BOM Processes Rely on Inadequate Solutions Ineffective BOM Processes Cause Disruption BOM management is critical to connecting design, purchasing, and production across a manufacturing business. Ineffective BOM processes, though, lead to low productivity and costly errors. With that in mind, why do so many manufacturers rely on substandard BOM management approaches like spreadsheets and email?…
- BOM Processes Rely on Inadequate Solutions
- The BOM is the Fundamental Communication Tool
- The BOM Process Status Quo
- The Five Fundamentals of a Successful BOM Process
- 1) Aim for Accuracy
- 2) Keep Data Current
- 3) Manage Complete BOMs
- 4) Communicate BOM Data Clearly
- 5) Put BOM Data into Action
- Next Steps
- Acknowledgments
The BOM is the Fundamental Communication Tool
BOMs are the Backbone of the Manufacturing Industry BOMs are the fundamental way that manufacturers define, communicate, and realize their products. The bill of material is essentially the backbone of the manufacturing business, specifying what to buy and what to build. In many companies, BOM communication has to bridge disciplines across company boundaries. BOMs are The Primary Communication Tool in Industry Sound BOM processes create a bridge that crosses all parts of the organization. They document engineering designs and provide the information that Purchasing needs to order parts. Then, they deliver the data needed for Manufacturing to plan and execute orders. BOM data also serves as the backbone for others to roll up important attributes like weight, costs, and more.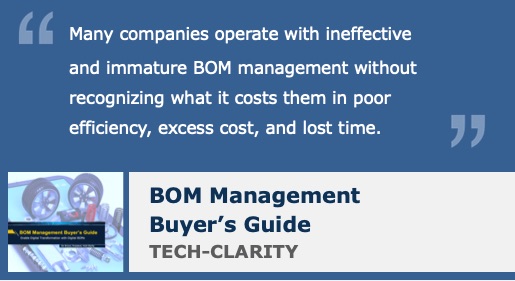
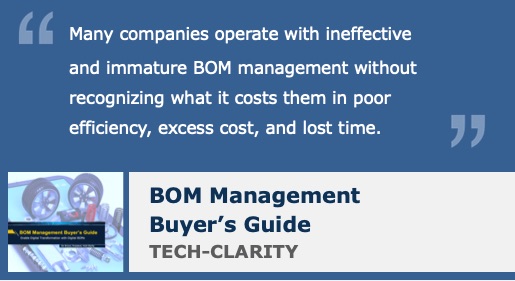
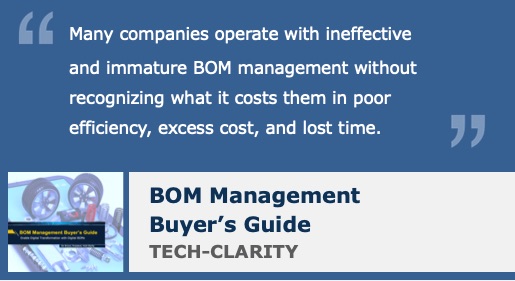
- Helps improve productivity
- Reduces the number of shipments delayed by missing parts
- Drives down scrap from using wrong parts or revisions
- Improves cost through item reuse
The BOM Process Status Quo
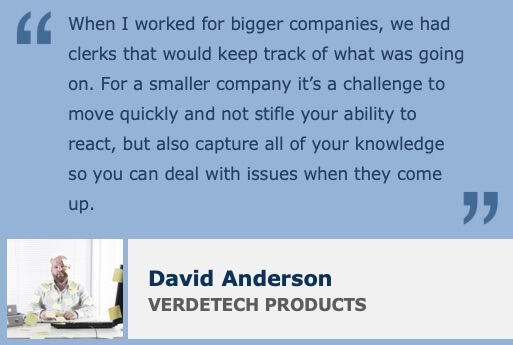
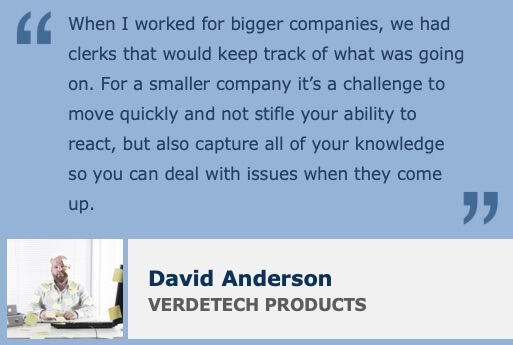
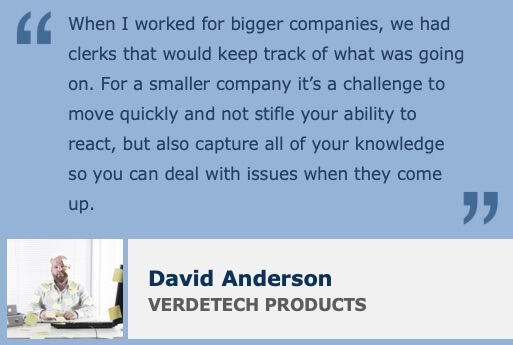
The Five Fundamentals of a Successful BOM Process
Get BOM Processes in Control Manufacturers who are ready to replace spreadsheets and email and get BOM processes under control can do so with reasonable effort. By focusing on the basics, they can make rapid improvements to productivity and reduce the impact of BOM-related errors. This leads to the question “What are the most important factors needed to improve BOM process?” We’ve identified five key areas that can easily be addressed and make a big impact on the business. Focus on the Fundamentals BOM Processes should be implemented and enabled in a way that ensures that they are:- Accurate
- Current
- Complete
- Clear
- Actionable
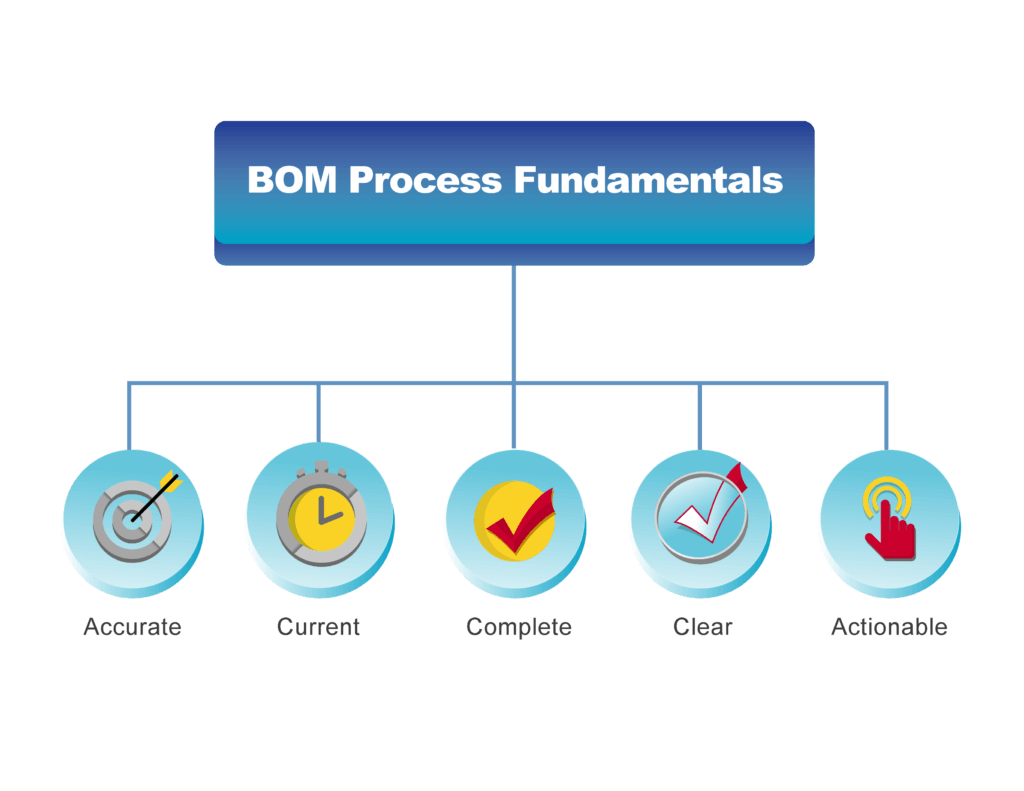
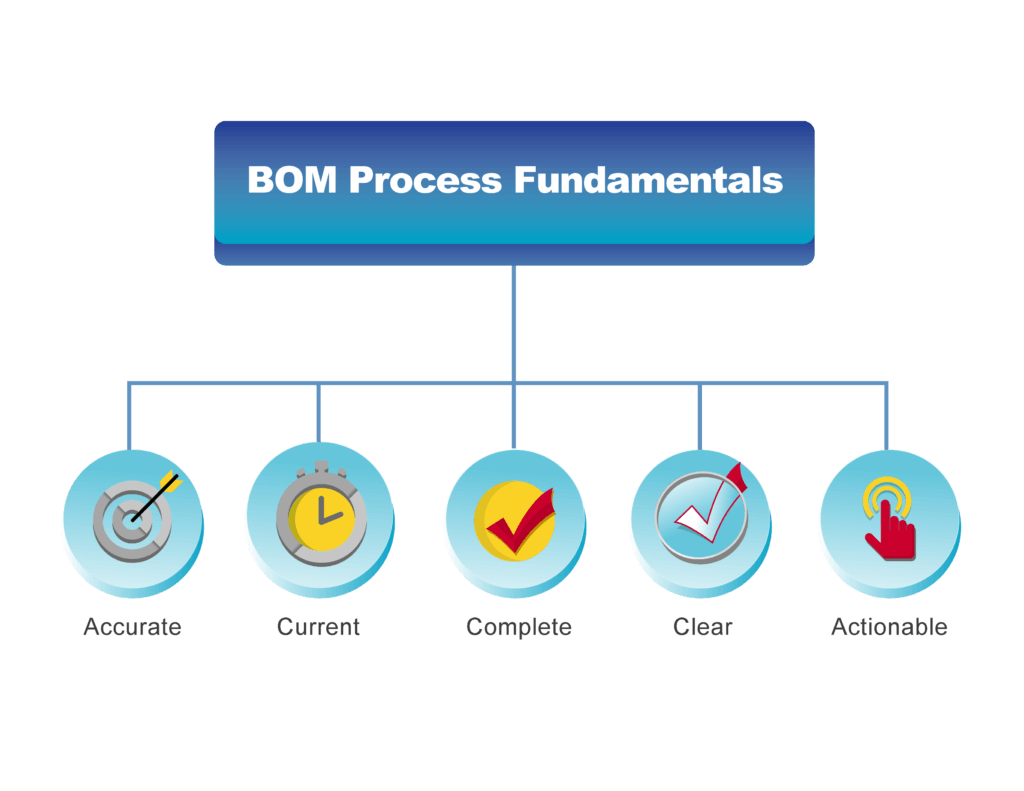
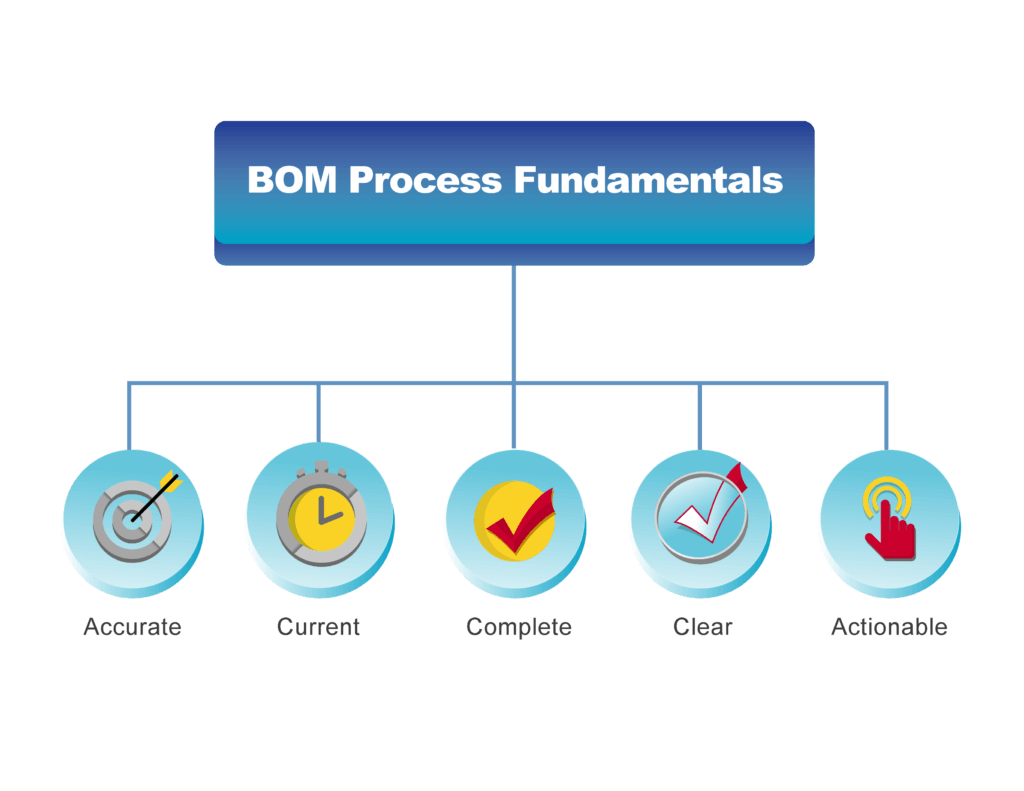
1) Aim for Accuracy
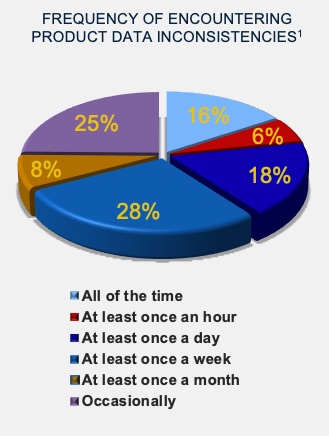
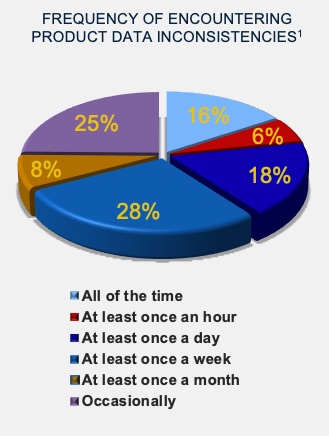
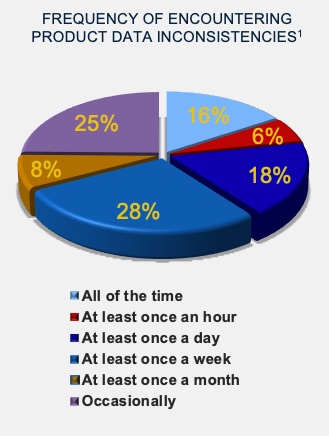
2) Keep Data Current
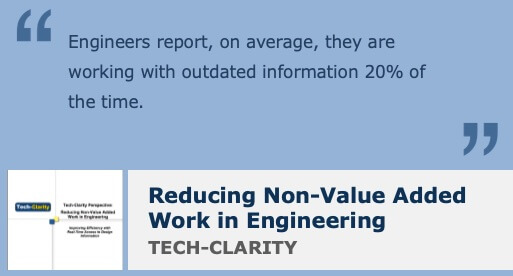
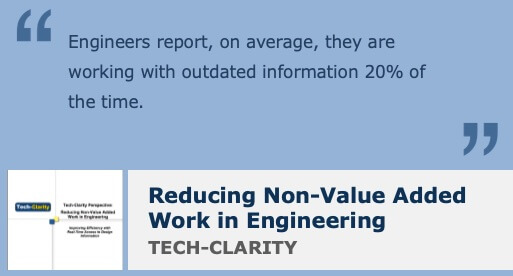
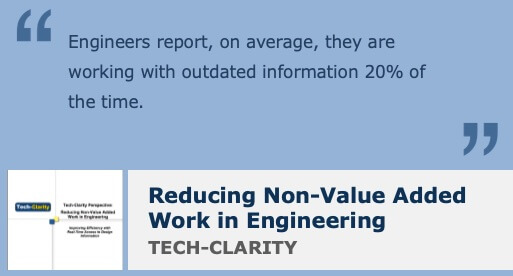
3) Manage Complete BOMs
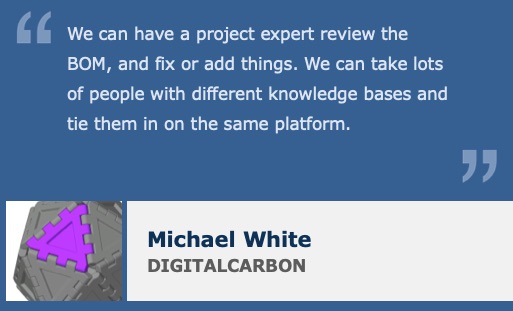
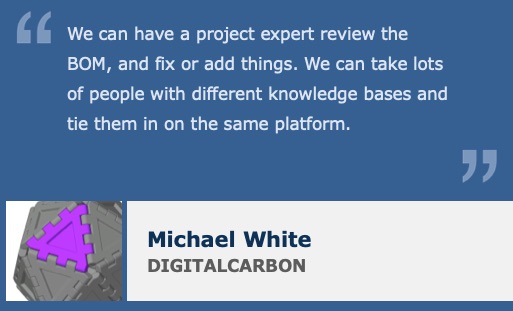
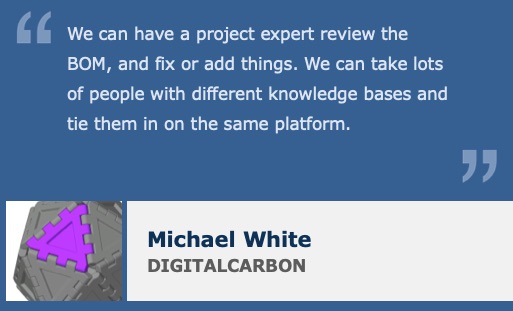
4) Communicate BOM Data Clearly
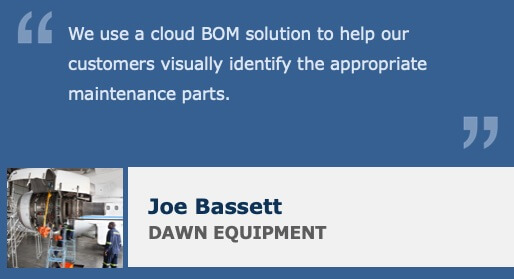
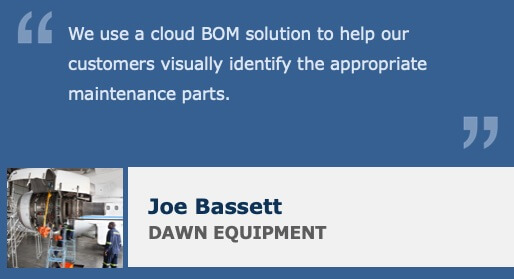
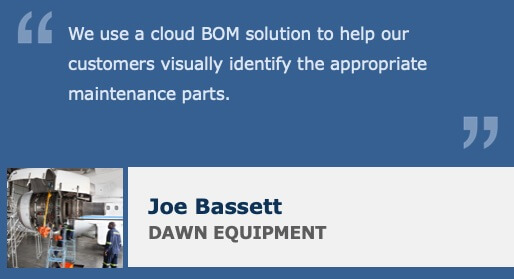
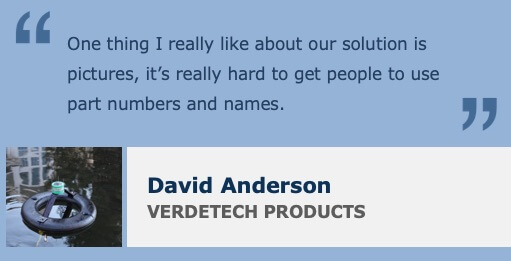
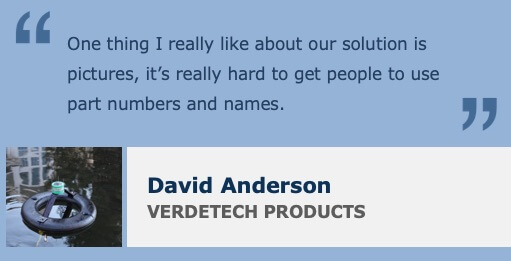
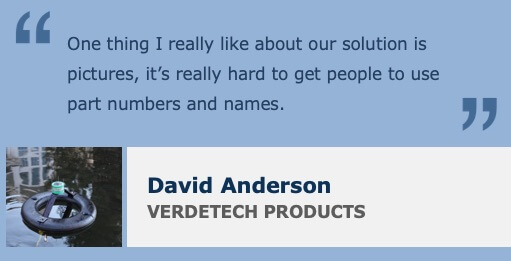
5) Put BOM Data into Action
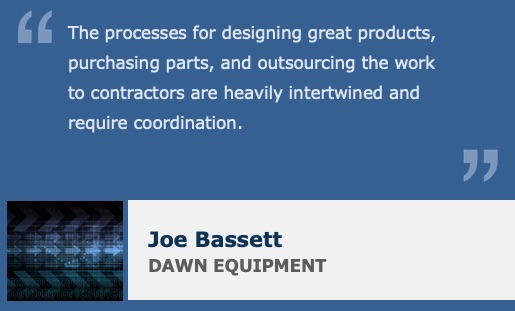
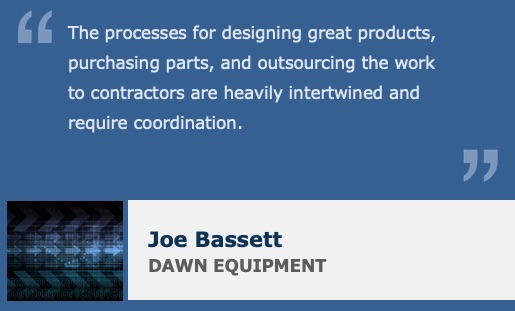
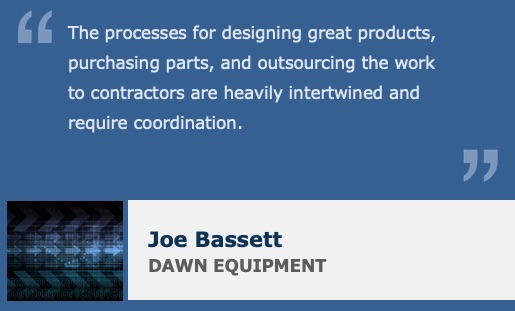
Next Steps
Go Beyond the Status Quo to Prevent Mistakes Today’s BOM process status quo, frequently relying on inadequate technology like spreadsheets and email, leads to inefficiency, excess cost, mistakes, quality issues, and late orders. The consequences of poor processes, especially for a smaller company, can be significant. As David Anderson of Verdetech Products shares, “Sometimes you get away with things by luck, but a major problem could kill a company.” It’s time for companies to raise the bar on BOM data and processes.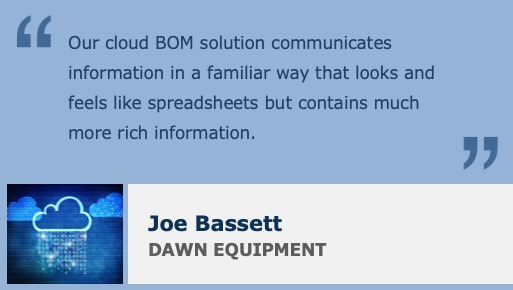
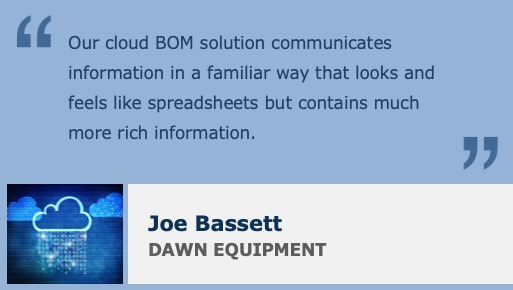
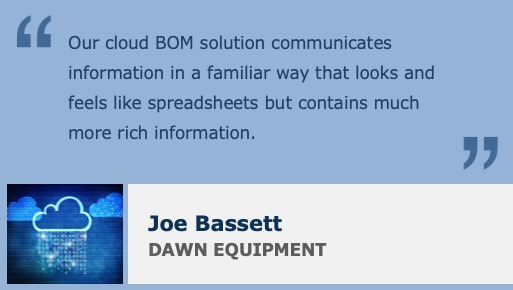
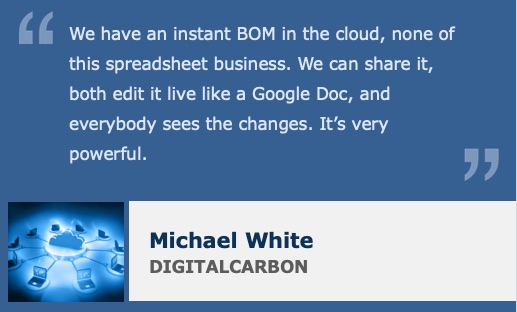
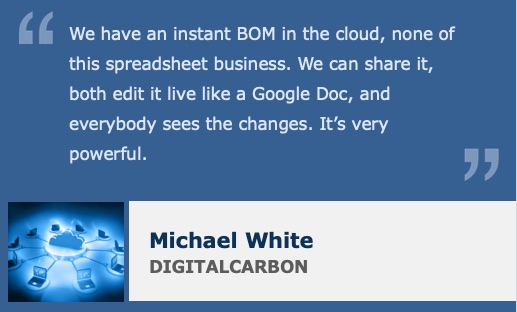
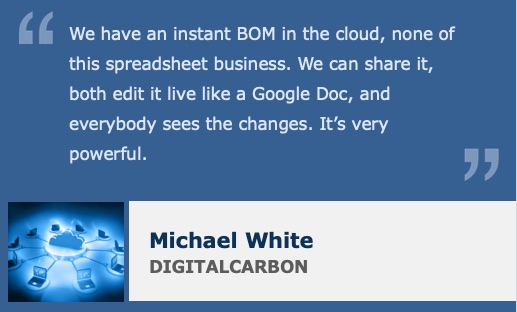
Acknowledgments
About the Author Jim is a recognized expert in enterprise software for manufacturers with over 25 years of experience in application software, management consulting, and research. He has extensive knowledge on how industrial companies use product innovation, product development, engineering, and other enterprise solutions to improve business performance. Jim is actively researching the value of improving product innovation and operational performance through digitalization. [post_title] => The Five Basics of Effective BOM Processes (eBook) [post_excerpt] => [post_status] => publish [comment_status] => open [ping_status] => open [post_password] => [post_name] => billofmaterials-management [to_ping] => [pinged] => [post_modified] => 2022-11-14 22:28:16 [post_modified_gmt] => 2022-11-15 03:28:16 [post_content_filtered] => [post_parent] => 0 [guid] => https://tech-clarity.com/?p=7823 [menu_order] => 0 [post_type] => post [post_mime_type] => [comment_count] => 1 [filter] => raw ) [1] => WP_Post Object ( [ID] => 7799 [post_author] => 2572 [post_date] => 2019-05-01 14:32:36 [post_date_gmt] => 2019-05-01 18:32:36 [post_content] =>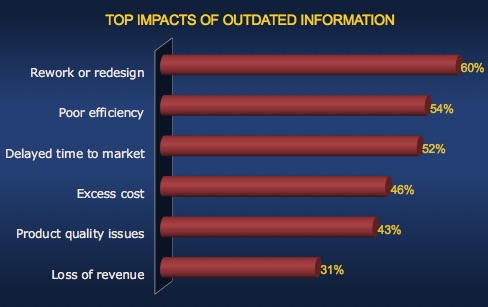
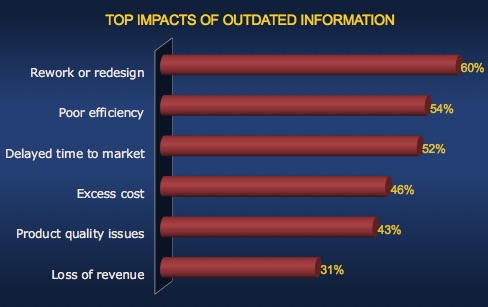
Focus on the Work You Enjoy
As an engineer, what gets you excited about your job? For most, it’s getting to work on really cool projects and innovating. Unfortunately, a good chunk of your time is wasted on other things, taking you away from the work you enjoy doing and the work that adds value for your company.How Do You Limit Non-Value Added Work?
