How can manufacturers adopt cloud PLM to support digital transformation but avoid being stuck with a dead-end, custom system? Is it time to force a hard decision between customization and the cloud? Read Digital Transformation Driving PLM to the Cloud to learn what three leading manufacturers and our research have to say. How today’s manufacturers…
- How today’s manufacturers are leveraging cloud PLM to support their digital transformation initiatives
- The business triggers that lead to upgrading current PLM solutions
- The compelling benefits of cloud and architecture choices that need to be made
- How low-code PLM can support digital transformation
Table of Contents
- Executive Summary
- The Manufacturer's Viewpoint on PLM
- The Need to Upgrade PLM
- Cloud is Compelling
- Evaluating PLM Deployment Options
- Out-of-the-Box (OOTB) is a Fallacy
- Functionality First
- Cloud and Custom Aren't Incompatible
- Key Takeaways
- Acknowledgments
Executive Summary
Digital Transformation Demands New Capabilities, Agility Digital transformation is intensifying the need to tailor PLM systems to serve as a company’s digital backbone and support new ways of innovating and operating. Engineers need the latest features and capabilities, but also need to keep the “right-for-me” PLM capabilities they already have. PLM solutions that are customized to achieve these goals, however, can create an ongoing need for specialized services that can limit agility and prevent adoption of new features and software versions. Transitioning to the Cloud Cloud solutions are compelling but are not commonly as tailorable as traditional solutions to provide a customized experience. Cloud offers numerous business and technical advantages including lower costs, less need for IT support, strong security, high availability, and practically infinite scalability. The tradeoff is typically a more out-of-the-box (OOTB) solution with lower ability to customize to enforce company standards and provide the right experience to the end user. "Cloud" and "Customization" can Co-Exist Our experience shows that most PLM implementations are not OOTB, especially for large organizations. This creates tension between cloud benefits and creating the new digital backbone and a “right-for-me” experience. As our experience and the research for this eBook shows, however, the right balance between cloud benefits and desired customization may be available through the emerging alternative to customization, low-code / no-code development.Evaluating PLM Deployment Options
Cloud Comes in a Variety of Options Cloud is compelling, but “the cloud” is not a single option. There are multiple ways to implement PLM. Let’s look at the impacts of the different options on factors like cost, agility, and the ability to customize for the “right for me” experience. Note that these are generalizations and we recognize that there are exceptions to every rule.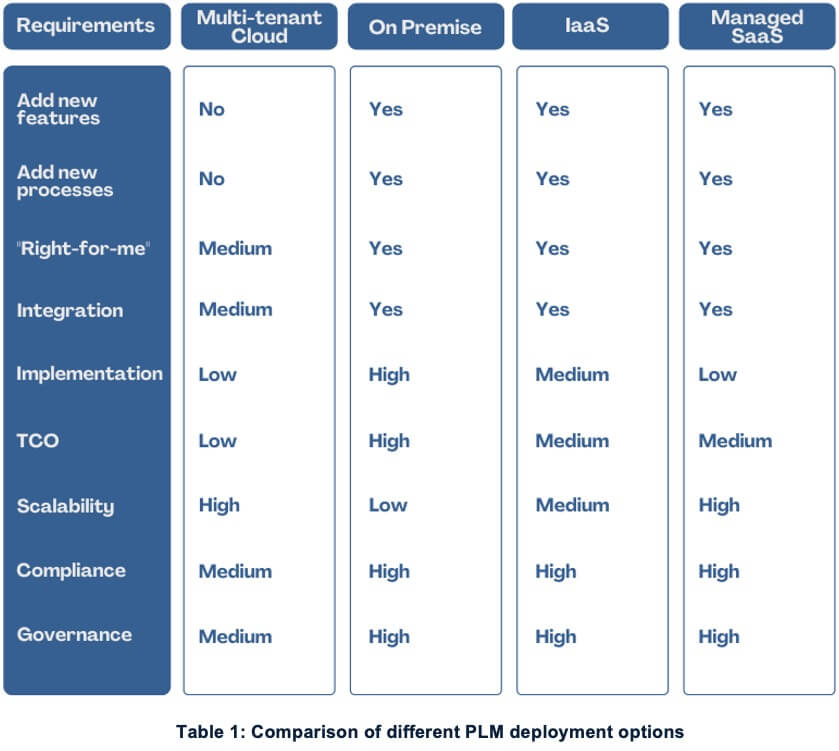
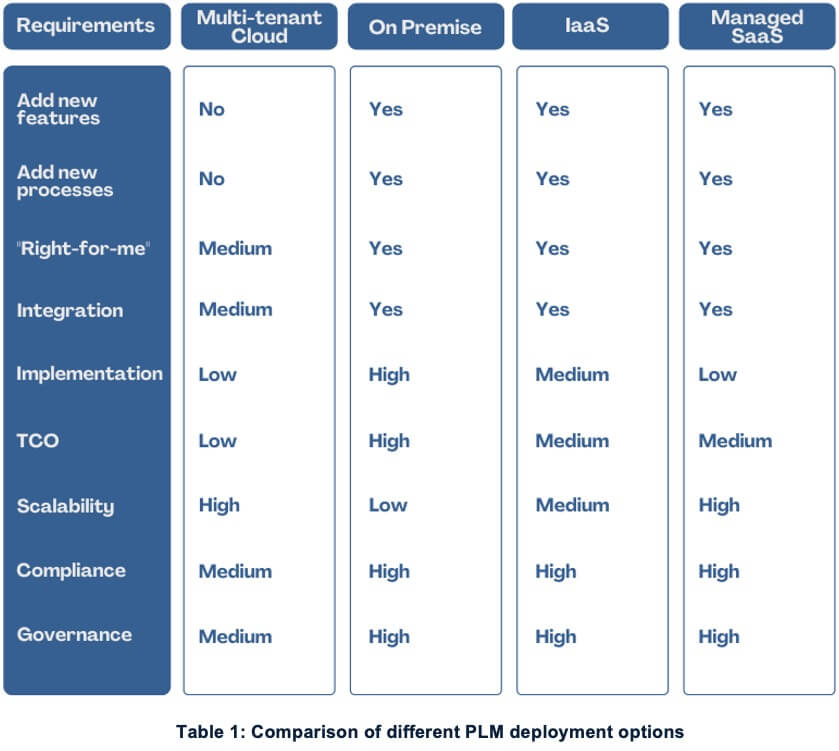
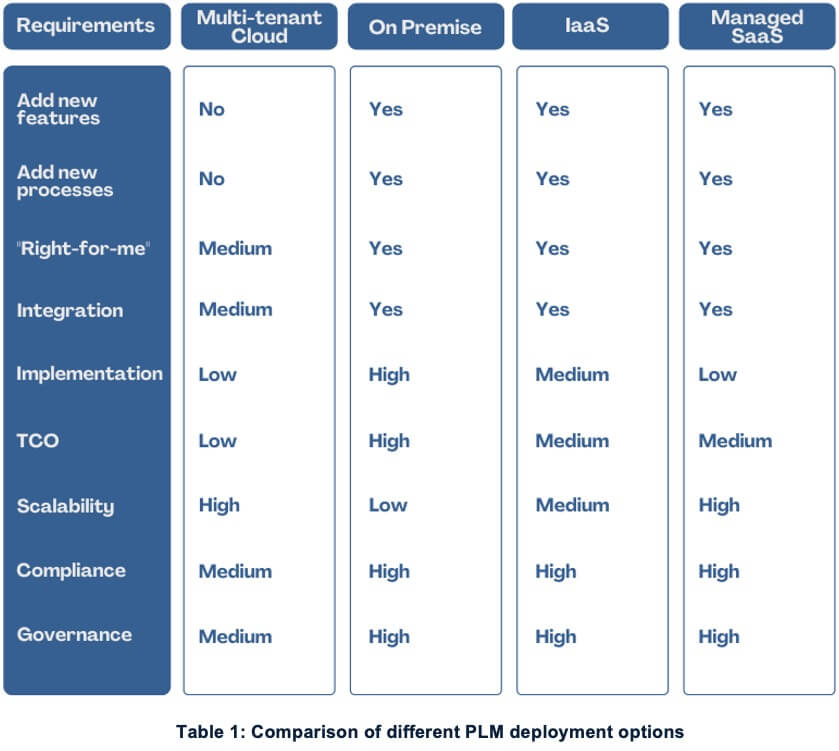
Key Takeaways
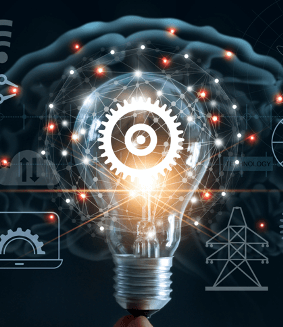
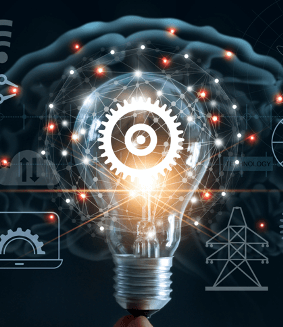
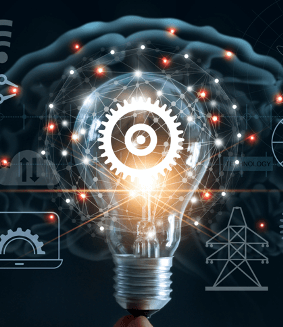
- PLM is becoming the digital backbone for manufacturers’ digital transformation strategy
- Most engineers prioritize PLM functionality and the “right-for-me” experience over cloud benefits. Traditional customization approaches lead to large technical debt and can result in dead-end customizations.
- PLM is a business imperative, and like the business, it’s a moving target. It’s important to have the ability to adapt the PLM system as needs change, to remain agile, without adding technical debt.
- Cloud and customization can both be options at the same time. The right PLM architecture can provide cloud benefits while also enabling customization without incurring significant technical debt.
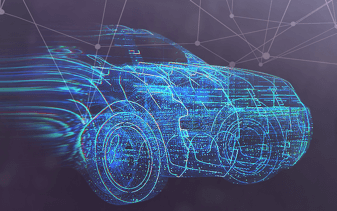
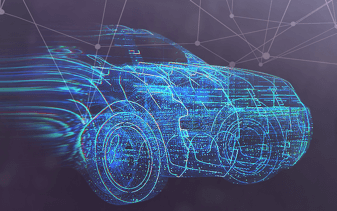
- How MBSE is different
- The value of a model-based approach vs. document-based
- Success factors for a model-based approach
- Challenges to look out for
- Advice to implement it
- Shelly Kramer, Lead Analyst and Founding Partner, Futurum Research
- Jim Anderton, Director of Content, engineering.com
- Douglas Orellana Ph.D, CSEP, OCSMP, ITIL4, SPC5, Vice President of Intelligent Systems Engineering, ManTech
- Michelle Boucher, Vice President of Research for Engineering Practices, Tech-Clarity, Inc
- Saulius Pavalkis, Industry Business Senior Consultant and MBSE Transformation Leader, CATIA Dassault Systèmes
- Sept. 22: Digital Transformation-Where Do We Go From Here?
