Some see low-code as a promising new technology, but is it really new? No. Is it promising for digital transformation? Our survey says yes. Please enjoy the summary below or see Jim Brown’s full guest post on the Siemen’s blog to learn how the low-code technology “breakthrough” helps fill digital transformation gaps. Digital Transformation Gaps…
- Challenges Facing Manufacturers
- What Are Digital Work Instructions?
- Ten Ways Digital Work Instructions Help
- 1. Connectivity to Existing Systems
- 2. Single Point of Access
- 3. Traceability from Engineering to Manufacturing
- 4. Supports Roll out of New or Customized Products
- 5. Real-Time Process Control
- 6. Analytics to Optimize Work Instructions
- 7. Hardware Agnostic
- 8. User friendly and Easy to Adopt
- 9. Good Vendor Support
- Select the Right Solution for Your Needs
- Acknowledgments
What Are Digital Work Instructions?
Industrial Internet of Things (IIoT) The IIoT integrates many technologies in a factory. It can create a digital thread across the product lifecycle, enabling traceability to support greater efficiency, improve quality, and support regulatory compliance. For many, investments in IIoT will likely create a competitive advantage, especially during a downturn. There are many different approaches to start with IIoT adoption. One way is with digital work instructions.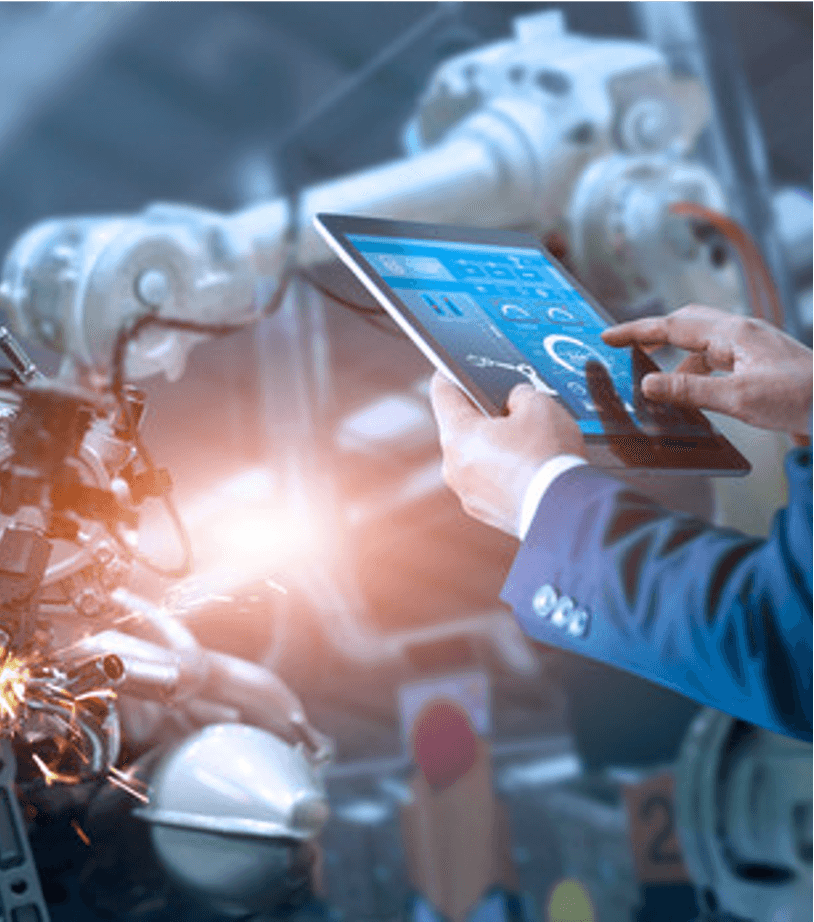
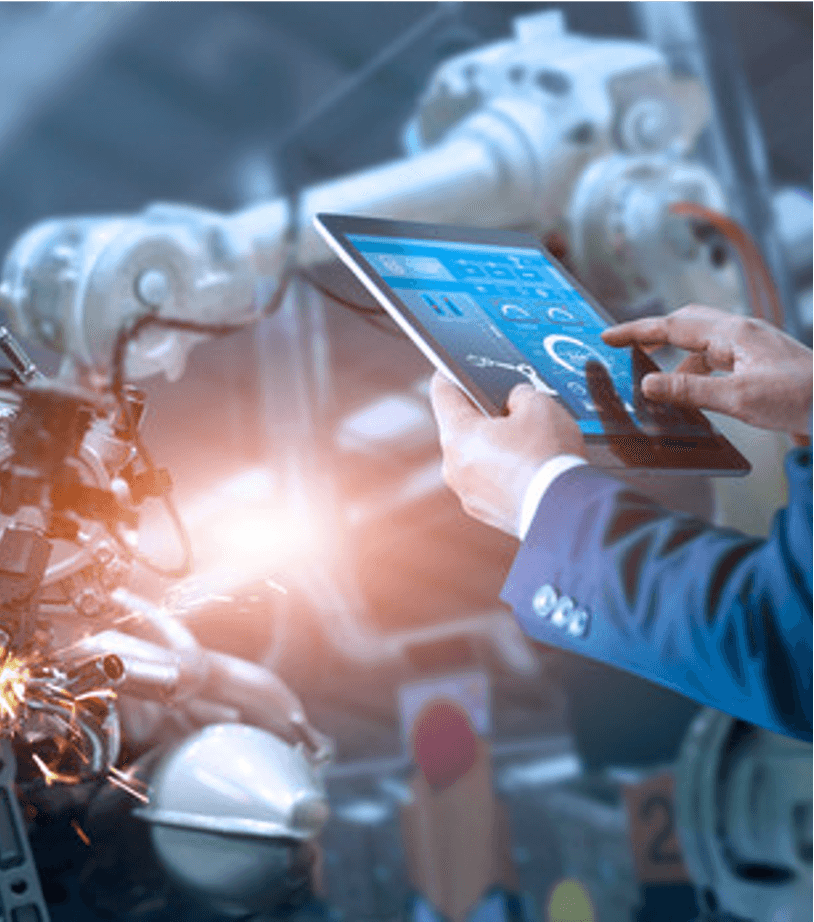
Select the Right Solution for Your Needs
Recommendations Based on industry experience and research for this report, Tech-Clarity has identified the following criteria to select the right solution for digital work instructions:- Connectivity to existing systems
- Single point of access
- Traceability from engineering to manufacturing
- Supports roll out of new products or customized products
- Real-time process control
- Analytics to optimize work instructions
- Hardware agnostic
- User friendly and easy to adopt
- Good vendor support
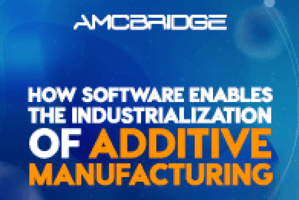
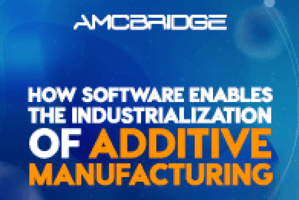
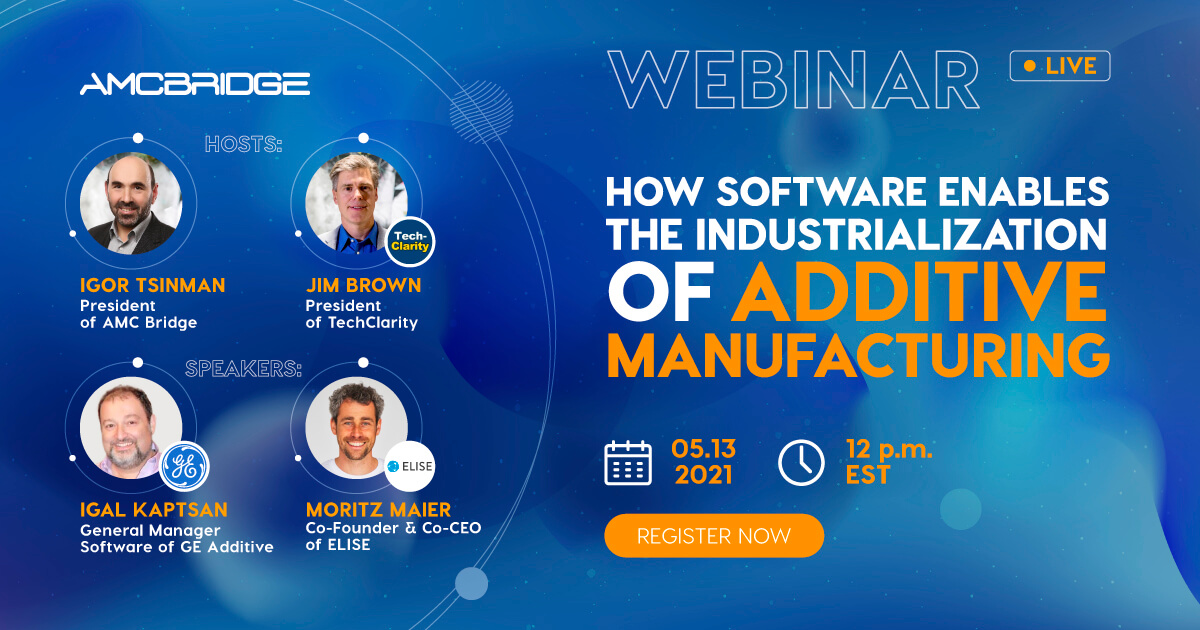
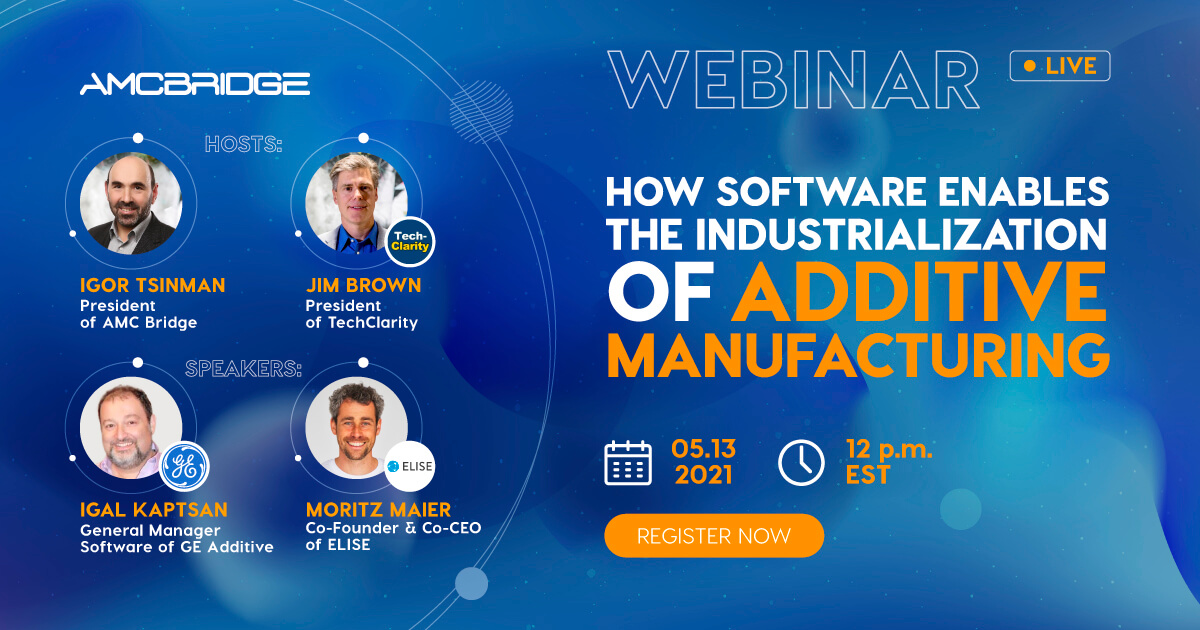
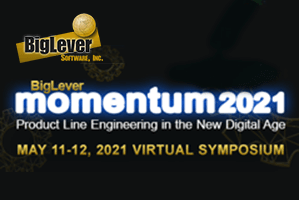
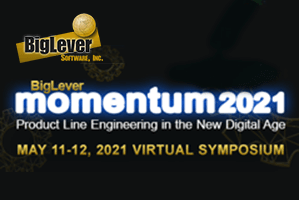
About the Event
In addition to Michelle, other speakers will include:- David Long, President, Vitech: Beyond Digital: Bridging the Divides
- Dr. Bobbi Young, Systems Engineering Fellow, Raytheon: Digital Transformation: Composing Your Digital Future
- Dr. Charles Krueger, CEO, BigLever: Product Line Engineering in the New Digital Age
- Eric MacKnight, Staff Engineer, GE Aviation: General Electric Aviation’s Use of Product Line Engineering and Model-based Systems Engineering
- Panel Discussion
- Sandy Friedenthal, Co-lead for OMG SysML V2 Submission Team: Model-Based Systems Engineering (MBSE) and the Digital Transformation
- Rick Flores, Technical Fellow, General Motors & Halim Ragab, Engineering Specialist, General Motors: Application of PLE in MBSE for an AUTOSAR-based Digital Supply Chain
- Bill Schindel, President, ICTT System Sciences: The Forces of Modularity: Macro and Micro Patterns in the Innovation Ecosystem
- Rowland Darbin, INCOSE PLE Working Group Chair: INCOSE Product Line Engineering International Working Group Perspectives on Modern Feature-based PLE
- Dr. William Donaldson, President & Founder, Strategic Venture Planning: We need to talk: Enabling the Conversation Between Business and Engineering about Organizational Change for Digital Transformation, Digital Engineering, and PLE
- Roger McNicholas, VP, General Dynamics Mission Systems: Application of PLE to US Army Live Training
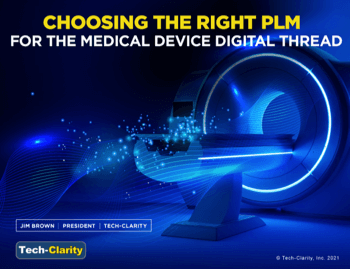
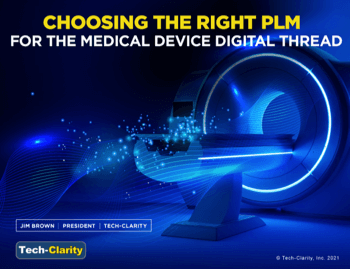
Table of Contents
- Introducing the Buyer's Guide
- The Digital Thread Imperative
- What to Look for to Streamline Engineering
- What to Look for to Closed-Loop Quality, Continuity