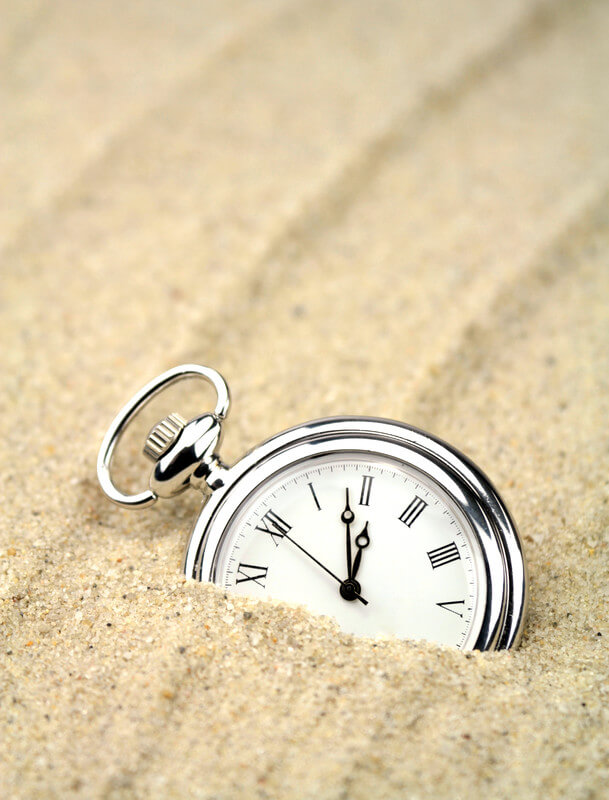
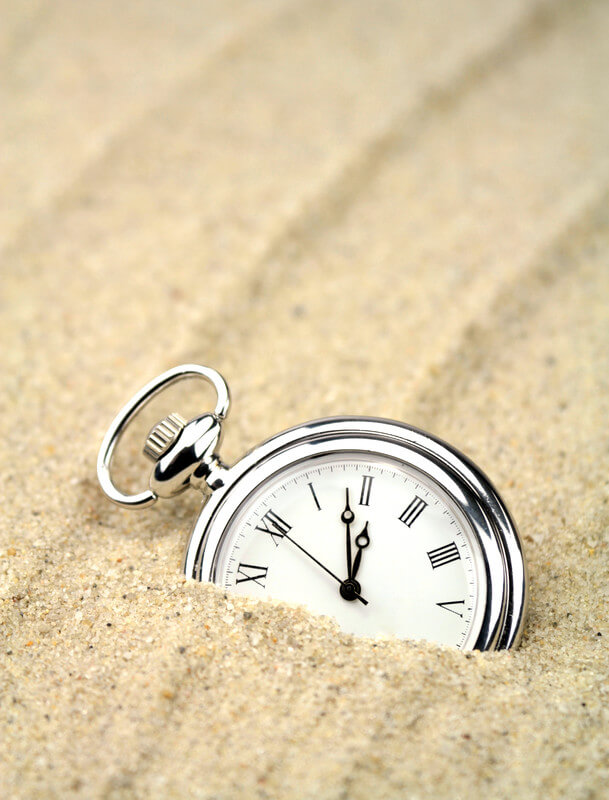
The Cost of Outdated Information
When design work is based on outdated information, error will be inevitable. These errors result in costly rework and redesign. Wasting even more time to correct these problems means poor efficiency which can delay time to market. As the design nears completion, there are fewer options to fix problems, so errors become much more expensive and time consuming to fix. Plus, with limited options, solutions may be less than ideal, which will hurt product quality or drive up cost. Of course, if problems are missed entirely, there will be even bigger quality problems in the field. The combination of poor quality, higher cost, and late to market all hurt competitiveness which can reduce revenue opportunities. This problem gets even worse when multiple engineering disciplines are involved. When products integrate mechanical components, electronics, and embedded software, there are inherent silos. Continue to the Sodius Willert blog for the full post. [post_title] => How to Avoid Non-Value Added Work for Engineers (guest post) [post_excerpt] => [post_status] => publish [comment_status] => open [ping_status] => open [post_password] => [post_name] => non-value-added-work [to_ping] => [pinged] => [post_modified] => 2022-11-14 22:25:36 [post_modified_gmt] => 2022-11-15 03:25:36 [post_content_filtered] => [post_parent] => 0 [guid] => https://tech-clarity.com/?p=7799 [menu_order] => 0 [post_type] => post [post_mime_type] => [comment_count] => 0 [filter] => raw ) [2] => WP_Post Object ( [ID] => 7516 [post_author] => 2572 [post_date] => 2019-04-25 11:30:48 [post_date_gmt] => 2019-04-25 15:30:48 [post_content] =>How do you navigate complex, omnichannel environments and manage multiple sources of data to make the best decisions? Can predictive analytics help?
Tech-Clarity’s Retail Analytics Buyer's Guide explains how predictive analytics provide better visibility across your retail business so that you can make better decisions to become more competitive. As the retail industry faces significant disruption, new approaches are required to survive. With volatile markets and fierce competition, the right decisions are critical to survival. Unfortunately, complex omnichannel environments, global supply chains, and dynamic development teams make it practically impossible to get timely visibility into the business. Even if you can, will you have confidence in your decisions? With the right predicative analytics solution, you can overcome these challenges, but only if you select the right technology. The research identifies eight capabilities to look for in a predicative analytics solution. These capabilities will help you make better decisions about your retail business.
Click here for the full eBook, thank you to our sponsor PTC.
WHY ARE PREDICTIVE ANALYTICS CRITICAL FOR TODAY’S RETAILERS?
In the retail industry, you need to support a complex, global, omnichannel environment, while navigating a dynamic market filled with economic volatility. It is not easy, especially as consumers have become more empowered and demanding through social media and online resources. To be successful, you need to make fast decisions, identify opportunities, respond to changing trends, react to competitors, adjust to shifts in the supply chain, and more. It’s complex. In many cases, margins are so thin that missing a trend, failing to spot an opportunity, or making the wrong decision can significantly hurt profitability. A few weak seasons can be disastrous for a brand.
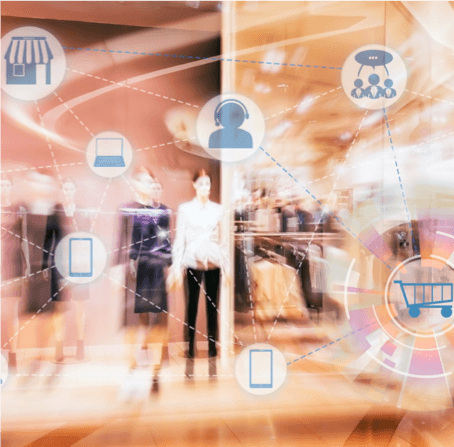
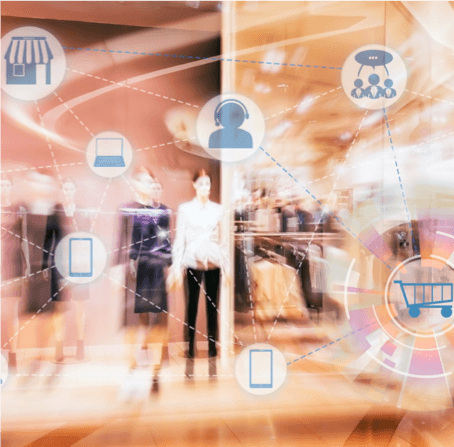
Making things even harder, the barriers to entry have dropped. It’s no longer enough to compete by becoming the biggest brand and leveraging scale. Online marketplaces have expanded the reach of start-ups and small companies. In many cases, the playing field has been leveled as resources that were only available to the largest companies are now available to everyone. This situation has further intensified the competition. Retail companies who can respond to market changes before their competitors will have the advantage.
To survive, retail companies must be nimble enough to react quickly, but they can only do that with the right insights. Information and knowledge are now competitive weapons and technology can be key to unleashing its potential. That knowledge comes from every aspect of the organization from business operations, product trends, supplier information, and more. This buyer’s guide reveals how retail companies can capitalize on their knowledge and uncovers eight capabilities that will help put the right technology in place to support them.
HOW DO PREDICTIVE ANALYTICS HELP?
The top challenges uncovered by research conducted by BOF and McKinsey reveal the importance of getting instant insights. The economic uncertainty related to events such as Brexit, a rise in protectionist policies in the US, a volatile stock market, and more can erode consumer confidence and make it even harder to predict buying trends. Key insights will help overcome some of this uncertainty. With online shopping and social media, consumers are more informed than ever, creating a need for retailers to know how they can best influence buying behavior. The right data, in context, will help. Merchandise needs to be at the right place at the right time while avoiding excess inventory. Retailers need to offer consumers the experiences that will keep them coming back, with the right products that reflect the latest trends. Again, analytics will guide those decisions.
SELECT THE RIGHT RETAIL PREDICTIVE ANALYTICS SOLUTION FOR YOUR NEEDS
By selecting the right software, you should get timely insights to help you bring the right products to market, optimize the management of supply chains, influence buying behavior and more. These needed insights will help you make smarter decisions which should lead to better operating margins
*This summary is an abbreviated version of the eBook and does not contain the full content. A link to download the full eBook is available above.
If you have difficulty obtaining a copy of the research, please contact us using the “Contact” link below.
[post_title] => Retail Analytics Buyer’s Guide (eBook) [post_excerpt] => [post_status] => publish [comment_status] => open [ping_status] => open [post_password] => [post_name] => retail-analytics-buyers-guide [to_ping] => [pinged] => [post_modified] => 2022-11-14 22:28:15 [post_modified_gmt] => 2022-11-15 03:28:15 [post_content_filtered] => [post_parent] => 0 [guid] => https://tech-clarity.com/?p=7516 [menu_order] => 0 [post_type] => post [post_mime_type] => [comment_count] => 0 [filter] => raw ) [3] => WP_Post Object ( [ID] => 7737 [post_author] => 2572 [post_date] => 2019-04-22 12:21:38 [post_date_gmt] => 2019-04-22 16:21:38 [post_content] =>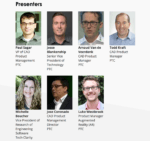
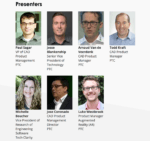
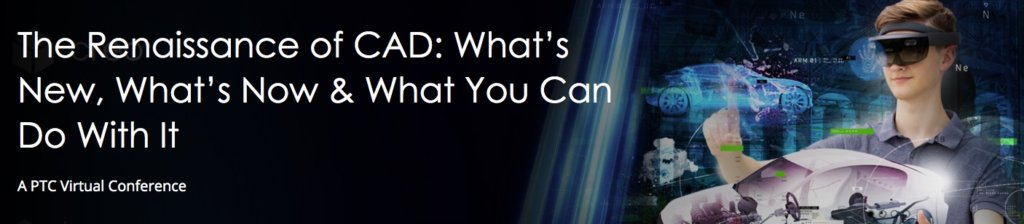
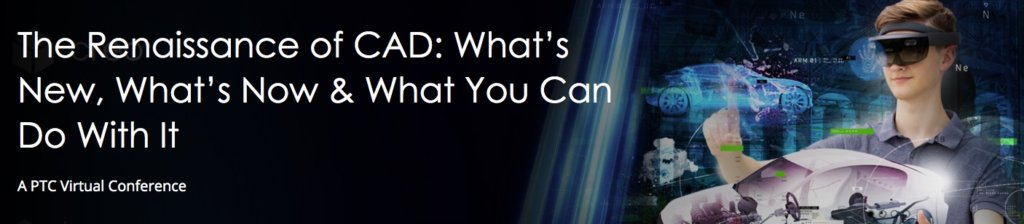
Transcript
The food and beverage industry is facing major disruption New competitors are adopting digital technologies and taking on the largest of companies, competing with unprecedented innovation and agility. Consumers are demanding more. To rise to the challenge, food and beverage plants need to increase flexibility while maintaining high productivity and compliance to ensure consumer confidence. The digital revolution has begun. Food companies have to leverage digital tools including the Internet of Things, the Digital Twin, the Cloud and Analytics to drive agility and consumer responsiveness. Using the IoT, digital food and beverage companies tap into data from a variety of sources and use analytics to gain deep consumer insights. Then, they quickly reformulate digital recipes to respond to trends. They leverage plant automation to capitalize on changing preferences. Digitalization allows food and beverage companies to get products that consumers want to market faster than the competition. But leading companies go beyond just internal agility and responsiveness. They use the IoT to gain advanced insights to optimize recipes and production schedules. The digital plant acts as one with their supply chain to rapidly adjust to changing supply and demand. Digital food and beverage companies also turn to digitalization to drive higher productivity. They reduce downtime by monitoring equipment health and servicing equipment before it fails using the Industrial IoT and predictive maintenance. They improve yields by identifying and correcting production issues in real-time. They use the IoT and analytics to benchmark performance to identity improvement opportunities. They use the digital twin of their plant to simulate and validate the impact of changing equipment. They quickly deploy new recipes, packaging and equipment using virtual commissioning. Finally, they identify opportunities to more accurately simulate production based on IoT data and a closed loop digital twin to better reflect reality and improve optimization using real-world information. Digitalization helps food and beverage companies improve throughput, increase uptime, decrease cost, improve quality and support high levels of traceability and compliance. It enables companies to raise the bar on innovation and agility without compromising productivity, cost or quality. The time has come for food and beverage plants to digitalize in order to survive in the digital age. To learn how, watch the rest of our video series on digitalization in the food & beverage industry. And learn more from our sponsor, Siemens PLM, a leader in digitalization for the food & beverage industry. [post_title] => IoT, Industrial IoT, and Digital Twins in Food & Beverage Production (animation) [post_excerpt] => [post_status] => publish [comment_status] => open [ping_status] => open [post_password] => [post_name] => iot-twin-foodbeverage [to_ping] => [pinged] => [post_modified] => 2022-12-02 15:05:38 [post_modified_gmt] => 2022-12-02 20:05:38 [post_content_filtered] => [post_parent] => 0 [guid] => https://tech-clarity.com/?p=7752 [menu_order] => 0 [post_type] => post [post_mime_type] => [comment_count] => 0 [filter] => raw ) [5] => WP_Post Object ( [ID] => 7580 [post_author] => 2572 [post_date] => 2019-04-03 14:25:01 [post_date_gmt] => 2019-04-03 18:25:01 [post_content] =>How can you get the quickest return on your investments in technology?
As we look ahead to the coming decade, technology will become increasingly critical for your company to stay competitive. New technology can include CAD, CAE, PLM, 3D printing, IoT, and more. However, for that technology to work for your business, your implementation must be successful. With a new technology, often it is the cultural changes that can derail the project. Starting with a plan to overcome challenges like this can be the most important part of a successful implementation. Tech-Clarity’s Ten Practices to Successfully Implement Technology shares 10 best practices to support the implementation and adoption of new technology so that you can get the expected return on your technology investments as quickly as possible.
Please enjoy the summary* below.
For the full eBook, please visit our sponsor SOLIDWORKS (free of charge, registration required).
HOW CAN YOU GET THE MOST FROM YOUR TECHNOLOGY INVESTMENTS?
Staying competitive in today’s global market means developing exceptional products that are innovative, high quality, and cost-effective. With so much to consider, how can you get ahead? For many, technology, including software tools, is the answer. Technology investments can help you grow your business, expand your customer base, and extend your services. With great software tools, you can accomplish more than you thought possible. Unfortunately, ignoring opportunities for improvement can stagnate the business, which can eventually lead to lost market share.
The key is selecting the right technology solution and successfully adopting it. This eBook identifies best practices for successful technology adoption to position your company for success for the next decade.
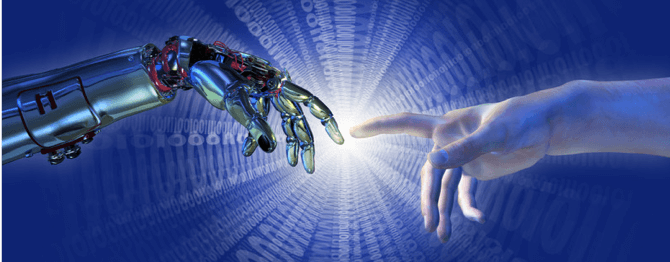
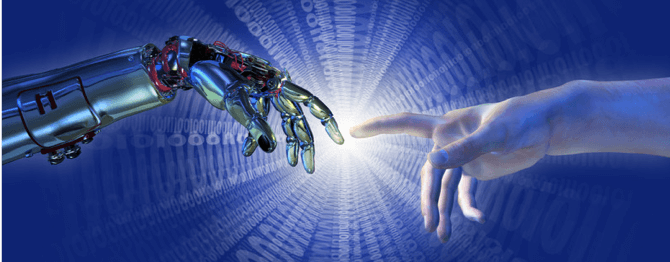
TECHNOLOGY SUPPORTS INNOVATION EFFORTS
Outsource vs. Internal Development?
Innovation often requires new skills. Many find they lack the internal expertise to take advantage of new materials, use the latest manufacturing techniques, support connectivity, or benefit from other industry advancements. When faced with this challenge, you can outsource or try to develop the skills internally. Regardless of which option you choose, technology will make it easier.
Support Outsourcing with Technology
For some, outsourcing can be a great option as a way to tap into expertise that you lack. When outsourcing, technology can ensure good collaboration, support communication, keep design data in sync, and protect intellectual property. As an example, cloud solutions can offer a platform to share data with third parties in a secure manner.
Technology Lowers Internal Development Cost
For other companies, especially smaller businesses, the overhead associated with outsourcing may be too much. It takes time to familiarize a third party with your product lines, manage quality, and coordinate changes, especially for highly engineered products. In these cases, it may be easier to do everything in-house. Again, technology can make that easier with software tools that have embedded intelligence to guide the design or manufacturing process.
RECOMMENDATIONS AND NEXT STEPS
Technology can have a significantly impact on your business in a positive way. It can be the key to help you expand, grow, and evolve your business. However, as good as the technology may be, it will only help your company if you take the right steps to ensure the adoption is successful.
The following checklist will help you achieve success:
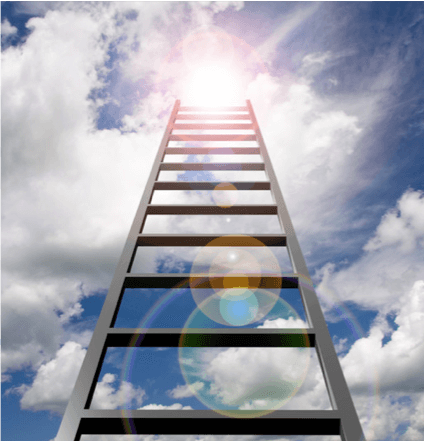
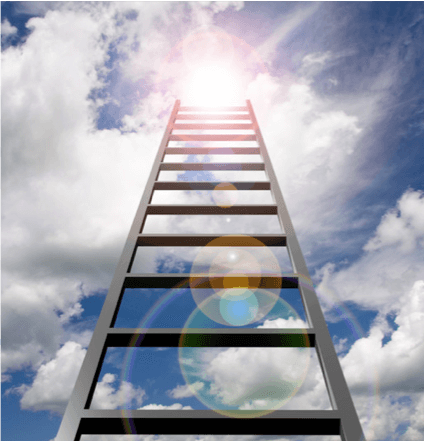
- Determine Your Business Needs Upfront
- Be Open to Change
- Keep the Focus on Customers
- Consider Vision and Future Needs
- Keep it Simple
- Automate Tedious Workflows
- Manage Scope
- Manage the Role of Team Members
- Overcome the Resistance to Change
- Provide Training
- Establish Success Factors
By following these ten recommendations, your company will be better positioned to successfully adopt technology and realize the expected ROI even faster.
*This summary is an abbreviated version of the eBook and does not contain the full content. A link to download the full eBook is available above.
If you have difficulty obtaining a copy of the research, please contact us using the “Contact” link below.
[post_title] => Ten Practices to Successfully Implement Technology (eBook) [post_excerpt] => [post_status] => publish [comment_status] => open [ping_status] => open [post_password] => [post_name] => ten-practices-to-successfully-implement-technology-ebook [to_ping] => [pinged] => [post_modified] => 2022-11-14 22:28:16 [post_modified_gmt] => 2022-11-15 03:28:16 [post_content_filtered] => [post_parent] => 0 [guid] => https://tech-clarity.com/?p=7580 [menu_order] => 0 [post_type] => post [post_mime_type] => [comment_count] => 0 [filter] => raw ) [6] => WP_Post Object ( [ID] => 7670 [post_author] => 2 [post_date] => 2019-04-01 09:44:21 [post_date_gmt] => 2019-04-01 13:44:21 [post_content] => How have manufacturers' opinions on using the cloud to support product innovation, product development, and engineering changed? How does that impact cloud adoption? Read the guest post in full in the Digital Transformation section of the Siemens PLM Community blog. Jim Brown recently shared a guest post on the Siemens' blog offering our experience on cloud adoption and starts a discussion about the variety of benefits that engineering software on the cloud offers. The post includes information from our prior research on using cloud for PLM, including this flowchart for companies to use when considering their cloud strategy.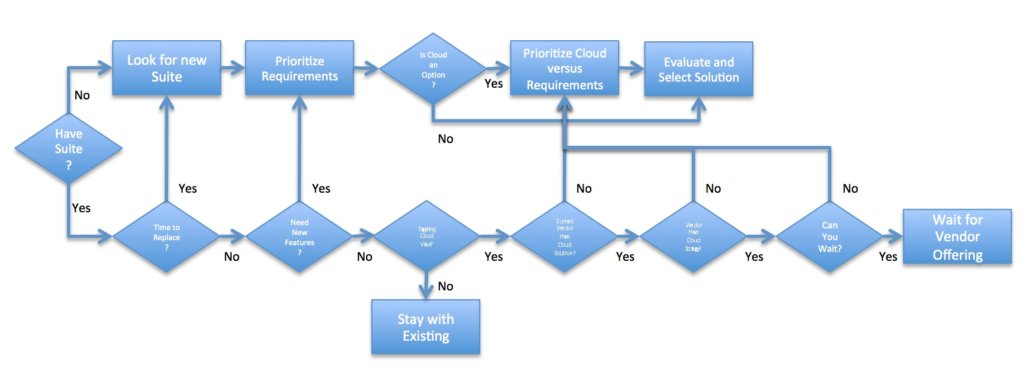
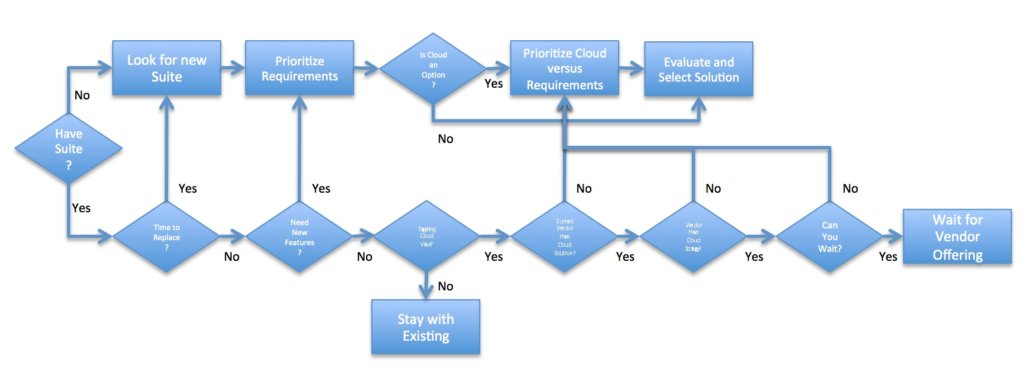
How do you empower engineers to design the best products possible?