- Sept. 23: How Manufacturing Success starts with Virtual + Real Operations
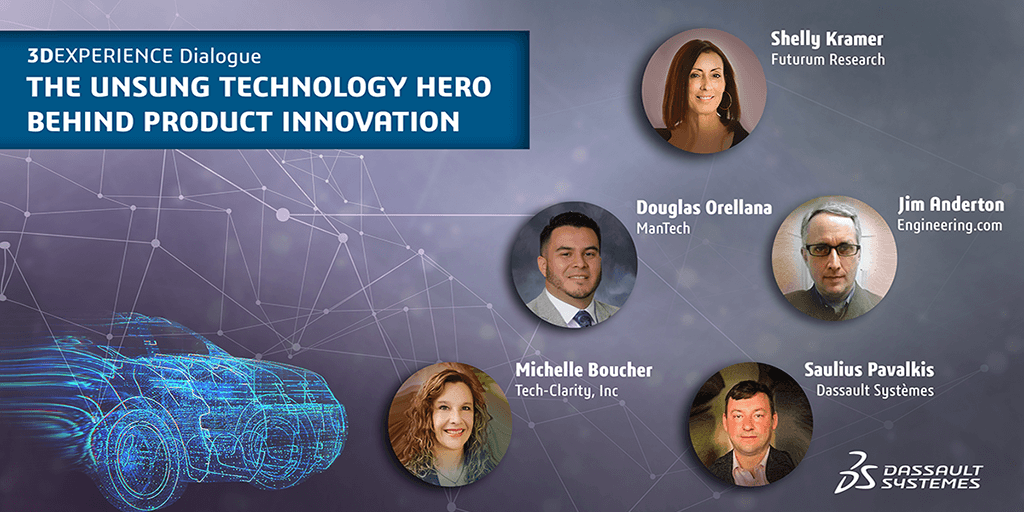
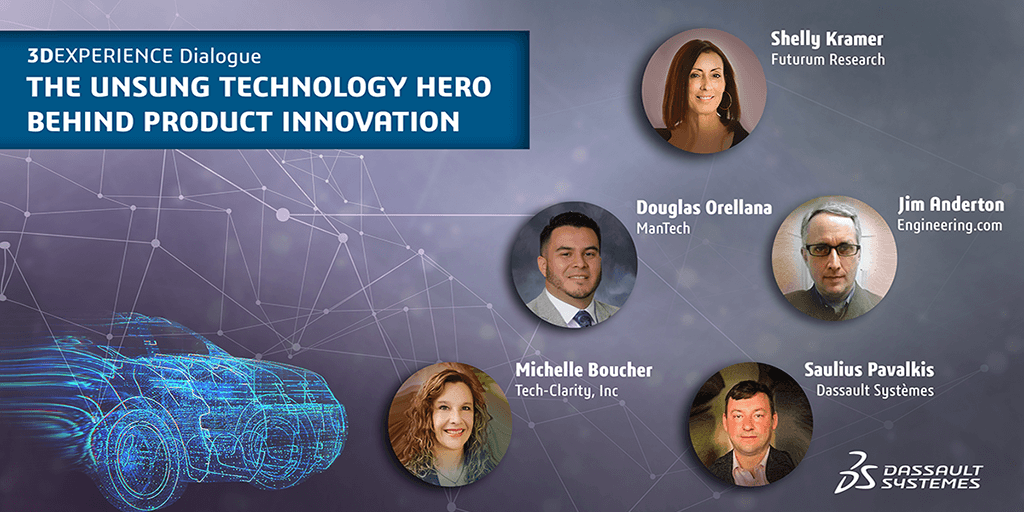
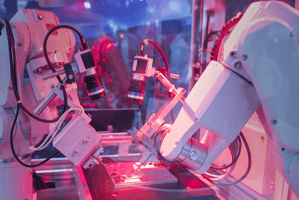
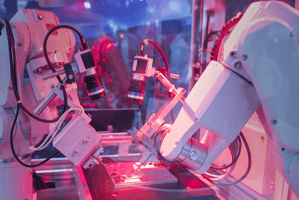
- Lower Six Manufacturing Costs with IoT (eBook)
- What is the Cost of Poor Quality in Your Environment (guest blog post)
- How Advanced Analytics in Manufacturing Can Lead to Cost Cuts (guest post)
Understanding MBSE: Your Secret Weapon for System Complexity
Staying Competitive Has Led to Increased Complexity

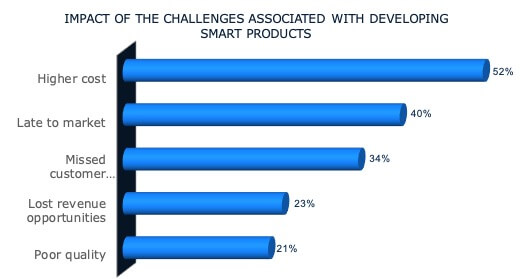
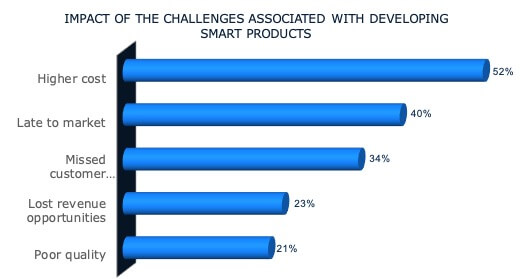
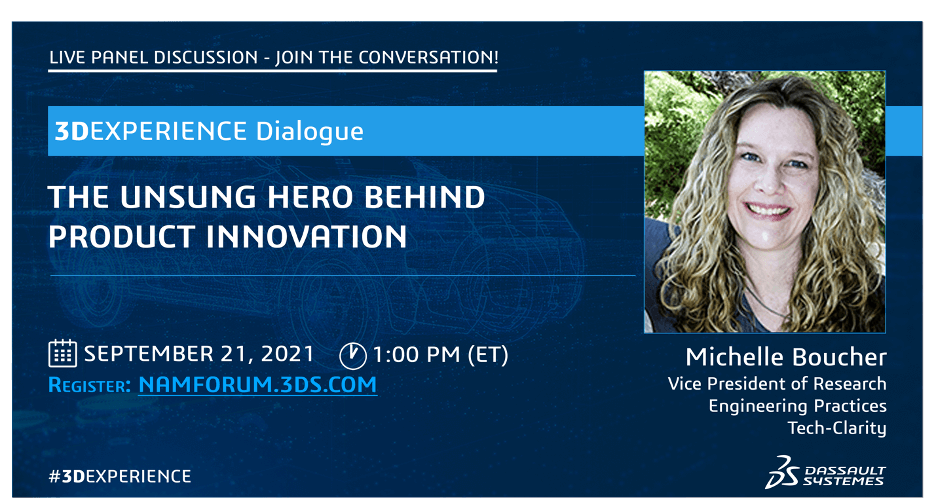
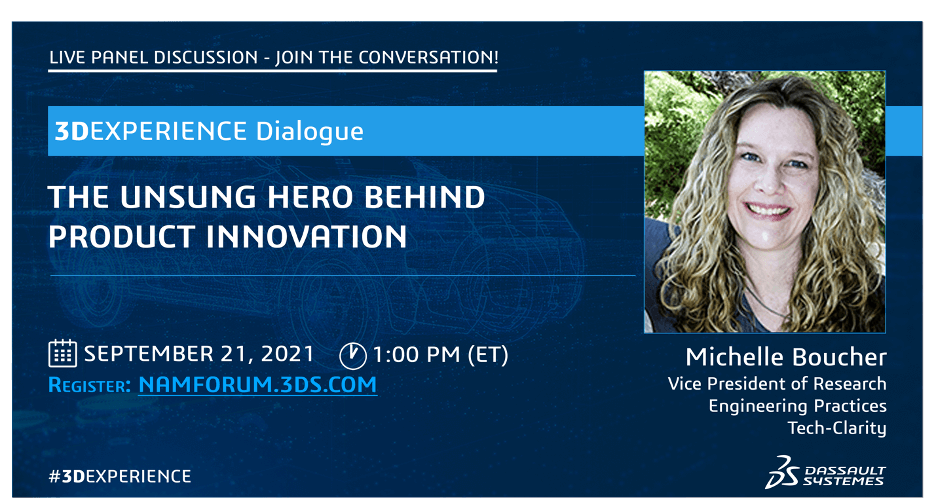
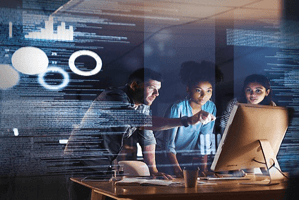
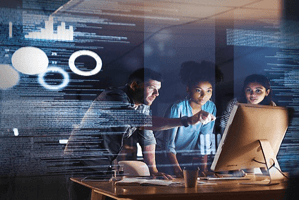
- The importance of digital transformation to business strategy
- The impact of digitalization on existing applications
- Which transformation initiatives generate the most gaps
- Common challenges developing apps
- The benefits of a low-code development approach
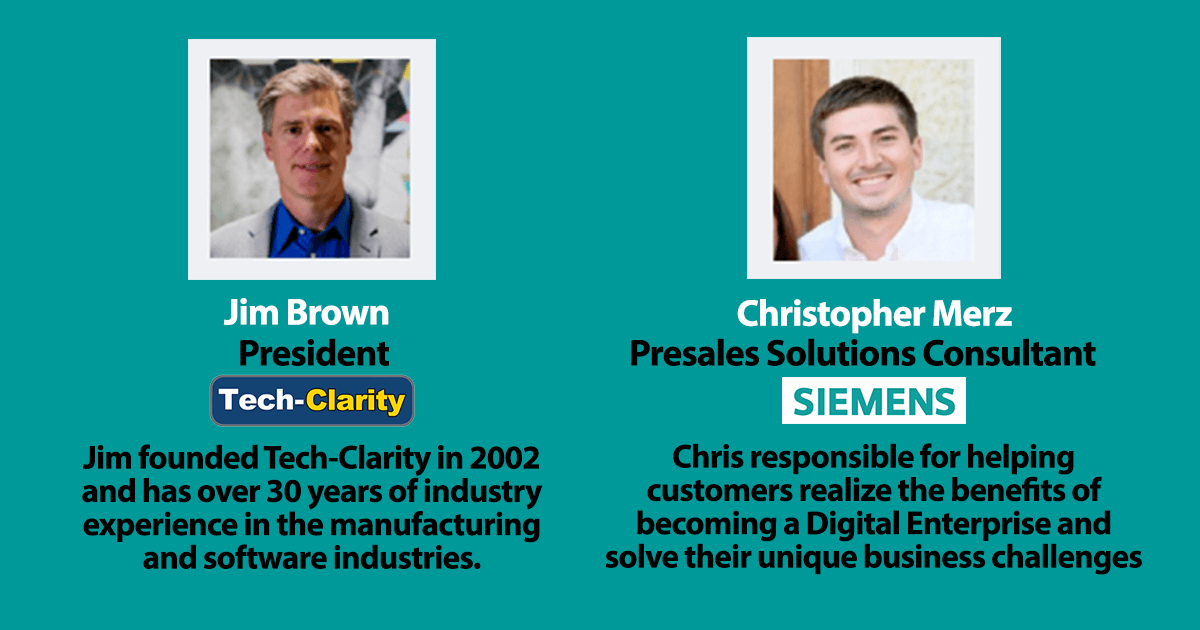
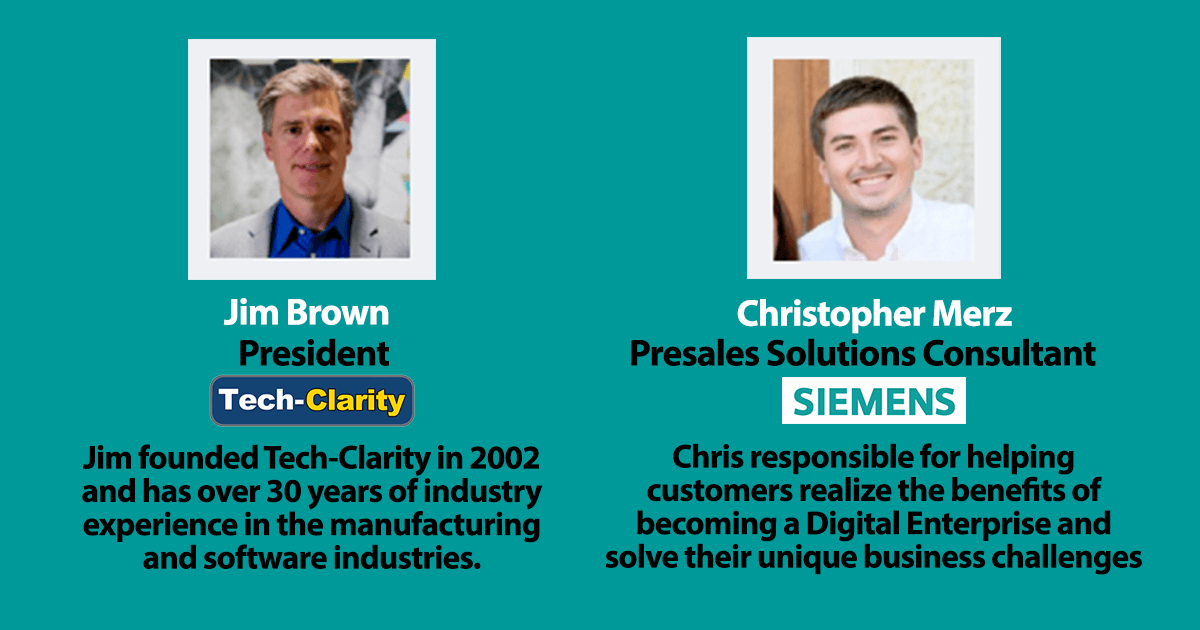
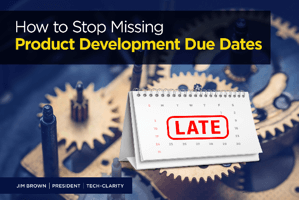
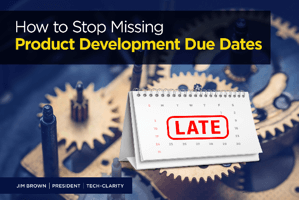
Table of Contents
- Executive Overview
- Individual Productivity or Process Efficiency?
- The Impact of Product Development Efficiency
- Process Efficiency from Better Collaboration and Coordination
- Process Efficiency from Data Management
- How Can Companies Improve NPD Performance?