- Digital Thread Business Value
- Considerations by Role - Engineering
- Considerations by Role - Manufacturing
- Considerations by Role - Quality
- Considerations by Role - IT
- Considerations by Role - Service
- PLM is the Digital Thread Backbone
- Special Considerations - Emerging Technologies
- Implementation Considerations
- Vendor Considerations
- Conclusions and Next Steps
- About the Research
- Acknowledgments
The Medical Device Digital Thread Imperative
Business Strategies Demand a Cohesive Digital Thread Over three-quarters of companies say that the digital thread is either important or critical to achieving their business strategy. About one-half of medical device manufacturers indicate they have already implemented a digital thread initiative, most likely to meet design control mandates such as Design History File (DHF) and Device Master Record (DMR) and rapidly changing, region-specific regulatory requirements such as EU Medical Device Regulation (MDR). Medical device manufacturers report a variety of important goals for their digital thread initiative (see chart). They are 30% more likely than other manufacturers to pursue compliance, for example seeking audit-ready data. They are investing in reducing errors and adverse events to improve patient outcomes, all while trying to control the cost of quality and compliance overhead. While definitions vary, medical device manufacturers are looking for quality, compliance, and streamlined engineering from the digital thread. Streamlined Engineering The digital thread streamlines design by allowing product development teams to share and reuse design data across the stages of innovation. Design continuity along the digital thread allows engineers to add their design information to a cohesive model, directly incorporating and extending design data from prior steps – allowing them to efficiently design for regulatory management. Continuity, Closed Loop Quality The digital thread ties product information, decisions, and history together in a structured, integrated way that captures product innovation and knowledge throughout the product lifecycle. It establishes traceability from early in the front end of innovation through development, manufacturing, service, and field operation. This continuity ensures data-driven handovers between departments and support for evolving global regulations, initiatives, and standards including the FDA’s Case for Quality (CfQ) and Quality System Regulation (QSR), ISO 13485, and the new EU MDR/EU IVDR.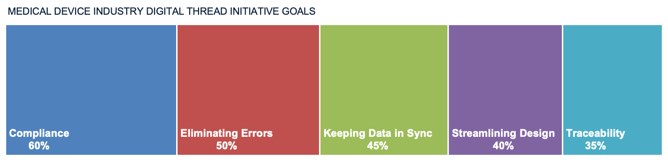
Conclusions and Next Steps
Invest in the Digital Thread Invest in the digital thread to streamline engineering and create digital continuity. Top Performers are 2.6 times as likely to view the digital thread as critical to supporting their business strategy. Extend the Thread across the Lifecycle Adopt a comprehensive scope that incorporates cross-departmental data. Top Performers are more likely to include manufacturing, quality, and service plans in the scope of their digital thread, and enrich it with actual data from the IoT. Leverage PLM as the Digital Medical Device Backbone for Closed-Loop Quality, Continuity, and Streamlined Engineering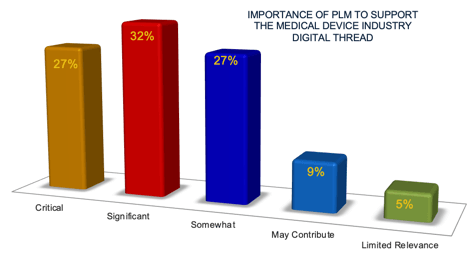
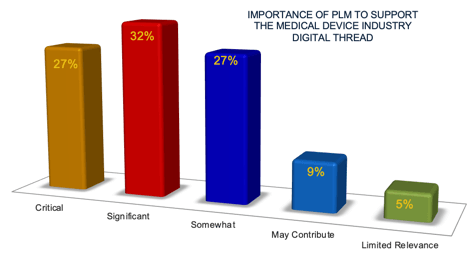
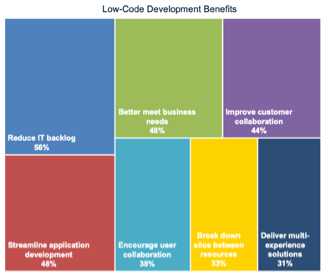
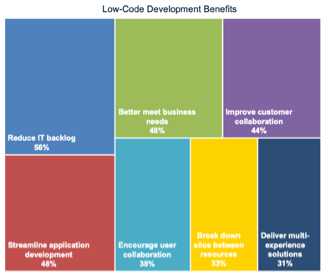
- Connect and communicate with equipment or products
- Monitor and analyze data and performance
- Notify and act on the findings


Table of Contents
- Digital Transformation Demands Development Agility
- Examining Digital Transformation Gaps
- Challenges
- Filling Digital Transformation Gaps
- IT Capabilities
- Exploring Low-Code Development
- Benefits
- Conclusions
- About the Research
- Acknowledgments
Digital Transformation