Research from Tech-Clarity’s Revolutionizing Simulation For Design Engineers research report finds that design engineers lack confidence in design decisions 28% of the time. The research identifies the most common ways engineers deal with this uncertainty, its impact, and how to improve confidence. This research study, based on a survey of 195 companies, examines the design process and identifies top challenges that hold engineers back. The report reveals how to empower engineers with insight to improve product quality, lower cost, and accelerate time-to-market, all while developing more innovative products and the role that CAE can play.
Please enjoy the summary* below.
For the full research report, please visit our sponsor PTC (free of charge, registration required).
ENGINEERING DECISIONS CAN MAKE OR BREAK YOUR PRODUCTS
How do you empower engineers to design the best products possible?
Engineers want to design great products. Unfortunately, factors like increasing product complexity, competing design criteria, and knowing how design decisions impact other parts of the design make it hard. On top of this, ever-shrinking timelines mean engineers have their work cut out for them. Yet, exceptional engineering has become critical to success in today’s competitive global market.
WHAT’S MOST IMPORTANT FOR YOUR PRODUCT’S MARKET SUCCESS?
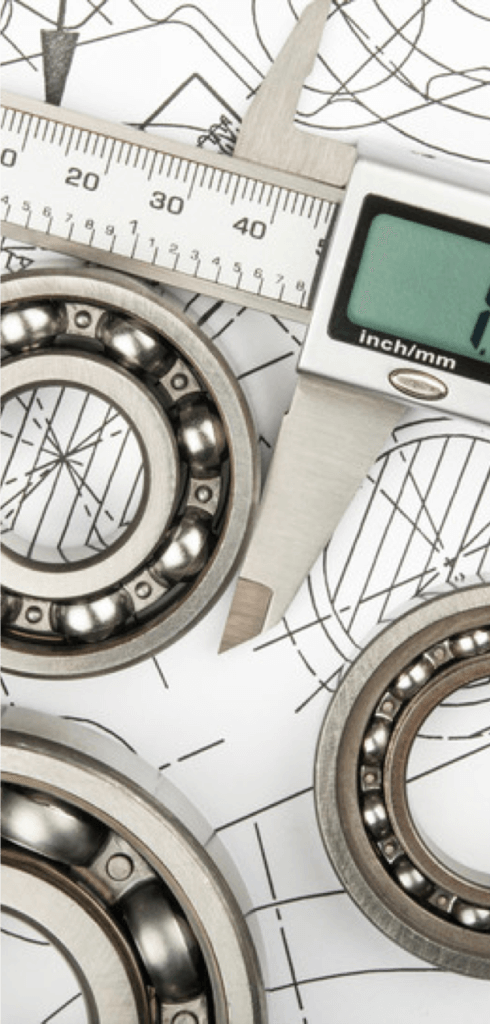
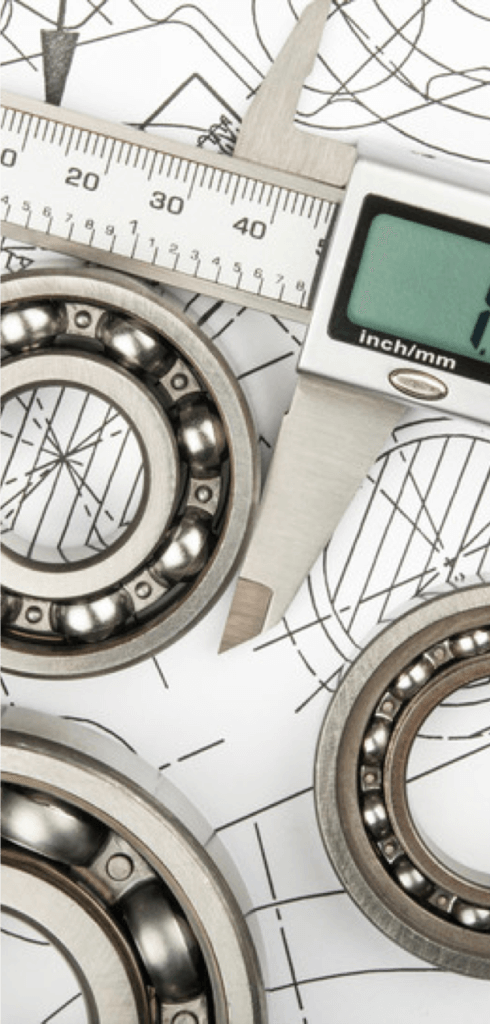
Product Quality
As companies face mounting pressure from global competitors, engineering criteria have become essential to competitively differentiate products. In fact, 80% of survey respondents believe that product quality is the most important product attribute to keep products competitive (see graph). Reliability and cost come next. This indicates customers have high expectations for quality and durability but don’t want to overpay. To be successful, companies should balance these criteria.
Engineering Decisions Are Critical – and Not Easy
Requirements for quality, reliability, and cost often conflict so balancing them is no small feat. Unfortunately, product complexity makes it hard for engineers to know the full impact of each design decision. Indeed, 76% of survey respondents rate design decisions that impact product competitiveness as ‘somewhat hard’ to ‘extremely difficult.’ This leads many engineers to overengineer, which unfortunately drives up cost.
Companies who can make this decision process easier will have an advantage.
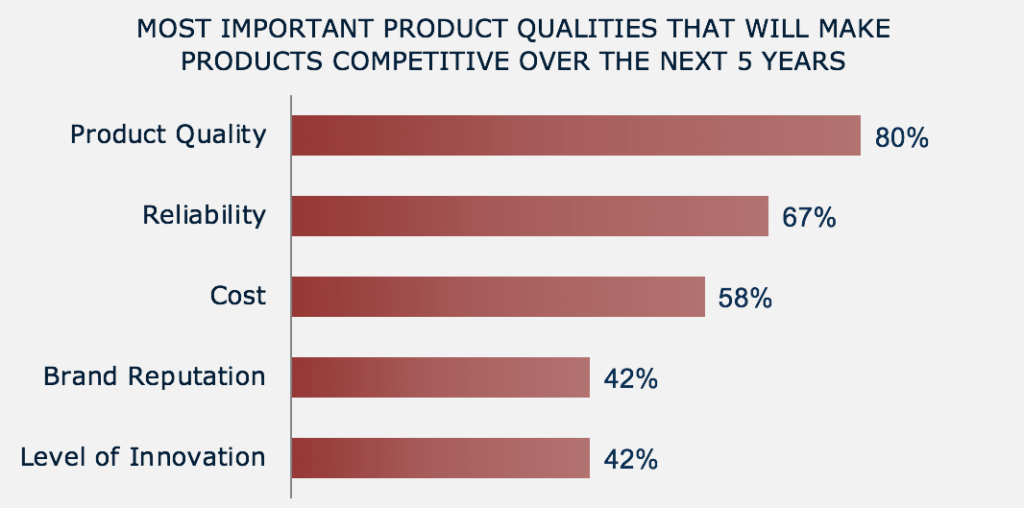
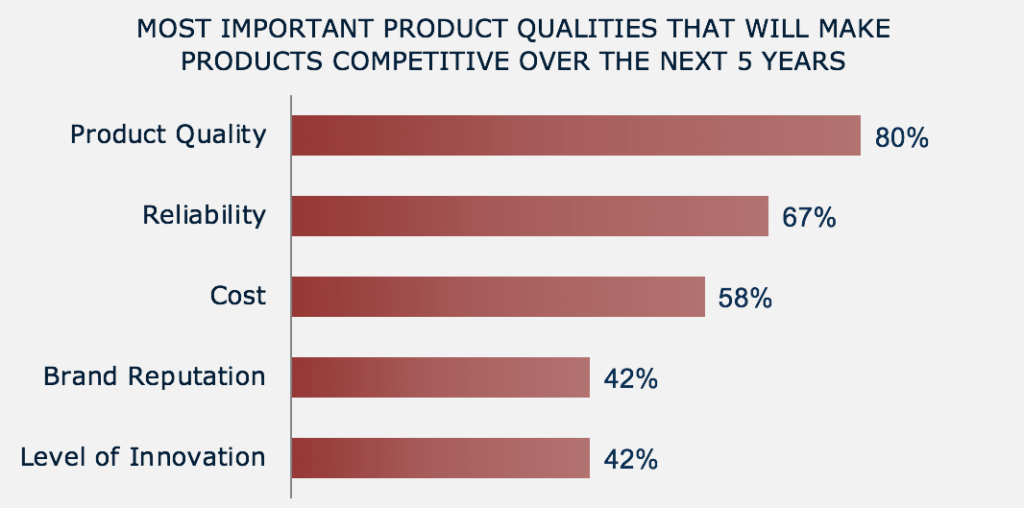
RECOMMENDATIONS TO IMPROVE ENGINEERING DECISIONS
To help improve engineering decisions, Tech-Clarity offers the following recommendations:
- Empower design engineers with simulation tools to help guide their decisions.
- Use simulation as early as possible during concept and design.
- Rely on simulation as a design tool to optimize the design and provide directional guidance.
- Consider new approaches to simulation that are tailored for design engineers and make setting up an analysis easier.
- Look for a simulation solution that can offer instant results.
*This summary is an abbreviated version of the report and does not contain the full content. A link to download the full report is available above.
If you have difficulty obtaining a copy of the research, please contact us using the “Contact” link below.
[post_title] => Revolutionizing Simulation For Design Engineers [post_excerpt] => [post_status] => publish [comment_status] => open [ping_status] => open [post_password] => [post_name] => revolutionizing-simulation-design-engineers [to_ping] => [pinged] => [post_modified] => 2024-01-20 00:23:15 [post_modified_gmt] => 2024-01-20 05:23:15 [post_content_filtered] => [post_parent] => 0 [guid] => https://tech-clarity.com/?p=7590 [menu_order] => 0 [post_type] => post [post_mime_type] => [comment_count] => 0 [filter] => raw ) [8] => WP_Post Object ( [ID] => 7596 [post_author] => 2 [post_date] => 2019-03-26 11:32:12 [post_date_gmt] => 2019-03-26 15:32:12 [post_content] =>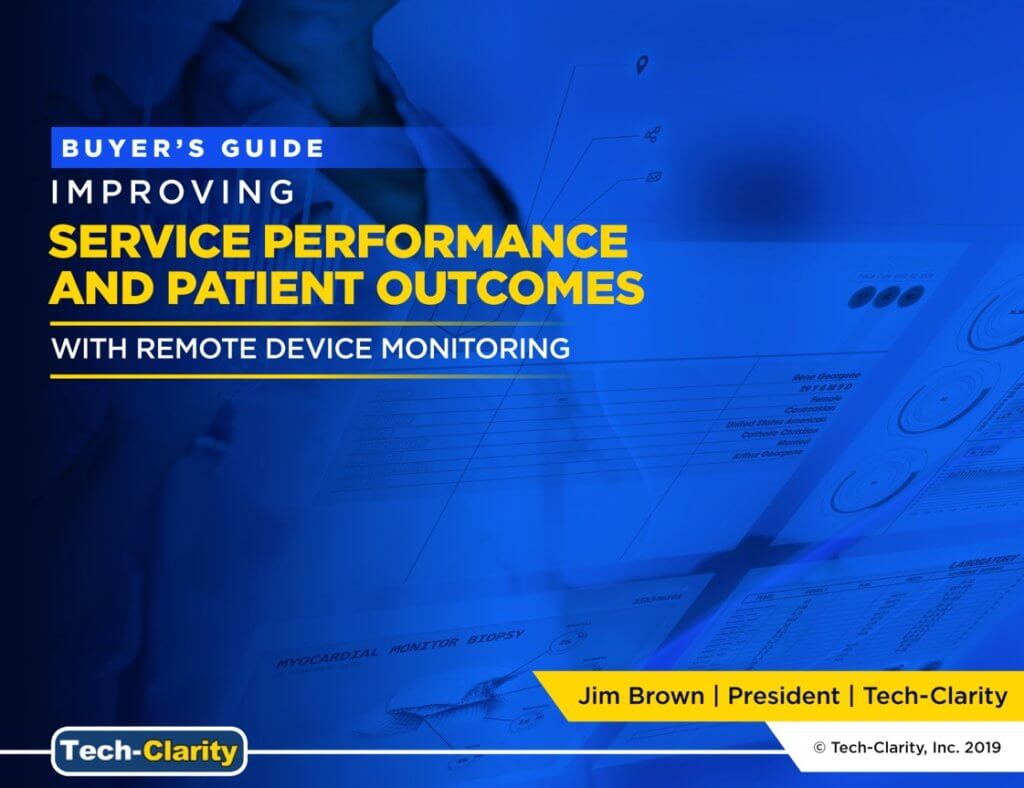
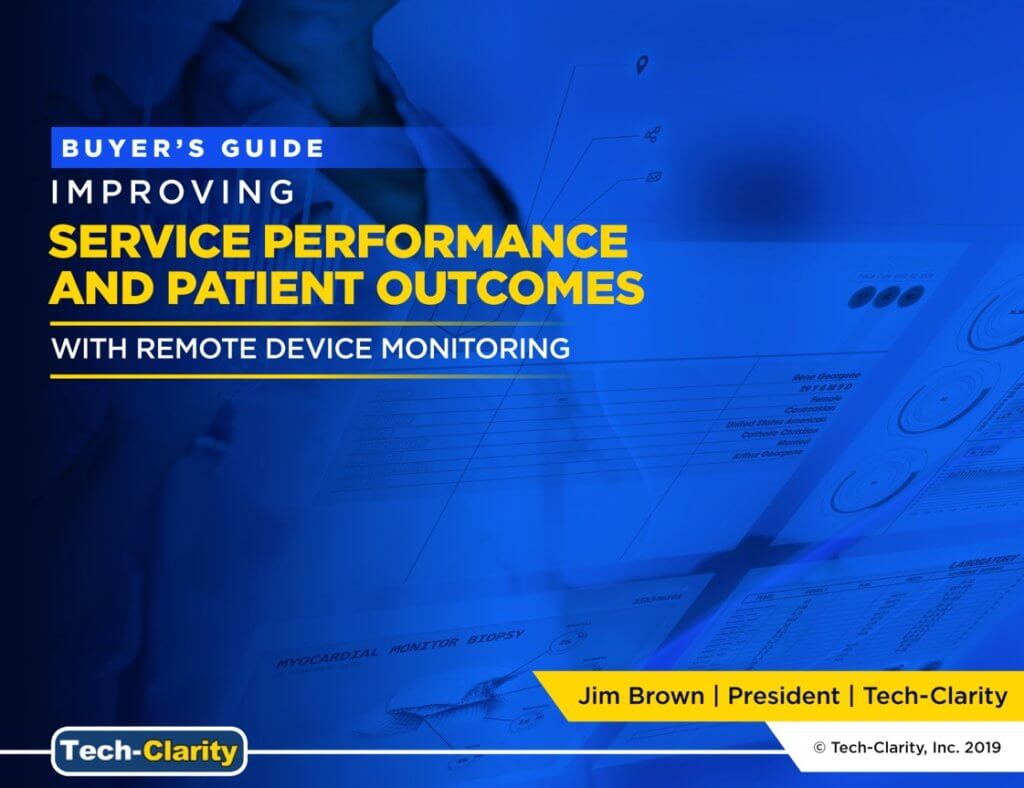
What should Life Sciences companies look for in a solution to help them simultaneously improve profitability and patient outcomes using remote device monitoring via the IoT?
Our new Improving Service Performance and Patient Outcomes with Remote Monitoring Buyer's Guide helps Life Sciences companies understand the business and social value of monitoring equipment with the IoT. It then offers evaluation criteria for companies to use as requirements to select a solution to achieve that value. The research also shares the experience of Varian Medical Systems and how they've used the IoT to drive improved service and customer relationships.
Please enjoy the summary below. For the full report, please visit our sponsor PTC (no charge, registration required).
Life Sciences Companies are Dramatically Improving Service by Digitalizing
Digitalization is changing the way innovative medical device, biotech, and related companies provide value and drive profitability. Research shows that one of the most compelling digital transformation opportunities is to revolutionize service, specifically:
- Deloitte finds1 that predictive maintenance can increase uptime and availability by 10-20 percent and reduce overall maintenance costs 5-10 percent
- Tech-Clarity’s Michelle Boucher shares2 that service is critical, that medical device downtime can impact lives, and that predictive maintenance can offer a significant advantage to minimize patient impact
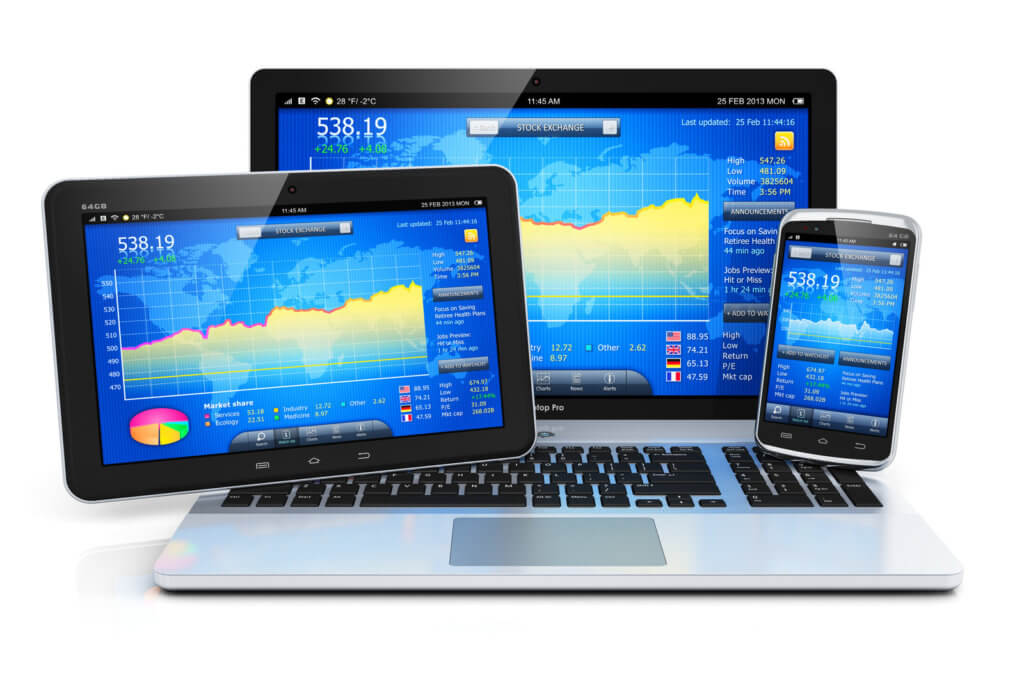
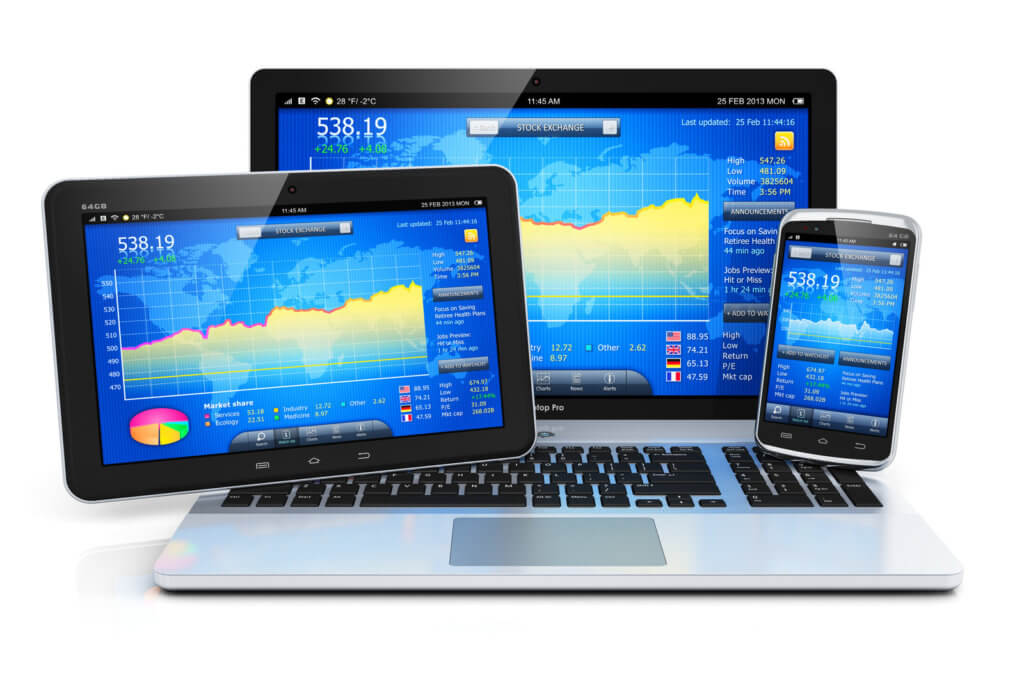
Table of Contents
- Improve Service ROI, Build your IoT Foundation for the Future
- Remote Monitoring Drives Service Performance
- Access Equipment and Device Data
- Communicate with Devices
- Leverage the Edge to Pre-Process Data
- Share Actionable Service Information
- Plan for Implementation and Adoption
- Select the Right Strategic Partner
- Next Steps
- Buyer’s Guide Checklist
- Acknowledgments
Improve Service ROI, Build your IoT Foundation for the Future
Industries are Digitally Transforming
Life Sciences companies have a tremendous opportunity to improve service operations and outcomes. At the same time, many are investigating how to benefit from the Internet of Things (IoT). Remotely monitoring medical equipment is a great way to accomplish both.
As our related Improving Service with Remote Monitoring Buyer’s Guide explains, a remote monitoring initiative allows companies to quickly achieve IoT value. In fact, the most common way that companies gain tangible ROI from IoT is through improved service. At the same time, it also paves the way for even more substantial benefits from initiatives like healthcare analytics.
Equipment Monitoring Has Proven Value
The IoT lets companies transform service to generate more – and more profitable – service revenue. They do this by moving from reactive to proactive to predictive service, and leveraging advanced technologies like AI, machine learning, and big data analytics. They can also adopt new service delivery processes like remote service. But the most common first step is reducing cost of service through remote monitoring.
Next Steps
Get Started
Leveraging the IoT can help companies improve service for themselves and their customers by reducing cost and transitioning to proactive and predictive service. Remote monitoring allows companies to identify and resolve issues remotely, providing faster service and increased uptime while reducing the cost of truck rolls and putting service technicians on site.
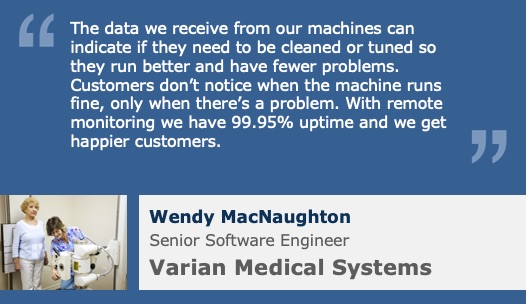
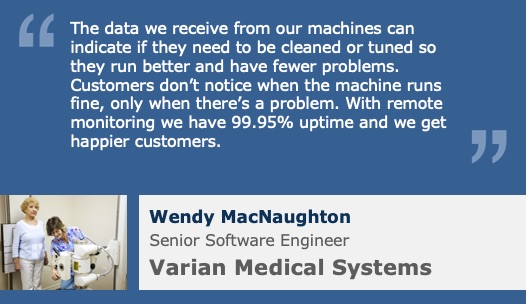
It can go beyond cost savings to create a new source of revenue from paid upgrades or remotely enhancing equipment capabilities or permissions by “unlocking” enhanced capabilities via a subscription. It also offers Life Sciences companies an opportunity to help ensure devices are available and operating optimally to serve patient needs.
Improve Service and Patient Outcomes
Medical device, biotech and other life science innovators embarking on a remote monitoring initiative to improve service should look for the capabilities outlined in the sections of this guide to help ensure they get the value they seek. In addition, they can use the following checklist as high-level criteria to compare offerings.
*This summary is an abbreviated version of the report and does not contain the full content. A link to download the full report is available above.
If you have difficulty obtaining a copy of the report, please contact us using the "Contact" link below.