- Top Performers Have Better NPD Coordination, Collaboration
- Top Performers Have Digital Data Continuity
- Top Performers Have a Cohesive Product Data Model
- Recommendations and Next Steps
- About the Research
- Acknowledgments
Executive Overview
Manufacturers Consistently Miss NPD Targets New product development (NPD) speed and agility have a clear impact on competitiveness and product profitability. Unfortunately, an earlier Tech-Clarity study found that manufacturers miss project launch dates 45% of the time2. The research also showed that time-to-market demands had increased for about two-thirds of manufacturers. Engineering Inefficiency is a Big Issue New product development (NPD) speed and agility have a clear impact on competitiveness and product profitability. Unfortunately, an earlier Tech-Clarity study found that manufacturers miss project launch dates 45% of the time2. The research also showed that time-to-market demands had increased for about two-thirds of manufacturers. Identifying Best Practices in NPD Is improving engineering efficiency enough to solve the long-time issue of missed product development dates? We believe there is more to this puzzle. We analyzed survey responses from 167 companies and identified those that were better able to develop products rapidly and efficiently while maintaining product development agility. Then, we analyzed what these “Top Performers” do differently than the poorer-performing “Others.” Top Performers Streamline NPD with a Cohesive Digital Thread Researchers found that the Top Performers are more likely to streamline their NPD process by creating digital continuity. In specific, they are twice as likely as Others to have full digital data continuity across phases or steps in their product development process. In a related finding, they are 37% more likely to leverage a common data model across the stages of new product development. This common product definition with full digital continuity creates a cohesive digital thread. The report explains these findings in depth and shares additional capabilities that Top Performers have mastered more than Others. Read more to learn how your company can improve NPD performance and profitability.Individual Productivity or Process Efficiency?
Time-to-Market Takes More Than Individual Productivity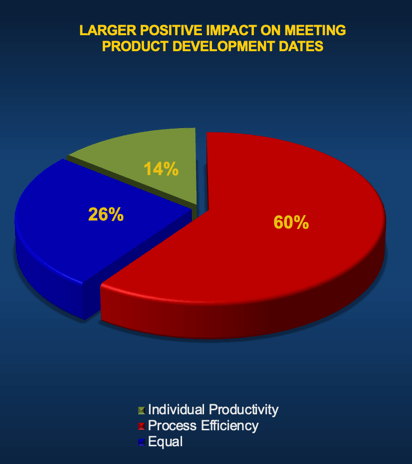
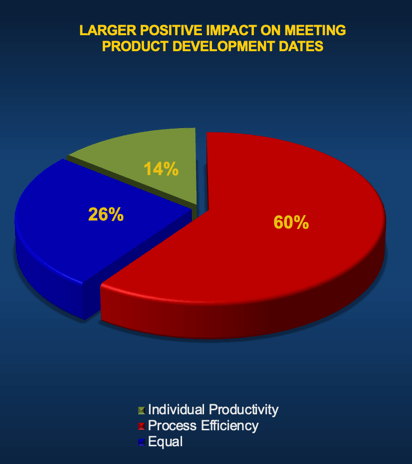
- Productivity of individual contributors (designers, engineers, etc.)
- Overall process efficiency (workflows, project execution, collaboration, coordination, working as a team, etc.)
- Both equally
Recommendations and Next Steps
Improve Product Development Capabilities, Drive NPD Results Clearly, manufacturers can’t choose between engineering efficiency and product development speed, productivity, and agility. They need both. In addition to reducing non-value-added work in engineering, they must adopt the Top Performers’ best practice processes in order to improve new product development speed, efficiency, and agility. The challenges and benchmarked capabilities lead us to recommend that manufacturers should streamline new product development with full digital continuity on a common data model, creating a complete digital thread to improve NPD performance. To do this, they should adopt best practice processes and technology. Streamline Processes and Transitions Manufacturers should streamline transitions between project phases by:- Implementing formal, cross-departmental processes
- Providing cohesive design and product development data needed for reviews, approvals, and change management
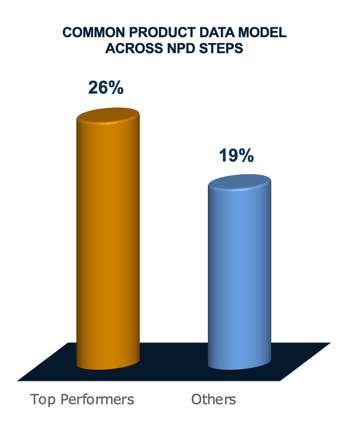
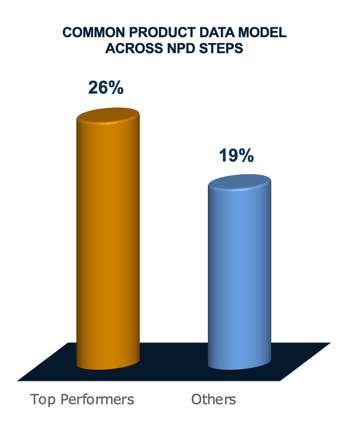
- Providing a common data model and digital data continuity across product design and development phases
- Promoting communication and collaboration across departmental boundaries and encouraging project-level coordination
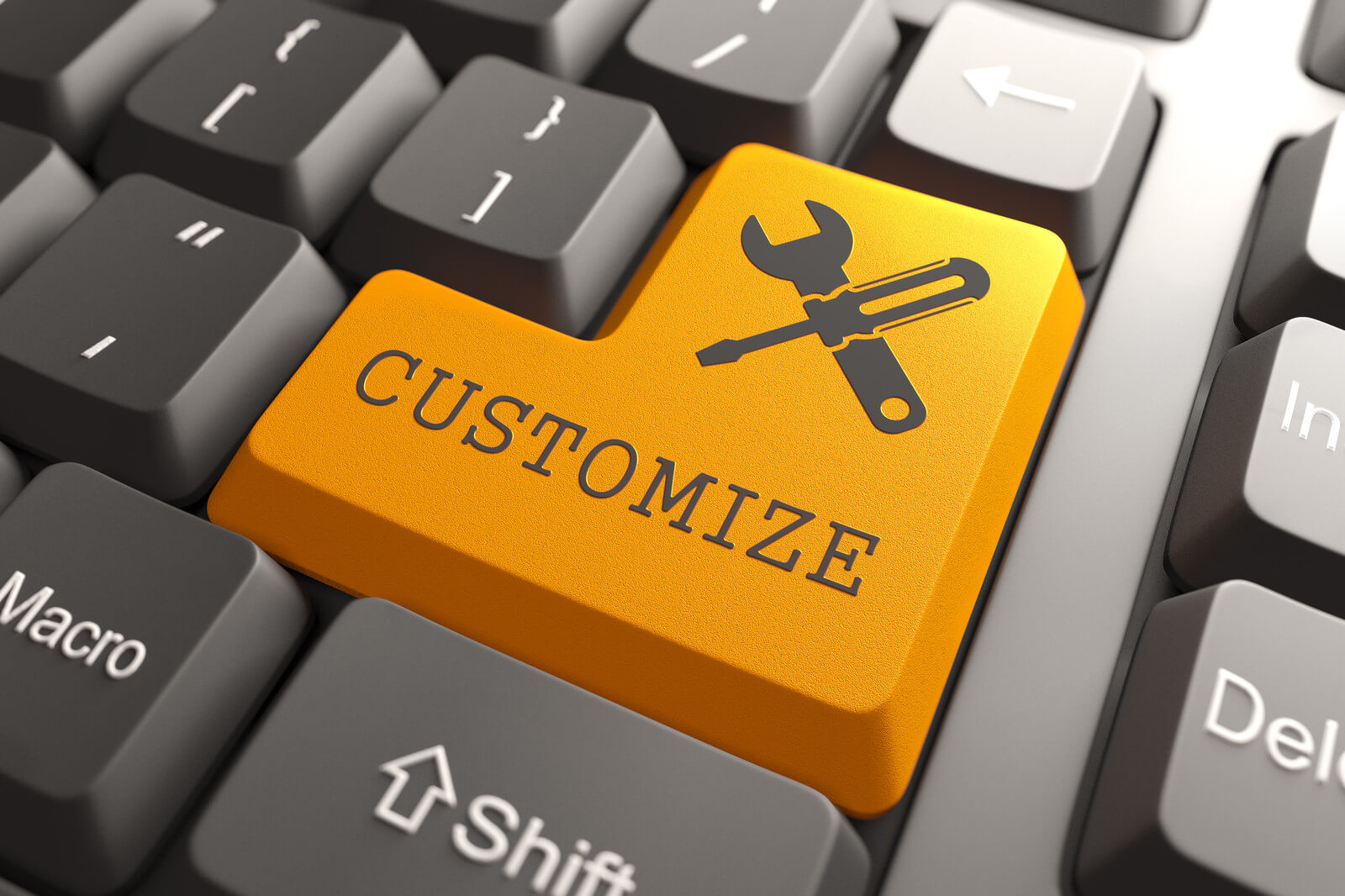
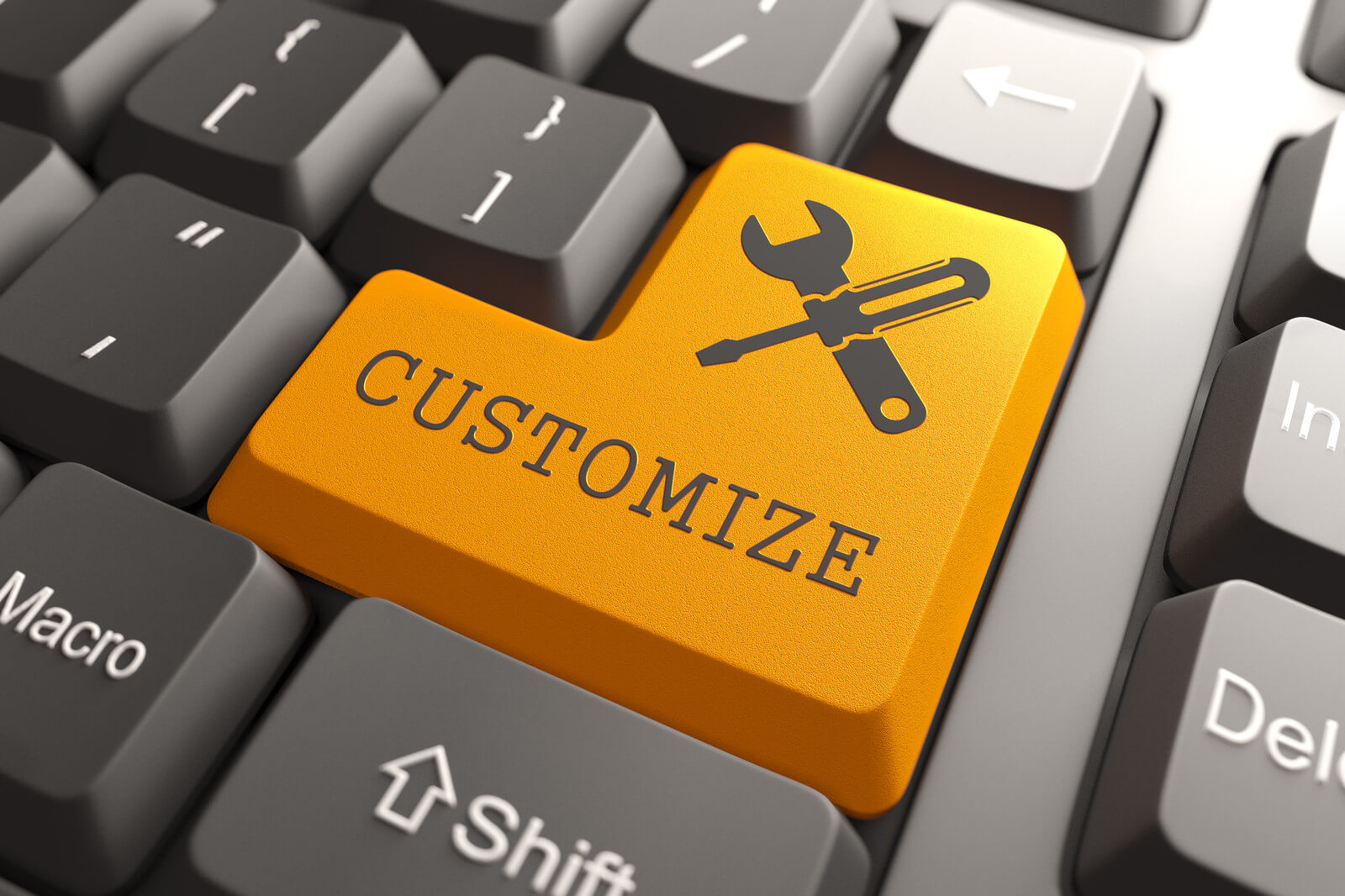
- How today’s manufacturers are leveraging cloud PLM to support their digital transformation initiatives
- The business triggers that lead to upgrading a custom PLM solution
- The compelling benefits of cloud and the choices that need to be made
- Merging the operational phase of the product lifecycle with the voice of the customer
- Closing the loop to deliver a true customer-centric product experience
- Integrating product and customer experience elements from several underlying systems
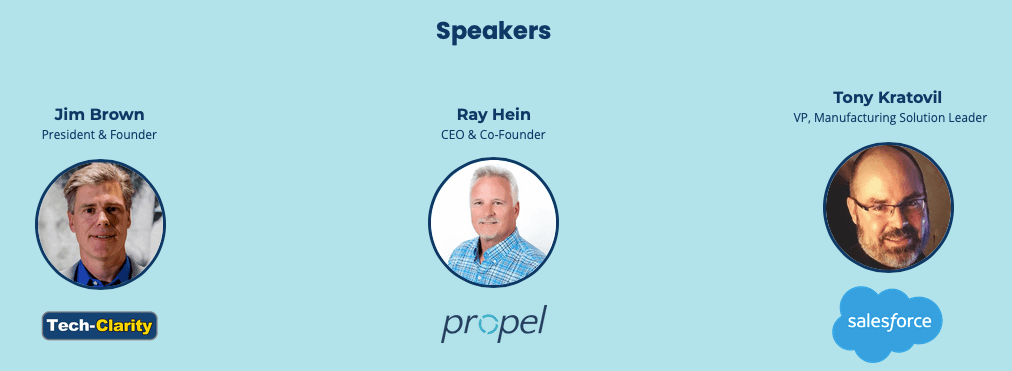
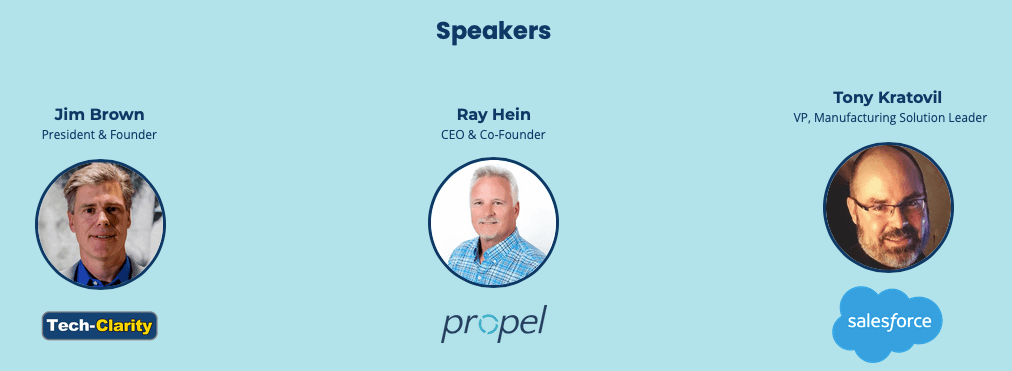
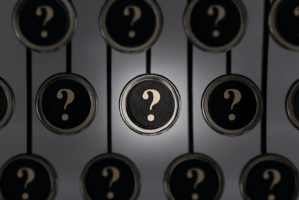
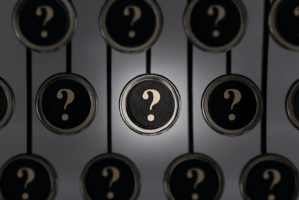
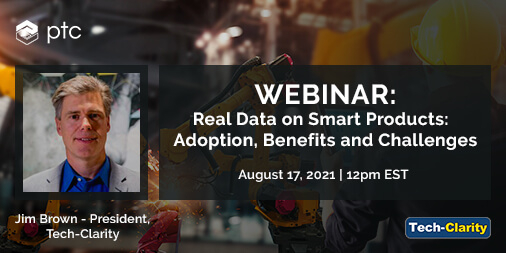
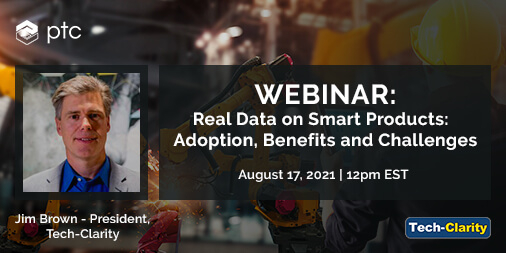
Table of Contents
- The Smart Product Imperative
- The Continuing Smart Product Revolution
- What's Driving Smart Products?
