakers to be competitive? What can mold makers do to improve their business? Tech-Clarity’s eBook, Breaking the Mold: How Toolmakers Are Transforming Operations to Stay Competitive explores these questions. The business of mold making is tough. Firstly, there is the time consuming bidding process where you need to provide an accurate,…
Empower Engineers with Cutting-Edge Design Tools
Do your design tools hold product development back? With the pressures of global competition, and the never-ending struggle of bringing innovative, cost-effective products to market efficiently, a smooth product design process is paramount. Unfortunately, the vast majority of companies, 99%, report they experience design bottlenecks that hold them back, which consequently hurts their success and…
Faster Product Development on the Cloud (webcast)
How can companies achieve faster product development and higher profitability using the cloud? Join Jim Brown on an exciting webcast as he shares four key takeaways from his recent survey of over 300 companies. Jim will be joined by an Onshape founder who will share how Onshape customers take advantage of the cloud to improve…
How-To Guide: Avoid Non-Value Added Work for Engineers
How can a company better utilize engineers’ time? Today’s market is hyper competitive; it is hard to stand out. To be successful, companies must empower their engineering teams to focus on product innovation, quality, performance and cost. Balancing those key criteria is challenging enough, but made even more challenging as engineers report they waste a…
Medical Device Manufacturers’ Software Selection Guide
What should you think about when selecting a software solution to support the development of medical devices while considering the Case for Quality and the EU MDR? Tech-Clarity’s Medical Device Manufacturers’ Software Selection Guide helps manufacturers identify the right buying criteria for software solutions to support developing, producing, and servicing medical devices. The guide also…
Accelerating Product Development with the Cloud (eBook)
How can the cloud help manufacturers improve product development to drive higher levels of profitability? Tech-Clarity surveyed over 300 companies about cloud product development to find out. The Cloud Improves Product Development Speed and Collaboration Researchers discovered that product development speed drives profitability, but that today’s status quo hampers time to market because product development…
Benchmark Your Innovation Processes and Systems (webcast)
How do your product innovation processes stack up against your competitors? Against top innovators? What practical steps can you take to improve it? Watch this webcast to understand how to benchmark your digital innovation maturity. Benchmark Your Digital Innovation Maturity This webcast shares definitions and details about the four pillars of digital innovation maturity: Digital…
Selecting PLM for the Digital Thread (webcast)
Why are manufacturers pursuing the digital thread? What is the right PLM system to support a digital thread initiative? Jim Brown joins PTC‘s Jeff Zemsky to share results from Tech-Clarity’s recent survey on PLM and the Digital Thread. Jim and Jeff discuss the goals and benefits of the digital thread, followed by requirements to ensure…
Avoid Wasting Design Time (infographic)
How can engineers avoid wasting precious design time on non-value-added data management tasks? Take a look at our new infographic Avoiding Time Wasters in CAD Design to see a graphical representation of our research. The “CAD Design Challenge” turns design into a board game that highlights key time wasters in design and the best practices…