- Deloitte, “Making Maintenance Smarter”
- Tech-Clarity, “Medical Device Manufacturer’s Selection Guide for 2018”
[post_title] => IoT Medical Device Monitoring (Buyer's Guide) [post_excerpt] => [post_status] => publish [comment_status] => open [ping_status] => open [post_password] => [post_name] => medical-device-iot [to_ping] => [pinged] => [post_modified] => 2022-11-14 22:27:56 [post_modified_gmt] => 2022-11-15 03:27:56 [post_content_filtered] => [post_parent] => 0 [guid] => https://tech-clarity.com/?p=7596 [menu_order] => 0 [post_type] => post [post_mime_type] => [comment_count] => 0 [filter] => raw ) [9] => WP_Post Object ( [ID] => 7469 [post_author] => 2572 [post_date] => 2019-03-21 14:45:28 [post_date_gmt] => 2019-03-21 18:45:28 [post_content] =>
Tech-Clarity's Preparing for EU MDR explains the impact of the EU MDR on your product data. While complying to the EU MDR may require an investment, taking the steps now to prepare your product data will not only support EU MDR compliance, but will position your company to support future regulatory requirements. In addition, these investment will also lead to greater efficiencies that will enable you to have more bandwidth to focus on innovation and quality. This report provides recommended steps to help you prepare and how software technology will make it easier.
Please enjoy the summary* below.
For the full eBook, please visit our sponsor PTC (free of charge, registration required).
The EU MDR: A Challenge and an Opportunity
The reasons for the new regulation are admirable. As stated, "This Regulation aims to ensure the smooth functioning of the internal market…[it] sets high standards of quality and safety for medical devices in order to meet common safety concerns..." Essentially, the EU wants to ensure that medical devices are safe, high quality, meet stated expectations, and improve patient health. The EU also wants to take advantage of the technological and scientific progress made over the last 20 years.
Better Devices, but There’s Work to Do
The Opportunity
While the scope of the new regulation is quite broad, its implications are especially significant for product teams who will – either directly or behind the scenes – participate in the product submissions process.
This eBook shares advice to prepare product data for regulatory submissions through a programmatic and extensible approach. In this view, EU-MDR compliance serves as a catalyst for implementing sound product design, change and configuration control best practices across your product development lifecycle.
Recommendations
To establish a foundation to comply with the EU MDR, medical device companies should look to adopt a product-centric approach. Based on this research and our experience, we recommend that medical device companies do the following to support the EU MDR and a product-centric approach:
- Use the EU MDR as an opportunity to improve product related processes to improve efficiency and create more bandwidth to focus on innovation and device quality.
- To meet the increased data requirements, consider a product-centric approach. A product-centric approach uses product data, specifically CAD models, as the primary design artifact rather than a PDF. This approach establishes traceability and breaks down silos between the engineering data and documentation, making it easier to collect the data for EU MDR submissions.
- A PLM system will support this a product-centric approach can serve as a foundation for EU MDR, a PLM system supports the digital thread to tie product information, decisions, and history together in a structured, integrated way that captures product innovation and knowledge throughout the product lifecycle.
To adopt a product-centric approach, consider the following steps:
- Obtain Executive support: An Executive is required to support adoption across multiple departments and make the initiative a priority.
- Create a product data hub: Your data needs to be accessed from a central location with traceability across the lifecycle. You can accomplish this with either a single database or a data hub that connects to multiple data sources. A PLM system with a connection platform will enable the latter option.
- Structure and manage data: Structure your product data so that it is centralized and you can find it. Consider starting with your CAD data.
- Identify a cross-functional team: Take advance of the collective expertise of your teams to help identify bottlenecks and opportunities for improvements.
- Automate Product Lifecycle Processes: Map out your current processes and then how you would like them to work. Look for opportunities for technology to automate the workflow to minimize the amount of manual work.
*This summary is an abbreviated version of the eBook and does not contain the full content. A link to download the full eBook is available above.
If you have difficulty obtaining a copy of the research, please contact us using the “Contact” link below.
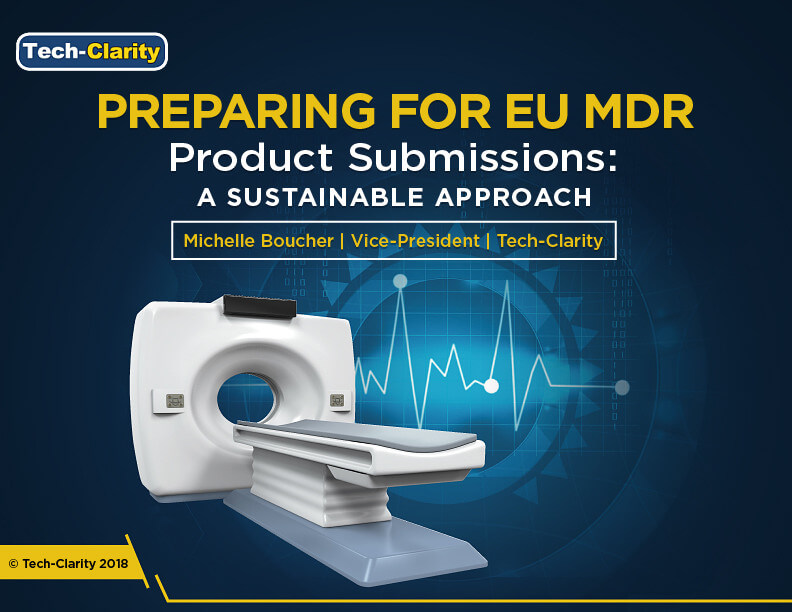
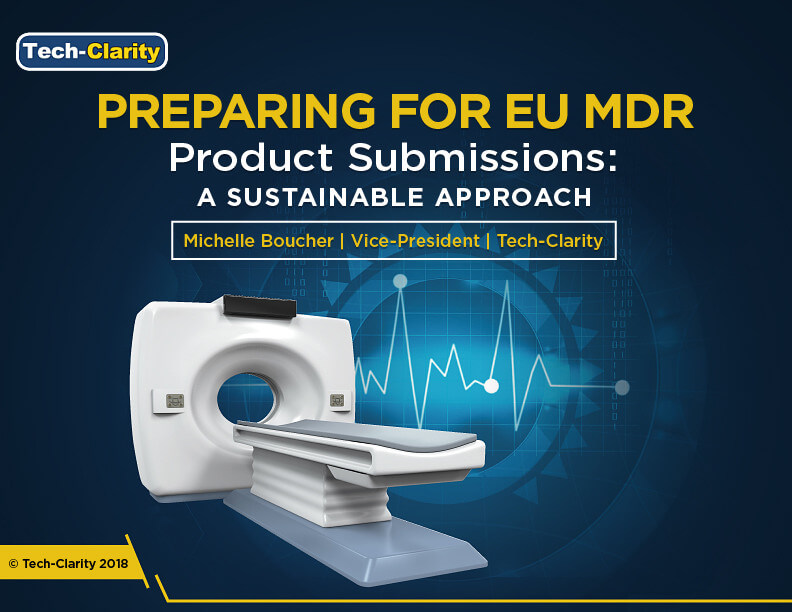


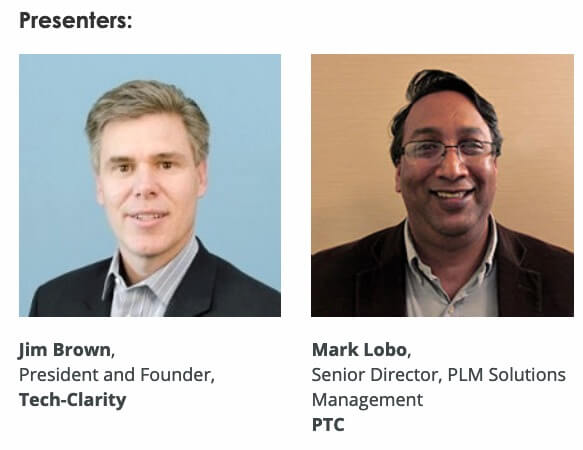
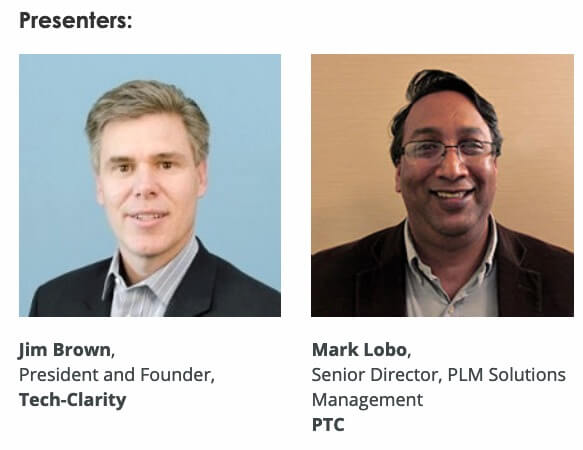
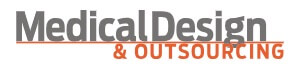
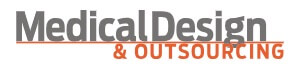


Event Synopsis
In the IoT era, service transformation is the new frontier of innovation. For life sciences and medical device innovators, remote monitoring is the superpower that unlocks service value through reduced service costs, improved customer satisfaction, and greater insight. When it comes to choosing the best remote monitoring software, medical device makers have many factors to consider. Fortunately, you don’t have to make the decision alone. In this upcoming February 28 discussion, Jim Brown and Anthony Moffa put remote monitoring under the microscope. Hear the crucial steps to choosing a remote monitoring solution and learn:- The three stages of connected services maturity.
- The critical role of software analytics – and what to look for.
- How to make the most of your IoT investment from device design all the way through to maintenance and service.
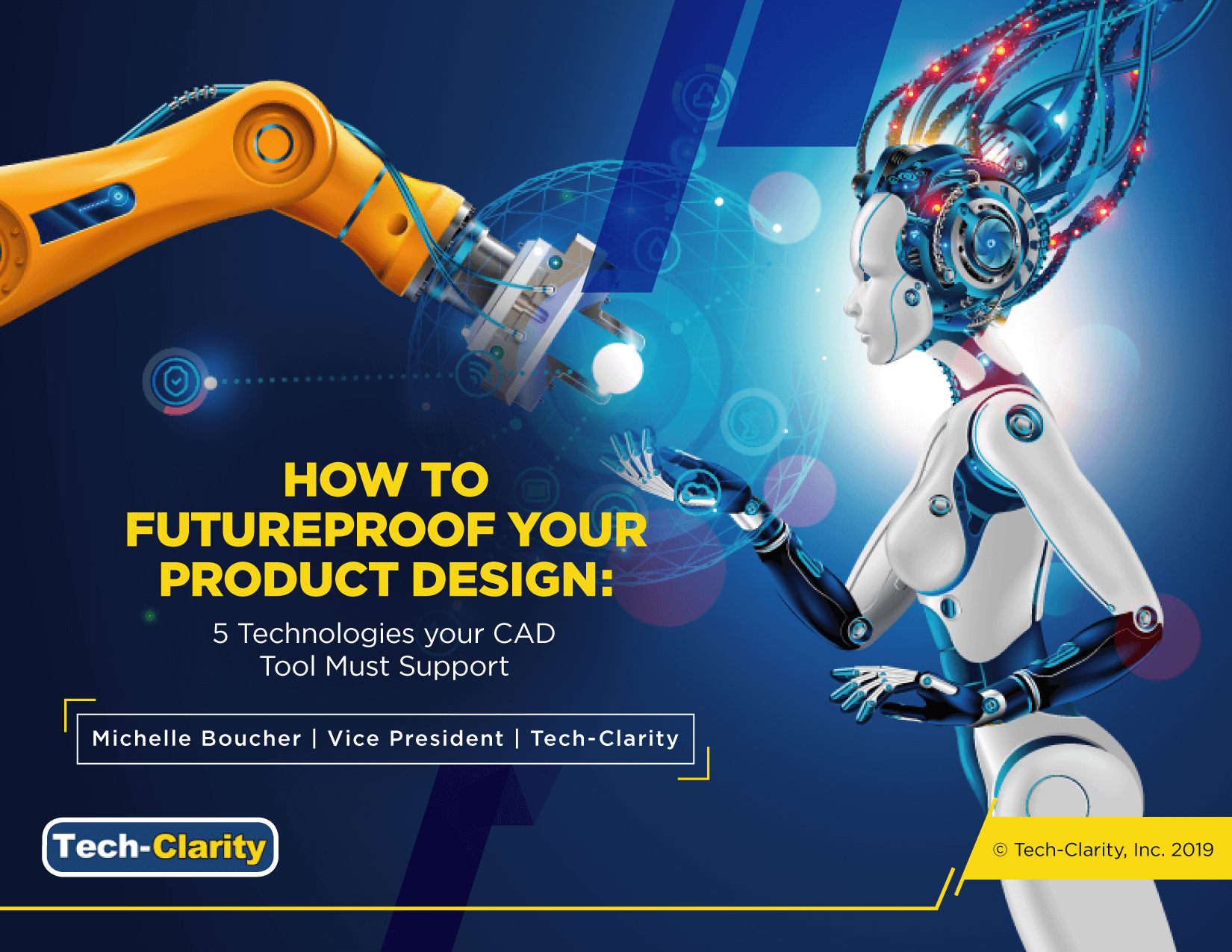
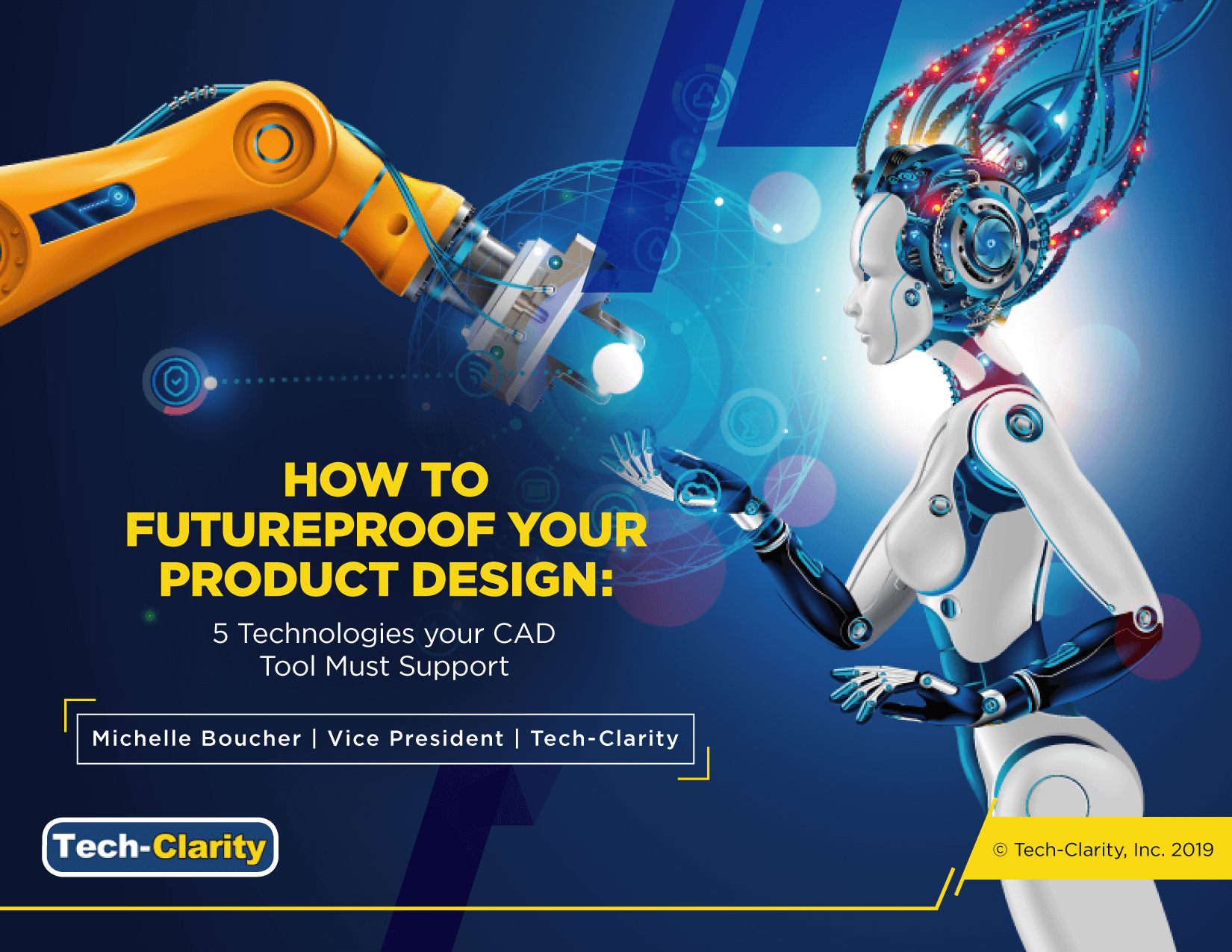
Is Your CAD Tool Ready for the 2020s?
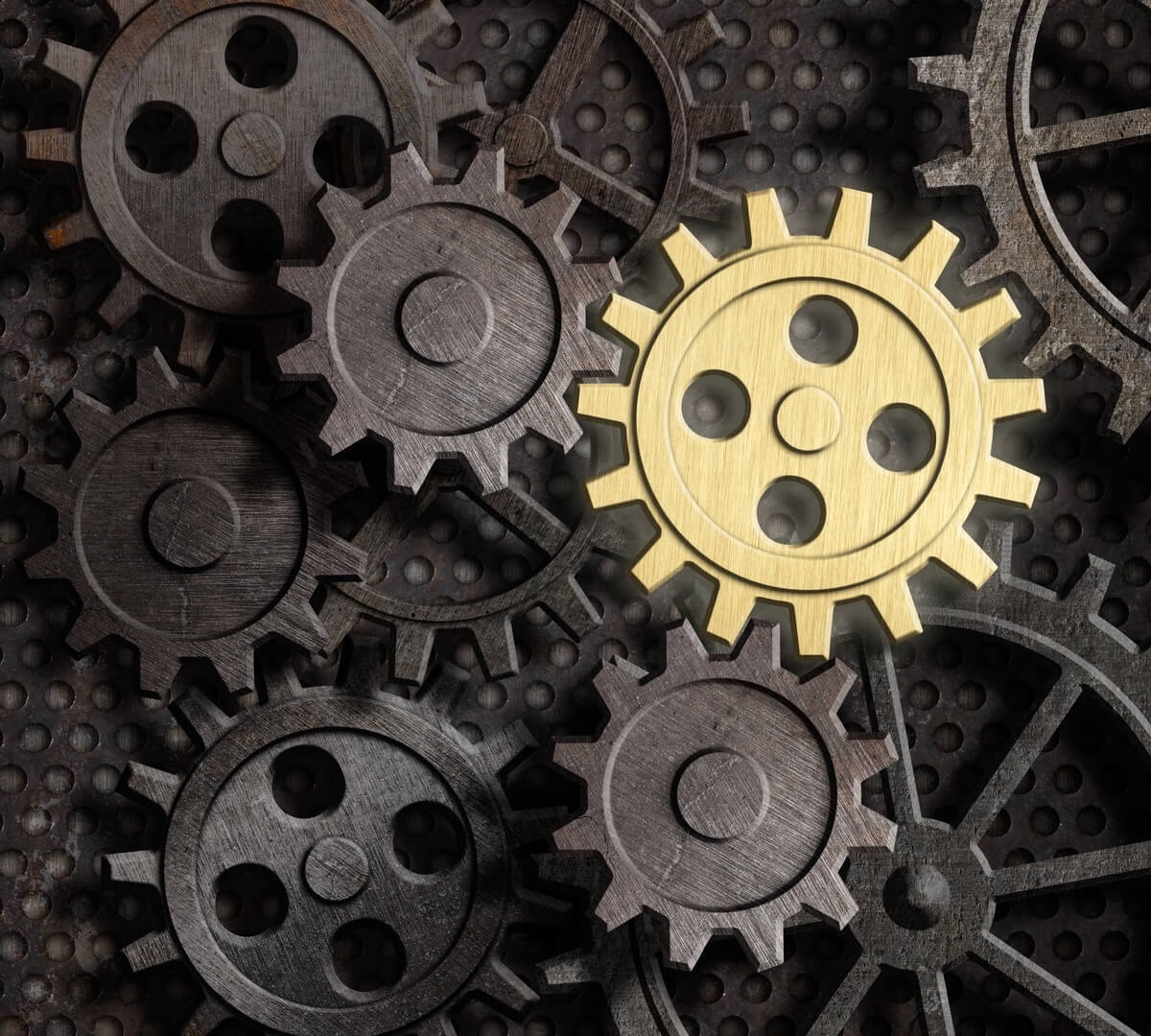
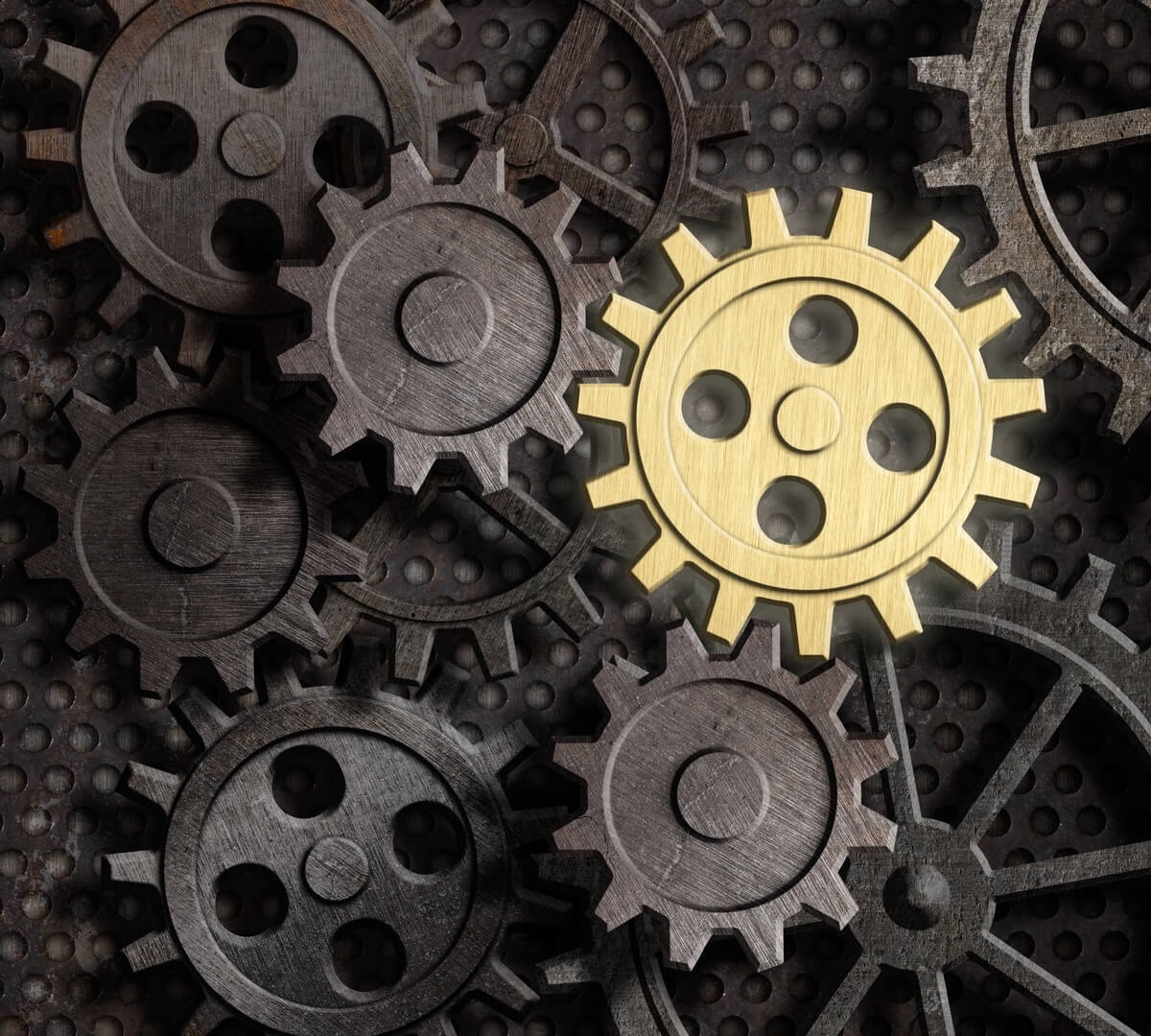
How Will You Stay Competitive in the 2020s?