Digital Transformation Puts Pressure on Development Digital transformation is crucial to the success and profitability of today’s industrial companies. But transitioning to a digital business exposes shortfalls and creates gaps in most companies’ software ecosystems. Manufacturers must fill the gaps in their company’s processes, organizational approaches, and systems. Developing solutions to meet digital demands puts significant pressure on application development to do more – and do it faster! How can manufacturers improve the way they develop software applications to fill their digital transformation gaps and achieve their business strategies? We surveyed over 300 manufacturers to find out.Digital Transformation Demands Development Agility
Business Risk Survey respondents share that the digital transformation trend in manufacturing impacts companies in many ways. Digitalization creates business complexity and risk that challenge company viability. Our research shows that about three-quarters of companies shared that business risk and disruption increased for their market over the last five years, and a full one-half of companies with over 10,000 employees said that it had grown “significantly.” These risks demand rapid responses. Demand for Agility The most commonly reported business benefit is the flexibility to work anytime / anywhere, reported by two-thirds of participants. This is followed by ease of collaboration. This capability, along with the ability to have more integrated workflows as reported by about one-half of companies, allows OEMs and the supply chain to work together more efficiently and effectively. This is particularly important for Automotive companies given the global nature of their business, the need to be agile, and the integrated nature of the automotive value chain. Impact on Software Development Digital transformation’s impact on software needs is dramatic. It creates the need to update legacy solutions built for different times and increases the demand to integrate systems and people. It generates the need for new kinds of solutions, including personalized solutions that provide simpler, more focused “apps” that help users accomplish a task and the need to implement new technologies such as Artificial Intelligence (AI) and Augmented Reality (AR). Companies can’t expect to meet these demands if they continue developing solutions in the same way they have been.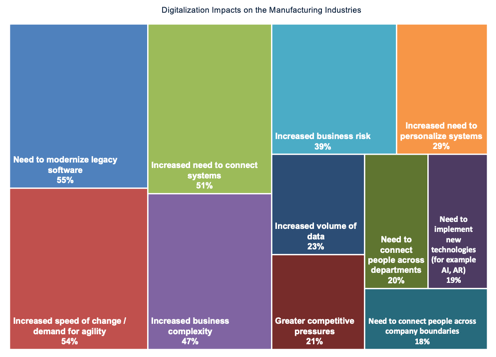
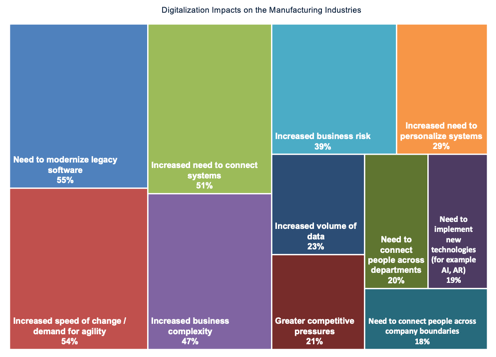
Conclusions
Digital Transformation Gaps Manufacturers are keenly aware that digital transformation increases business complexity and risk. Digitalization increases the speed of change, demands more agility, and creates the need for more (and faster) software development. The vast majority of companies have gaps across the digital transformation initiatives they are pursuing. Few companies can fill these gaps very well. This disadvantage is partly due to technical challenges and partly due to their poor ability to collaborate with critical subject matter experts. Filling Gaps with Low-Code Companies must fill their gaps and they are doing so by both building and buying solutions. Low-code development provides them with the ability to build custom their solutions faster. It also enables companies to integrate and extend their COTS solutions more rapidly. Although still in early adoption, low-code development addresses companies’ technical challenges, creates development agility, and supports collaboration so manufacturers can efficiently modernize legacy systems and deploy new applications. The result is that manufacturers using low-code development are better able to fill their digital transformation gaps. We believe that low-code development is a critical capability to explore to drive overall digital transformation efforts. *This summary is an abbreviated version of the ebook and does not contain the full content. For the full