- Beyond Smart Equipment to Digital Business Models
- Multi-faceted Business Benefits
- Smart Products Improve Profitability
- Business Challenges
- Technical Issues
- How Can Companies Improve Performance?
- What Do Top Performers Do Differently?
- Top Performers Have More Integrated Systems
- Conclusions
- About the Research
- Acknowledgments
The Smart Product Imperative
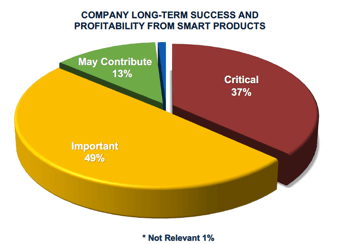
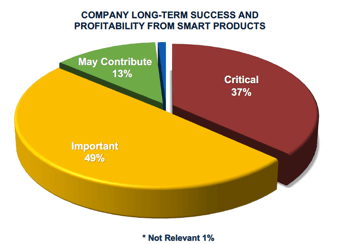
How Can Companies Improve Performance?
Identifying the Top Performers Researchers used our performance banding process to understand what companies that excel at profiting from smart products do differently. Respondents were asked to compare their performance as compared to their competition over the prior 24 months in a number of business metrics for smart products:- Revenue growth
- Profit margin expansion
- Service cost reduction
- Customer retention
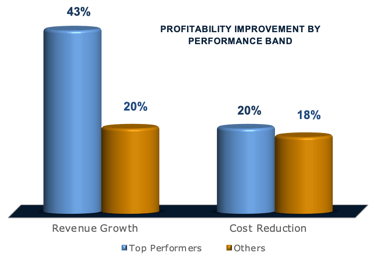
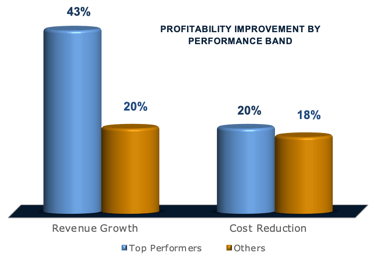
Conclusions
Smart Products are Mandatory Smart products are important or critical to the long-term profitability of most manufacturers. The vast majority of companies surveyed have transitioned to smart products and about one-half of their equipment, devices, and machines are smart. The Benefits are Compelling The transition to smart products provides significant business benefits, including double-digit revenue increase and cost reduction. The leaders, the Top Performers, are gaining even more significant gains from smart equipment, including on average:- 43% revenue growth
- 20% cost reduction
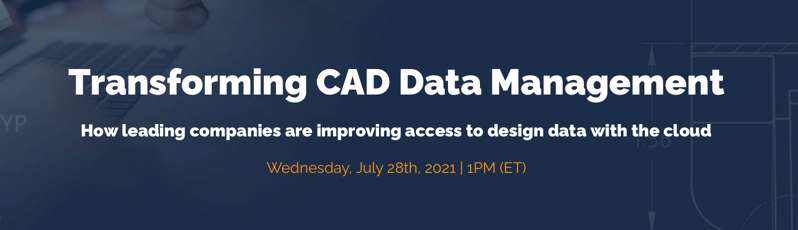
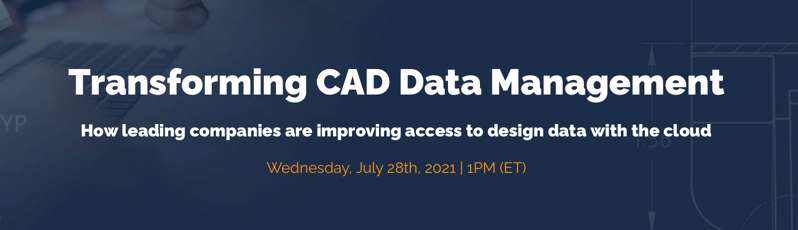
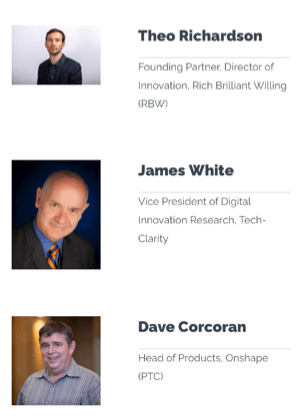
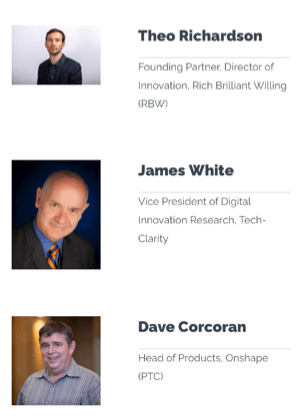
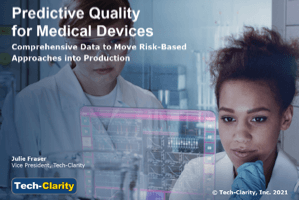
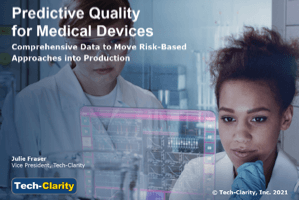
Table of Contents
- Predictive Quality
- Risk-based Approach
- The Next Level of Risk-Based Approaches
- Feedback Loops
- Data Flows for Good Decisions
- Manufacturing Data Platform
- Advanced Quality Analytics
- Predictive Quality Recommendations
- Getting to Action
- Software for Predictive Quality
- Conclusions
- Recommendations
- Acknowledgements
Predictive Quality
Beyond Traditional Quality Systems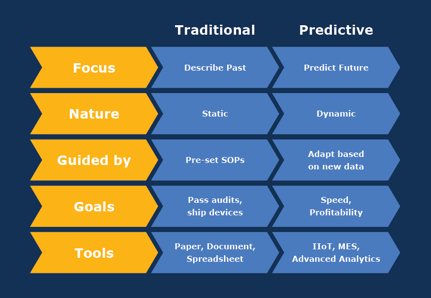
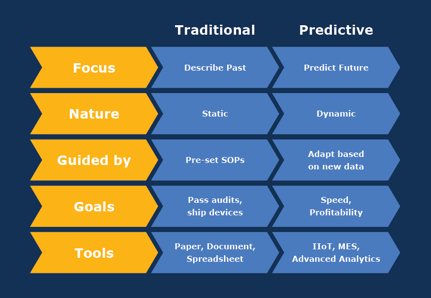
- Margin: Lower costs through reduced scrap, rework, sampling and testing
- Speed of new products: Improve design for manufacturability and quality (DFM/DFQ)
- Risk: Realize regulators’ vision of minimizing both regulatory non-compliance harm and potential health hazards
- Cycle time: Products move in the process envelope with complete documentation at every step
- Quality: Fewer non-conformances during production
- Field outcomes: Reduced customer complaints, adverse events, and in-use products issues, and ability to quickly improve
Conclusions
Predictive quality allows a medical device manufacturer not only to comply, but to improve its business results. Building on the risk-based approach to more fully encompass the complete quality system, including production, is a logical next step. Yet, traditional software approaches leave too many gaps in the information flow. Predictive quality is only possible when medical device manufacturers have an agile, responsive, and integrated manufacturing data system to support it. The platform must pull in many data streams, put them in context, and conduct effective predictive analysis. It must integrate both to OT and enterprise, creating feedback loops at many levels. There are companies starting to do that today. Medical device industry leaders are building out the information systems to enable automated release. So, beyond documentation of the process and product, the system will understand whether all processes stayed within the designed envelope to ensure a high-quality product result. Companies that can step into this next level of predictive quality will have advantages in speed, regulatory compliance, cost, and confidence. *This summary is an abbreviated version of the research and does not contain the full content. Please visit our sponsor Critical Manufacturing for the full research (registration required). If you have difficulty obtaining a copy of the report, please contact us. [post_title] => Predictive Quality for Medical Devices (eBook) [post_excerpt] => [post_status] => publish [comment_status] => open [ping_status] => open [post_password] => [post_name] => predictive-quality-ebook [to_ping] => [pinged] => [post_modified] => 2022-11-14 22:28:25 [post_modified_gmt] => 2022-11-15 03:28:25 [post_content_filtered] => [post_parent] => 0 [guid] => https://tech-clarity.com/?p=10670 [menu_order] => 0 [post_type] => post [post_mime_type] => [comment_count] => 0 [filter] => raw ) [13] => WP_Post Object ( [ID] => 10650 [post_author] => 2 [post_date] => 2021-07-13 14:36:29 [post_date_gmt] => 2021-07-13 18:36:29 [post_content] =>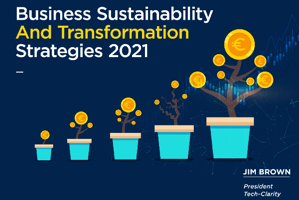
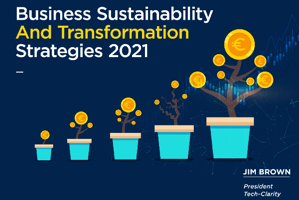
Table of Contents
- Business Risk and Disruptions Have Grown
- COVID-19 Disruption Brought Surprises
- Some Are More Prepared For Future Disruptions
- 2021 Returns to Balanced Response to Disruption
- Actions and Strategies Realigned (Exiting Crisis Mode)
- Strategic Drivers Return to Long-Term Sustainability
- Importance of Technology To Long-Term Success
- A Wide Variety of Technologies Are Strategic
- Pursuing A Variety of Tech-Supported Initiatives
- Executing Initiatives Is Still A Challenge
- Technology Adoption Challenges
- Conclusions and Next Steps
- About the Research
- Acknowledgments
Risk and Disruption Countered By Transformation
The Crisis Is Passing, But Business Risk and Disruption Persist In 2019, our Executive Strategies for Long-Term Business Success1 study found that business risk and disruption had increased for about three-quarters of survey participants over the prior five years. Clearly, business risk and disruption are not new. In 2020, our Business Sustainability (and Survival) Strategies 20202 research found that the COVID-19 disruption led many organizations to go into survival mode. The impact of the pandemic was unpredictable and had a more prolonged impact than other recent disruptions including earthquakes, tsunamis, volcanic activity, hurricanes, and human-created events like terrorism and armed conflict. Although they remained committed to important strategic initiatives like digital transformation and innovation, they lost focus on other essential pillars of long-term business sustainability. Although some are still struggling personally and professionally, our 2021 survey of 246 organizations finds that many organizations have emerged stronger because they innovated and implemented new technology to survive. The result is a market divided into organizations that are more agile and prepared for the next disruption and others who are at significant survival risk.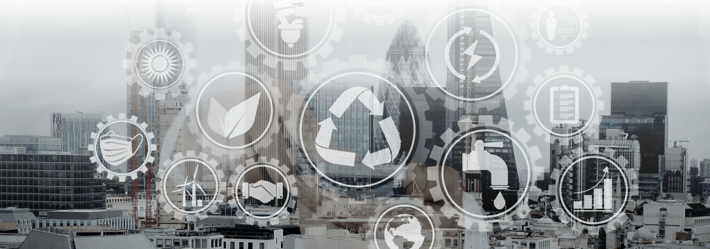