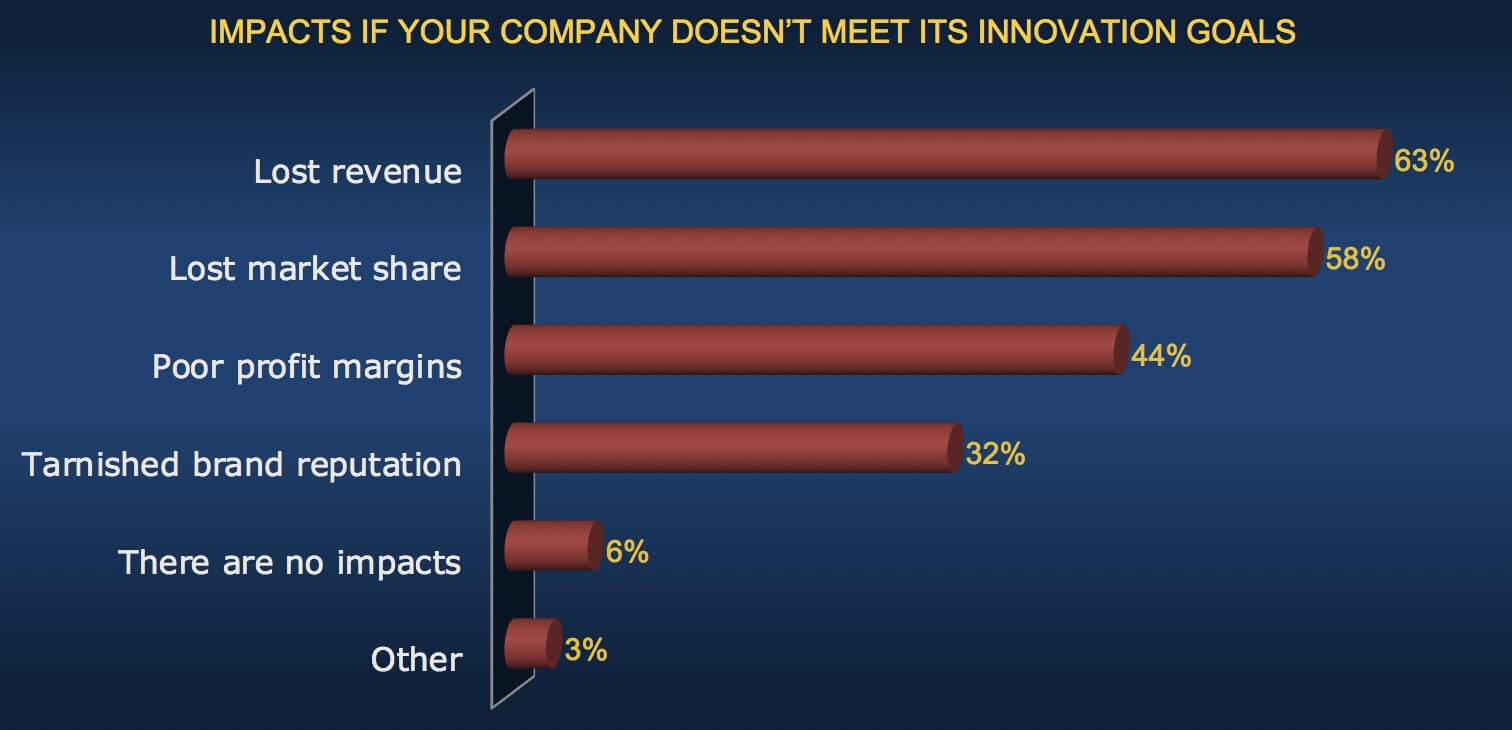
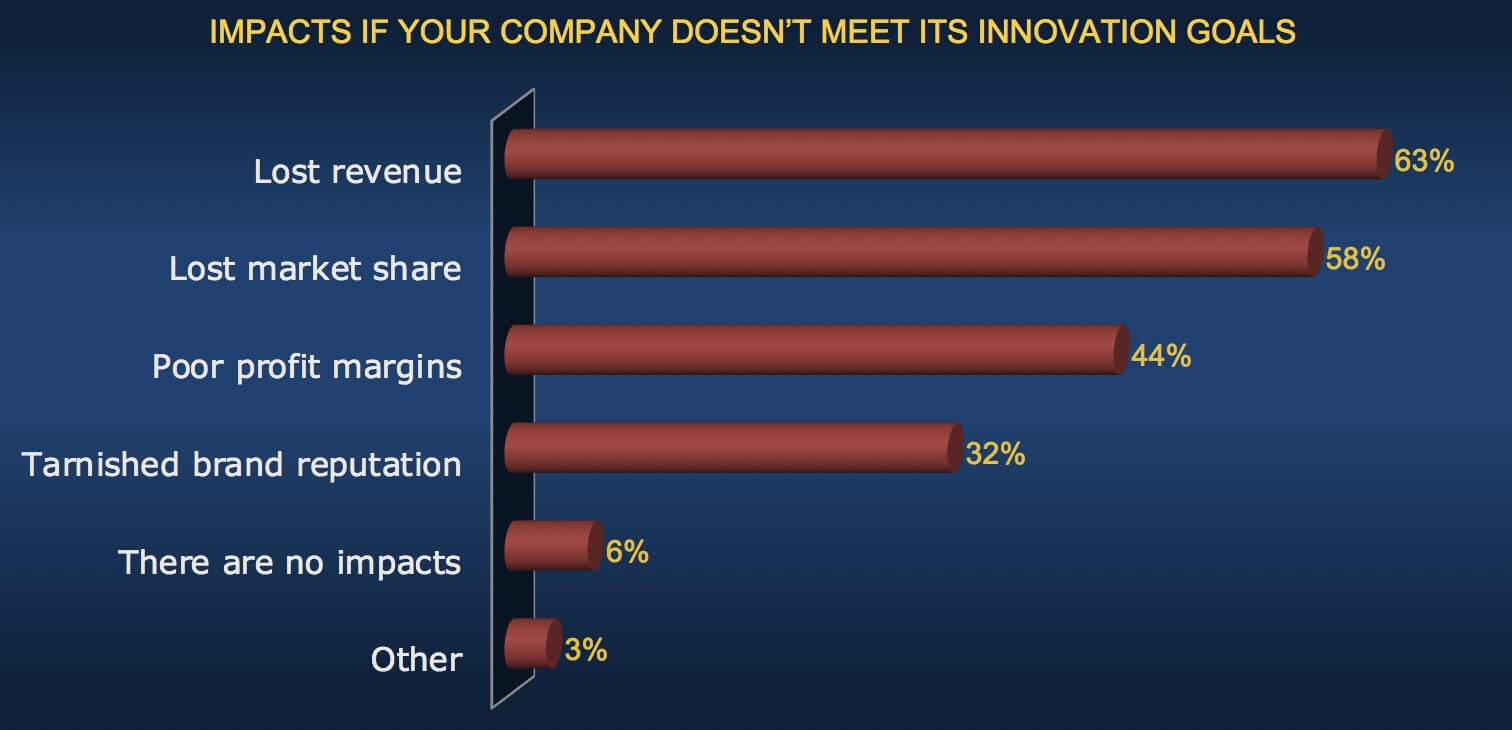
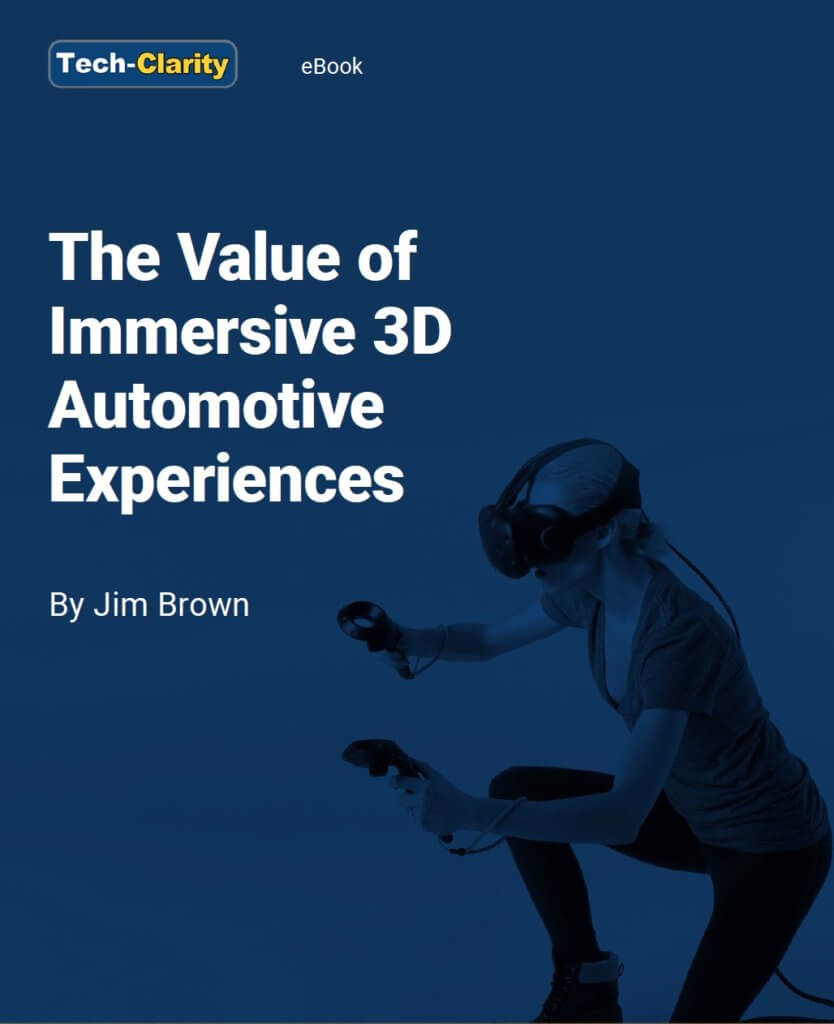
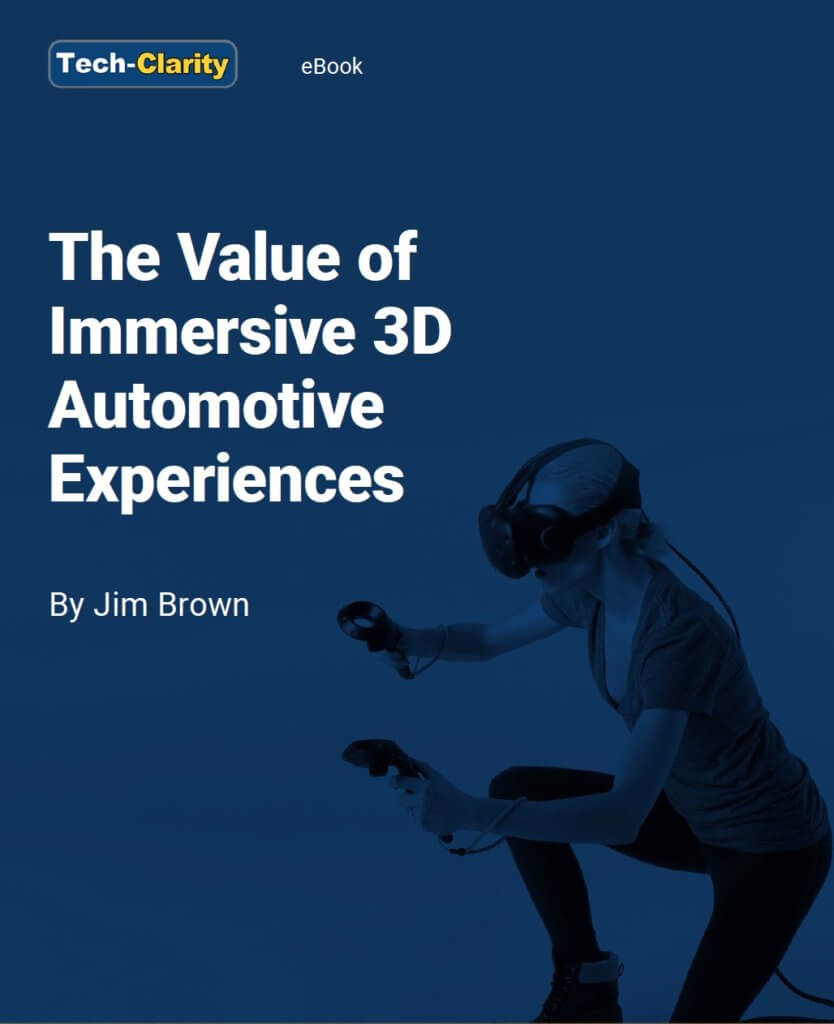
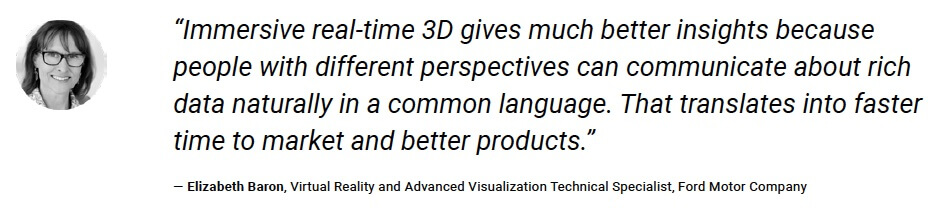
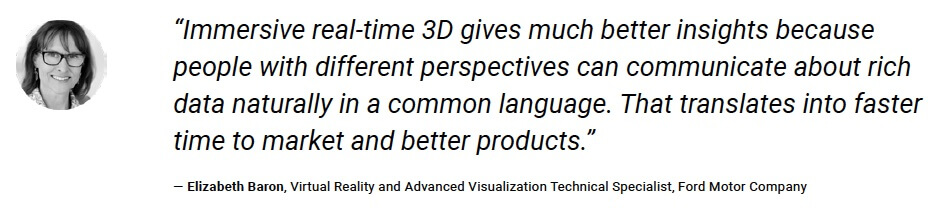
Table of Contents
- Automotive Innovators Gaining Value from Real-Time, Immersive 3D
- Add Excitement and Efficiency to Marketing and Sales
- Increase Insight and Iteration in Product Innovation and Design
- Add Realism and Immersion to R&D and Engineering
- Boost Productivity and Quality in Manufacturing Engineering
- Reduce Constraints and Add Interest to Training
- Unleash Innovation and Explore Additional Uses
- Roadblocks and Speed Bumps Removed
- The Automotive Industry Is Hitting the Accelerator
- Lead, Follow the Leaders, or Fall Further Behind
- About the Author
- Experience Automotive Emotion in Action
A car represents a unique blend of advanced technology and consumer desires, and automotive marketing campaigns are tailored to evoke both rational and emotional responses from customers. Auto companies and advertising agencies have become highly adept at showing lifelike driving experiences. Today’s customers have the opportunity to experience a car in a spectacular setting, even before a single unit has been produced.
Innovators Taking 3D Beyond the Basics
The innovators are doing even more, gaining value by sharing interactive, real-time 3D experiences across the enterprise and the supply chain. They can create buyer excitement with fully immersive configurators that customers can interactively explore in 3D. They can collaborate on interior designs in global, virtual reality design reviews to innovate and catch errors early. They can analyze the impact of manufacturing engineering decisions on perceived quality by viewing fit and finish in real-time under a variety of lighting conditions. They can even interactively experience airflow simulation results by stepping inside a virtual smoke stream. Or, they can train operators to assemble engines in augmented reality before the line is built and without expensive mockups.
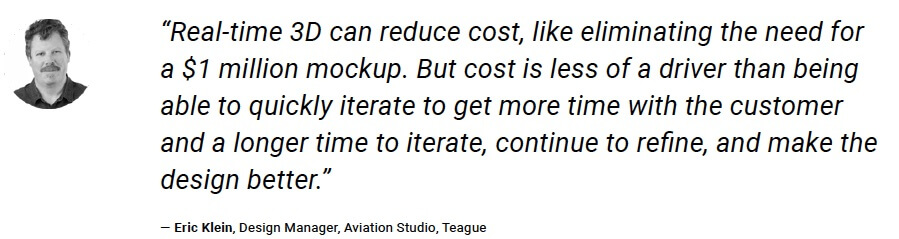
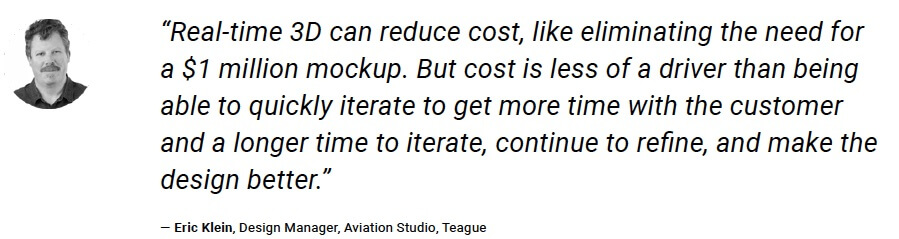
Opportunities Span the Automotive Enterprise
The opportunities are extensive. This eBook examines the benefits along multiple dimensions, including the following:
- Marketing and Sales
- Product Innovation and Design
- R&D and Engineering
- Manufacturing Engineering
- Training
The eBook shares valuable insights from interviews with industry leaders Ford and Teague, and highlights from a recent industry conference with speakers from Audi, EDAG, and Team One. It concludes with some valuable insights to help auto companies better understand the opportunities and enabling technologies available to help them take advantage of real-time, interactive, immersive 3D.
Real-time 3D Is Coming, Ready or Not
The value of using real-time, immersive 3D in the automotive industry is compelling. The leaders will continue to innovate and expand on their lead. More importantly, lowered barriers to entry mean more companies will be able to take advantage of real-time 3D benefits, including startups that are embracing digitalization in order to displace industry veterans. Immersive, real-time 3D is quickly becoming a critical part of the modern technical toolkit for the automotive industry. We believe the innovators will continue to push forward, while those that don’t adopt immersive 3D technologies will fall further behind.
Getting Started
It’s time for companies to find an opportunity or a problem and address it. Companies should start small with a proof of concept (POC) as a first step. The POC, however, should provide value and not just serve as a learning exercise. Create value, learn, and build on that knowledge with next steps. Companies can choose a project similar to the ones described here, leveraging the experience of the pioneers, or unlock the creativity of their own organization by, for example, holding a “hackathon.”
The Time to Act Is Now
If your company has been waiting to get involved with real-time 3D, now is the time. The costs have dropped tremendously. The time required to build valuable solutions in 3D is much lower. Specialized development resources are now ready to go. Computing power is available onsite or via the cloud. Real-time, immersive 3D use cases have never been more in reach. Companies that adopt real-time 3D can still gain an advantage, while automotive companies can reap significant benefits in multiple dimensions of their business:
- Marketing and Sales
- Product Innovation and Design
- R&D and Engineering
- Manufacturing Engineering
- Training
- Autonomous Vehicle Training
- VR Analytics
During this on-demand webinar, Tech-Clarity's Michelle Boucher and Anshuman Prakash from Siemens share perspectives on better requirements management. They also provide advice to make the process easier. During the webinar, you will learn:
- How to address common challenges that lead to missed requirements
- How to easily assess the impact of proposed design changes
- What strategies can keep budgets in check when requirements change
- How to manage requirements across mechanical and electrical domains
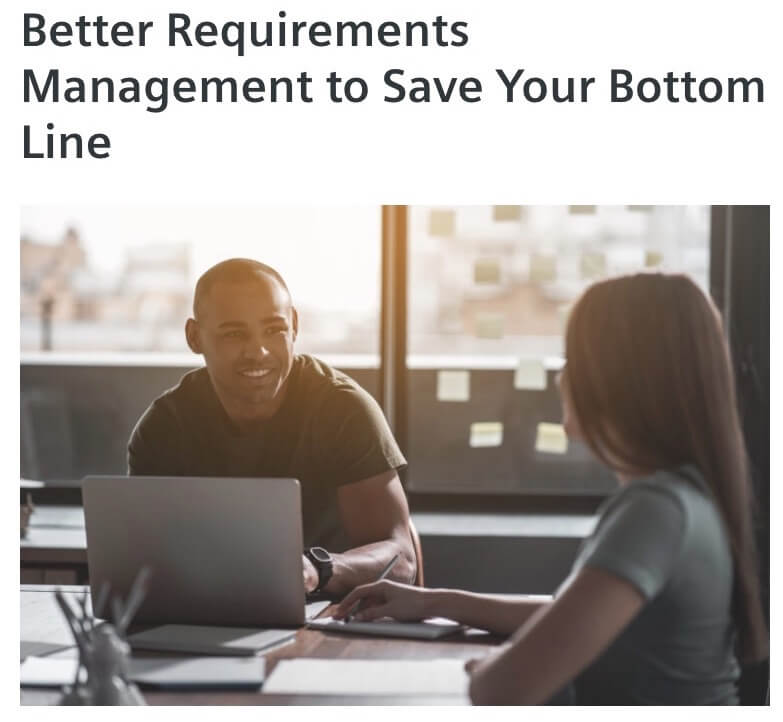
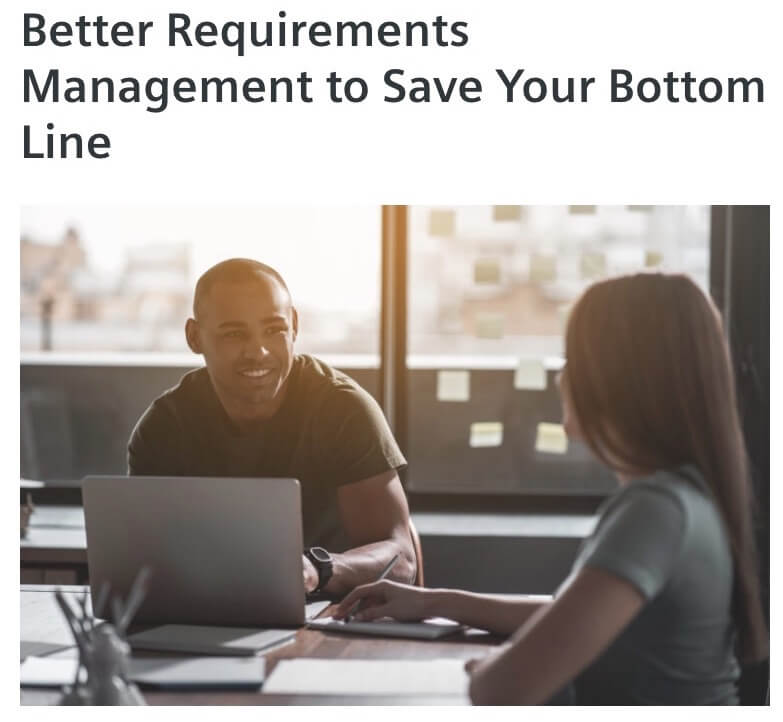
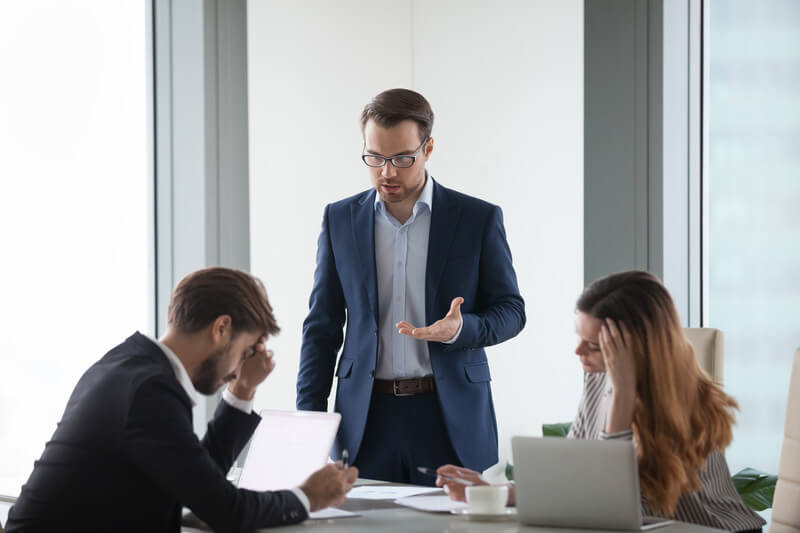
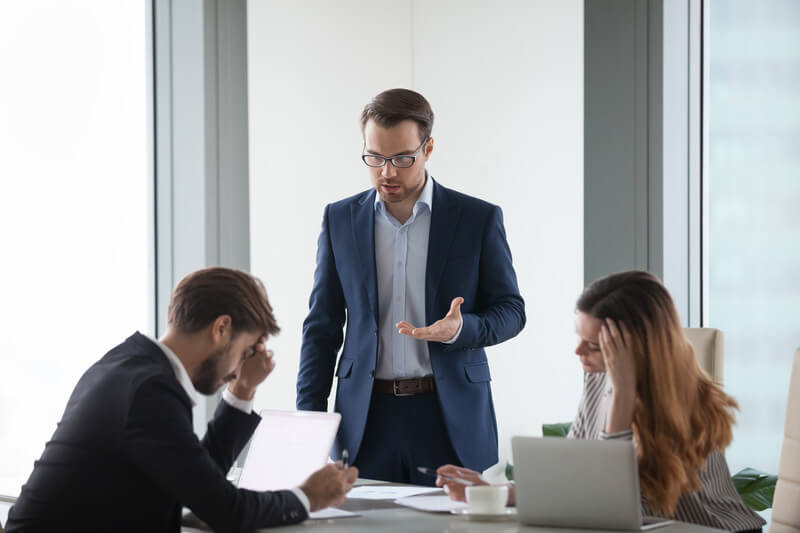
Requirements Management Is Critical to Project Success
When PMI dug deeper into the reasons for project failures, they found that the top three issues include changing priorities, changing objectives, and inaccurate requirements gathering. While these problems create substantial challenges, they can become easier to manage with improvements to requirements management. Requirements management has a significant impact on project performance. Getting it right can mean the difference between a successful new product development project or a failure.New Ways of Working Are Needed
So how do these issues impact requirements management? The critical point is adapting to change, which companies must do to survive in today's competitive global economy. For a new product development project, getting the design right starts with the requirements. However, markets are evolving so rapidly, no wonder there are changing priorities and objectives. Disruptive technologies are bringing new sources of innovation and changing how we do business. Alternative sources of funding like Kickstarter have lowered the barriers to entry for start-ups, and the internet and cloud technology have expanded companies’ global reach so that even small companies can operate like larger ones. Responding to these trends impacts requirements, but if you cannot adapt quickly, you risk losing market share. With today's changing market dynamics, old ways of working may no longer be enough. You may need to find new ways of working to be competitive Continue to the Siemens Solid Edge blog for the full post. For more information on requirements management, access the on demand webinar titled, Better Requirements Management to Save Your Bottom Line. (registration required). [post_title] => Better Requirements Management: An Immediate Payback (Guest Post) [post_excerpt] => [post_status] => publish [comment_status] => open [ping_status] => open [post_password] => [post_name] => better_requirements_management [to_ping] => [pinged] => [post_modified] => 2022-11-14 22:26:06 [post_modified_gmt] => 2022-11-15 03:26:06 [post_content_filtered] => [post_parent] => 0 [guid] => https://tech-clarity.com/?p=7382 [menu_order] => 0 [post_type] => post [post_mime_type] => [comment_count] => 0 [filter] => raw ) [16] => WP_Post Object ( [ID] => 7369 [post_author] => 2 [post_date] => 2019-01-03 08:23:54 [post_date_gmt] => 2019-01-03 13:23:54 [post_content] =>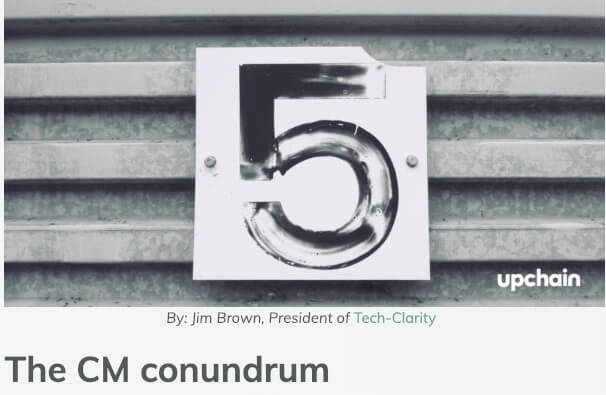
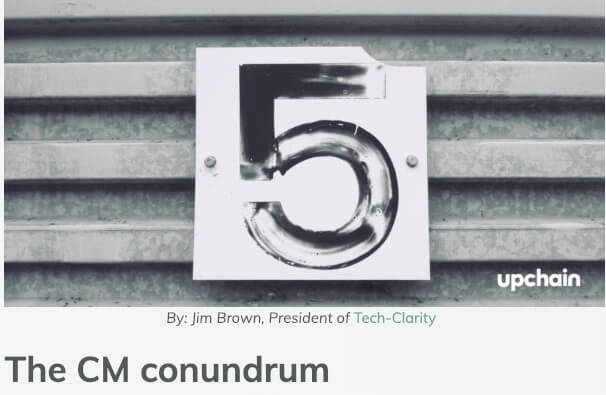
Introduction
Working with contract manufacturers can be one of those “you can’t live with them, you can’t live without them” scenarios. Leveraging contract manufacturing organizations (CMO) is a reality for many companies and can be a great way to jumpstart a product when you don’t have the time or capital to bring up your own plants. What’s more, manufacturers with complex, digital products like telecommunications or other electronic devices may not have another viable option. They simply can’t get from prototype to scale on their own given the required time, money, and manufacturing knowhow. But working with third parties can be frustrating, particularly if you’re used to making all of the calls and you’re new to the process. It doesn’t seem like it should be so hard, but there’s a lot that can go wrong – and it usually does. You may find yourself asking some frustrating questions, but there are ways to manage the inherent challenges and be successful. Let’s explore five questions you may find yourself asking during your CMO partnership, and what you can do about them. Continue to the upchain site for the full post. [post_title] => 5 Frustrations of Working with Contract Manufacturers (guest post) [post_excerpt] => [post_status] => publish [comment_status] => open [ping_status] => open [post_password] => [post_name] => contract-mfg-challenges [to_ping] => [pinged] => [post_modified] => 2022-11-14 22:25:36 [post_modified_gmt] => 2022-11-15 03:25:36 [post_content_filtered] => [post_parent] => 0 [guid] => https://tech-clarity.com/?p=7369 [menu_order] => 0 [post_type] => post [post_mime_type] => [comment_count] => 0 [filter] => raw ) [17] => WP_Post Object ( [ID] => 7356 [post_author] => 2 [post_date] => 2018-12-13 09:30:15 [post_date_gmt] => 2018-12-13 14:30:15 [post_content] =>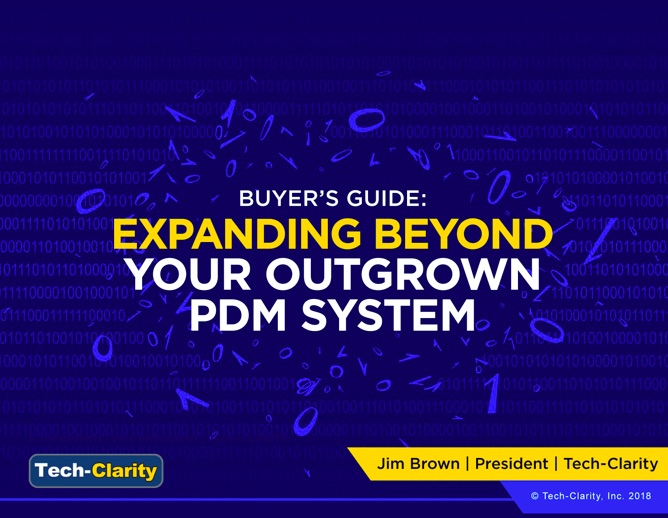
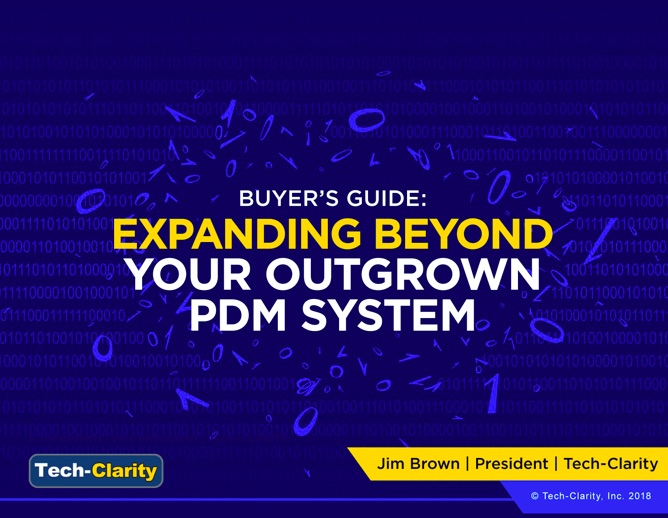
Table of Contents
- What to do When You've Outgrown Your PDM
- Introducing the Buyer’s Guide for a More Capable PDM Solution
- Top Ten Signs You've Outgrown Your PDM System
- Extending the Control - Access - Share Basics
- Going Beyond PDM Basics
- Extended PDM Requirements
- New Considerations for Service, Vendor, and Special Considerations
- Next Steps
- About the Author