research, please visit our sponsor Siemens (registration required). If you have difficulty obtaining a copy of the research, please contact us. [post_title] => Can Low-Code Fill Gaps in Digital Transformation (survey results) [post_excerpt] => [post_status] => publish [comment_status] => open [ping_status] => open [post_password] => [post_name] => low-code-digital-transformation [to_ping] => [pinged] => [post_modified] => 2024-09-09 20:46:55 [post_modified_gmt] => 2024-09-10 00:46:55 [post_content_filtered] => [post_parent] => 0 [guid] => https://tech-clarity.com/?p=10320 [menu_order] => 0 [post_type] => post [post_mime_type] => [comment_count] => 0 [filter] => raw ) [8] => WP_Post Object ( [ID] => 10309 [post_author] => 2574 [post_date] => 2021-03-08 19:30:42 [post_date_gmt] => 2021-03-09 00:30:42 [post_content] =>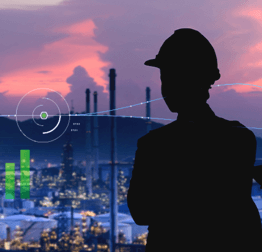
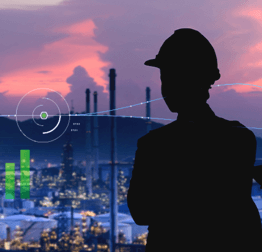
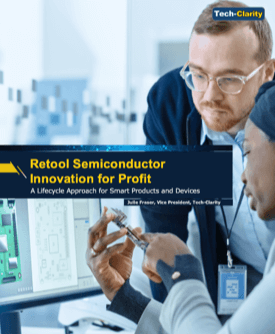
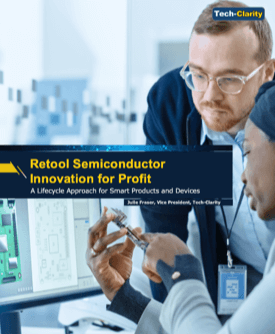
Table of Contents
- Executive Overview
- Opportunity Brings Challenges
- Retooling to Lifecycle Management Strategies
- Identifying the Top Performers
- Business Capabilities Matter
- Top Performers Manage Product Data Better
- Organizing and Supporting People for Success
- Semiconductor’s Complex Technology Landscape
- Tech-Clarity PLM Value Maturity Model
- Digital Continuity from PLM
- How Semiconductor Companies Differ from Their Customers
- Conclusions
- Recommendations
- About the Author
- About the Research
- Acknowledgments
Overview
Gaining design wins and getting each product into the market profitably is a puzzle. Solving that puzzle repeatedly and reliably is an enterprise- and ecosystem-wide endeavor that requires retooling semiconductor innovation to support that scope. Some appear to have done that. We identified these companies as Top Performers: the companies with the best revenue, profit margin growth, and revenue from products less than two years old. They think and act more holistically. Top Performers have better capabilities for ecosystem collaboration and IP protection, waste less time in product development processes, and have faster time to market. These leaders accomplish their higher performance through better use of commercial technology, including PLM. They have better access to data and digital continuity. Top Performers also exhibit higher digital maturity, managing and sharing data across partners and disciplines. The Top Performers show a way forward for semiconductor, electronics, and high-tech companies.Conclusions
Every aspect of life increasingly depends on semiconductors and electronics to become smarter. Opportunity is growing. Yet to seize it, companies must retool innovation in not only product technology but also enterprise and ecosystem processes. Remember, success rests on achieving product quality, reliability, performance, innovativeness, and cost all at once. Beating the competition in all those ways is no small feat. Top Performers’ Holistic View What differentiates Top Performers from Others is how much they have done to ensure their business and product innovation work effectively. They are better at cross-functional and multi-partner processes than others. Rather than settling for trade-offs, they have developed capabilities to balance all the objectives. They can design successful innovative products while at the same time being efficient and protecting their IP. This balanced view and set of capabilities enable them to get to market faster and more confidently with lower operating costs.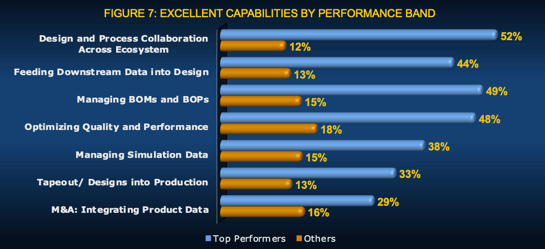
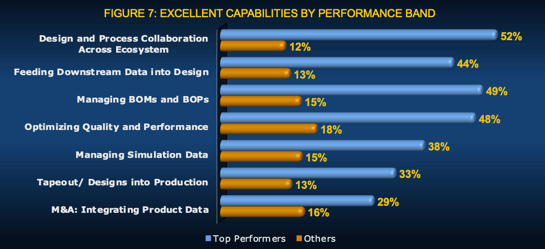
- managing their product data, whether BOMs, BOPs, simulation data, or IP
- digital continuity
- data access through the lifecycle
- using PDM or PLM technologies
- collaboration across their enterprise, ecosystem, and product lifecycle.