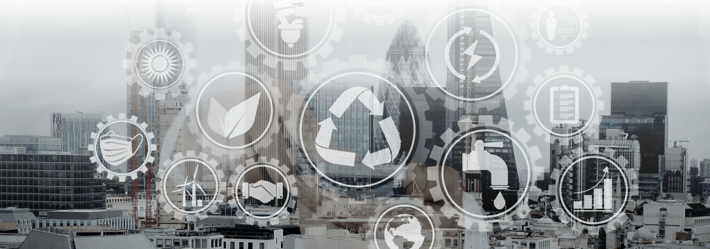
2021 Returns to Balanced Response to Disruption
Survival Mode 2020 In 2020, we shared how organizations were responding to the disruption. The results were simultaneously encouraging and discouraging. We saw that organizations enhanced their activity on some long-term business sustainability priorities while putting others on the back burner. We believe this was a short-term survival tactic. We learned that organizations were:- Accelerating digital transformation
- Maintaining investment in innovation and agility
- Decreased attention, slowed down, or even put on hold developing the workforce of the future and improving environmental impact
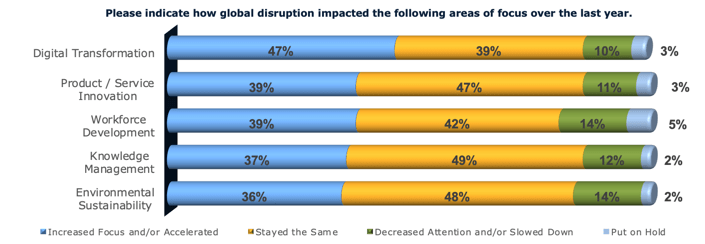
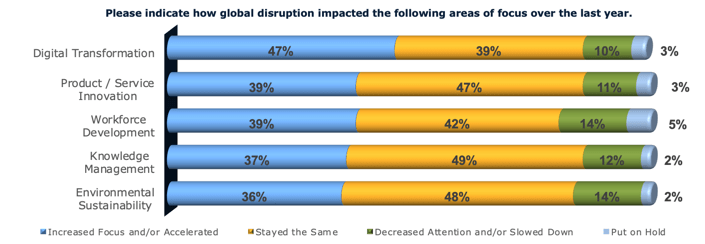
Importance of Technology To Long-Term Success
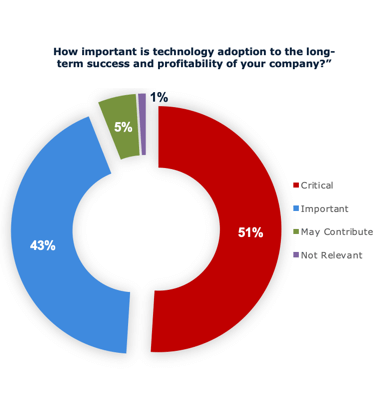
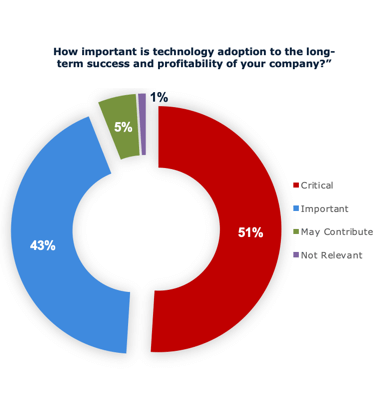
Conclusions and Next Steps
The Crisis Is Subsiding Our 2021 survey finds that responding to COVID-19 disruption is no longer the most pressing inhibitor to focusing strategy on long-term business success and profitability. Researchers found that company strategies are now more balanced and organizations can better address all of the pillars of long-term business success – including those related to corporate responsibility. Stronger Capabilities During the disruption, many organizations accelerated digital transformation, enhanced innovation, and increased their agility. They also adopted new, digital technologies and ways of working to better collaborate and support remote work. In many ways, those organizations that invested in these types of digital transformation are better prepared for the next disruption. Risk, Disruption, and Opportunity Despite the reduced impact of the current disruption, business risk skyrocketed between 2019 and 2021. The disruption led to new risks like new competitors. Further, organizations still need to address rapidly evolving business models, new technology adoption, environmental concerns, socio-economic issues, and political uncertainty. Be Better, Adapt, Or Risk Being Obsolete Now that the short-term crisis has passed, organizations can focus on the three pillars of long-term business sustainability. But organizations must remain agile, continue to transform, and learn to be prepared to respond to future disruptions. They must continue to adopt new technology and business models, despite initiative execution and technology adoption challenges. Lastly, they must remember to maintain a balanced strategy that includes product and service innovation, workforce development, environmental stewardship, and corporate social responsibility. *This summary is an abbreviated version of the ebook and does not contain the full content. For the full research, please visit our sponsor Dassault Systèmes. If you have difficulty obtaining a copy of the research, please contact us. [post_title] => Business Sustainability and Transformation Strategies [post_excerpt] => [post_status] => publish [comment_status] => open [ping_status] => open [post_password] => [post_name] => transformation-strategies-ebook [to_ping] => [pinged] => [post_modified] => 2025-01-06 21:36:27 [post_modified_gmt] => 2025-01-07 02:36:27 [post_content_filtered] => [post_parent] => 0 [guid] => https://tech-clarity.com/?p=10650 [menu_order] => 0 [post_type] => post [post_mime_type] => [comment_count] => 0 [filter] => raw ) [14] => WP_Post Object ( [ID] => 10610 [post_author] => 2 [post_date] => 2021-07-07 10:26:47 [post_date_gmt] => 2021-07-07 14:26:47 [post_content] =>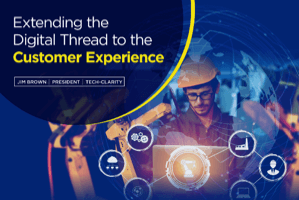
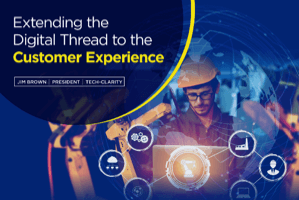
Table of Contents
- Digital Thread Context and Definition(s)
- Digital Thread Maturity
- The Business Value of Extending the Digital Thread
- Merge Product Threads with Customer Experience
- Identify Hurdles to Extending the Digital Thread
- Not an "All or Nothing" Proposition
- Reduce the Barriers
- Conclusion
- Next Steps
- Acknowledgments
Digital Transformation Unlocks Customer Value
Digital Transformation Drives Greater Customer Intimacy and Profitability Our research shows that 95% of companies view digital transformation as either important or critical to the long-term success of their company. The survey further finds the only thing more critical to a company's long-term business success than digital transformation is their customer relationships. This eBook explores extending the digital thread into the operational phase of the product lifecycle – capturing the current, as-is configuration of the product and how the customer actually uses it. Read on to learn how capturing the customer experience helps manufacturers gain new levels of intelligence and insight into products and customers so they can develop stronger customer relationships and drive higher levels of profitability.Digital Thread Maturity
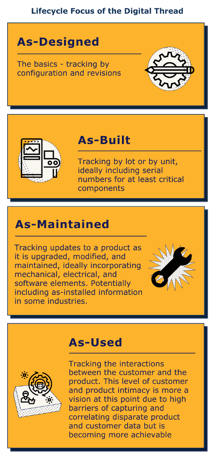
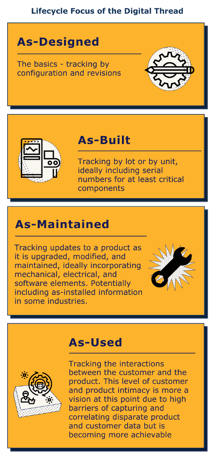
- The approach, ranging from maintaining basic history in spreadsheets and text documents to more rigorous, structured data approaches
- The scope, starting from developing a partial picture and expanding to capture information from more disciplines
- The lifecycle, representing a variety of maturity that ranges from only design and engineering phases to extension to the in-use phase
Next Steps - Incorporate the Customer Experience
Extend the Digital Thread Extend the digital thread to the customer experience to achieve even greater value:- Develop a more intimate understanding of the customer and product experience.
- Create new value from increasing profitability with lower costs and higher revenue from spares, suppliers, upgrades, replacements, and cross-selling opportunities.
- Unlock new potential by closing the loop for continuous improvement.
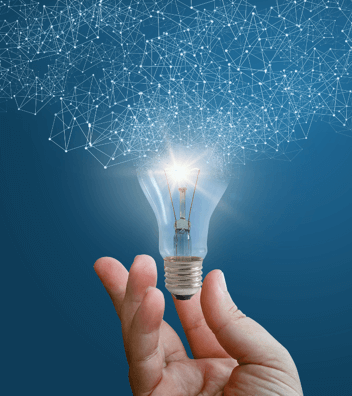
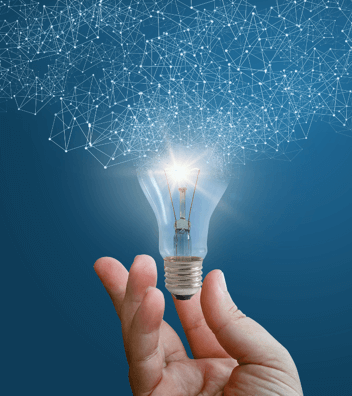
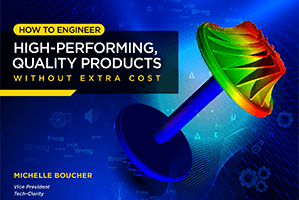
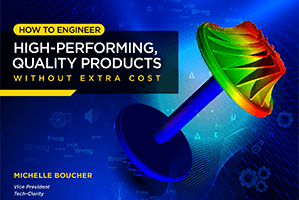
Table of Contents
- Executive Summary
- What It Takes to Succeed
- What Holds Engineers Back?
- Consider the Variety of Engineering Problems
- Better Insight Early on Will Improve Products
- Identifying Top Performing Companies
- Make Design Decisions Easier
- Benefits Regardless of Product Complexity
- Benefits of Analyzing Multiple Physics
- Best Practices for Multiple Physics
- Access What You Need, When You Need It
- Recommendations and Conclusions
- About the Research
- Acknowledgments
Executive Summary
Engineering Is Critical to Success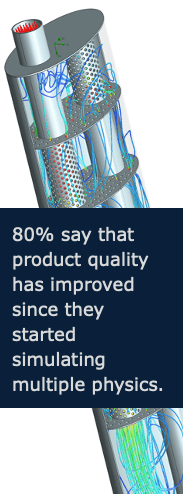
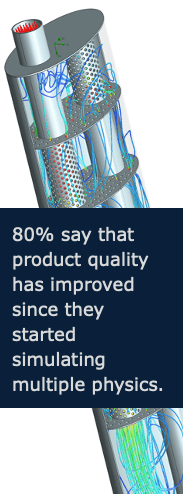
Recommendations
Recommendations and Next Steps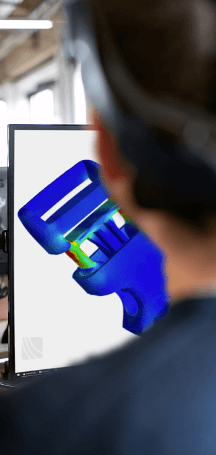
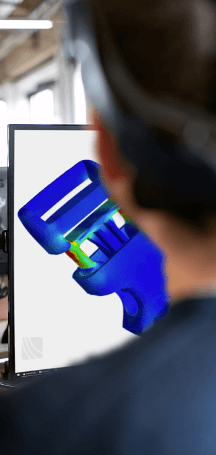
- To win over customers, ensure engineers are empowered measure KPIs and make the right design decisions that will lead to high quality, reliable, innovative, top-performing products.