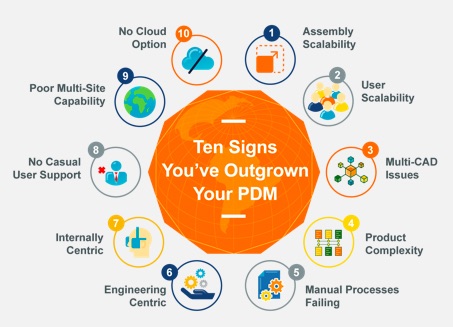
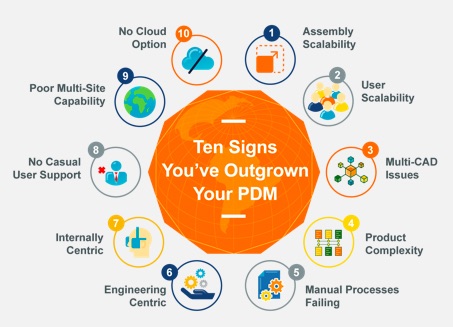
Introducing the PDM Buyer’s Guide
Exceeding the Limits of Basic PDM Although our PDM Buyer’s Guide recommends “considering both current and future needs” when evaluating solutions and “building a foundation to grow on,” there are many valid reasons companies end up outgrowing their system:- Product complexity has increased
- Product development complexity has grown
- Business has expanded
- Business has globalized
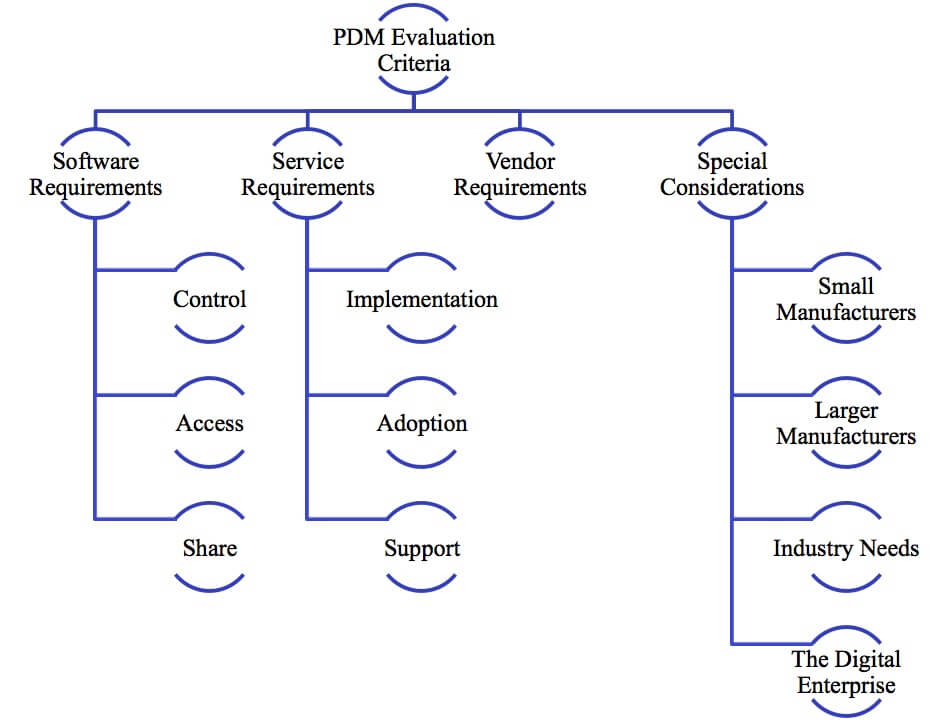
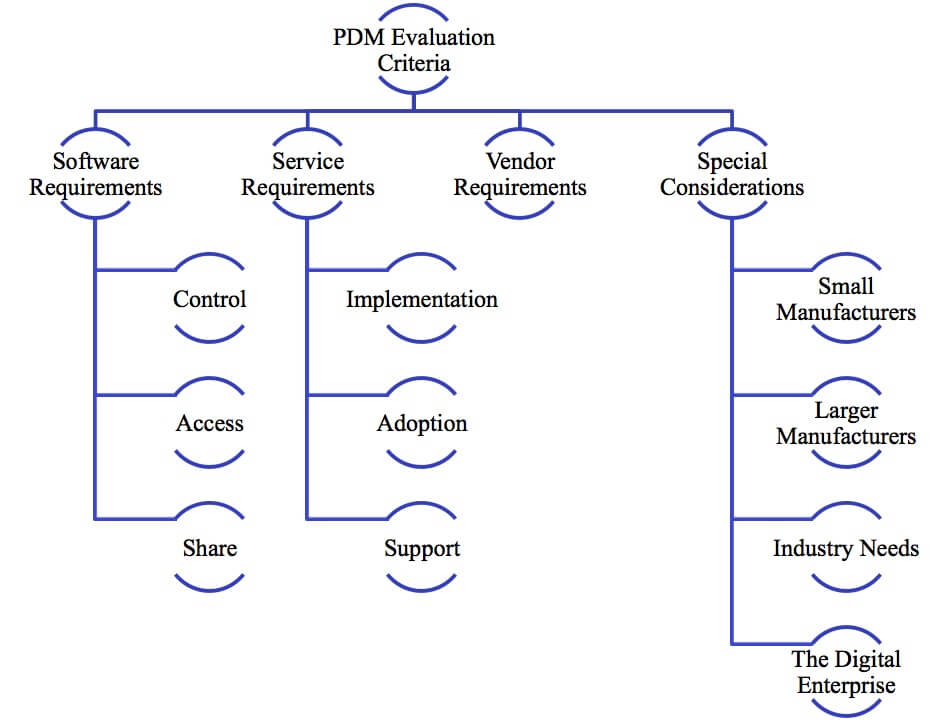
Next Steps
Extend Basic PDM Investment to Increase Value Companies that have outgrown their PDM system can leverage their existing investment in organizing CAD files and adopt a new system to take advantage of more mature capabilities. Our research shows the value of the transition. Top Performing companies are more likely to have structured, collaborative systems like a more mature PDM or a PLM system. It’s time to go beyond EDM or basic PDM systems to help unlock innovation and improve product development efficiency. The requirements set forth in this guide can help frame the software selection and decision-making process to find the right system. Companies should start by focusing on the highlighted areas in the Control - Access – Share sections. This is where less capable, “generalist” file management solutions fall short because they lack an intimate understanding of processes for product innovation, product development, engineering, and support. Companies should also consider the requirements in the four new areas discussed in this guide. Create the Foundation for Further Growth As companies adopt a more advanced PDM system, it’s important to give themselves room to expand to more mature capabilities over time. For many companies, that involves adopting advanced PDM capabilities as part of a more comprehensive PLM system to address additional aspects of products, process, departments, and product lifecycles. These are the key areas that expand PDM to PLM, and areas that PLM vendors continue to expand their solution scope. Consider a Platform for the Greatest Potential Value One good option manufacturers should consider to meet extended PDM needs is adopting a Product Innovation Platform (PIP). A PIP offers manufacturers the ability to expand PDM today and create room to grow as they are ready to adopt more, or more mature, processes. A PIP with a modular approach will allow them to scale and add capabilities as they need them. Some common areas that manufacturers extend include:- Requirements Management
- Quality Management
- Product Costing
- Product Compliance and Sustainability
- Manufacturing / Bill of Process
- Service Lifecycle Management
- Systems Engineering
- Program Management
*This summary is an abbreviated version of the report and does not contain the full content. A link to download the full report is available above.
If you have difficulty obtaining a copy of the report, please contact us using the "Contact" link below. [post_title] => Expanding Beyond Your Outgrown PDM System (Buyer's Guide) [post_excerpt] => [post_status] => publish [comment_status] => open [ping_status] => open [post_password] => [post_name] => outgrown-pdm [to_ping] => [pinged] => [post_modified] => 2022-11-14 22:27:55 [post_modified_gmt] => 2022-11-15 03:27:55 [post_content_filtered] => [post_parent] => 0 [guid] => https://tech-clarity.com/?p=7356 [menu_order] => 0 [post_type] => post [post_mime_type] => [comment_count] => 0 [filter] => raw ) [18] => WP_Post Object ( [ID] => 7325 [post_author] => 2 [post_date] => 2018-11-19 09:10:21 [post_date_gmt] => 2018-11-19 14:10:21 [post_content] =>- If they have executive sponsorship
- Whether they're budgeted
- If a cross-functional team is deployed
- How systems like PLM can help
“Digital” is Viewed as a Significant Business Priority
Executive Overview Manufacturers are weighing their options and considering a number of strategic manufacturing initiatives. Many of them are related and all are competing for budget, time, and attention. Which investments are getting the most attention? How are manufacturers addressing the opportunities? How are they leveraging PLM solutions as an enabler? Tech-Clarity conducted a survey of over 130 manufacturers to find out. The program most frequently cited as critical to the business strategy is Digitalization / Digital Enterprise. More than one-half of respondents say that these digital initiatives are “important” if not “critical” to their business strategy.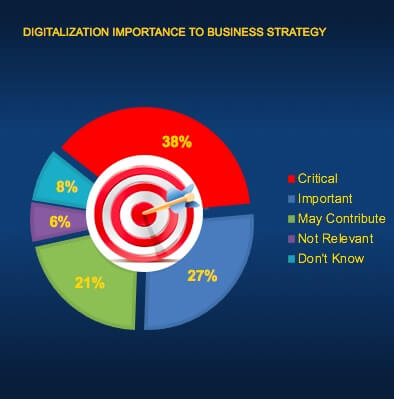
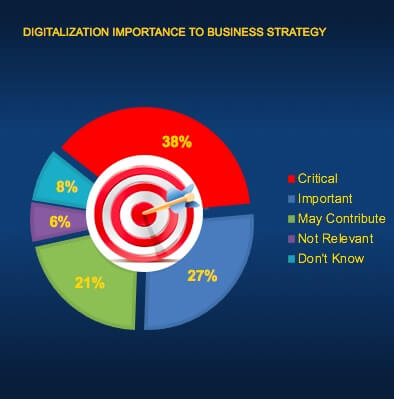
A Variety of Digital Initiatives are Deemed Strategic
Digital Transformation is the Leading Priority Surveyed companies report Digital Transformation as the initiative most critical to achieving their business strategy. The second most commonly cited initiative is IoT (Internet of Things). IoT may be a subset of an overall digital transformation initiative. In fact, “Digital Transformation” may serve as a strategic umbrella for many of the initiatives investigated. Industry 4.0 is a High Priority Beyond digitalization, reported on par with IoT initiatives, is Industry 4.0 which was defined as “Industry 4.0 / Smart Manufacturing.” Roughly one-half of companies surveyed say that these initiatives are important or critical to achieving their business strategy.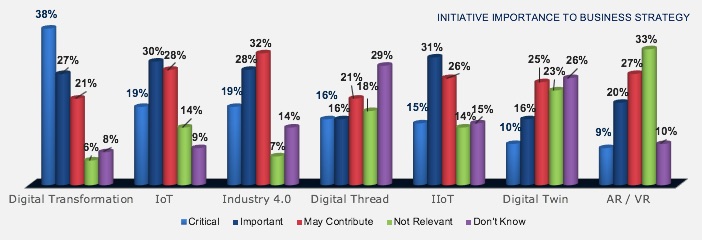
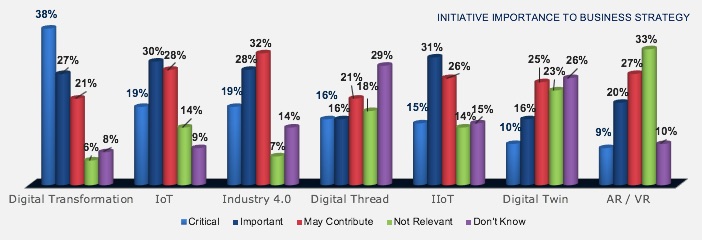
Initiatives Vary in Level of Executional Traction
Investigating Initiative Traction The initiatives most frequently reported as critical to the business strategy are Digitalization, IoT, and Industry 4.0. Let’s look beyond what companies say is important to understand what they’re doing about it.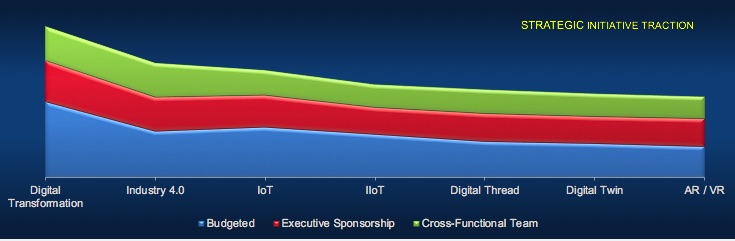
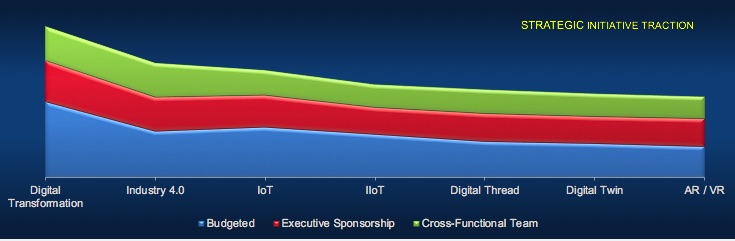
PLM is Key to Strategic Manufacturing Initiatives
PLM Enables Digital Transformation The survey analyzed how PLM supports the strategic initiatives manufacturers recognize as important to their business strategy. The responses show that PLM plays a critical or significant role in many of the initiatives. This highlights the importance of PLM as the innovation backbone for the digital enterprise.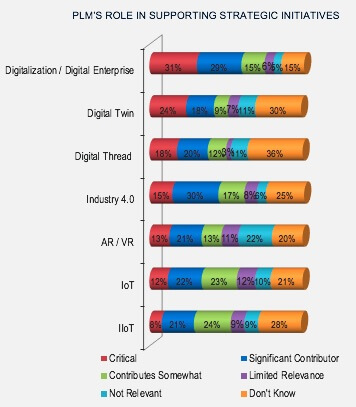
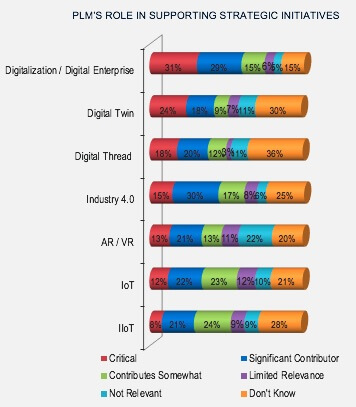
Conclusions and Next Steps
The Manufacturing Industry is in a Revolution The manufacturing industry is changing rapidly and companies have to digitalize or risk losing their market position. Manufacturers are responding, targeting a number of important strategic initiatives related to becoming a digital enterprise. The Digital Transformation Has Begun Digital Transformation is seen as the most critical initiative for the manufacturing industries. Research for this report shows that digital transformation has significant support at the Board level. It’s also a funded initiative that’s more likely to have cross-functional teams executing the program. Industry 4.0 and IoT Initiatives are also frequently viewed as contributors to the corporate business strategy. Although the other initiatives may not have as much executive and enterprise traction, they are also being addressed and play important roles in the overall digital transformation of the company. PLM is a Key Enabler to Support the Digital Revolution PLM plays a key role in supporting digitalization initiatives, serving as the digital innovation backbone. PLM also supports important digital capabilities, including Digital Twin and Digital Thread, which show promise but require some additional education for many companies. PLM is important to the entire Digital Transformation strategy because it provides the product context, history, and details required to support the digital product and manufacturing strategy. Recommended Next Steps Activity level is high, and so are the stakes in terms of impact on business performance. We believe it’s time for manufacturers to review their business strategy, make sure they are educated on these high-level initiatives, and determine how to put these strategies into action. [post_title] => The State of Digitalization in Manufacturing (survey results) [post_excerpt] => [post_status] => publish [comment_status] => open [ping_status] => open [post_password] => [post_name] => state-digitalization [to_ping] => [pinged] => [post_modified] => 2022-11-14 22:28:49 [post_modified_gmt] => 2022-11-15 03:28:49 [post_content_filtered] => [post_parent] => 0 [guid] => https://tech-clarity.com/?p=7325 [menu_order] => 0 [post_type] => post [post_mime_type] => [comment_count] => 0 [filter] => raw ) [19] => WP_Post Object ( [ID] => 7314 [post_author] => 2 [post_date] => 2018-11-12 16:06:31 [post_date_gmt] => 2018-11-12 21:06:31 [post_content] =>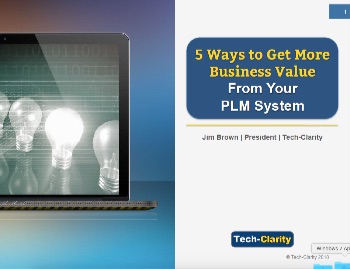
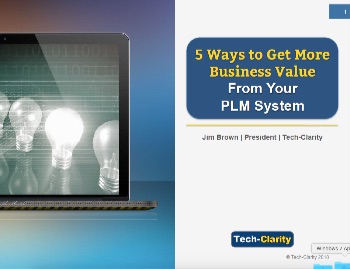
Has your PLM Value Stalled?
It’s time to re-energize your PLM solution. Most companies start their PLM implementations with high ambitions for strategic business results. Too often they get through the first implementation, typically supporting core Product Data Management (PDM), and stall. Companies like this are missing a golden opportunity. Once the PLM foundation is in place, there’s a lot more than can be done to leverage it for greater value. Our research shows that companies gain significantly higher levels of ROI from supplemental PLM projects than from their initial implementation. “Expanding capabilities is much easier when you have the foundation in place and a community with PLM skills,” offers the manager of a leading transportation equipment manufacturer.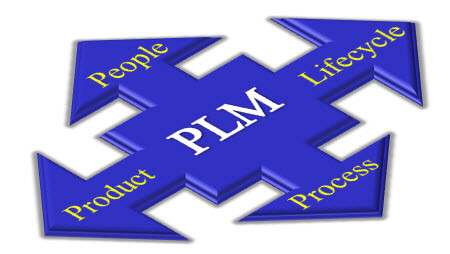
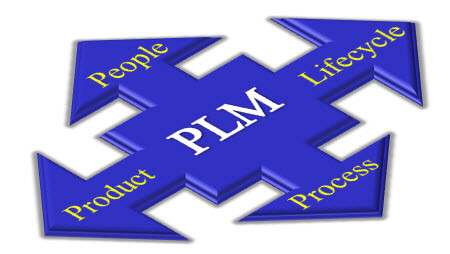
Even if your company has already gone beyond the basics, it’s likely that changes in your business have opened up opportunities that weren’t considered earlier. Beyond that, the manufacturing industry’s shift to the digital enterprise offers compelling new opportunities that can expand PLM value including IoT, Digital Twin, Augmented Reality (AR), and more. There are proven ways to do it. Let’s explore how your company can leverage what you have to do more.