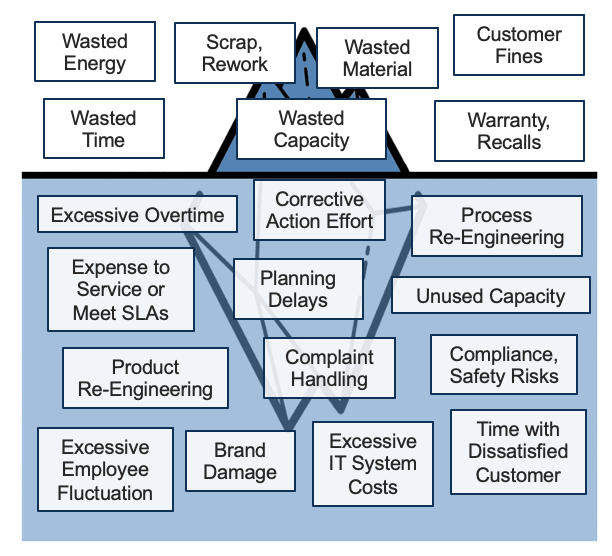
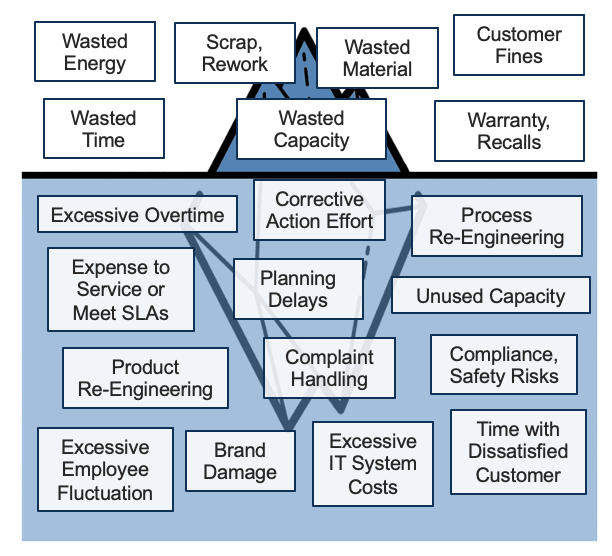
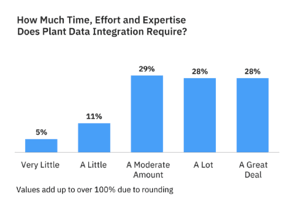
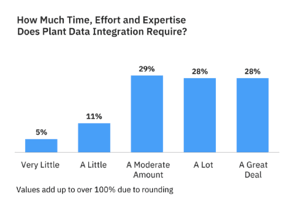
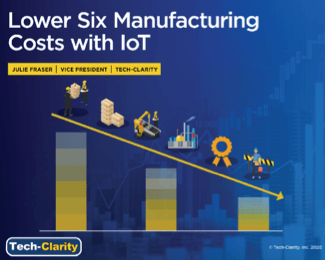
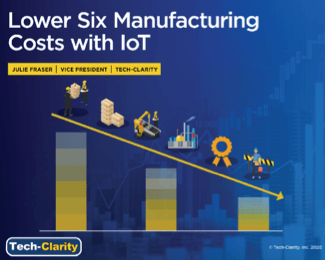
Table of Contents
- Cost and Margin
- Workforce Productivity
- Material Costs
- Asset Costs
- Energy Costs
- Cost of Quality
- Safety and Compliance Costs
- Recommendations
- Acknowledgments
Cost and Margin
Age-old Manufacturing Challenges Margins matter. Ever since people began turning materials into higher-value goods and selling them for a living, lowering costs has been an objective for manufacturers. In the margin equation (simplified to income minus expenses), costs are often the easiest to control. For manufacturers, operating costs are a logical place to seek improvement. Manufacturing inherently has a set of input costs: workforce, materials, machinery, energy; lowering those costs improves operating margin. Problems with quality, safety, or compliance can add to the margin squeeze. Smarter Manufacturing to Lower Costs Each advancement in production methods and information technology has allowed better and less expensive production. Previous moves from artisans to steam power to mass production to control automation have each done this. Costs continue to drop with the transition to IT in operations and today’s IoT-connected distributed intelligence. Yet those savings require initial investments to create a smart connected factory. New technologies offer specific ways to reduce costs. We’ll show them in six primary areas:- Workforce productivity
- Materials
- Assets
- Energy
- Quality
- Safety & Compliance
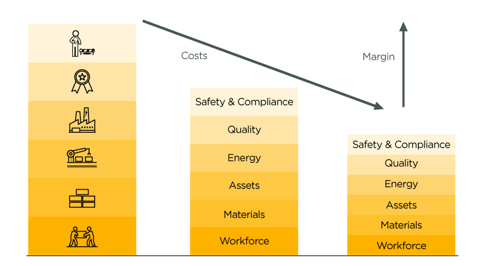
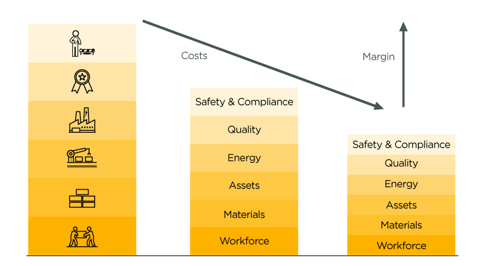
Recommendations
Continuing Cost Reductions Cost improvements are crucial for manufacturers to remain profitable in the “new normal.” Fortunately, technologies for every level are now available to reduce operating costs across all six dimensions. Capabilities to bolster include sensing, monitoring, communicating, analyzing, predicting, and displaying operational data and performance indicators. As with previous generations of manufacturing technology, adding new technologies can create incremental – and sometimes dramatic – cost reductions. Some are one-time savings; many continue to reduce costs. Actions to Get Started While every company’s cost structure and situation is different, there are some things every manufacturer should do.- Examine operating costs and focus efforts on significant needs or easy-to-identify wastes.
- Add IoT sensors to gather more data where critical opportunities lurk.
- Provide workers with as much support as possible through work instructions and remote expert support on-line or through AR goggles.
- Use all data feeds available to monitor materials, processes, and equipment precisely.
- Assess energy and quality in detail and add guidance or monitoring to keep costs in line with revenues.
- Consider compliance and EH&S systems – are you still facing risks?
- Consider how new technologies in this paper will integrate with and leverage current automation and software systems.