- Recognize the variety of materials, components, and subsystems engineers must work with and analyze in the context of the entire product.
- Empower engineers to solve a wide variety of engineering problems while considering the complexity of the components and materials involved.
- Simulate multiple physics to get a more accurate and realistic insight into product performance.
- Ensure design engineers have access to the simulation licenses your company has so that they can simulate a variety of physics.
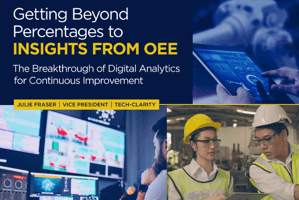
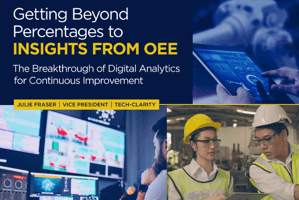
Table of Contents
- True to Continuous Improvement
- OEE: Beyond the Number
- OEE for Everyone
- How Advanced Manufacturing Enhances CI
- More, Faster Data for the CI Process
- Everyone Engaged
- OEE to Improve in the Ways that Matter Most
- Acknowledgments
Introduction
A New Normal for Overall Equipment Effectiveness and Continuous Improvement Overall Equipment Effectiveness (OEE) and Continuous Improvement (CI) are not new approaches, but the conditions in which manufacturers deploy them are. Today’s conditions include remote working, constant change, new competitors, and business uncertainty with large quantities of data that are not always used. Fortunately, many new technologies support CI processes and improve the accuracy, timeliness, and ability to act on OEE measurements. As a result, new opportunities for improving business results will arise from using digital analytics-based CI approaches.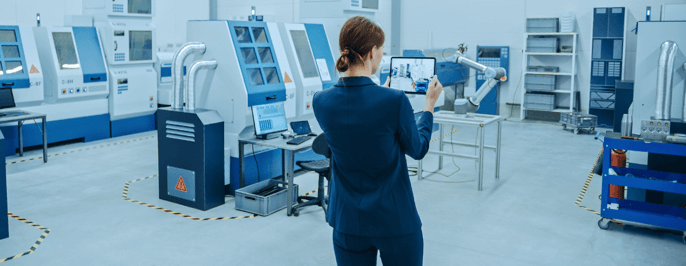
OEE to Improve in the Ways that Matter Most
Digital Advances to Boost the Basics With today’s new conditions, it is time to get back continuous improvement intentions, but do it with advanced digital analytics. Those primary intentions revolve around eliminating waste through process improvements that can impact the business. Digital matters because it delivers speed and accuracy of analysis for insights from OEE. Those characteristics enable high confidence in decisions, focused understanding of where losses occur, and thus greater improvements. *This summary is an abbreviated version of the research and does not contain the full content. Please visit our sponsor PTC for the full research (registration required). If you have difficulty obtaining a copy of the report, please contact us. [post_title] => Getting Beyond Percentages to Insights with OEE (eBook) [post_excerpt] => [post_status] => publish [comment_status] => open [ping_status] => open [post_password] => [post_name] => insights-with-oee-ebook [to_ping] => [pinged] => [post_modified] => 2022-11-14 22:28:22 [post_modified_gmt] => 2022-11-15 03:28:22 [post_content_filtered] => [post_parent] => 0 [guid] => https://tech-clarity.com/?p=10556 [menu_order] => 0 [post_type] => post [post_mime_type] => [comment_count] => 0 [filter] => raw ) [17] => WP_Post Object ( [ID] => 10541 [post_author] => 2 [post_date] => 2021-06-21 17:31:10 [post_date_gmt] => 2021-06-21 21:31:10 [post_content] =>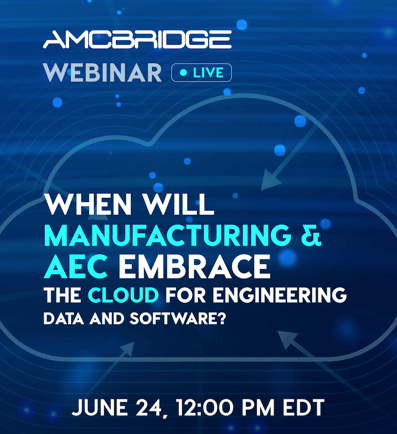
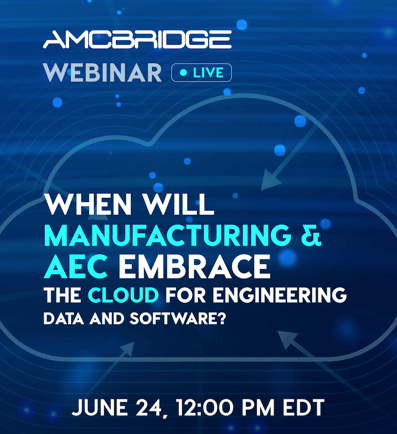
- Igor Tsinman, Co-founder and President of AMC Bridge,
- Oleg Shilovitsky, Co-founder and CEO of OpenBOM
- Marc Lind, Sr. Vice President, Strategy of Aras
- Lynn Allen, Global Technology Evangelist of Dassault Systèmes.
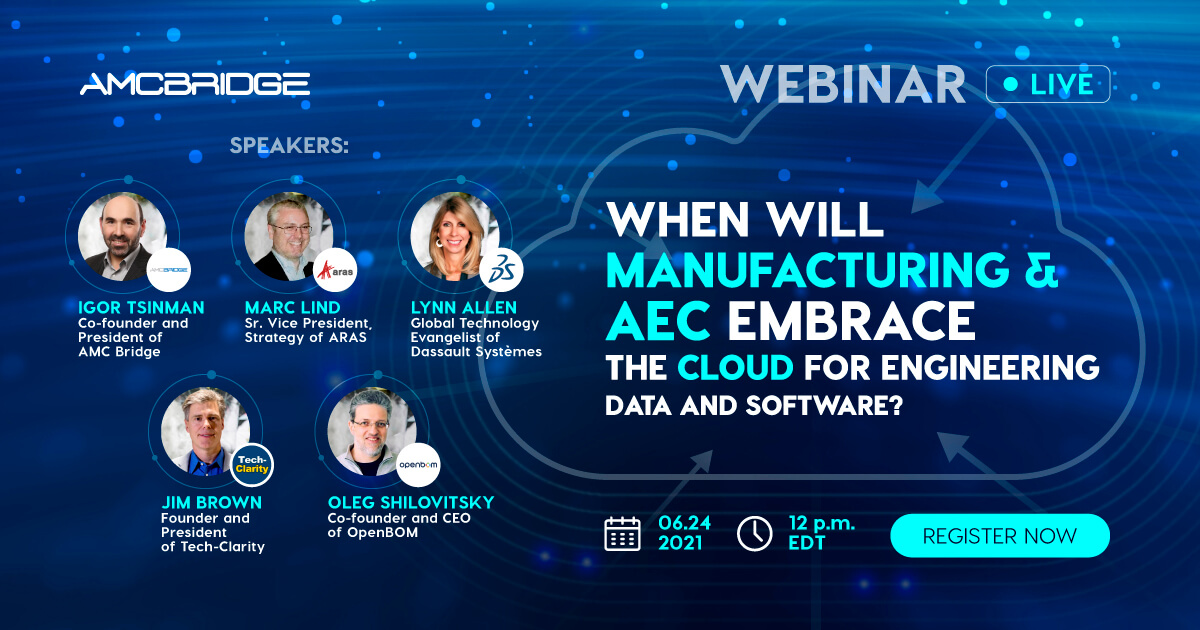
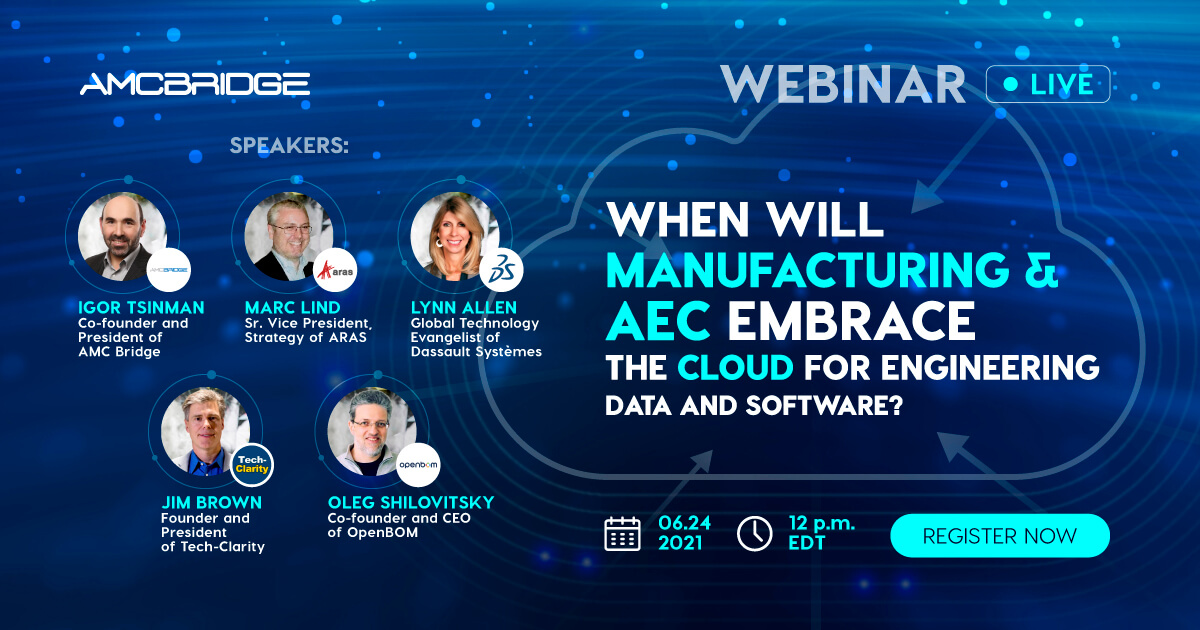


Table of Contents
- Introducing the Guide
- Why Digital Thread?