Expanding Your PLM Value
Most companies have a lot more value to extract from PLM. Even if your company has completed all of your planned phases and met your original goals, it’s very likely they could go beyond what they initially expected. Many companies can get more by simply extending what they have. The digital evolution of the manufacturing industry and PLM’s adoption of platform and cloud architectures have unlocked significant new opportunities for business value for those that want to go further. It’s time for companies to start with the business in mind, make sure they’ve locked in the value available from the basics, and then look to achieve more. “Think of it as an ROI driven investment,” advises the manager of the transportation equipment manufacturer. “Don’t just do it because it’s cool, have a vision for where you want to go and how the tools will get you there. Do the evaluation to make sure it’s worthwhile for the business. Keep improving so you don’t become stagnant.” PLM helps companies manage complexity, improve productivity, and reduce cost. But PLM can do more, enabling top-line growth and margin expansion. It’s also important to recognize that digitalization is changing the market landscape. PLM can provide the foundation to support IoT and other transformational initiatives that may significantly change your company’s value proposition and competitive standing. It’s time to get started. [post_title] => 5 Ways to Get More Business Value from PLM [post_excerpt] => [post_status] => publish [comment_status] => open [ping_status] => open [post_password] => [post_name] => more-from-plm [to_ping] => [pinged] => [post_modified] => 2022-11-14 22:27:53 [post_modified_gmt] => 2022-11-15 03:27:53 [post_content_filtered] => [post_parent] => 0 [guid] => https://tech-clarity.com/?p=7314 [menu_order] => 0 [post_type] => post [post_mime_type] => [comment_count] => 0 [filter] => raw ) ) [post_count] => 20 [current_post] => -1 [before_loop] => 1 [in_the_loop] => [post] => WP_Post Object ( [ID] => 7823 [post_author] => 2 [post_date] => 2019-05-08 10:43:03 [post_date_gmt] => 2019-05-08 14:43:03 [post_content] =>BOM Processes Rely on Inadequate Solutions
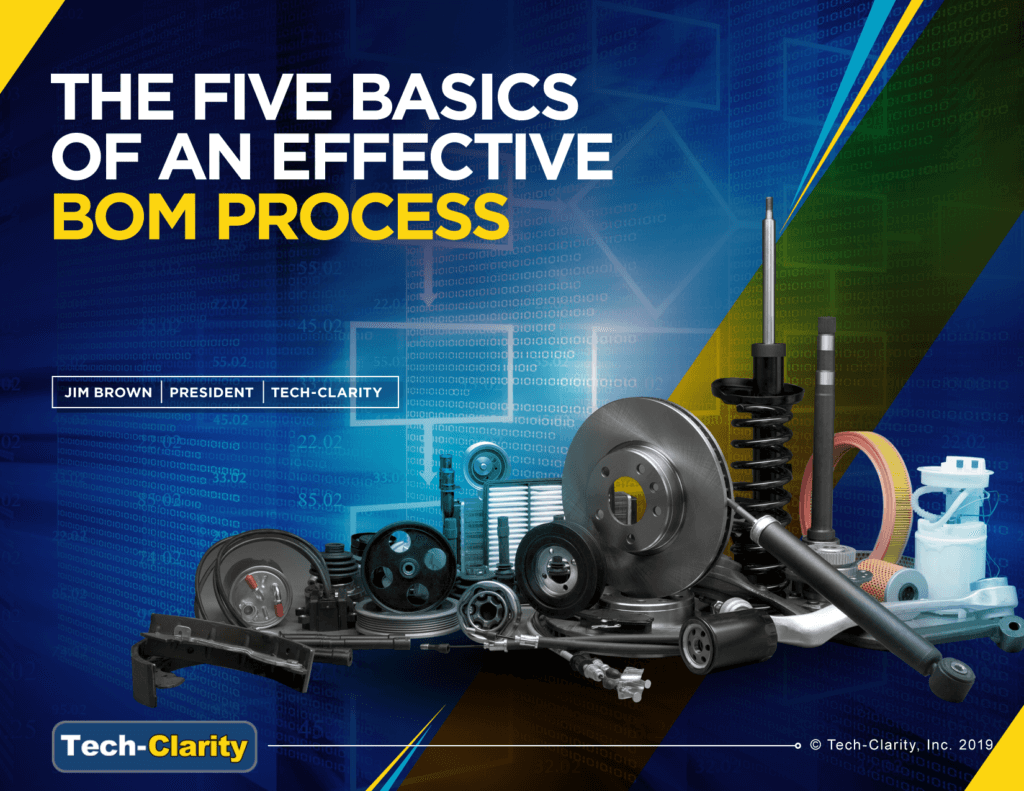
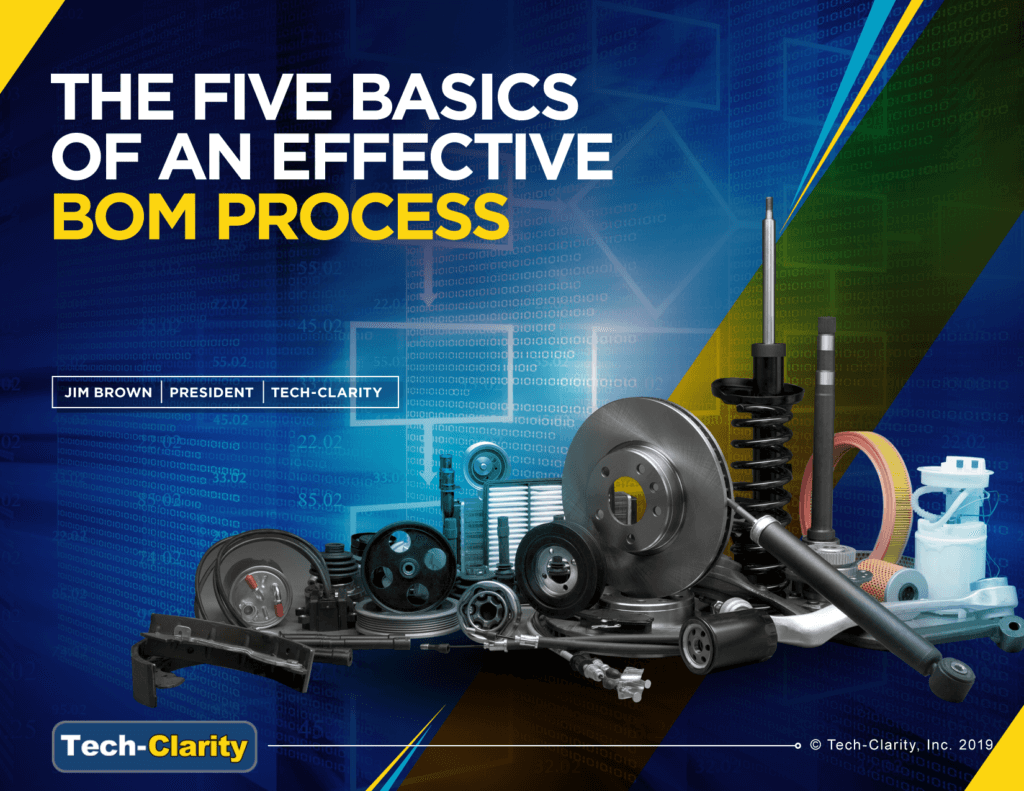
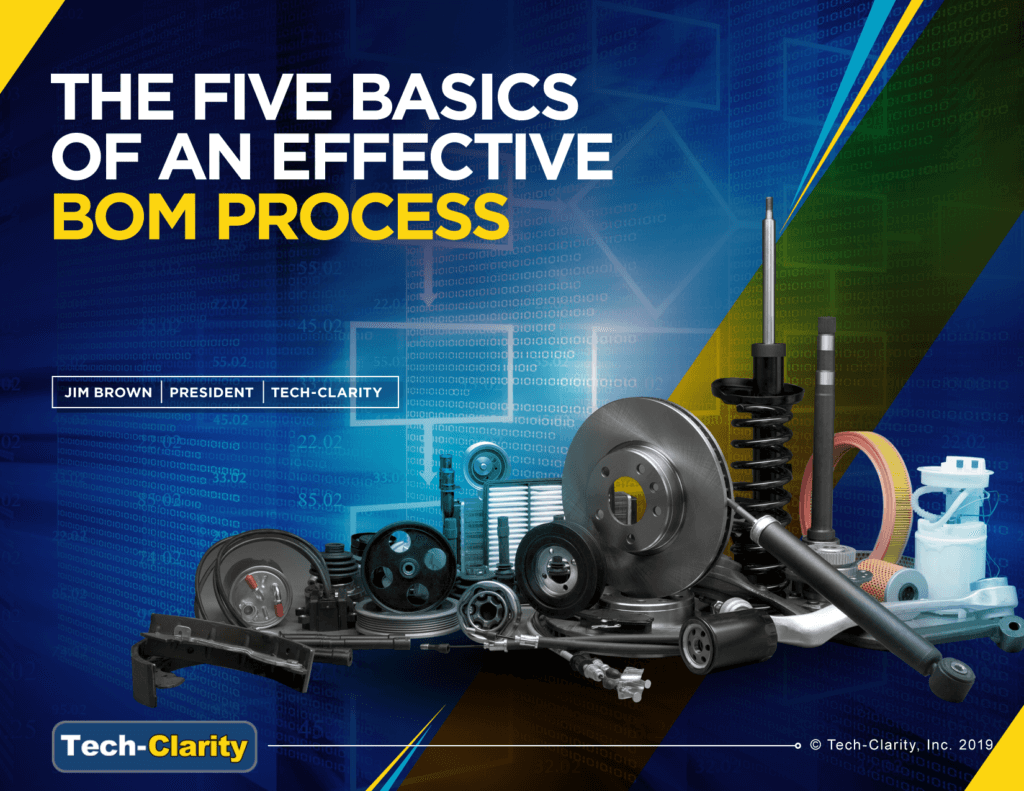
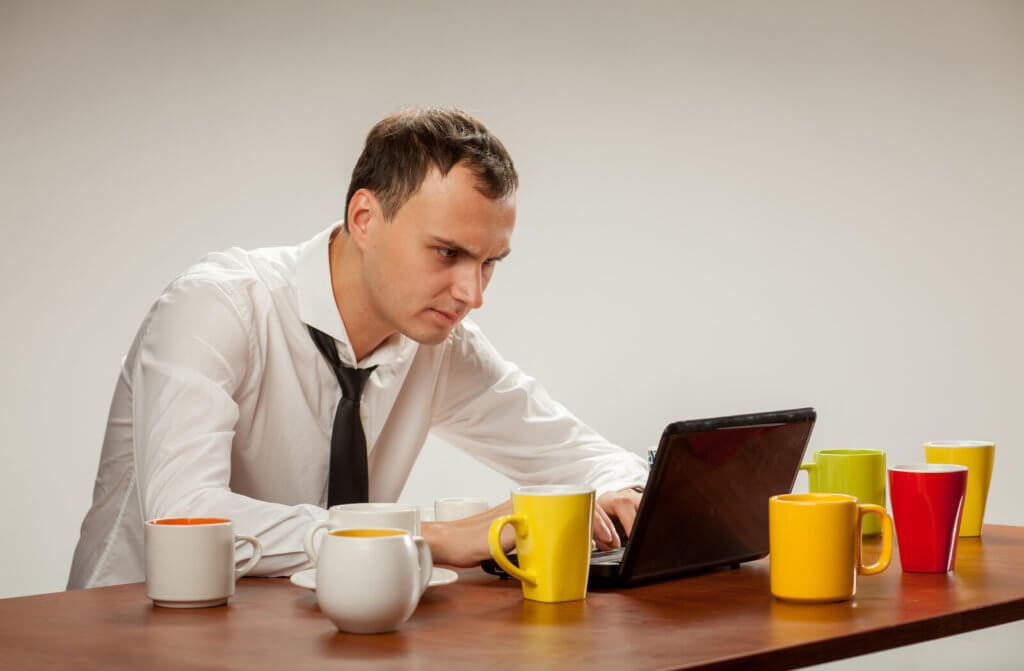
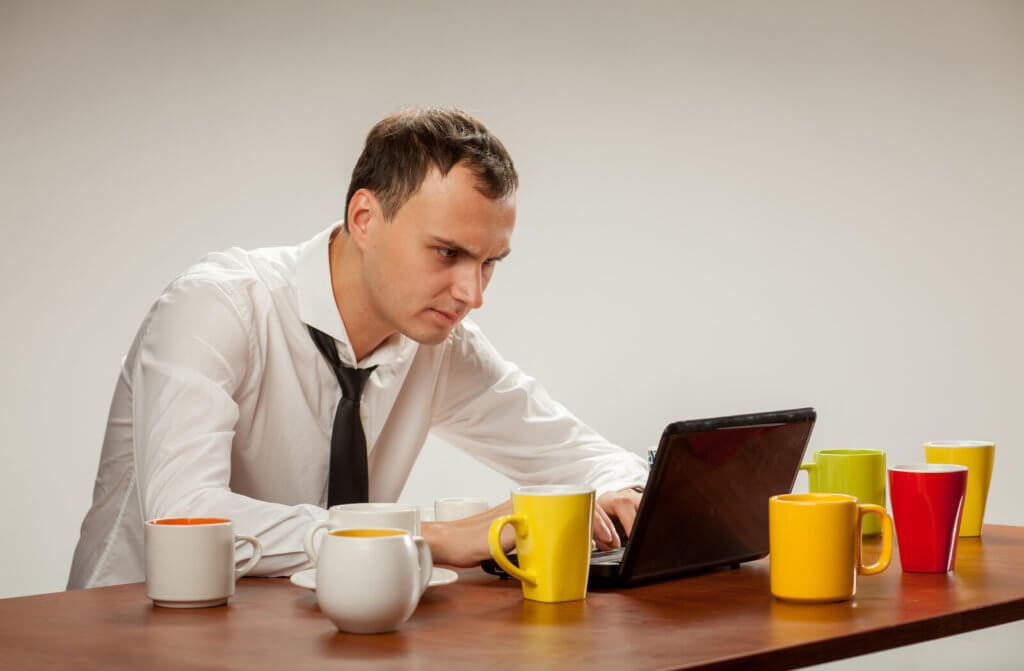
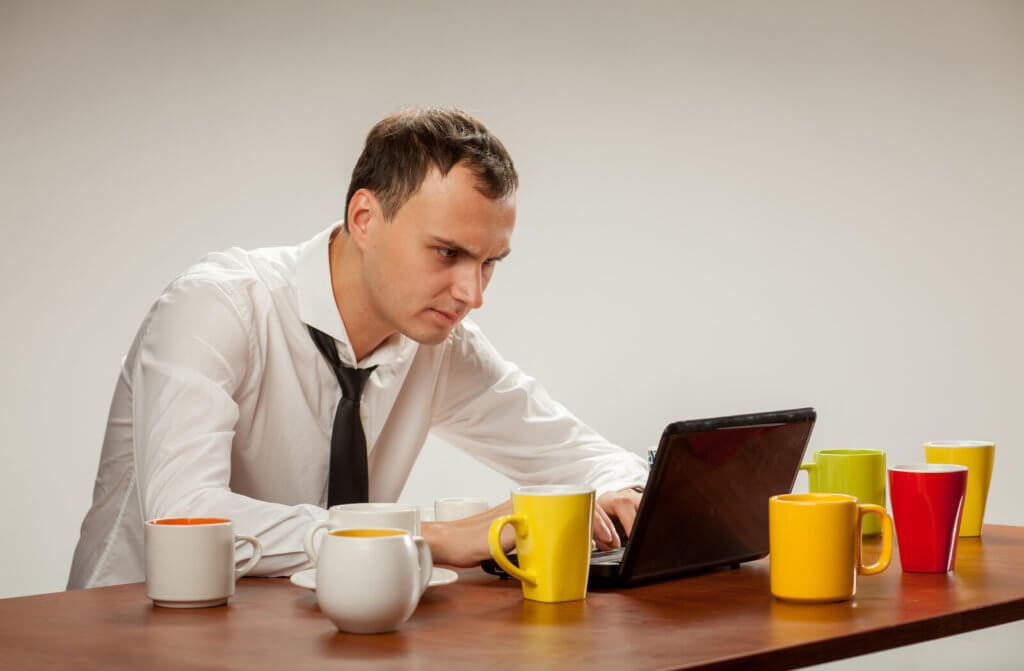
Table of Contents
- BOM Processes Rely on Inadequate Solutions
- The BOM is the Fundamental Communication Tool
- The BOM Process Status Quo
- The Five Fundamentals of a Successful BOM Process
- 1) Aim for Accuracy
- 2) Keep Data Current
- 3) Manage Complete BOMs
- 4) Communicate BOM Data Clearly
- 5) Put BOM Data into Action
- Next Steps
- Acknowledgments
The BOM is the Fundamental Communication Tool
BOMs are the Backbone of the Manufacturing Industry BOMs are the fundamental way that manufacturers define, communicate, and realize their products. The bill of material is essentially the backbone of the manufacturing business, specifying what to buy and what to build. In many companies, BOM communication has to bridge disciplines across company boundaries. BOMs are The Primary Communication Tool in Industry Sound BOM processes create a bridge that crosses all parts of the organization. They document engineering designs and provide the information that Purchasing needs to order parts. Then, they deliver the data needed for Manufacturing to plan and execute orders. BOM data also serves as the backbone for others to roll up important attributes like weight, costs, and more.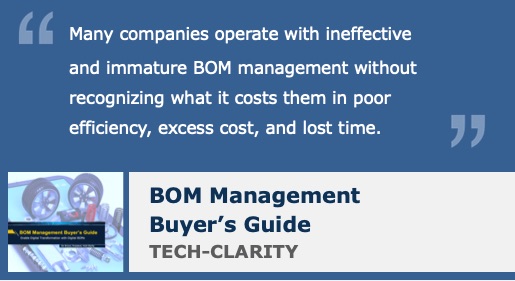
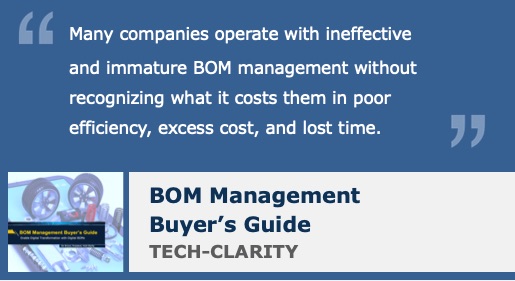
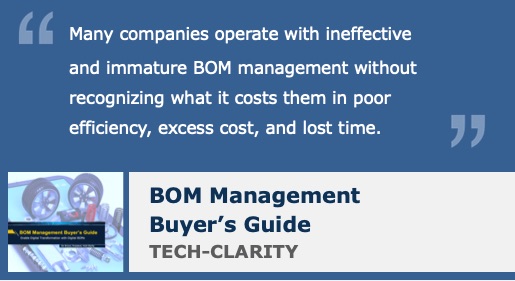
- Helps improve productivity
- Reduces the number of shipments delayed by missing parts
- Drives down scrap from using wrong parts or revisions
- Improves cost through item reuse
The BOM Process Status Quo
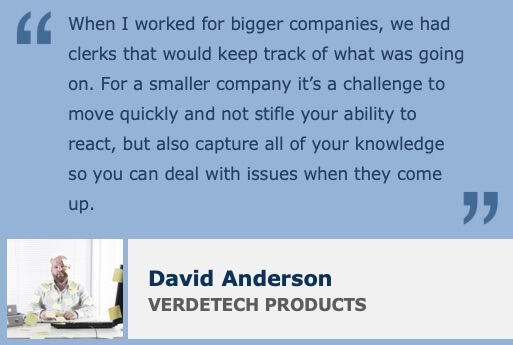
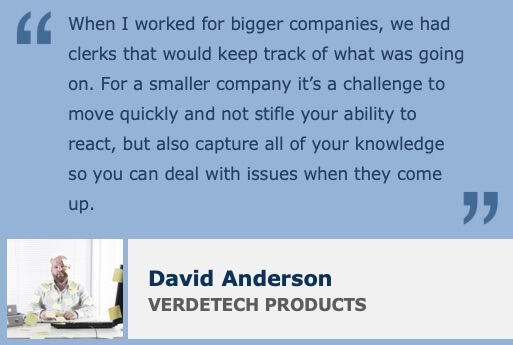
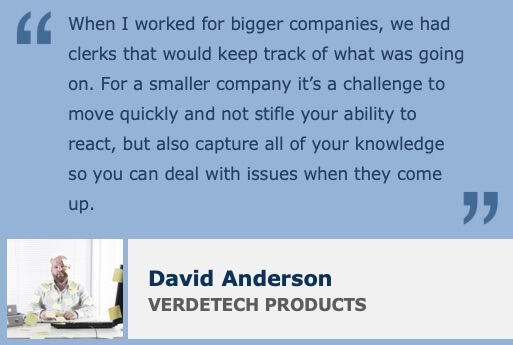
The Five Fundamentals of a Successful BOM Process
Get BOM Processes in Control Manufacturers who are ready to replace spreadsheets and email and get BOM processes under control can do so with reasonable effort. By focusing on the basics, they can make rapid improvements to productivity and reduce the impact of BOM-related errors. This leads to the question “What are the most important factors needed to improve BOM process?” We’ve identified five key areas that can easily be addressed and make a big impact on the business. Focus on the Fundamentals BOM Processes should be implemented and enabled in a way that ensures that they are:- Accurate
- Current
- Complete
- Clear
- Actionable
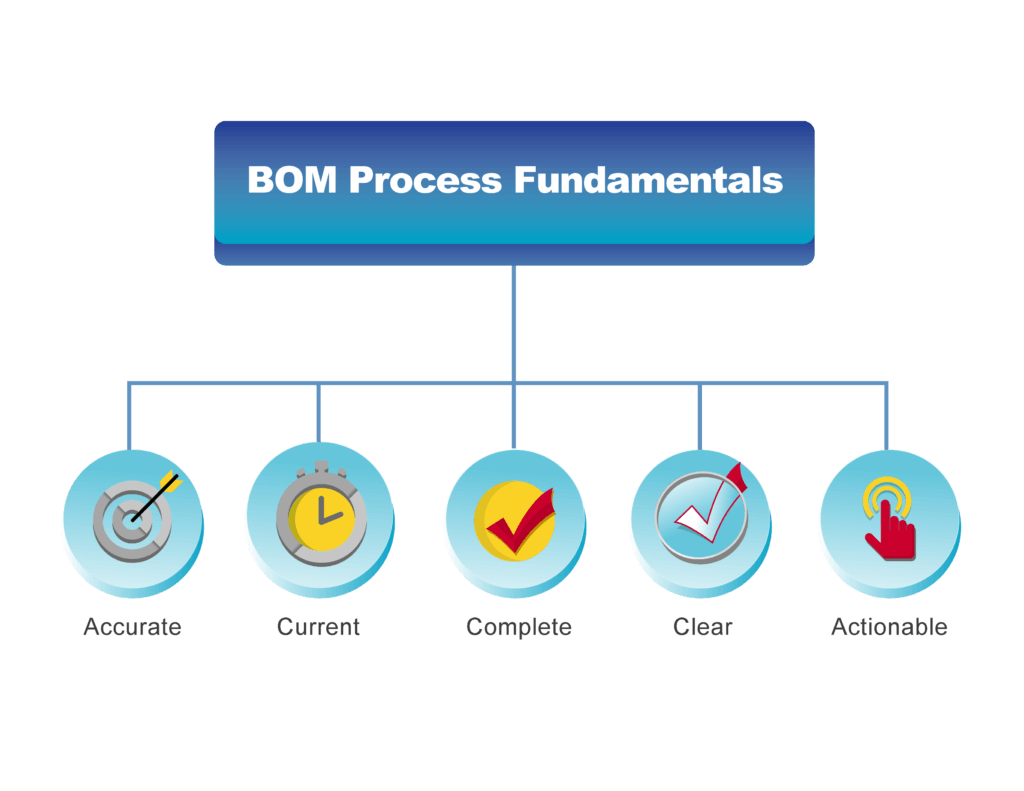
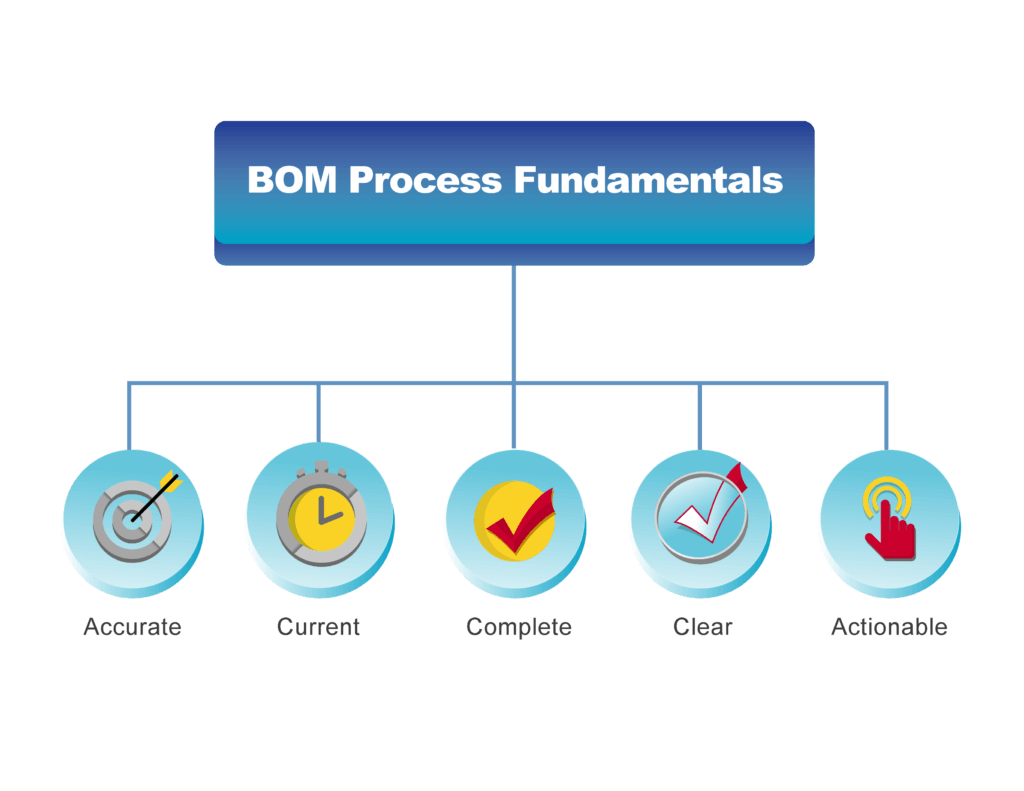
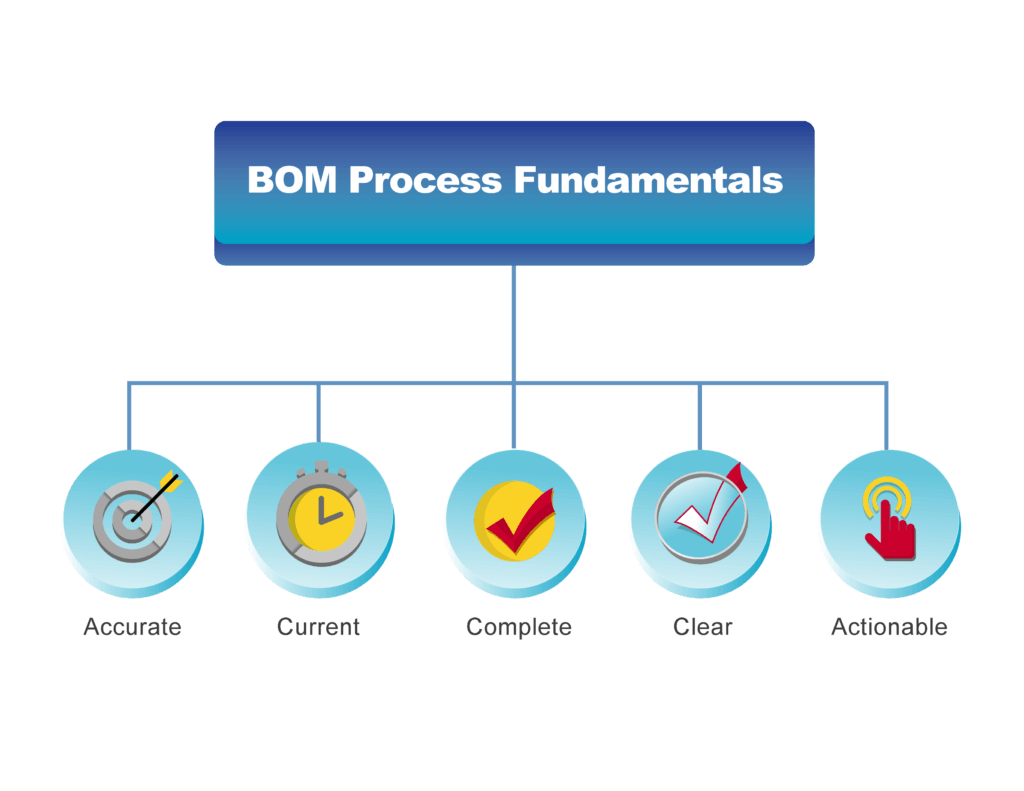
1) Aim for Accuracy
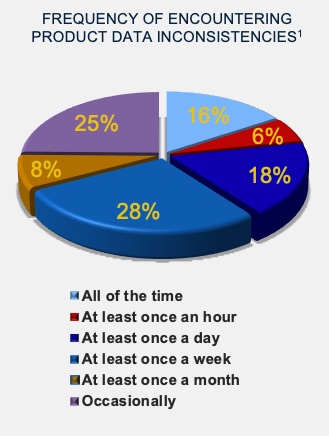
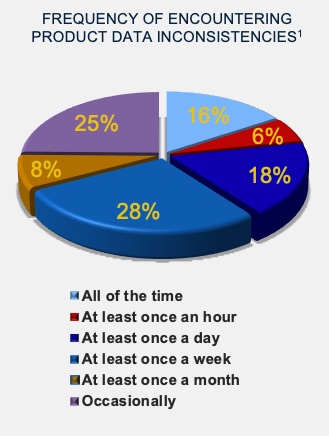
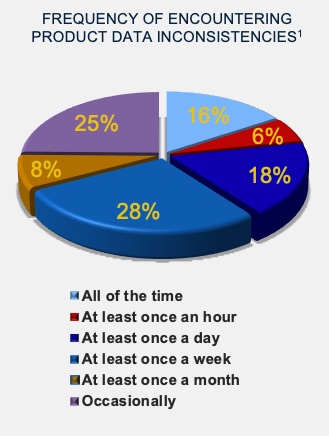
2) Keep Data Current
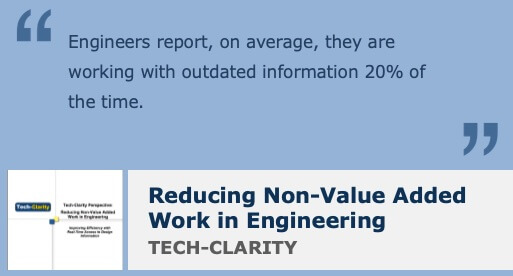
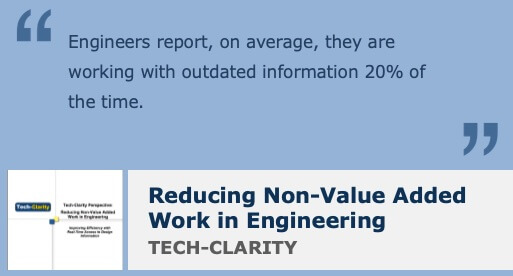
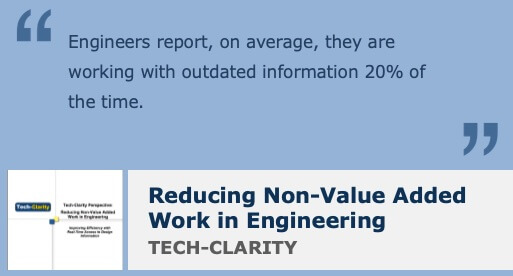
3) Manage Complete BOMs
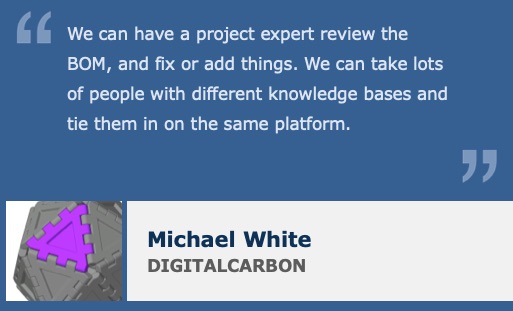
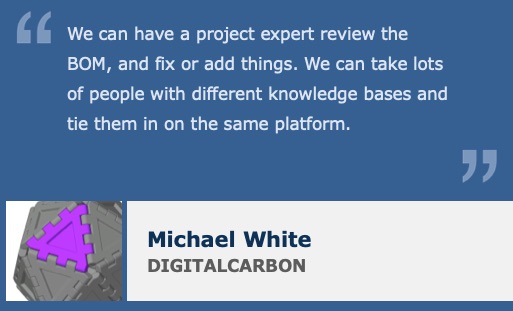
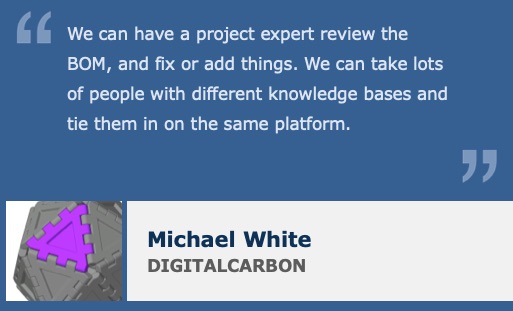
4) Communicate BOM Data Clearly
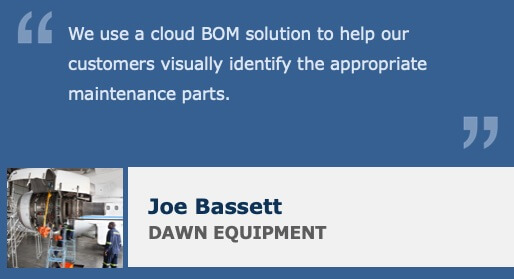
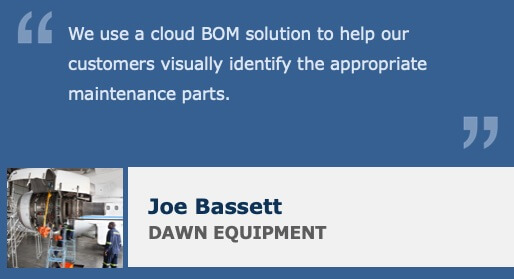
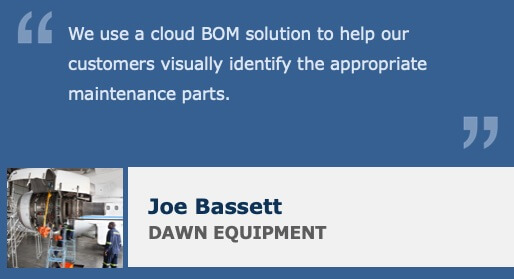
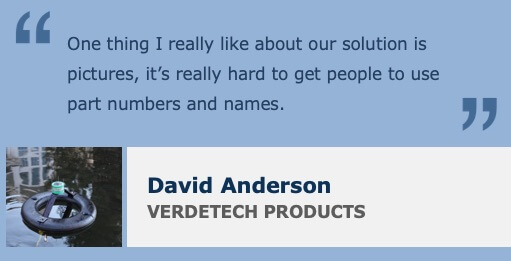
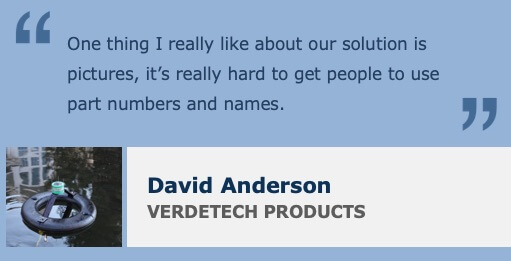
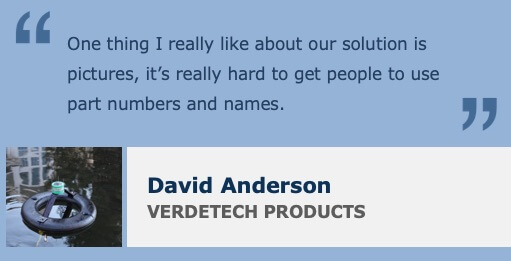
5) Put BOM Data into Action
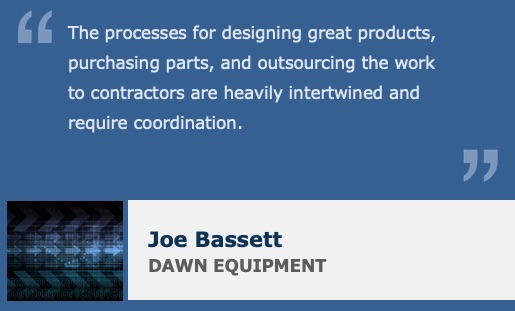
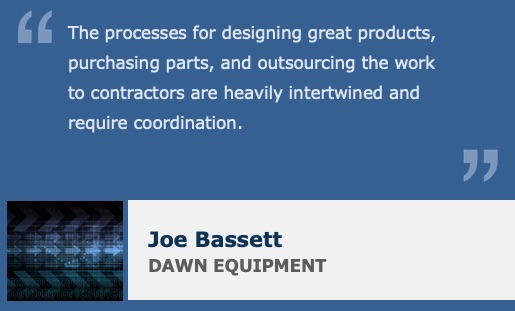
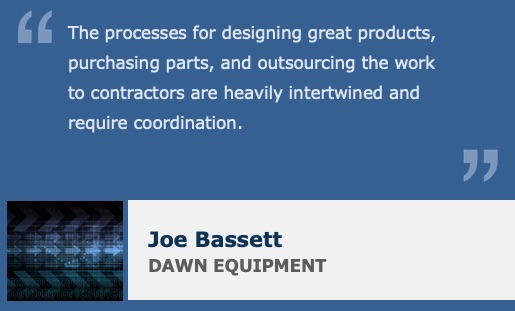
Next Steps
Go Beyond the Status Quo to Prevent Mistakes Today’s BOM process status quo, frequently relying on inadequate technology like spreadsheets and email, leads to inefficiency, excess cost, mistakes, quality issues, and late orders. The consequences of poor processes, especially for a smaller company, can be significant. As David Anderson of Verdetech Products shares, “Sometimes you get away with things by luck, but a major problem could kill a company.” It’s time for companies to raise the bar on BOM data and processes.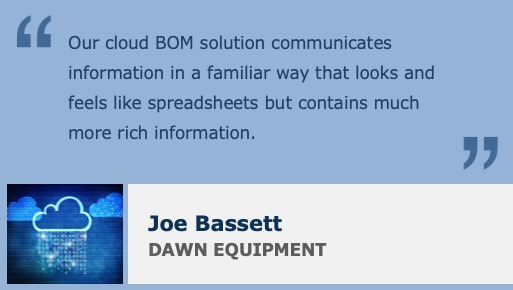
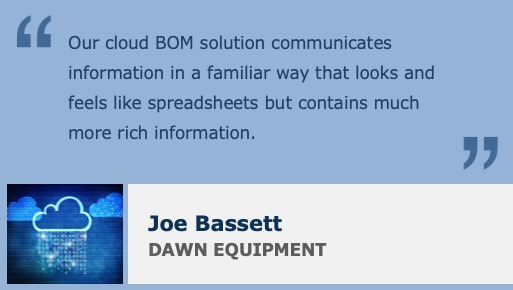
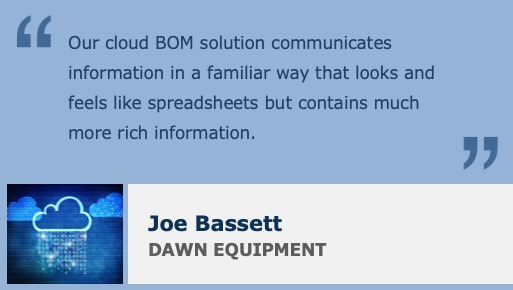
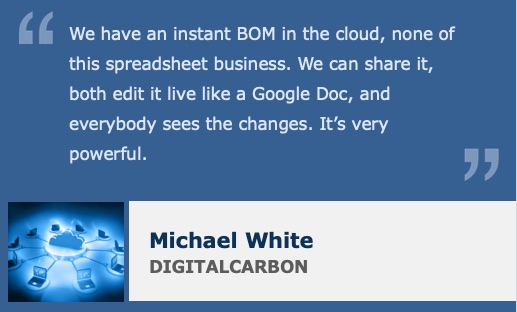
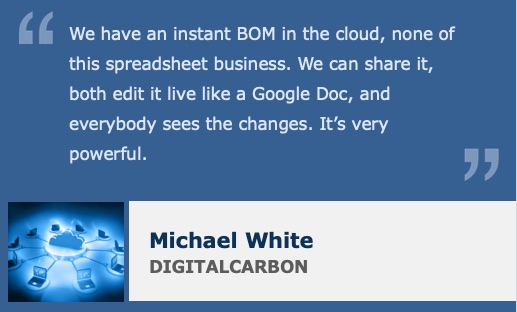
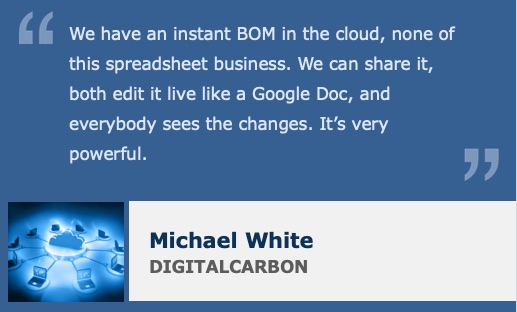
Acknowledgments
About the Author Jim is a recognized expert in enterprise software for manufacturers with over 25 years of experience in application software, management consulting, and research. He has extensive knowledge on how industrial companies use product innovation, product development, engineering, and other enterprise solutions to improve business performance. Jim is actively researching the value of improving product innovation and operational performance through digitalization. [post_title] => The Five Basics of Effective BOM Processes (eBook) [post_excerpt] => [post_status] => publish [comment_status] => open [ping_status] => open [post_password] => [post_name] => billofmaterials-management [to_ping] => [pinged] => [post_modified] => 2022-11-14 22:28:16 [post_modified_gmt] => 2022-11-15 03:28:16 [post_content_filtered] => [post_parent] => 0 [guid] => https://tech-clarity.com/?p=7823 [menu_order] => 0 [post_type] => post [post_mime_type] => [comment_count] => 1 [filter] => raw ) [comment_count] => 0 [current_comment] => -1 [found_posts] => 763 [max_num_pages] => 39 [max_num_comment_pages] => 0 [is_single] => [is_preview] => [is_page] => [is_archive] => [is_date] => [is_year] => [is_month] => [is_day] => [is_time] => [is_author] => [is_category] => [is_tag] => [is_tax] => [is_search] => [is_feed] => [is_comment_feed] => [is_trackback] => [is_home] => 1 [is_privacy_policy] => [is_404] => [is_embed] => [is_paged] => [is_admin] => [is_attachment] => [is_singular] => [is_robots] => [is_favicon] => [is_posts_page] => [is_post_type_archive] => [query_vars_hash:WP_Query:private] => 984528891410df99576b8e322f7e3e6b [query_vars_changed:WP_Query:private] => 1 [thumbnails_cached] => [allow_query_attachment_by_filename:protected] => [stopwords:WP_Query:private] => [compat_fields:WP_Query:private] => Array ( [0] => query_vars_hash [1] => query_vars_changed ) [compat_methods:WP_Query:private] => Array ( [0] => init_query_flags [1] => parse_tax_query ) [query_cache_key:WP_Query:private] => wp_query:4d44c943ea2a9a727efc39012502aecb:0.71626200 17554203220.72658300 1755420322 )All Results for "All"