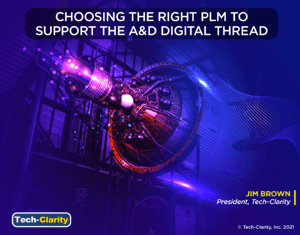
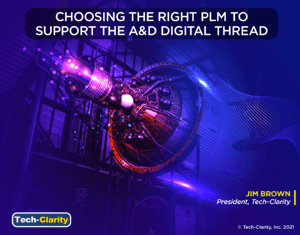
Table of Contents
- Choosing the Right PLM
- Introducing the Buyer's Guide
- The Digital Thread Imperative
- What to Look for to Streamline Engineering
- What to Look for to Create Digital Continuity
- Digital Thread Business Value
- Considerations by Role - Engineering
- Considerations by Role - Manufacturing
- Considerations by Role - Quality
- Considerations by Role - IT
- Considerations by Role - Service
- PLM is the Digital Thread Backbone
- Special Considerations - Emerging Technologies
- Implementation Considerations
- Vendor Considerations
- Conclusions and Next Steps
- About the Research
- Acknowledgments
The Digital Thread Imperative
Business Strategies Demand a Cohesive Digital Thread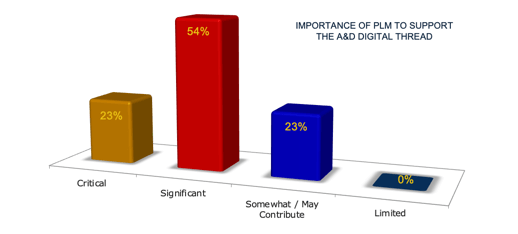
Conclusions and Next Steps
Invest in the Digital Thread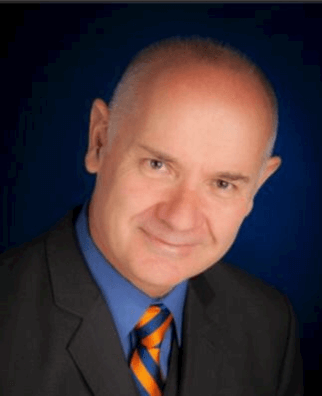
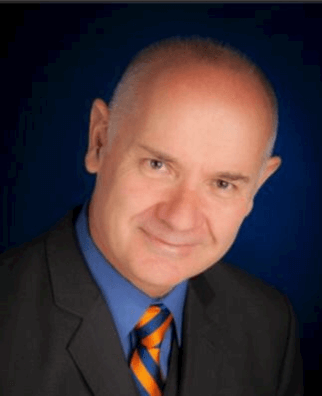
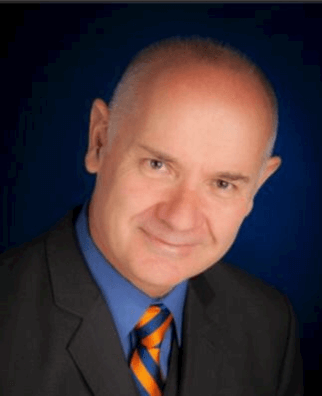
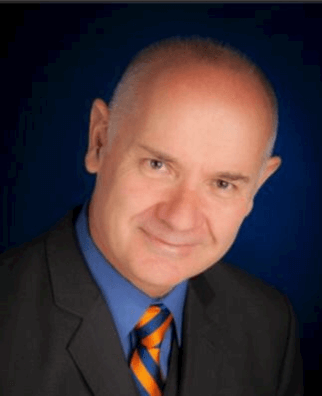
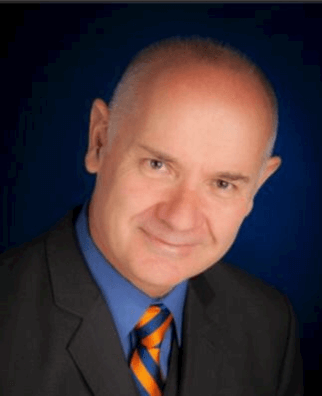
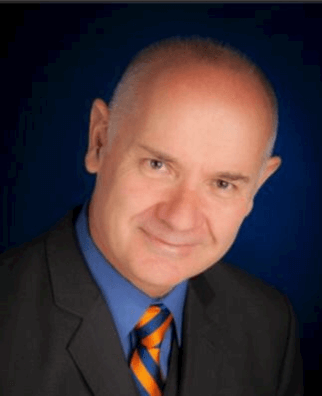
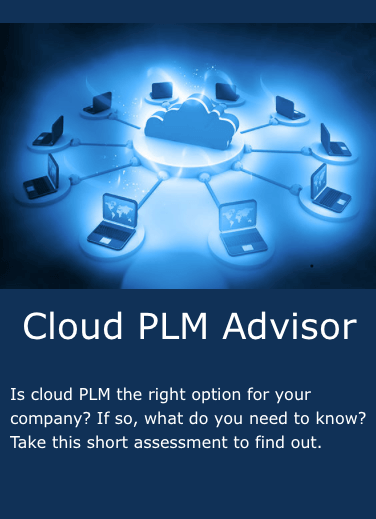
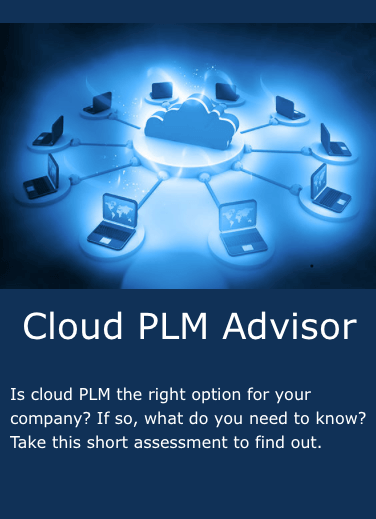
- Strategy
- Functionality
- Governance
- Existing Solutions
- Cloud Transition
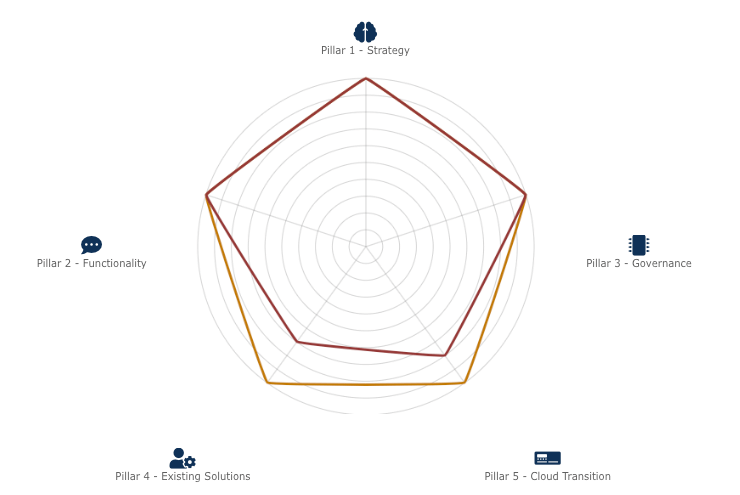
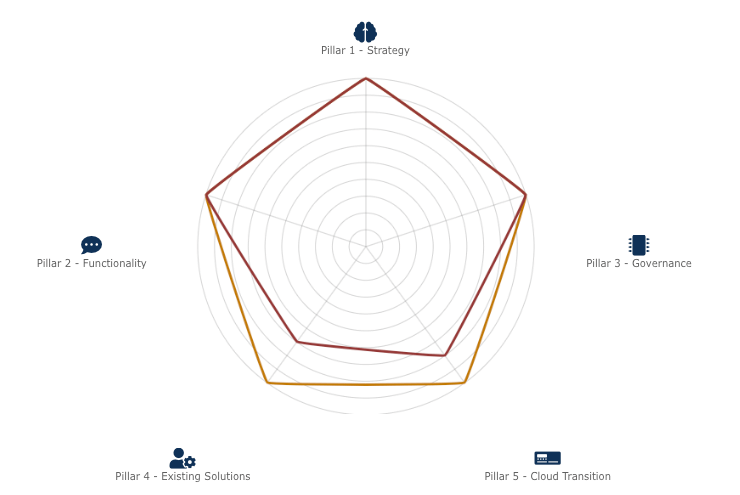
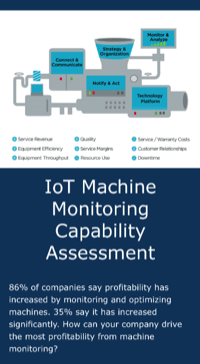
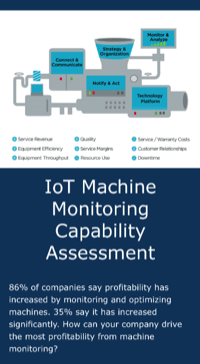
- Compares your capabilities to Top Performing companies
- Offers tailored recommendations to improve performance
- Strategy and Organization
- Connect and Communicate with Equipment
- Monitor and Analyze
- Notify and Act
- Technology Platform
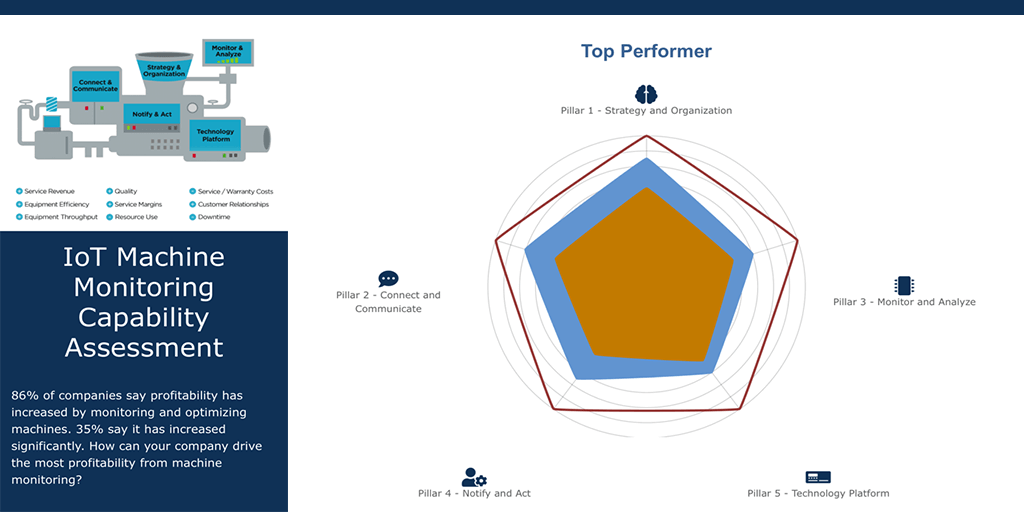
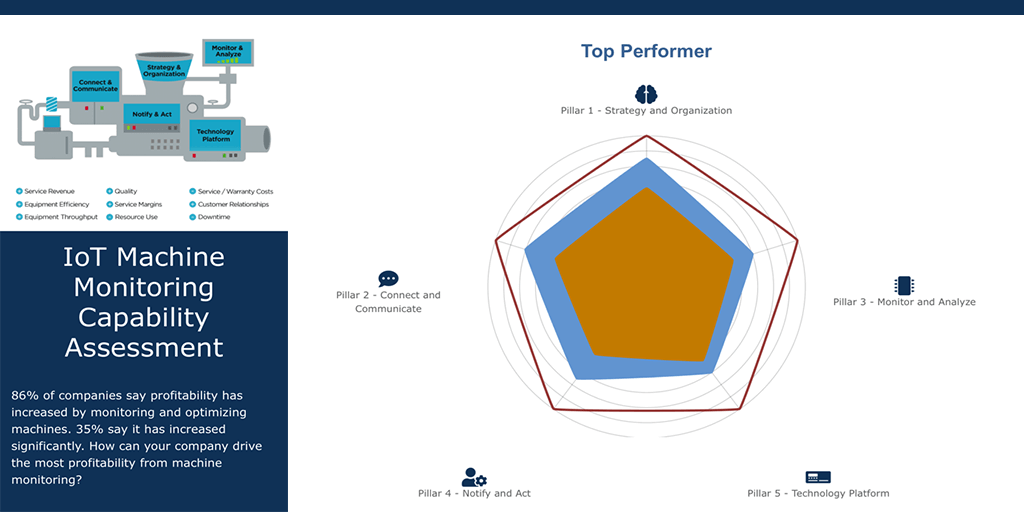
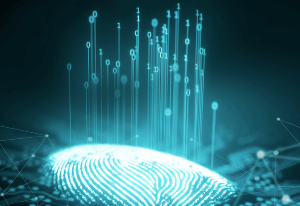
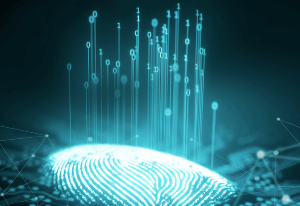
- Challenges for profitability
- What Top Performers are doing to succeed
- Key process capabilities to improve
- Technology supports for digital continuity
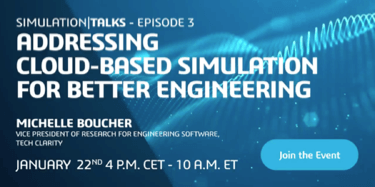
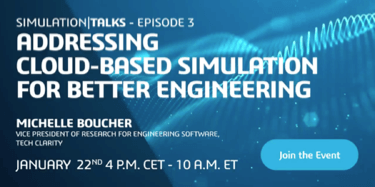
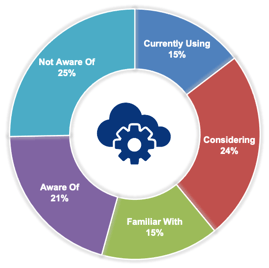
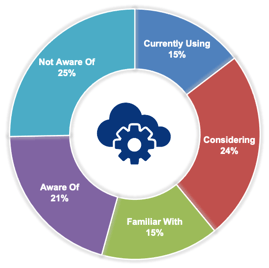
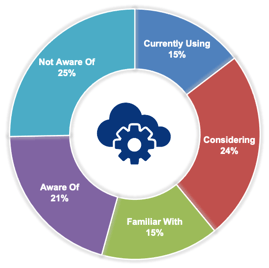
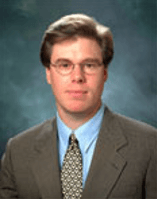
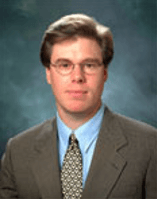
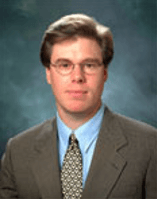
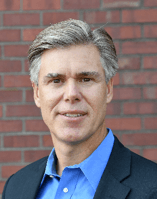
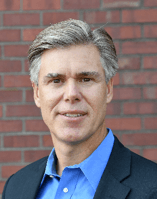
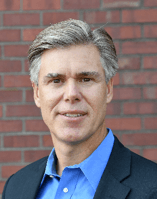
All Results for "All"
The Power in the Hidden Factory: Unlocking the Untapped Potential in Manufacturing Operations (webcast)
Could your production operation be more productive? Sometimes it’s difficult to tell, despite having plenty of data. Sometimes, metrics like overall equipment effectiveness (OEE) don’t even help uncover the hidden factory. Yet, OEE can and should pinpoint opportunities. Find out how to improve more reliably in this June 2021 webcast. Listen in to Tech-Clarity’s Julie…
Buyer’s Guide for Digital Work Instructions
With increasing demands for highly skilled operators, yet a shortage of workers with those skills, what can manufacturers do to boost manufacturing productivity? With workforce shortages, market volatility, and rising costs plaguing most manufacturers, many are turning to new ways of operating, and digital transformation is playing a pivotal role. Digital work instructions can be…
How Software Enables Industrial Additive Manufacturing (webcast)