- Supporting the Digital Thread
- 1) Managing Engineering Data
- 2) BOMs, Configurations, and DMU
- 3) Production Planning
- 4) Part and Supplier Management
- 5) Product Traceability and Closed-Loop Quality
- 6) Enterprise Change
- 7) Secure Collaboration
- Implementation and Adoption
- Special Considerations
- Vendor Considerations
- Conclusions and Next Steps
- Acknowledgments
Executive Overview
The Digital Thread is Essential Over three-quarters of manufacturers view the digital thread as either important or critical to achieving their business strategy. These industrial companies view the digital thread as a fundamental way to improve performance and gain an advantage over their competitors. Our research, however, shows that only about one-quarter of companies have implemented a digital thread initiative. Having a comprehensive digital thread is moving from an advantage to a competitive necessity. But many companies struggle to define their needs and start an initiative. This guide introduces the top 7 fundamentals that manufacturers should consider to implement and support their digital thread, along with some key solution requirements to support them.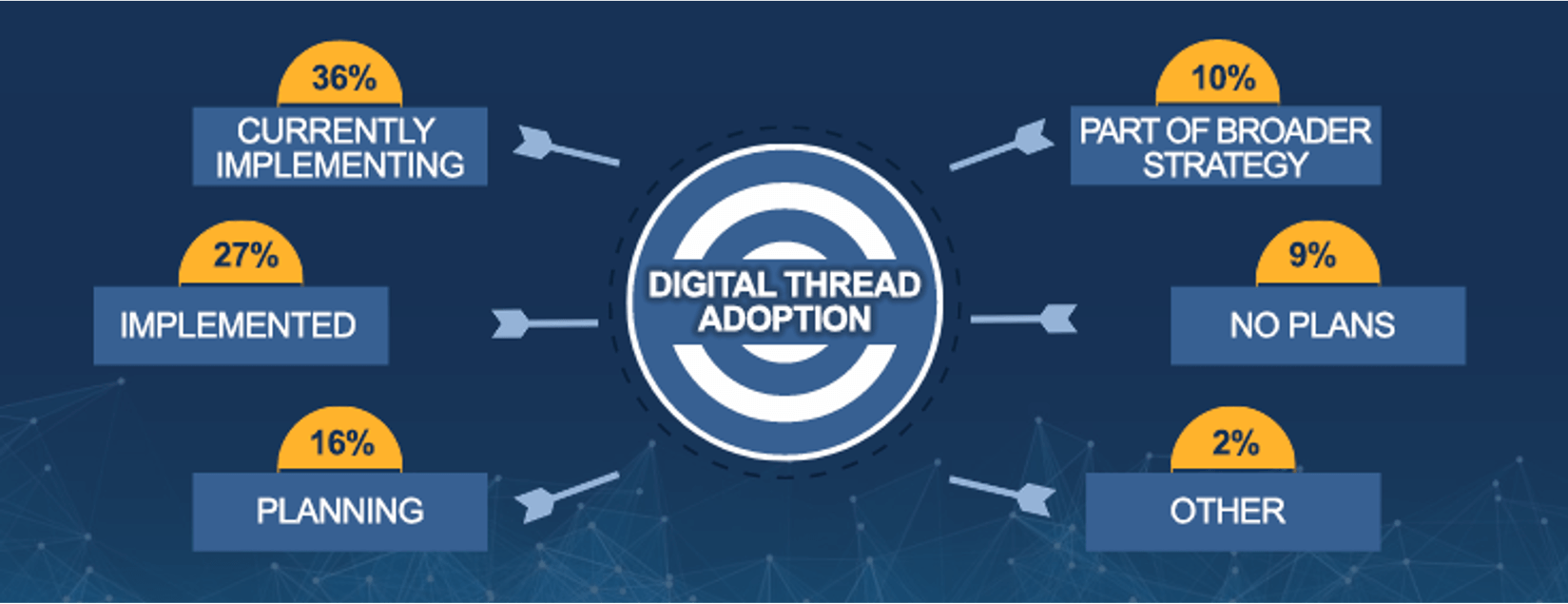
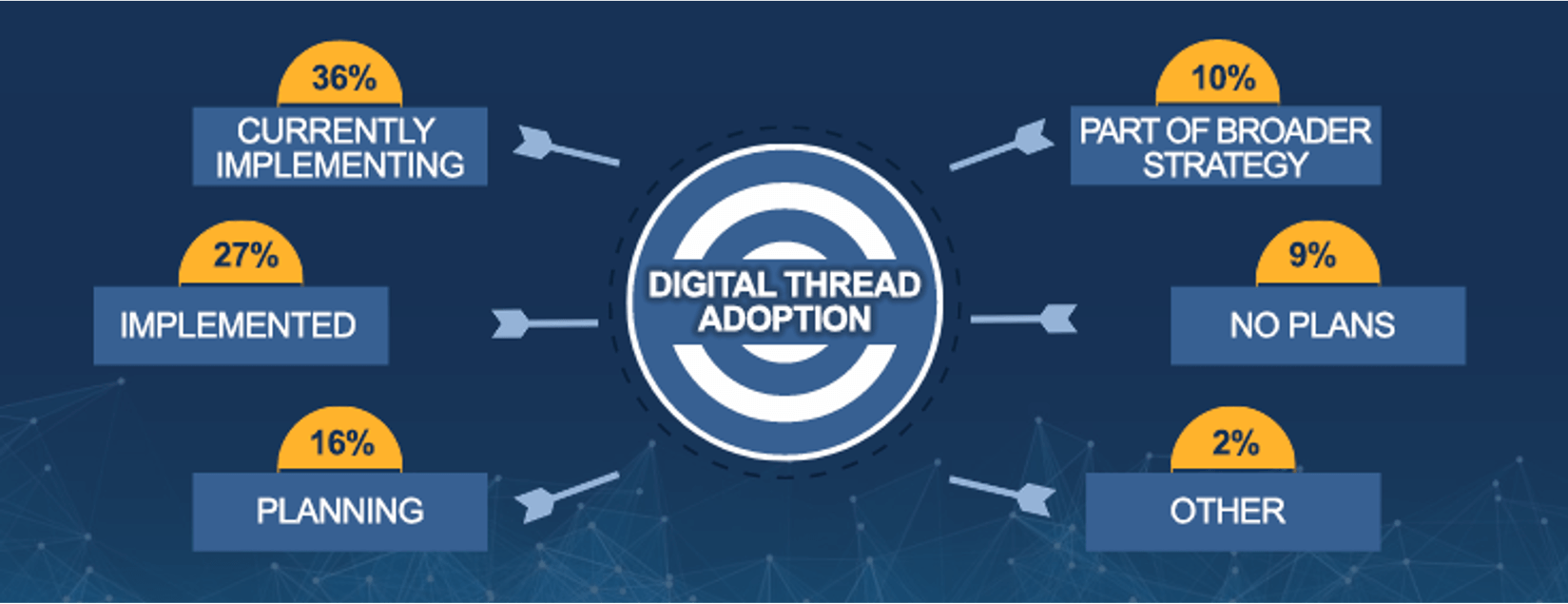
Why Digital Thread?
Business Benefits of the Digital Thread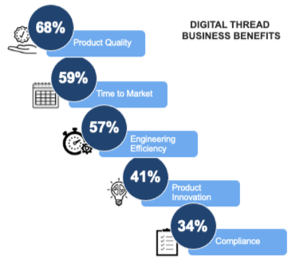
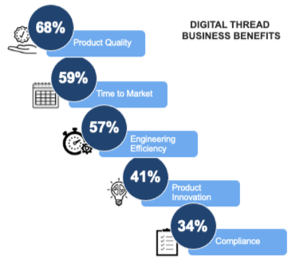
Conclusions and Next Steps
Achieving the Business Value of the Digital Thread The digital thread is crucial to business performance and competition for today’s manufacturer. We believe that those companies that adopt the efficiencies and traceability available from the digital thread have an opportunity to outperform their competitors. In fact, our research shows that Top Performers, those that outperform their competitors across key product development metrics, are almost two and one-half times as likely to have already implemented a digital thread initiative. Secure the Foundation of the Digital Thread with PLM The digital thread starts in Engineering and PLM is the foundation. Our survey finds that Top Performing companies are 2.4 times as likely to view PLM as critical to supporting the digital thread. PLM supports the basics of data management, processes, and collaboration that make up the seven foundational necessities of the digital thread. But PLM provides much more than that, supporting more advanced capabilities, integration, and technologies that will allow manufacturers to extend the value of their digital thread over time and continue to create competitive advantages. But they can start with the fundamentals and grow their capabilities – and value – over time. Get the Right PLM and Get Started As with any technology, it’s important to recognize the importance of not only software capabilities but also factors like implementation, adoption, vendor considerations, industry needs, and specific company needs. Most importantly, manufacturers should get started because the window where the digital thread provides an advantage is closing as basic digital thread maturity becomes the industry norm. *This summary is an abbreviated version of the research and does not contain the full content. Please visit our sponsor PTC for the full research (registration required). If you have difficulty obtaining a copy of the report, please contact us. [post_title] => Seven Building Blocks of the Digital Thread (eBook) [post_excerpt] => [post_status] => publish [comment_status] => open [ping_status] => open [post_password] => [post_name] => digital-thread-fundamentals-book [to_ping] => [pinged] => [post_modified] => 2022-11-14 22:28:22 [post_modified_gmt] => 2022-11-15 03:28:22 [post_content_filtered] => [post_parent] => 0 [guid] => https://tech-clarity.com/?p=10513 [menu_order] => 0 [post_type] => post [post_mime_type] => [comment_count] => 0 [filter] => raw ) [19] => WP_Post Object ( [ID] => 10507 [post_author] => 2574 [post_date] => 2021-05-24 09:55:29 [post_date_gmt] => 2021-05-24 13:55:29 [post_content] => Are your manufacturing workers safe? Many companies don’t know. Yet, the risk of not knowing workplace safety is high. The global COVID-19 pandemic has brought a new focus to the health and safety of onsite frontline employees. Those workers are in high demand, and part of knowing who is at risk comes down to their training, certifications, and qualifications. Another part is analyzing the types of issues that commonly arise in each work area and having preventive measures in place. A modern and proactive enterprise approach to health and safety software and processes is essential. For many companies, it’s quite different from the piecemeal and reactive processes currently in place. Watch this webinar with Tech-Clarity’s Julie Fraser and ComplianceQuest’s Michael Bower to learn more. Enjoy this important discussion about the rightful place of health and safety in your company’s strategy. Hear about ways to lower workplace safety and health risks.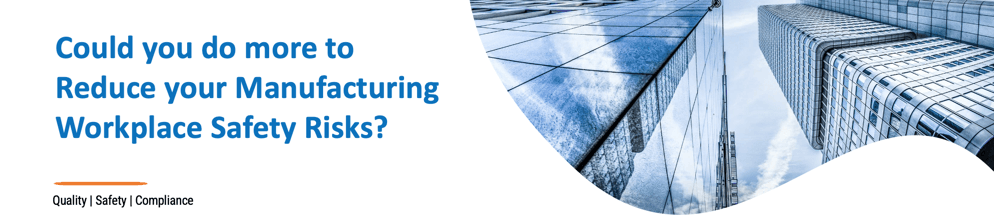
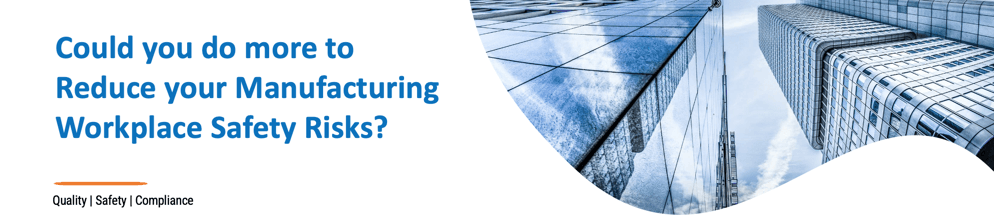
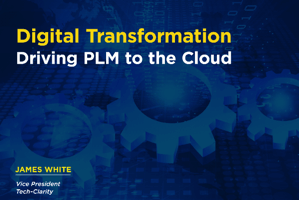
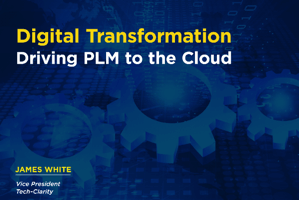
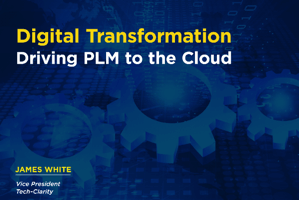
- How today’s manufacturers are leveraging cloud PLM to support their digital transformation initiatives
- The business triggers that lead to upgrading current PLM solutions
- The compelling benefits of cloud and architecture choices that need to be made
- How low-code PLM can support digital transformation
Table of Contents
- Executive Summary
- The Manufacturer's Viewpoint on PLM
- The Need to Upgrade PLM
- Cloud is Compelling
- Evaluating PLM Deployment Options
- Out-of-the-Box (OOTB) is a Fallacy
- Functionality First
- Cloud and Custom Aren't Incompatible
- Key Takeaways
- Acknowledgments
Executive Summary
Digital Transformation Demands New Capabilities, Agility Digital transformation is intensifying the need to tailor PLM systems to serve as a company’s digital backbone and support new ways of innovating and operating. Engineers need the latest features and capabilities, but also need to keep the “right-for-me” PLM capabilities they already have. PLM solutions that are customized to achieve these goals, however, can create an ongoing need for specialized services that can limit agility and prevent adoption of new features and software versions. Transitioning to the Cloud Cloud solutions are compelling but are not commonly as tailorable as traditional solutions to provide a customized experience. Cloud offers numerous business and technical advantages including lower costs, less need for IT support, strong security, high availability, and practically infinite scalability. The tradeoff is typically a more out-of-the-box (OOTB) solution with lower ability to customize to enforce company standards and provide the right experience to the end user. "Cloud" and "Customization" can Co-Exist Our experience shows that most PLM implementations are not OOTB, especially for large organizations. This creates tension between cloud benefits and creating the new digital backbone and a “right-for-me” experience. As our experience and the research for this eBook shows, however, the right balance between cloud benefits and desired customization may be available through the emerging alternative to customization, low-code / no-code development.Evaluating PLM Deployment Options
Cloud Comes in a Variety of Options Cloud is compelling, but “the cloud” is not a single option. There are multiple ways to implement PLM. Let’s look at the impacts of the different options on factors like cost, agility, and the ability to customize for the “right for me” experience. Note that these are generalizations and we recognize that there are exceptions to every rule.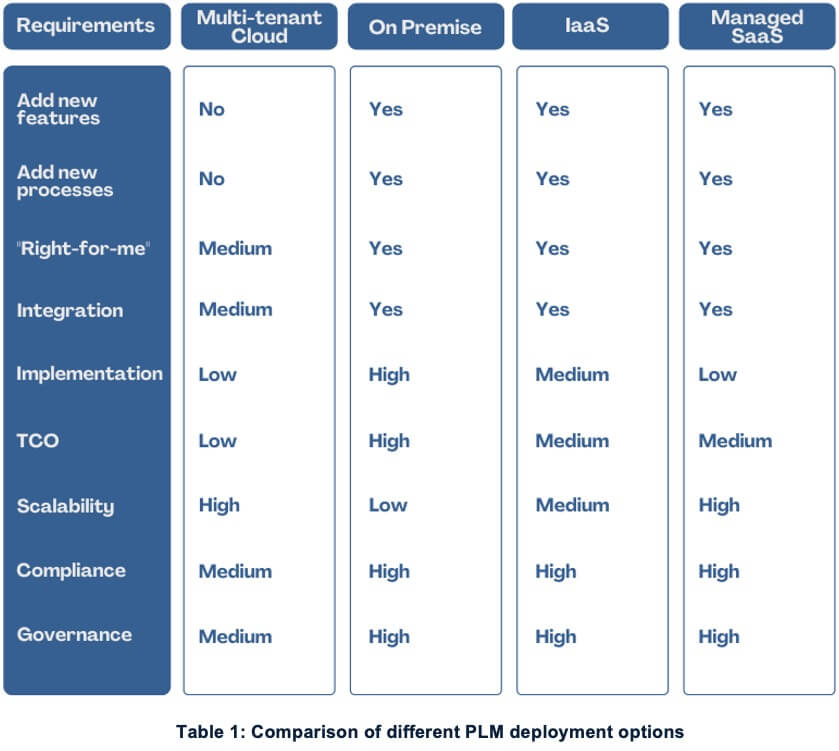
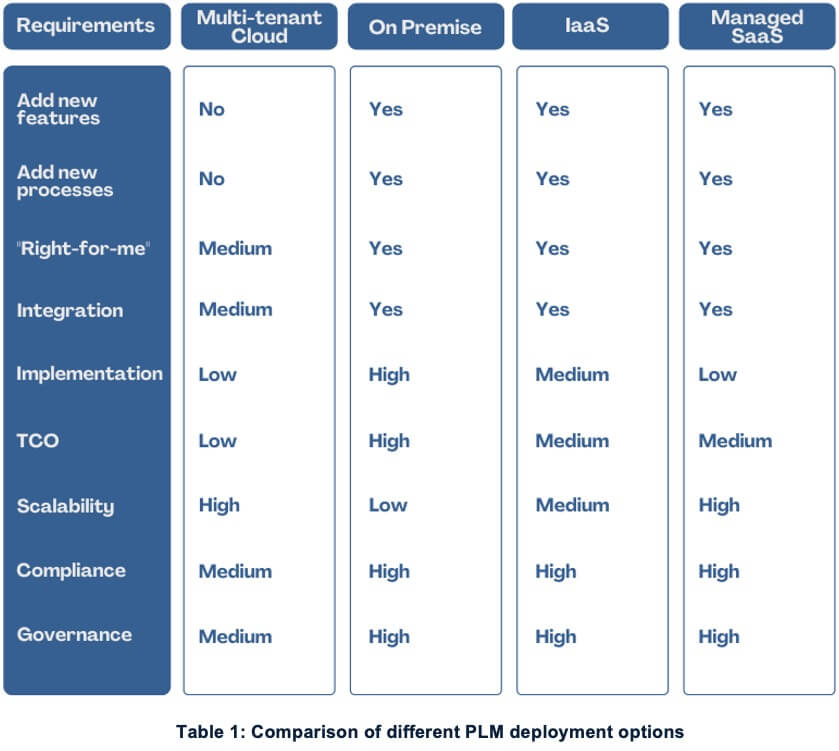
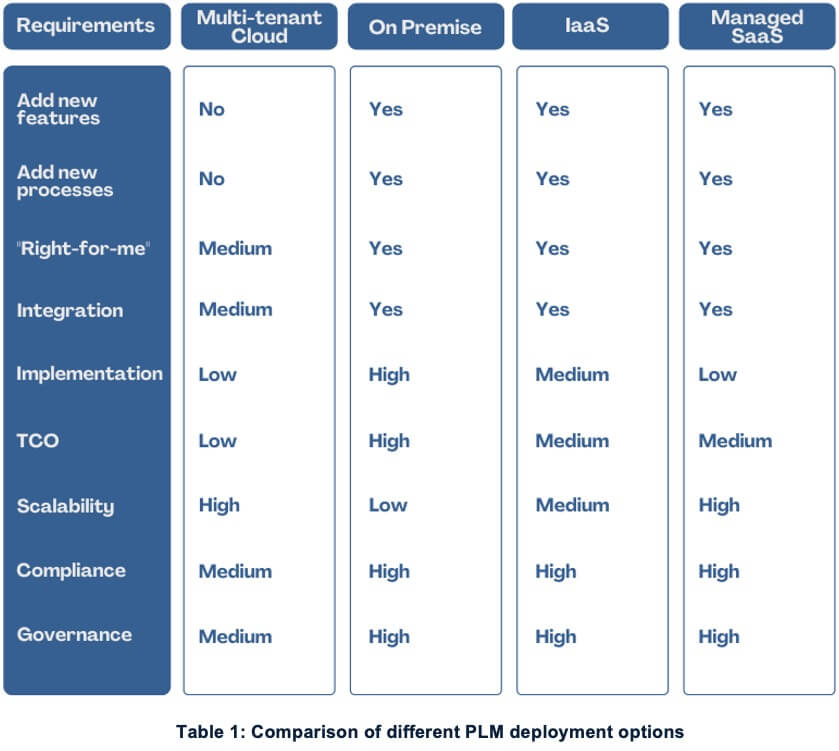
Key Takeaways
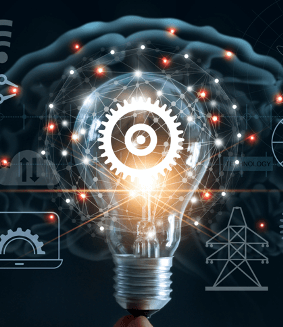
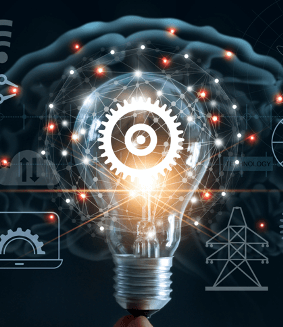
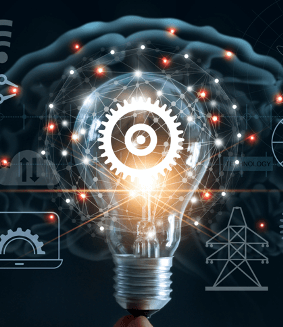
- PLM is becoming the digital backbone for manufacturers’ digital transformation strategy
- Most engineers prioritize PLM functionality and the “right-for-me” experience over cloud benefits. Traditional customization approaches lead to large technical debt and can result in dead-end customizations.