How to Avoid Non-Value Added Work for Engineers (guest post)
Imagine what you could do if you could get almost a third of your time back? In a guest post on the Sodius Willert blog, Michelle Boucher shares research on how much engineering time is wasted on non-value added work and explains what you can do. Focus on the Work You Enjoy As an engineer,…
Retail Analytics Buyer’s Guide (eBook)
How do you navigate complex, omnichannel environments and manage multiple sources of data to make the best decisions? Can predictive analytics help? Tech-Clarity’s Retail Analytics Buyer’s Guide explains how predictive analytics provide better visibility across your retail business so that you can make better decisions to become more competitive. As the retail industry faces significant…
The Renaissance of CAD
As our changing world impacts product design, how should CAD evolve? How can CAD support your efforts to adopt some of the latest technologies? During the PTC on-demand virtual session, “The Renaissance of CAD: What’s New, What’s Now & What You Can Do With It” you will hear about some of the latest advancements in…
IoT, Industrial IoT, and Digital Twins in Food & Beverage Production (animation)
How can food and beverage companies use digitalization to dramatically increase flexibility, enhance consumer responsiveness, and improve productivity? This episode of Tech-Clarity TV, Revolutionizing Food and Beverage Production with the Industrial IoT and the Digital Twin, shares how food producers can leverage digital twins and the IoT to improve performance. This video series is sponsored…
Ten Practices to Successfully Implement Technology (eBook)
How can you get the quickest return on your investments in technology? As we look ahead to the coming decade, technology will become increasingly critical for your company to stay competitive. New technology can include CAD, CAE, PLM, 3D printing, IoT, and more. However, for that technology to work for your business, your implementation must…
Why Not Adopt Cloud for Product Innovation and Engineering? (guest post)
How have manufacturers’ opinions on using the cloud to support product innovation, product development, and engineering changed? How does that impact cloud adoption? Read the guest post in full in the Digital Transformation section of the Siemens PLM Community blog. Jim Brown recently shared a guest post on the Siemens’ blog offering our experience on…
Revolutionizing Simulation For Design Engineers
How do you empower engineers to design the best products possible? Research from Tech-Clarity’s Revolutionizing Simulation For Design Engineers research report finds that design engineers lack confidence in design decisions 28% of the time. The research identifies the most common ways engineers deal with this uncertainty, its impact, and how to improve confidence. This research…
IoT Medical Device Monitoring (Buyer’s Guide)
What should Life Sciences companies look for in a solution to help them simultaneously improve profitability and patient outcomes using remote device monitoring via the IoT? Our new Improving Service Performance and Patient Outcomes with Remote Monitoring Buyer’s Guide helps Life Sciences companies understand the business and social value of monitoring equipment with the IoT….
Preparing for EU MDR (eBook)
Are you ready for the EU MDR? Tech-Clarity’s Preparing for EU MDR explains the impact of the EU MDR on your product data. While complying to the EU MDR may require an investment, taking the steps now to prepare your product data will not only support EU MDR compliance, but will position your company to…
Top Ten Signs You’ve Outgrown Your PDM System (webcast)
How can manufacturers tell when they’ve outgrown their Product Data Management system? What should they look for to replace it? Join Tech-Clarity’s Jim Brown and PTC‘s Mark Lobo as they help companies navigate this all-too-common scenario. The interactive presentation will share what’s missing in most basic PDM / Engineering Document Management (EDM) systems and what…
Remote Monitoring Solution Selection for Medical Device Service (webcast)
What should Life Sciences Companies look for in a solution to transform service using IoT remote monitoring? Tech-Clarity’s Jim Brown and PTC’s Anthony Moffa will share recent research and industry experience on this Medical Design & Outsourcing webcast, How to Select a Remote Monitoring Solution to Transform Your Service Model. The webcast will cover how…
How to Futureproof Your Product Design (survey results)
Is your CAD tool ready for the 2020s? Does it have the features you need to keep your company competitive? Tech-Clarity’s How to Futureproof Your Product Design: 5 Technologies Your CAD Tool Must Support describes the key technologies that will impact design in the 2020s. Based on a survey of over 200 manufacturers, respondents identified…
The Value of Immersive 3D Automotive Experiences (eBook)
How are innovative automotive companies leveraging immersive, real-time 3D to improve innovation? How can they use highly realistic, interactive, virtual experiences to enhance design, engineering, manufacturing engineering, sales, marketing, training, and more? This eBook shares industry insights and experiences from Ford, Audi, Teague, Team One / Saatchi & Saatchi, and other manufacturers to shed light…
Better Requirements Management to Save Your Bottom Line (Webcast)
Does your company excel at meeting and managing product requirements? If not, this webinar will help you develop better requirements management practices. During this on-demand webinar, Tech-Clarity’s Michelle Boucher and Anshuman Prakash from Siemens share perspectives on better requirements management. They also provide advice to make the process easier. During the webinar, you will learn:…
Better Requirements Management: An Immediate Payback (Guest Post)
Did you know that 9.9% of every dollar spent on projects is wasted due to poor project performance? This startling statistic comes from research done by the Project Management Institute (PMI), published in their 2018 Pulse of the Profession® report. In a guest post on the Siemens Solid Edge blog, Michelle Boucher outlines some key reasons why…
5 Frustrations of Working with Contract Manufacturers (guest post)
What challenges do manufacturers encounter when working with contract manufacturers? What should they do to reduce the frustration and streamline the relationship? Jim Brown introduces five questions you may find yourself asking if you’re working with a CMO, CDMO, or other supply chain partners and then offers recommendations based on our experience and research in…
Expanding Beyond Your Outgrown PDM System (Buyer’s Guide)
What should manufacturers look for when it’s time to replace their outgrown PDM system? Our research shows a high correlation between elevated business performance and strong product data management capabilities. Unfortunately, we find many manufacturers have already stretched the limits of what their basic Product Data Management (PDM) system can do. In most cases, it meets…
The State of Digitalization in Manufacturing (survey results)
Manufacturing is going through a significant, digital transformation that’s disrupting the industry status quo. Companies are investing in digital transformation, smart manufacturing, Industry 4.0, Internet of Things (IoT), and other related initiatives. What are they prioritizing? And, what are they actually taking action on? Tech-Clarity surveyed over 130 manufacturers to find out. The report analyzes…
5 Ways to Get More Business Value from PLM
How can manufacturers extend their PLM investments to gain higher levels of business value? The new 5 Ways to Get More Business Value from Your PLM System offers practical approaches for companies to leverage their existing Product Lifecycle Management investment to improve top-line and bottom-line performance, including tips gained from two leading manufacturers. Please enjoy…