What role does software play in the maturation of additive manufacturing to industrial scale? This live webcast, hosted by Jim Brown and Igor Tsinman, President of AMC Bridge, explores the symbiotic relationship between additive manufacturing technology and the software applications that work cohesively with them. The panel includes Igal Kaptsan – General Manager Software of GE…
Michelle Boucher Speaks at Big Lever’s Momentum 2021 Symposium
What role should feature-based Product Line Engineering (PLE) play in a digital transformation strategy? On May 11-12, 2021, Big Lever will be holding their Momentum 2021 Symposium and this question will be the underlying theme of the event. Tech-Clarity’s Michelle Boucher will join the list of speakers and she will explore the question, why should…
PLM for the Medical Device Digital Thread (buyer’s guide)
How can PLM enable medical device companies to streamline engineering and create digital continuity with a cohesive medical device digital thread? What should they look for in a PLM solution to improve closed-loop quality and patient outcomes while meeting complex, regional compliance demands? This eBook takes a deeper dive into the data from our original, cross-industry digital thread study to…
Fill IoT Gaps with Low-Code (guest post)
How can low-code help fill digital transformation gaps to help companies achieve the value of IoT opportunities? Jim Brown’s guest post on Siemen’s blog shows how companies can fill IoT gaps with low-code applications. Below is a short summary, click here to read Jim Brown’s full guest post on the Siemen’s blog. Digital Transformation Creates Opportunities Today’s…
Can Low-Code Fill Gaps in Digital Transformation (survey results)
Digital transformation creates, exposes, and widens gaps in processes, organizational approaches, and systems. This leads 96% of industrial companies to say they need to create and implement new software more quickly. Addressing these application shortfalls is critical to long-term business success. Is developing applications with low-code the answer to filling the gaps? We surveyed over…
How Advanced Analytics in Manufacturing Can Lead to Cost Cuts (guest post)
Could deeper insights lower some manufacturing costs? For years, continuous improvement programs have successfully lowered operating costs. Now, companies are using advanced analytics in manufacturing to find even more opportunities. This is not your father’s analytics. Rather, it correlates among different data sources, including IoT, to deliver fresh insights for confidently moving to reduce costs….
Retool Semiconductor Innovation for Profit (survey results)
How can semiconductor companies make their product innovation even more profitable? By moving beyond technical prowess. By retooling innovation for a modern lifecycle management approach for digital continuity. This white paper is based on a Tech-Clarity survey of 277 semiconductor and high-tech professionals to find out how semiconductor companies manage product development and product lifecycles….
What is the Cost of Poor Quality in Your Manufacturing Environment? (guest post)
What does Poor Quality Really Cost? Calculating the actual cost of quality problems is not straightforward. Some of the expenses are apparent, but many are not. Quality is important to customers and to business profitability. So, truly understanding the cost of quality warrants the effort. Fortunately, advanced manufacturing technologies can help analyze and understand expenses…
Manufacturing Data: Can It Finally Flow? (guest blog)