- PLM is a business imperative, and like the business, it’s a moving target. It’s important to have the ability to adapt the PLM system as needs change, to remain agile, without adding technical debt.
- Cloud and customization can both be options at the same time. The right PLM architecture can provide cloud benefits while also enabling customization without incurring significant technical debt.
All Results for "All"
MBSE: The Unsung Hero
Would you like to learn more about one of the fastest growing best practices for systems engineering, MBSE: The Unsung Hero? Michelle Boucher joined an expert panel to discuss MBSE as the unsung hero of systems engineering and a key enabler of innovation in complex products. The panel discussed: How MBSE is different The value…
What is Advanced Manufacturing? (podcast)
Manufacturing is constantly evolving, so how do you define advanced manufacturing? In this podcast episode, Julie Fraser and James Zhang, VP Market Development, Connected Operations at PTC, share their views. It starts with what constitutes advanced manufacturing today and how that has changed. New technologies can play a role, but are not sufficient. How a…
Understanding MBSE
How are your engineers managing increasing product complexity? As competitive pressures have driven innovations such as smarter features and new services, product complexity has increased. Consequently, this continues to make the job of an engineer that much harder. Our research has found that this complexity is only going to increase. Yet, the most successful companies…
Solve Digital Transformation Gaps with Low-Code (webcast)
How can you navigate digitalization challenges in a way that will evolve with current and future needs? Join this webcast where we’ll share the results of Tech-Clarity’s research on how manufacturers accelerate digital transformation with low-code applications, and Siemens’ Christopher Merz will share practical experience from the field. You will learn: The importance of digital transformation…
How to Stop Missing NPD Due Dates (survey results)
What is more important to meeting new product development due dates, individual engineering productivity or product development efficiency? We surveyed over 160 companies to find out. Please enjoy the summary below.* For the full report, please visit our sponsor SOLIDWORKS (registration required). Table of Contents Executive Overview Individual Productivity or Process Efficiency? The Impact of Product Development…
How Digital Transformation is Driving PLM to the Cloud
How can a customized PLM system be moved to the cloud and avoid becoming stuck in a dead-end? Join James White, VP Digital Innovation Research, Tech-Clarity, and Mark Reisig, VP of Product Marketing, Aras Corporation, as they discuss: How today’s manufacturers are leveraging cloud PLM to support their digital transformation initiatives The business triggers that…
Extending the Digital Thread to the Customer Experience (webcast)
How can you include the customer experience in your digital thread to gain deeper insights and increase customer intelligence? Join Jim Brown (Tech-Clarity), Ray Hein (CEO & Co-Founder of Propel), and Tony Kratovil (VP, Manufacturing Solution Leader at Salesforce) as they discuss: Merging the operational phase of the product lifecycle with the voice of the…
3 Ways Manufacturers Can Respond Confidently in the Face of Unpredictable Demand (webcast)
What’s the one constant for manufacturers today? Change. The market is uncertain, and disruptions continue. Manufacturers cannot control demand for their products. Yet, with the right foundational technologies, they can respond confidently. Hear Tech-Clarity’s Julie Fraser, VP of Research for Operations and Manufacturing at Tech-Clarity, and Allan Fine, Manager Sage X3 Field Sales Engineers, as…
How to Profit from Smart Products (webcast)
How can companies increase profits from smart products? Join our smart product webcast with PTC where we’ll review real data from our recent survey on companies’ level of involvement with smart products, quantified business results, and the opportunities and challenges of pursuing a smart products strategy. Register now to learn more insights on August 17th…
Profiting from Smart Products (survey results)
Smart products are the new norm. How can manufacturers differentiate and grow profitability as even their smart products become commodities? Our survey of over 150 companies shows that manufacturers are targeting much larger goals as they mature their smart product strategies beyond their products by adopting smart, connected, digital business models. Please enjoy the summary*…
Transforming CAD Data Management
How can engineers improve efficiency, personal productivity and find the information they need faster? Join this live Onshape webcast with James White, VP of Digital Innovation Research at Tech-Clarity; Theo Richardson, founding partner and Director of Development at Rich Brilliant Willing (RBW); and Dave Corcoran, Head of Products at Onshape to gain insight into how top performing…
Predictive Quality for Medical Devices (eBook)
Could medical device companies improve both patient outcomes and profit? Yes, and Predictive Quality for Medical Devices: Comprehensive Data to Move Risk-based Approaches into Production discusses how to modernize the quality system for best results. The predictive approach to quality is proactive and requires strong manufacturing data management. The report includes insights from executives at…
Business Sustainability and Transformation Strategies
With the crisis phase of COVID-19 passing, how are companies adjusting corporate strategies and priorities to address intensified business risk and disruption? How are they setting transformation strategies to ensure long-term business success and profitability in the face of rapidly evolving business models, new technology adoption, environmental concerns, socio-economic issues, and political uncertainty? We surveyed…
Extending Digital Threads to the Customer Experience (eBook)
How can manufacturers get closer to customers, gain more intimacy, and create more business value for themselves and their customers? How does extending the digital thread into the customer experience and operational phase of the product lifecycle help? Our eBook shares the results of interviews with eight manufacturers to shed some light. Please enjoy the…
How to Engineer High-Performing, Quality Products without Extra Cost
What is the best way for engineers to manage multiple design criteria, impacted by multiple physics, yet still meet deadlines, cost targets, and quality requirements? Tech-Clarity’s eBook, How to Engineer High-Performing, Quality Products without Extra Cost, examines this question. The eBook shares findings based on the results of a survey of 272 manufacturers. It also…
Getting Beyond Percentages to Insights with OEE (eBook)
Could your overall equipment effectiveness (OEE) metrics do more to accelerate improvement? Most manufacturers’ can, but not necessarily by doing what they have been doing. Read our eBook, Getting Beyond Percentages to Insights with OEE, to learn more. Please enjoy the summary* below. Please visit our sponsor PTC for the full research (registration required). For related…
Embracing Cloud Engineering Software and Data (webcast)
How ready are manufacturers and AEC companies to embrace the cloud in engineering? AMC Bridge’s live webcast, hosted by Jim Brown, explores whether now is the right time to move toward cloud engineering software and data. Hear the panel of speakers share their deep experience and unique perspectives: Igor Tsinman, Co-founder and President of AMC Bridge,…
Seven Building Blocks of the Digital Thread (eBook)
What are the core fundamentals that manufacturers need in their digital thread? What do they need in their PLM system to serve as their digital thread backbone? Read our eBook, The Seven Building Blocks of the Digital Thread, to learn more. Please enjoy the summary* below. Please visit our sponsor PTC for the full research (registration…
Could You Reduce your Manufacturing Workplace Safety Risks? (webcast)
Are your manufacturing workers safe? Many companies don’t know. Yet, the risk of not knowing workplace safety is high. The global COVID-19 pandemic has brought a new focus to the health and safety of onsite frontline employees. Those workers are in high demand, and part of knowing who is at risk comes down to their…