What current challenge have manufacturers been wrestling with for at least 35 years? System integration. Getting manufacturing data to flow has always been a problem. And it still is. Based on Tech-Clarity research The Manufacturing Data Challenge: Lessons from Top Performers, most of the 300 respondents’ companies need better ways to integrate IT and OT data….
Lower Six Manufacturing Costs with IoT (eBook)
How can IoT and advanced technologies lower costs in manufacturing? Lower Six Manufacturing Costs with IoT explores how new technologies can help keep age-old manufacturing expenses in check. The report discusses how the Internet of Things (IoT) and related technologies for monitoring and using data can streamline processes and support people in making profitable decisions….
Choosing PLM for the A&D Digital Thread (survey results)
How can Aerospace and Defense (A&D) companies streamline collaboration and create digital continuity? What should they look for in a PLM system to support a cohesive digital thread, especially given that their IT systems were not designed for remote work during a pandemic? This eBook takes a deeper dive into the data from our original,…
Tech-Clarity adds Digital Innovation and Transformation Analyst James White
Tech-Clarity is pleased to announce that we are expanding our research team and extending our coverage of Digital Innovation, Digital Transformation, and Additive Manufacturing. Well-known industry thought leader and research analyst James White is joining Tech-Clarity as Vice President of Digital Innovation Research. James brings with him decades of experience in Digital Enterprise specializing in…
James White
James White is the Vice President of Digital Innovation Research for independent research firm Tech-Clarity. He covers the Digital Enterprise specializing in Digital Transformation, Design Innovation, PLM, Industrial Additive Manufacturing, BIM, and other solution areas for manufacturers. He began his career in special purpose machine design before moving into the CAD/CAE/PLM industry focused on heavy…
Are You Ready for Cloud PLM? (online assessment)
Is cloud PLM the right option for your company? If so, what do you need to know? Take our Cloud PLM Advisor assessment to find out. The assessment leverages our research to assess your company’s readiness to transition to the cloud. Should you switch to a new system? Wait for your current solution to be…
Benchmark Your IoT Machine Monitoring Capability (Performance Assessment)
How does your company stack up in its ability to monitor and optimize equipment performance using the IoT? Answer a few questions in our IoT Machine Monitoring Assessment and you’ll get a customized report that: Compares your capabilities to Top Performing companies Offers tailored recommendations to improve performance The assessment leverages our survey data to…
Semiconductor Innovation for Profitability (webcast)
Semiconductor innovation is multi-faceted; can lifecycle management improve product and thus business success? This on-demand webinar features Julie Fraser sharing Top Performers’ best practices for digital continuity based on her new semiconductor industry research. Semiconductor companies are great at technical innovation, but many do not have all the capabilities they need for product profitability. The…
Cloud-Based Simulation for Better Engineering
How can design engineers improve confidence in simulation results? Can cloud-based simulation help? Watch Michelle Boucher as she shares best practices from her research to explain how design engineers can get even more value from simulation. Simulation can be a powerful design tool by providing engineers with design guidance. However, some are concerned they lack the…